What is a Form-in-Place Gasket?
September 14, 2021
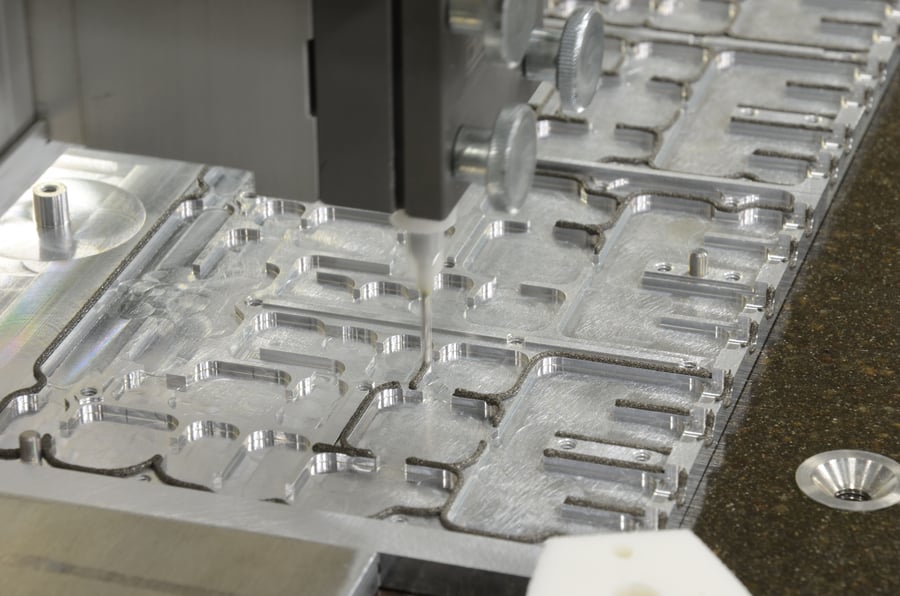
Manufactured with Speed and Precision
The manufacturing capabilities you need and the engineering support you want, all from a single partner.
Submit a DesignKey Points
- Form-in-place (FIP) gaskets are liquid materials dispensed onto a surface that cure to create precise seals and shields for various applications.
- FIP gaskets offer significant advantages including precision in complex spaces, durability in extreme conditions, flexibility in sizing, waste-free production, and reduced assembly steps.
- These gaskets can be made conductive with fillers like silver, nickel, copper, graphite, aluminum, or ferrite to create electromagnetic interference (EMI) shields.
- Common base materials for FIP gaskets include silicone, fluorosilicone, and synthetic rubber, each offering unique strengths for different applications.
- FIP gaskets are widely used in critical industries including military/defense, communications, electronics, aerospace, and medical devices.
- Modus Advanced offers vertically integrated manufacturing through their SigShield™ process, which includes metal housing machining, plating application, gasket dispensing, and installation of additional materials.
You probably already know what a gasket is. It’s simply a seal that fits the space between mating surfaces. As you can imagine, there are dozens of types of gaskets, and form-in-place gaskets are one of them.
So, what is a form-in-place gasket? That’s exactly what we cover below. Read on to learn what a form-in-place gasket is, what it’s used for and the answers to some frequently asked questions about these gaskets.
Want to learn everything there is to know about form-in-place gaskets? We have an in-depth guide that will answer all the questions you have. Check it out.
Visit the Modus Form-in-Place Gasket Resource Center
Form-in-Place Gaskets: Defined
There is a short answer and a long answer to the question, “What is a form-in-place gasket?” Let’s start with the short answer.
Definition
What is a Form-in-Place (FIP) Gasket?
A form-in-place (FIP) gasket is a gasket that is dispensed onto a surface as a liquid. That way, the liquid gasket fills only the space it needs to, and then it is cured either by heat, light, or moisture causing the material to form in place.
That is fairly simple, but there is a lot more to FIP gaskets, of course. You can get a more in-depth FIP gasket definition by learning the answers to some frequently asked questions about FIP gaskets.
FIP Gasket FAQs
Asking what an FIP gasket is makes for a great first step, but there is plenty more to know and understand before you include an FIP gasket in your design. We cover those facts in the FAQ below.
Commonly asked questions about Form-in-Place Gaskets:
- What is an FIP gasket used for?
- What are the advantages of FIP gaskets?
- Can FIP gaskets conduct electricity?
- What are the most common FIP gasket materials?
- Can an FIP gasket manufacturer also machine the metal housing?
- What is the typical curing process for FIP gaskets?
- What tolerances can be achieved with FIP gaskets?
- How do FIP gaskets compare to die-cut or extruded gaskets?
- What design considerations are important when incorporating FIP gaskets?
- What testing methods are used to verify FIP gasket performance?
- What is the typical lifespan of an FIP gasket?
- Can FIP gaskets be repaired or replaced?
- What are the environmental considerations for FIP gaskets?
What Is an FIP Gasket Used For?
FIP gaskets are used to create environmental seals and even electromagnetic interference (EMI) shields. You can find FIP gaskets in use in nearly every industry, but some of the industries that rely on these gaskets the most include the following:
- Military and defense
- Communications
- Electronics
- Aerospace
- Medical devices
From satellites, semiconductors and cellular devices to WiFi routers, radar systems and radiotherapy devices, FIP gaskets are everywhere.
