RF Gasket Integration in Secure Military Data Centers: EMI Shielded Government Applications
April 18, 2025
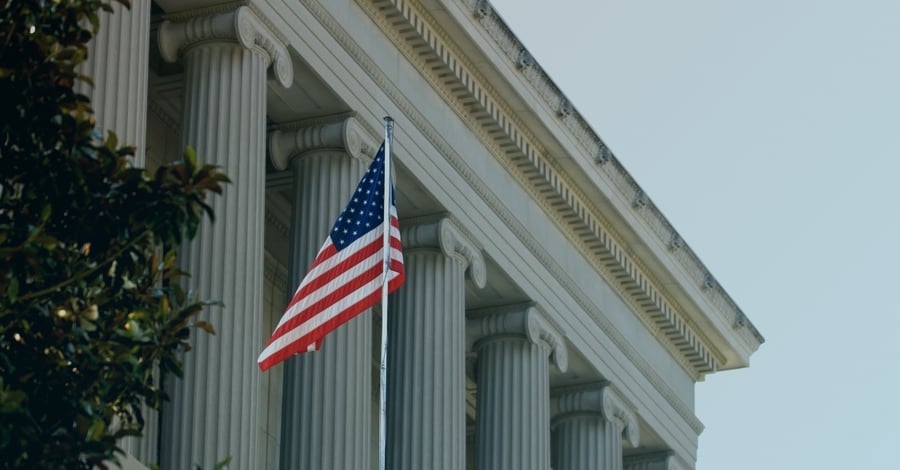
Manufactured with Speed and Precision
The manufacturing capabilities you need and the engineering support you want, all from a single partner.
Submit a DesignKey Points
- RF gaskets serve as critical components in maintaining electromagnetic interference containment in military data centers
- Form-in-place (FIP) gasket technology provides superior sealing for complex enclosure designs
- Military-grade gaskets must meet specific performance standards including temperature resistance, durability, and corrosion resistance
- Vertical integration in manufacturing streamlines the production process and enhances quality control
- Security certifications like CMMC compliance and ITAR registration are mandatory for government contracting
- EMI shielded enclosures for government applications must balance accessibility with maximum signal attenuation
Military data centers represent some of the most tightly secured facilities in our nation's defense infrastructure. These installations don't just require physical security – they demand comprehensive electromagnetic interference isolation to prevent both inadvertent signal leakage and intentional electronic surveillance of sensitive devices. RF gaskets form the invisible shield between sensitive information and potential adversaries.
RF gaskets might seem like minor components, but they represent the critical line of defense in maintaining the electromagnetic integrity of secure facilities. When properly engineered and installed, these specialized sealing solutions prevent electromagnetic interference signals from both entering and escaping shielded environments – a necessity for EMI shielded enclosures for government applications.
Understanding RF Gasket Technology for Defense Applications
RF gaskets are specialized sealing components designed to fill gaps in EMI shielding enclosures. They create conductive bridges between metal surfaces, ensuring continuous conductivity across the entire enclosure. This complete electromagnetic seal prevents signal leakage and external interference – both critical factors in secure military environments.
Military-grade gaskets differ substantially from commercial variants. These specialized components must withstand extreme environmental conditions while maintaining perfect electromagnetic sealing properties. Defense installations require EMI shielded solutions for government applications that can maintain their integrity under pressure, temperature variations, and potential physical impacts.
Form-in-place (FIP) gasket technology represents the highest tier of RF gasket implementation for military data centers. These gaskets are dispensed as liquid silicone rubber filled with conductive particles directly onto the housing surface, then cured in place. This approach creates a perfect seal conforming to even the most complex enclosure designs.
Critical Performance Requirements for Military-Grade RF Gaskets
Military-grade RF gaskets must meet stringent performance standards to qualify for EMI shielded applications in government facilities:
- Temperature Resilience: Must maintain integrity in environments ranging from -65°F to +257°F
- Corrosion Resistance: Must resist galvanic corrosion when paired with various metals
- Chemical Resistance: Must withstand exposure to cleaning agents, solvents, and fuels
- Compression Force: Must provide consistent EMI shielding at specified compression levels
- Shielding Effectiveness: Must achieve a minimum of 100dB attenuation across specified frequency ranges
- Durability: Must maintain performance through thousands of compression cycles
These exacting requirements guarantee that EMI shielded enclosures for government applications will maintain their integrity throughout their operational lifespan. The security of classified information depends on this consistent performance.
Manufacturing Challenges for Military-Grade RF Gaskets
Creating RF gaskets for EMI shielded government applications presents unique manufacturing challenges. These specialized components must meet precise dimensional tolerances while maintaining consistent electrical properties throughout the entire gasket profile. This requires specialized manufacturing capabilities and rigorous quality control processes.
The integration of RF gaskets into military data center infrastructure demands a comprehensive understanding of both materials science and electromagnetic theory. Manufacturers must select appropriate conductive fillers and base elastomers that meet military specifications while maintaining manufacturability at scale.
