Parker Chomerics Form-in-Place Gasket Materials
August 5, 2021
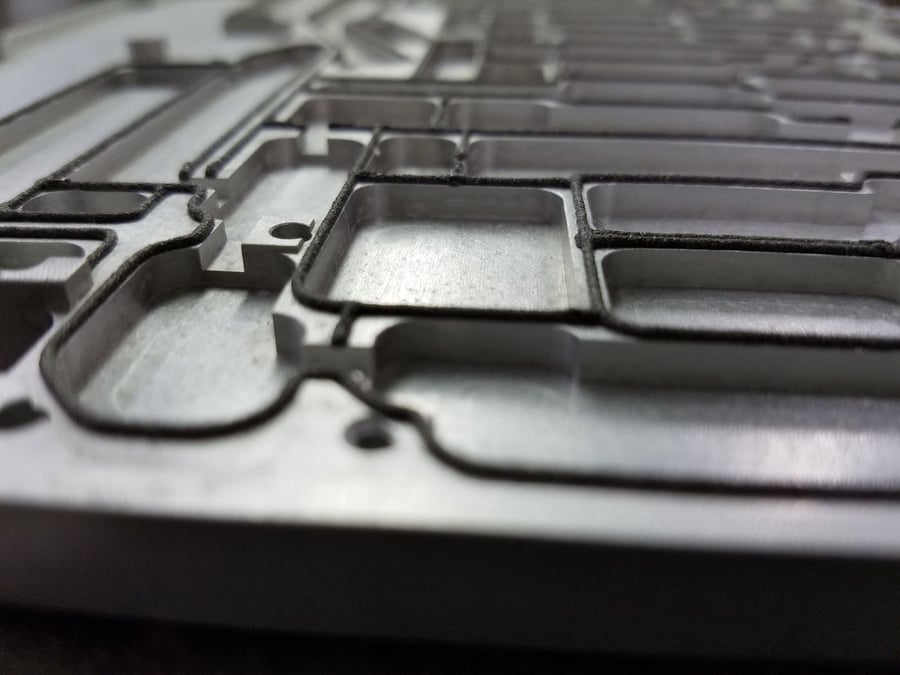
Manufactured with Speed and Precision
The manufacturing capabilities you need and the engineering support you want, all from a single partner.
Submit a DesignKey Points
- Parker Chomerics, a division of Parker Hannifin Corporation, is a global leader in developing thermal interface and electrically conductive materials for form-in-place (FIP) gaskets.
- Chomerics offers two main product lines: conductive CHO-FORM® gasket materials with various metal fillers (silver, copper, nickel, aluminum, graphite) and non-conductive ParPHorm® gasket materials.
- Different CHO-FORM materials offer varying properties for conductivity, EMI shielding, temperature resistance, and corrosion protection, allowing engineers to select the optimal material for their specific application.
- Parker Chomerics FIP gasket materials use either thermal curing (100-150°C for at least 30 minutes) or moisture curing (room temperature for at least 24 hours), with thermal curing generally providing stronger adhesion.
- Modus Advanced routinely works with Parker Chomerics materials to produce high-quality FIP gaskets for customers in aerospace, defense, telecommunications, and electronics industries.
The Chomerics division of Parker Hannifin Corporation is a global leader in the development of thermal interface and electrically conductive materials. The company serves a broad range of industries and creates high-quality materials for a variety of applications, including those that require form-in-place (FIP) gaskets.
Major companies across aerospace, defense, telecommunications and electronics know Parker Chomerics form-in-place gasket materials for their high level of quality. Modus Advanced routinely employs Parker Chomerics materials in the production of FIP gaskets for our customers.
In this post, the Modus Advanced team walks you through the available FIP gasket materials from Parker Chomerics so you can make an informed gasket material choice as you move forward with your design. Read on to learn more.
Visit the Modus Form-in-Place Gasket Resource Center
Conductive Parker Chomerics Form-in-Place Gasket Materials
Parker Chomerics offers a line of electrically conductive FIP gasket materials called CHO-FORM®. These materials are dispensed directly onto machined metal, castings and conductive plastic housings and provide excellent electrical contact.
