ML-210-IB Black Thermal Control Paint: Material Guide for Aerospace Applications
May 15, 2025
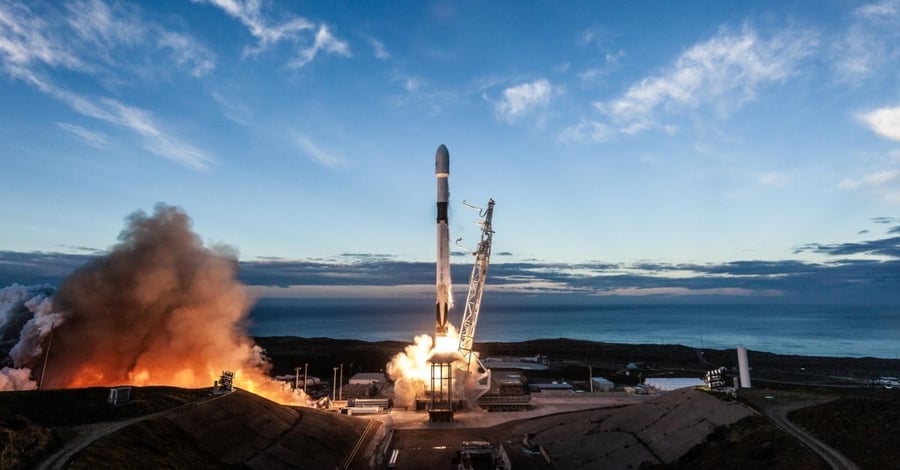
Manufactured with Speed and Precision
The manufacturing capabilities you need and the engineering support you want, all from a single partner.
Submit a DesignKey Points
- ML-210-IB is an inorganic black thermal control paint designed specifically for spacecraft and satellites, capable of withstanding extreme space environments
- This specialized coating offers exceptional optical properties with 0.98 solar absorptance and 0.91 thermal emittance, making it ideal for thermal management applications
- The paint has been rigorously tested for Low Earth Orbit (LEO) conditions, including Atomic Oxygen (AO) exposure equivalent to 15 years in space
- ML-210-IB can withstand temperatures from -180°C to 600°C while maintaining its optical properties
- Application methods include airbrush and HVLP spray systems with specific preparation and curing requirements
- Environmental considerations include proper handling, storage, and disposal according to hazardous material regulations
What is ML-210-IB?
ML-210-IB is an inorganic black thermal control paint that combines carbon black pigment in a silicate binder, specifically engineered for spacecraft and satellite applications requiring precise thermal management. This specialized coating delivers exceptional optical properties (0.98 solar absorptance and 0.91 thermal emittance) while withstanding extreme space environments, including atomic oxygen exposure and temperatures ranging from -180°C to 600°C.
Thermal control paint plays a critical role in aerospace engineering, particularly for components that experience extreme temperature variations. ML-210-IB represents an advanced solution in this category, offering specialized thermal management capabilities for demanding applications. This inorganic coating combines a carbon black pigment with a silicate binder to create a non-specular black surface that delivers precise optical and thermal properties.
Unlike organic thermal control paints that break down in space environments, ML-210-IB's inorganic composition provides exceptional durability when exposed to the harsh conditions of orbit. The thermal control paint maintains its performance characteristics even after extended exposure to atomic oxygen and vacuum ultraviolet radiation, making it an optimal choice for long-duration space missions.
ML-210-IB is an inorganic black thermal control paint that combines carbon black pigment in a silicate binder, specifically engineered for spacecraft and satellite applications requiring precise thermal management. This specialized coating delivers exceptional optical properties (0.98 solar absorptance and 0.91 thermal emittance) while withstanding extreme space environments, including atomic oxygen exposure and temperatures ranging from -180°C to 600°C.
Visit the Resource Center: Advanced Coatings for Aerospace Optics
Material Composition and Properties
ML-210-IB thermal control paint consists of a carefully formulated blend of carbon black pigment in a potassium silicate binder. This composition gives the coating its distinctive thermal and optical characteristics. Understanding these properties is essential for engineers determining the suitability of this thermal control coating paint for specific applications.