Material Selection Considerations for Government Applications
Material selection represents one of the most critical decisions in developing EMI shielded solutions for government applications. The table below outlines common conductive fillers used in military-grade RF gaskets and their key properties:
Conductive Filler | EMI Shielding Effectiveness | Galvanic Compatibility | Cost Factor | Best Applications |
Silver/Aluminum | Excellent (>100dB) | Good with aluminum | High | Mission-critical enclosures |
Silver/Copper | Excellent (>100dB) | Fair with aluminum | High | Military communications |
Silver/Nickel | Very Good (90-100dB) | Excellent with most metals | Very High | Aerospace applications |
Nickel/Graphite | Good (80-90dB) | Excellent with aluminum | Medium | General military electronics |
Material selection must consider not just electromagnetic performance but also long-term reliability within the intended operating environment. EMI shielded solutions for government applications must balance immediate performance with lifecycle durability.
Engineering Expertise in Military-Grade RF Gasket Design
Designing effective RF gaskets for EMI shielded government applications requires specialized engineering knowledge. The Modus Advanced engineering team, representing over 10% of our total staff, brings decades of combined experience in military specification compliance and EMI shielding design.
This engineering-first approach ensures that EMI shielding designs for government applications and electronic device address not just immediate performance requirements but also manufacturing efficiency and long-term reliability concerns. Our engineers partner with defense contractors from initial concept through final production.
What does a Design for Manufacturing review look like? Read about it here.
Critical Design Considerations for Military Data Centers
Effective RF gasket design for secure military data centers requires attention to several key factors:
- Enclosure Design Compatibility: Gasket designs must account for enclosure materials, surface finishes, and dimensional tolerances
- Installation Method: Gaskets must be designed for efficient installation while maintaining shielding integrity
- Maintenance Requirements: Designs must consider periodic maintenance and replacement procedures
- Thermal Management: Gaskets must accommodate thermal expansion without compromising shielding
- Vibration Resistance: Installations must maintain shielding effectiveness despite operational vibration
- Integration With Other Systems: Gaskets must coordinate with HVAC, power, and data systems
Addressing these considerations ensures that EMI shielded solutions for government applications perform reliably throughout their operational lifespan. This design expertise represents a crucial differentiator when selecting manufacturing partners.
The Vertical Integration Advantage in Military RF Shielding
Vertical integration represents a significant advantage when manufacturing EMI shielded enclosures for government applications. By controlling multiple manufacturing processes under a single roof, vertically integrated manufacturers can ensure consistent quality while reducing production timelines.
The Modus Advanced approach to vertical integration includes machining, plating, FIP gasket dispensing, and final assembly – all within our secure facilities. This comprehensive manufacturing ecosystem ensures rigorous quality control throughout the production process while eliminating risks associated with transportation between multiple vendors.
The SigShield Process: Complete RF Shield Manufacturing
The proprietary SigShield process exemplifies the vertical integration advantage for EMI shielded solutions in government applications. This process includes:
- Precision CNC machining of aluminum housings to military specifications
- Conductive plating application under strict quality control
- Form-in-place gasket dispensing with military-grade conductive materials
- Integration of RF absorbers and thermal management materials
- Comprehensive quality testing including shielding effectiveness verification
This end-to-end manufacturing approach eliminates the coordination challenges and quality risks associated with using multiple vendors. For EMI shielded projects in government applications, this streamlined process translates to faster deployment with higher reliability.
Security and Compliance in Military RF Gasket Manufacturing
Security considerations extend beyond the physical characteristics of RF gaskets for government applications. Manufacturing partners must maintain rigorous security protocols and comply with stringent government regulations throughout the design and production process.
Modus Advanced maintains comprehensive security certifications including ITAR registration, CMMC compliance preparation, and AS9100 quality management systems. These credentials ensure that EMI shielded projects for government applications maintain appropriate security controls throughout the manufacturing process.
Essential Security Protocols for Defense Manufacturing
Securing the manufacturing process for EMI shielded solutions in government applications requires:
- ITAR registration and compliance
- Controlled facility access with security clearance verification
- Secure data management systems with appropriate encryption
- Compartmentalized manufacturing information
- Regular security audits and compliance verification
- Thorough personnel screening and ongoing security training
These security protocols protect sensitive design information while ensuring compliance with government regulations. For EMI shielded projects in government applications, this security framework represents an essential element of the manufacturing partnership.
Partnering with Modus Advanced for a Mission-Critical EMI Shielding Solution
Selecting the right manufacturing partner for EMI shielded solutions in government applications represents a mission-critical decision. The ideal partner combines technical expertise, manufacturing capabilities, security credentials, and a proven track record in defense applications.
Modus Advanced brings together all these essential elements – engineering expertise, vertical integration, security credentials, and defense manufacturing experience. Our team understands that EMI shielded enclosures for government applications protect our nation's most sensitive information and critical infrastructure.
When one day matters – and in defense applications, it always does – choosing a partner with comprehensive capabilities makes the difference. Your secure military data center deserves nothing less than excellence in RF gasket design and implementation.