Material Spotlight
CHO-FORM®
CHO-FORM is Parker Chomerics' line of electrically conductive form-in-place gasket materials designed primarily for EMI shielding applications in electronics, defense, and telecommunications. These silicone-based materials contain various metal fillers (silver, copper, nickel, aluminum, and graphite) that provide specific electrical conductivity, temperature resistance, and corrosion protection properties depending on the application requirements.
There are several FIP gasket materials to choose from within the CHO-FORM line:
CHO-FORM 5513
CHO-FORM 5513 has a silicone base and conductive filler material made from silver and copper. This material comes with excellent electrical properties and adheres strongly to the surface on which it is dispensed.
CHO-FORM 5541
With a silicone base and a nickel and graphite filler, CHO-FORM 5541 offers superior resistance to corrosion and high temperatures, as well as strong electrical conductivity. This material is also highly effective at electromagnetic interference (EMI) shielding, although it is less effective than CHO-FORM 5513 and CHO-FORM 5560.
CHO-FORM 5550
CHO-FORM 5550 is another Parker Chomerics form-in-place gasket material that contains a nickel and graphite filler material and silicone base material. The main property that differentiates this material from CHO-FORM 5541 is softness. Its hardness and tensile strength ratings are lower, but CHO-FORM 5550 still offers galvanic corrosion resistance and the ability to withstand high temperatures.
CHO-FORM 5560
Nickel and aluminum fill this silicone-based FIP gasket material. CHO-FORM 5560 stands out among the CHO-FORM line because it offers the best resistance to galvanic corrosion. Its other properties are highly similar to CHO-FORM 5550, with only slight differences.
CHO-FORM 5575
CHO-FORM 5575 has a silicone base and a silver and aluminum filler. This material scores the highest hardness rating of the CHO-FORM materials. Although it is not the most effective EMI shield of the line, CHO-FORM 5575 still offers effective EMI shielding.
CHO-FORM 5526
Silver filler makes this FIP gasket material from Parker Chomerics an excellent choice for conductivity, grounding and EMI shielding, but the costs associated with silver can make this material among the more expensive options. CHO-FORM 5526 is not recommended for applications that require galvanic corrosion resistance.
CHO-FORM 5528
CHO-FORM 5528 is a relatively soft material with low closure force. It’s filled with silver and copper and based in silicone. Note that this material is less resistant to higher temperatures than many of the other materials in the CHO-FORM family.
CHO-FORM 5538
A silicone base and nickel and carbon filler make CHO-FORM 5538 resistant to galvanic corrosion. It is similar to CHO-FORM 5528, but it offers higher hardness and tensile strength ratings.
Conductive CHO-FORM Materials Comparison
Material | Base | Conductive Filler | EMI Shielding | Galvanic Corrosion Resistance | Hardness | Notable Properties | Curing Method |
---|---|---|---|---|---|---|---|
CHO-FORM 5513 | Silicone | Silver/Copper | Excellent | Low | Medium | Excellent electrical properties, strong adhesion | Thermal |
CHO-FORM 5541 | Silicone | Nickel/Graphite | Good | High | Medium | Superior resistance to high temperatures | Thermal |
CHO-FORM 5550 | Silicone | Nickel/Graphite | Good | High | Low | Softer material with lower closure force | Thermal |
CHO-FORM 5560 | Silicone | Nickel/Aluminum | Good | Excellent | Low-Medium | Best galvanic corrosion resistance in CHO-FORM line | Thermal |
CHO-FORM 5575 | Silicone | Silver/Aluminum | Good | Medium | High | Highest hardness rating of CHO-FORM materials | Moisture |
CHO-FORM 5526 | Silicone | Silver | Excellent | Low | Medium | Excellent conductivity and grounding, higher cost | Moisture |
CHO-FORM 5528 | Silicone | Silver/Copper | Excellent | Low | Low | Soft material with low closure force, limited temperature resistance | Moisture |
CHO-FORM 5538 | Silicone | Nickel/Carbon | Good | High | Medium | Similar to 5528 but with higher hardness and tensile strength | Moisture |
For more information on the properties of CHO-FORM FIP gasket materials, check out the material selector guide here and here.
Learn everything you have ever wanted to know about FIP gaskets in our ultimate guide!