Key Material Properties
The following table outlines the critical specifications of ML-210-IB thermal control paint after proper curing:
Property | Specification | Notes |
Solar Absorptance (α_s) | 0.98 ± 0.02 | At ≥ 1.5 mils thickness |
Thermal Emittance (ε_t) | 0.91 ± 0.02 | Room temperature measurement |
Use Temperature Range | -180°C to 600°C (-292°F to 1112°F) | Maintains optical properties |
Surface Appearance | Nonspecular optical black | Low specular reflection |
Nominal Dry Thickness | 2.5+1.0, -1.5 mils | Over 85% of coated area |
ASTM D3359A Adhesion | Not less than 3A | Industry standard test |
Full Cure Time | 7 days | At standard conditions |
These specifications demonstrate why ML-210-IB thermal control coating paint excels in applications requiring high solar absorption and thermal emission properties. The near-unity values for both solar absorptance and thermal emittance make this coating particularly valuable for precise thermal management in space environments.
Deep Dive: What is Thermal Emittance?
Discover the critical role thermal emittance plays in spacecraft temperature regulation in our comprehensive technical guide.
Learn MoreDeep Dive: What is Solar Reflectance?
Explore how solar reflectance impacts thermal management systems in aerospace applications in our detailed engineering analysis.
Learn MoreDeep Dive: What is Solar Absorptance?
Learn why precise solar absorptance values are essential for mission success in our expert breakdown of thermal control coatings.RetryClaude can make mistakes.
Learn MoreEnvironmental Performance
ML-210-IB thermal control paint has undergone extensive testing to validate its performance in space environments. The results demonstrate exceptional durability under extreme conditions that would degrade many alternative coatings.
The coating has been subjected to:
- Atomic Oxygen (AO) flux equivalent to approximately 15 years in Low Earth Orbit
- Vacuum Ultraviolet (VUV) exposure at 130 times normal intensity
- Thermal cycling across its operational temperature range
- Vacuum environment testing
These tests confirm that ML-210-IB thermal control paint maintains its optical and thermal properties even after extended exposure to the harsh space environment. This stability makes it particularly valuable for long-duration missions where coating degradation could compromise thermal management systems.
Surface Preparation Requirements
Proper surface preparation is essential for achieving the specified adhesion and performance characteristics of ML-210-IB thermal control paint. The substrate must be thoroughly cleaned to remove any contaminants that could interfere with adhesion.
The recommended surface preparation process includes:
- Solvent cleaning to remove oils and organic contaminants
- Abrasive cleaning to create an appropriate surface profile
- Final cleaning to remove abrasive residue
- Priming if required for specific substrate materials
The surface should be completely dry before application of the thermal control paint, as moisture can interfere with the silicate binder's curing process and compromise coating adhesion.
Modus Advanced brings specialized expertise to this critical preparation phase, with aerospace-grade cleaning facilities and AS9100/ISO 9001 certified processes that ensure consistent quality. Our engineering team evaluates each substrate to determine the optimal preparation method, preventing costly adhesion failures that can occur with improper surface treatment.
Read the guide: Optical and Thermal Coatings in Aerospace
Application Methods
ML-210-IB thermal control paint can be applied using several methods, with spray application being preferred for most situations. The choice of application method depends on the geometry of the component and the required coating uniformity.
Recommended application methods include:
- Airbrush application for small areas and complex geometries
- High-Volume, Low-Pressure (HVLP) spray systems for larger areas
- Conventional spray equipment with appropriate setup
Multiple thin coats are preferable to a single thick coat, allowing for proper drying between applications. This approach minimizes the risk of coating defects and ensures uniform thickness across the substrate.
Modus Advanced utilizes state-of-the-art application equipment operated by certified technicians who specialize in aerospace coatings. Our controlled environment spray booths maintain precise temperature and humidity conditions, critical factors in achieving the specified optical properties of ML-210-IB thermal control paint. With more than 10% of our staff comprised of engineers, we provide technical expertise throughout the application process to ensure your specifications are met with precision.
Curing Process
The curing process for ML-210-IB thermal control paint involves both physical drying and chemical reaction phases. Complete curing is essential for achieving the specified thermal and optical properties.
The standard curing schedule consists of:
- Air drying for 24 hours at ambient temperature
- Heat curing at 65-93°C for 2 hours
- Final curing for 7 days at ambient conditions
Variations in the curing schedule may be necessary based on specific application requirements. The manufacturer's guidelines should be consulted for any deviations from the standard process.