What Are the Advantages of FIP Gaskets?
The reason you can find FIP gaskets in all kinds of devices across all kinds of industries comes down to the unique advantages these gaskets offer. Here are some of the key benefits of FIP gaskets:
- Precision. Because FIP gaskets are dispensed in liquid form, they can fill extremely precise and complex spaces that gaskets produced via other methods cannot.
- Durability. FIP gaskets can withstand extreme heat and cold, corrosion, UV exposure and repeated force. That makes them ideal in a wide variety of engineering applications.
- Flexibility. Although FIP gaskets can fit small spaces with a high degree of precision, they are not limited to these kinds of applications. You can dispense an FIP gasket of almost any size, large or small.
- Waste-free. Unlike other gasket production methods, FIP doesn’t require cutting, binding or any of the other parts of the process that leave wasted gasket materials on the floor. FIP gaskets fill exactly the space they are supposed to and nothing more.
- Reduced assembly steps. Extrusion, die-cutting and similar gasket production methods require someone to apply the gasket to its housing, but FIP gaskets skip this step. That’s because they are dispensed and cured directly on their housing. Reducing assembly steps also reduces production costs.
Can FIP Gaskets Conduct Electricity?
FIP gaskets absolutely can conduct electricity. In fact, they are a common choice for devices that require a conductive gasket. To make an FIP gasket conductive, you have to include a filler material. This is also how you turn an FIP gasket into an EMI shield. Here are the typical materials used to make FIP gaskets conductive:
- Silver
- Nickel
- Copper
- Graphite
- Aluminum
- Ferrite
The conductive filler material you use for your FIP gasket will depend on your device’s needs and the project’s budget. Also, keep in mind that filler materials are sometimes mixed together.
What Are the Most Common FIP Gasket Materials?
Whether you need a conductive gasket or not, you will still have to select a base material. Base materials for FIP gaskets boil down to three choices:
- Silicone
- Fluorosilicone
- Synthetic rubber
Each of these materials offers unique strengths for particular applications. To learn more about the available gasket materials, check out our gasket materials guide.
Learn more about our small bead size capabilities.
Can an FIP Gasket Manufacturer Also Machine the Metal Housing?
If you’re in need of an FIP gasket, you probably need someone to manufacture several other related pieces of your design, such as the metal housing for the gasket. Some manufacturers have the skills and tools to machine metal housings, but many don’t.
At Modus Advanced, we put a premium on vertical integration. Being able to manufacture both FIP gaskets and the other parts required for all kinds of designs not only makes sense, but increases efficiency and lowers costs for our customers. That’s why we developed SigShield™.
SigShield™ allows Modus Advanced to machine your metal housing, apply platings and coatings, dispense the FIP gasket and build and install microwave-absorbing and thermal materials. The end result for you? Half the typical lead time you would expect for such a manufacturing project.
What is the Typical Curing Process for FIP Gaskets?
FIP gaskets can cure through three primary methods: heat curing, moisture curing, and UV light curing. Heat curing typically occurs in an oven at 100-150°C for 30-60 minutes and offers the fastest turnaround and best adhesion properties. Moisture curing happens at room temperature (typically 22°C at 50% relative humidity) and takes approximately 24 hours, making it ideal for temperature-sensitive substrates like coated plastics.
UV curing is the fastest method, often completing in seconds to minutes, but requires special equipment and transparent substrates. The curing method chosen affects both production timelines and the gasket's final performance characteristics.
What Tolerances can be Achieved with FIP Gaskets?
FIP gaskets can achieve impressive precision with typical height tolerances of ±0.1mm for gaskets between 0.8-2.0mm tall. Width tolerances vary based on the material used, with more particle-filled materials producing narrower gaskets. The height-to-width ratio decreases as gasket height increases.
The dispensing process can create gaskets on surfaces as narrow as 0.4mm (though 0.76mm is more common), and the technology allows for incredibly intricate patterns with complex geometries that would be impossible with traditional die-cut gaskets. This precision is particularly valuable in miniaturized electronics and medical devices where space is at a premium.
How do FIP Gaskets Compare to Die-cut or Extruded Gaskets?
FIP gaskets excel in applications requiring complex geometries, miniaturization, or high precision, while die-cut gaskets typically have lower tooling costs for simple shapes produced in high volumes. FIP gaskets eliminate material waste and reduce assembly steps since they're dispensed directly onto the housing, whereas die-cut gaskets require separate assembly. FIP gaskets can be applied to extremely narrow surfaces (as small as 0.4mm) that would be impossible with die-cutting.
However, die-cut gaskets may be more economical for very high-volume production of simple shapes, while extrusions work best for consistent cross-section applications like edge seals. Your specific requirements for precision, volume, and complexity should guide your selection.
What Design Considerations are Important when Incorporating FIP Gaskets?