Non-Conductive Parker Chomerics FIP Gasket Materials
Parker Chomerics offers a range of non-conductive FIP gasket materials with its ParPHorm® line. With dispensing beads ranging from 0.46 millimeters to 1.57 mm, these compounds are specifically designed to be dispensed onto small housings.
Material Spotlight
ParPHorm®
ParPHorm is Parker Chomerics' family of non-conductive form-in-place elastomeric sealing compounds designed specifically for environmental sealing in small enclosures. These precision materials can be robotically dispensed into beads ranging from 0.46mm to 1.57mm, offering various hardness levels and base materials (silicone or fluorosilicone) to meet different application needs for environmental protection without electrical conductivity.
Non-conductive Parker Chomerics form-in-place gasket materials come in three varieties:
ParPHorm 1800
A silicone elastomer, ParPHorm 1800 offers the lowest hardness and tensile strength of the ParPHorm line, but its elongation properties score the highest of the three materials. This material is meant for very small enclosures and offers strong compression set, low closure force and excellent adhesion.
ParPHorm S1945-25
ParPHorm S1945-25 is similar to ParPHorm 1800 in that it is a silicone elastomer, but it is somewhat harder and has higher tensile strength.
ParPHorm L1938-45
Unlike silicone-based ParPHorm 1800 and ParPHorm S1945-25, ParPHorm L1938-45 is a fluorosilicone FIP gasket material. It is the hardest of the ParPHorm materials, nearly doubling the hardness of ParPHorm S1945-25.
Non-Conductive ParPHorm Materials Comparison
Material | Base Material | Hardness | Tensile Strength | Elongation | Recommended Applications | Curing Method |
---|---|---|---|---|---|---|
ParPHorm 1800 | Silicone | Lowest | Lowest | Highest | Small enclosures requiring low closure force | Moisture |
ParPHorm S1945-25 | Silicone | Medium | Medium | Medium | General purpose environmental sealing | Thermal |
ParPHorm L1938-45 | Fluorosilicone | Highest | Highest | Lowest | Applications requiring higher durability | Thermal |
For more information on the properties of ParPHorm FIP gasket materials, check out the ParPHorm selector tool here.
Learn how Modus is redefining the traditional supplier relationship
Curing Parker Chomerics FIP Gasket Materials
Parker Chomerics FIP gasket materials are all cured either thermally or with moisture. Thermal curing takes place for at least half an hour at temperatures ranging from 100 to 150°C. Moisture curing takes place over at least 24 hours at room temperature. The thermal curing process tends to offer stronger adhesion, while the moisture curing process allows materials to be dispensed onto low-temperature housings.
Here are the Parker Chomerics FIP gasket materials that are cured thermally:
- CHO-FORM 5513
- CHO-FORM 5541
- CHO-FORM 5550
- CHO-FORM 5560
- ParPHorm S1945-25
- ParPHorm L1938-45
And here are the materials that are cured with moisture:
- CHO-FORM 5575
- CHO-FORM 5526
- CHO-FORM 5528
- CHO-FORM 5538
- ParPHorm 1800
Why Choose Modus Advanced for Your FIP Gasket Dispensing?
At Modus Advanced, we've mastered the art and science of FIP gasket dispensing while offering a complete manufacturing ecosystem that accelerates your path to market. Our engineering-first approach means your critical components receive expert attention at every stage.
With Modus, you gain:
- Vertical integration that eliminates shipping between vendors and reduces lead times
- Concurrent manufacturing processes including machining, plating, and thermal material application
- Engineering expertise with over 10% of our staff being engineers who understand your technical challenges
- Enhanced quality control through a single quality system governing the entire process
- Simplified communication with one partner instead of multiple vendors
When one day matters—and we believe it does—our vertically integrated approach doesn't just save time; it helps your innovations reach the field faster, whether that's life-saving medical devices or mission-critical defense systems.
FIP Dispensing ServicesThe Best Manufacturers Use the Best Materials
In manufacturing, materials matter. The best gasket manufacturers know that, and they make an enormous, ongoing effort to work with only the best material manufacturing companies. Parker Chomerics is one of those companies.
With a broad range of options to suit nearly any gasket application, Parker Chomerics form-in-place gasket materials offer a solution for even the most intricate FIP gasket design. If you want the best materials and the best manufacturer for your design, you want to work with Modus Advanced. To get started, give us a call at (925) 960-8700 or contact us online.