Modus Advanced's climate-controlled facilities and calibrated curing equipment ensure that your thermal control paint application follows the exact curing parameters required. Our vertically integrated quality control systems monitor the entire process, with documentation that meets aerospace and defense industry standards. This rigorous approach eliminates the variability that can compromise coating performance in critical applications.
The Modus Advanced Advantage
Working with Modus Advanced for your ML-210-IB thermal control paint application delivers several key advantages:
- Dedicated engineering support from initial design through production
- Vertically integrated processes that reduce lead times by up to 50%
- AS9100/ISO 9001 certified quality management system
- ITAR compliance for defense and aerospace applications
- Comprehensive documentation and traceability
- Proven experience with mission-critical coatings
Our commitment to quality and technical excellence makes Modus Advanced the obvious choice for aerospace manufacturers who understand that precision thermal control coatings are too important to leave to chance.
Coating ServicesPerformance Comparison with Alternative Coatings from AZ Technologies
ML-210-IB thermal control paint offers specific advantages compared to other thermal control coatings. Understanding these differences helps engineers select the optimal coating for their specific application requirements.
Comparative Analysis
The following table compares ML-210-IB with other common thermal control paints used in aerospace applications:
Property | ML-210-IB | RM-550-IB | TMD-560-IB | Z-93P |
Solar Absorptance (α_s) | 0.98 | 0.93 | 0.94 | 0.14 |
Thermal Emittance (ε_t) | 0.91 | 0.89 | 0.90 | 0.92 |
Max Temperature | 600°C | 800°C | 900°C | 400°C |
Composition | Carbon black in silicate | Refractory oxide | Metal oxide | Zinc oxide |
Primary Use | Thermal absorption | High-temp baffle | Ultra-high temp | Thermal reflection |
ML-210-IB thermal control paint provides the highest solar absorptance of these options, making it ideal for applications requiring maximum thermal energy collection. However, it has a lower maximum temperature capability than RM-550-IB or TMD-560-IB, which should be considered when selecting a coating for extremely high-temperature environments.
Application-Specific Considerations
When selecting ML-210-IB thermal control paint for a specific application, engineers should consider:
- Required optical properties (absorptance/emittance ratio)
- Maximum and minimum service temperatures
- Exposure environment (LEO, GEO, or ground applications)
- Service lifetime requirements
- Substrate material compatibility
The high solar absorptance of ML-210-IB thermal control paint makes it particularly suitable for optical baffles, sun sensors, and thermal management systems that require efficient absorption of solar energy.
Real-World Applications in Aerospace
ML-210-IB thermal control paint has proven its value in numerous aerospace applications where precise thermal management is critical to mission success. The coating's combination of high solar absorptance and thermal emittance makes it particularly suitable for specific spacecraft components.
Typical Use Cases
ML-210-IB thermal control paint is commonly applied to:
- Optical baffles in spacecraft imaging systems
- Sun sensors and solar attitude detectors
- Radiator components requiring specific α/ε ratios
- Thermal management surfaces in satellite systems
- Ground test equipment simulating space thermal environments
The nonspecular black finish also makes this thermal control paint useful for reducing stray light in optical systems, combining thermal management with optical performance enhancement.
Performance Expectations
When properly applied and cured, ML-210-IB thermal control paint provides:
- Consistent optical properties across its operational temperature range
- Excellent adhesion to properly prepared substrates
- Resistance to degradation from atomic oxygen in LEO
- Stability under vacuum ultraviolet radiation exposure
- Long-term performance in space environments
These characteristics have been validated through both laboratory testing and actual space flight experience, confirming the coating's suitability for critical aerospace applications.
Engineering with Excellence
ML-210-IB thermal control paint represents an advanced solution for aerospace thermal management challenges. Its specialized formulation provides the precise optical and thermal properties required for spacecraft operating in the extreme environment of space.
For engineers developing systems that must function reliably in these demanding conditions, understanding the capabilities and application requirements of ML-210-IB thermal control paint is essential. This knowledge enables the creation of thermal management solutions that contribute to mission success through consistent, predictable performance.
When your application demands precision thermal control in extreme environments, ML-210-IB delivers the performance characteristics needed for engineering excellence. Partner with Modus Advanced to ensure your thermal management solutions meet the highest standards of quality and reliability.