When designing for FIP gaskets, consider several key factors: First, ensure wall widths are at least 0.4mm wider than your gasket width. Maintain flat dispensing surfaces whenever possible, as any radius or slope can reduce effective wall width. Avoid dispensing in grooves, as this complicates height and width tolerances. Minimize starts, stops, and T-spots in your dispensing path to improve quality and reduce costs. Keep surface height variations under 0.4mm across the part for consistent gasket dimensions. Provide adequate clearance (minimum 0.25mm) between the gasket path and any obstructions to accommodate dispensing equipment.
For three-dimensional dispensing, select high-viscosity materials to prevent slumping on vertical surfaces. Early collaboration with your manufacturing partner will help identify potential issues before production.
Deep Dive: 6 Tips for Designing a Form-in-Place EMI Gasket
Discover six proven engineering tips for designing form-in-place EMI gaskets that enhance electromagnetic shielding performance while reducing manufacturing complexity and production time.
Learn MoreRelated: Design Considerations for Machined Parts
Get 13 design tips for your metal housing, ensuring the best adherence and performance for any FIP materials applied to them.
Learn MoreWhat Testing Methods are Used to Verify FIP Gasket Performance?
FIP gasket performance verification typically includes multiple testing methods based on application requirements. Compression testing measures force deflection and ensures the gasket provides adequate sealing pressure. Adhesion testing verifies the gasket's bond strength to the substrate through pull or peel tests. For conductive gaskets, electrical resistance testing measures volume resistivity and shielding effectiveness.
Environmental testing subjects gaskets to temperature extremes, humidity cycling, salt spray, and UV exposure to verify long-term performance. In specific industries, additional tests may include fluid compatibility, flammability (UL-94), and outgassing tests. Testing protocols often follow industry standards like MIL-DTL-83528 for conductive gaskets or ASTM D395 for compression set characteristics.
What is the Typical Lifespan of an FIP Gasket?
FIP gaskets, particularly those made from high-quality silicone elastomers, typically offer 10-15 years of effective service life in controlled environments. Factors affecting longevity include material selection, operating temperature ranges, chemical exposure, compression levels, and UV exposure. Silicone-based FIP gaskets generally outperform other elastomers in temperature resistance (typically -55°C to +125°C) and maintain their properties longer under compression.
Conductive fillers may affect aging characteristics, with silver-filled materials often providing the most stable long-term conductivity. For critical applications in aerospace, defense, or medical devices, accelerated aging tests can help predict performance over time, allowing engineers to select materials that meet specific lifecycle requirements.
Can FIP Gaskets be Repaired or Replaced?
While FIP gaskets aren't typically repairable in the traditional sense, they can be replaced when necessary. The removal process involves carefully scraping away the old gasket material without damaging the substrate surface, followed by thorough cleaning with an appropriate solvent to remove any residue. Once the surface is properly prepared, a new FIP gasket can be dispensed in the same location.
For particularly challenging applications, some manufacturers offer partial repair options where additional material can be dispensed to reinforce failing sections. The best approach is preventative, working with an experienced FIP gasket manufacturer to ensure proper material selection, dispensing, and curing from the start to maximize gasket lifespan and minimize the need for replacement.
What are the Environmental Considerations for FIP Gaskets?
FIP gaskets perform across a wide range of environmental conditions, but material selection is crucial based on your application requirements. Silicone-based FIP gaskets typically operate from -55°C to +125°C, while fluorosilicone variants offer superior resistance to fuels, oils, and solvents. Consider chemical exposure carefully, silicones excel in weather resistance but may degrade when exposed to certain oils and fuels. UV resistance varies by material, with specially formulated compounds available for outdoor applications. Altitude considerations are important for aerospace applications, as pressure differentials affect sealing requirements.
Humidity resistance is generally excellent for silicone-based gaskets. For medical applications, biocompatibility and sterilization compatibility may require USP Class VI or FDA-approved materials. Always discuss your specific environmental challenges with your FIP gasket manufacturer to ensure optimal material selection.
Modus Advanced: FIP Gaskets Done Right
FIP gaskets provide an affordable, efficient solution to complex gasket problems — when they are done right, that is. At Modus Advanced, doing FIP gaskets right is what we do. We are prepared to partner with you throughout the gasket design process. We can even manage the other phases of design through our SigShield™ process.
Your design deserves a manufacturing partner who can make it perfect. Give your design what it deserves. To speak with an FIP gasket expert at Modus Advanced, (925) 960-8700 or contact us online.
Why Choose Modus Advanced for Your FIP Gasket Dispensing?
At Modus Advanced, we've mastered the art and science of FIP gasket dispensing while offering a complete manufacturing ecosystem that accelerates your path to market. Our engineering-first approach means your critical components receive expert attention at every stage.
With Modus, you gain:
- Vertical integration that eliminates shipping between vendors and reduces lead times
- Concurrent manufacturing processes including machining, plating, and thermal material application
- Engineering expertise with over 10% of our staff being engineers who understand your technical challenges
- Enhanced quality control through a single quality system governing the entire process
- Simplified communication with one partner instead of multiple vendors
When one day matters—and we believe it does—our vertically integrated approach doesn't just save time; it helps your innovations reach the field faster, whether that's life-saving medical devices or mission-critical defense systems.
FIP Dispensing Services