Selecting the Right RF Gasket Material for Defense Applications
April 19, 2025
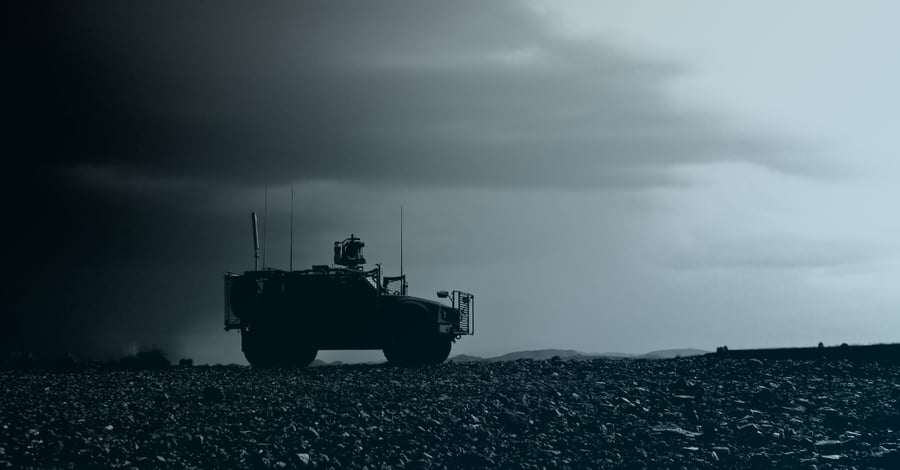
Manufactured with Speed and Precision
The manufacturing capabilities you need and the engineering support you want, all from a single partner.
Submit a DesignKey Points
- Defense applications demand RF gasket material that can withstand extreme environments while maintaining critical shielding effectiveness.
- Material selection must account for factors including temperature extremes, chemical exposure, vibration resistance, and galvanic compatibility.
- Silver-filled silicones provide superior conductivity but nickel-graphite options offer better corrosion resistance and cost-effectiveness.
- Specialized fluorosilicone compounds ensure reliability in environments with fuel and solvent exposure.
- Working with an engineering partner who understands defense requirements can significantly reduce development time and ensure compliance with military specifications.
RF gasket material form the critical interface between components in defense systems where signal integrity can mean the difference between mission success and failure. For defense engineers tasked with protecting sensitive electronics in battlefield conditions, choosing the right RF gasket material is a decision that directly impacts operational readiness and soldier safety.
The defense industry presents unique challenges for RF gasket selection that commercial applications rarely encounter. These include extreme temperature fluctuations, prolonged exposure to harsh chemicals, constant vibration, and the need to meet stringent military specifications while maintaining effective shielding against increasingly sophisticated electronic warfare tactics.
In this guide, we'll examine the crucial factors defense engineers must consider when selecting RF gasket materials, explore the most effective material options for military applications, and provide practical guidance for ensuring your RF shielding gasket solution meets the demanding requirements of defense systems.
Critical Factors in RF Gasket Material Selection for Defense
Before selecting specific RF gasket materials for defense applications, engineers must understand the unique demands of military environments. Each factor significantly impacts material performance and longevity in field conditions.
Temperature Resistance
Defense equipment operates in some of the world's most extreme environments, from desert heat exceeding 140°F to arctic conditions below -40°F. The RF gasket material must maintain its shielding effectiveness and mechanical properties across this entire range.
Key Temperature Considerations:
- Silicone-based RF gasket materials typically offer excellent stability between -67°F and +257°F
- For extreme conditions, specialized fluorosilicone compounds extend this range
- Temperature cycling in aircraft systems requires materials that accommodate expansion/contraction
- Compression set retention across the temperature range is critical for long-term performance
Temperature cycling presents a particular challenge in applications like aircraft systems, where rapid changes can cause differential expansion and contraction. The ideal RF gasket material must accommodate these changes without losing compression set or developing leakage paths.
Chemical Resistance
Military equipment encounters a wide range of chemicals, from jet fuels and hydraulic fluids to decontamination agents and saltwater exposure. Each presents potential degradation mechanisms for RF shielding gasket materials.
Common chemical exposures in defense applications include:
- Aircraft/vehicle fuels (JP-8, diesel, gasoline)
- Hydraulic fluids (phosphate esters, synthetic oils)
- Cleaning/decontamination agents
- Salt spray/fog (maritime environments)
- Lubricants and coolants
Fluorosilicone RF gasket materials offer superior resistance to fuels, oils, and many solvents common in defense applications. For extreme chemical environments, specialized compounds containing fluorocarbons may be necessary, though they often come with trade-offs in compression properties and cost.
Vibration and Shock Resistance
From vehicle-mounted systems to aircraft and naval applications, defense equipment experiences continuous vibration and intermittent shock. The RF gasket material must maintain continuous contact under these conditions.
Vibration resistance factors include:
- Low-durometer silicones (30-50 Shore A) provide excellent vibration dampening
- Material resilience prevents permanent deformation under continuous stress
- Proper groove design and compression ratio maintain contact during vibration
- Hybrid designs combining elastomers with mechanical retention for extreme conditions
The design often matters as much as the material itself. Proper groove dimensions, sufficient compression ratio, and appropriate material resilience all contribute to maintaining shield effectiveness under vibration conditions.
Galvanic Compatibility
When dissimilar metals come into contact in the presence of moisture, galvanic corrosion can quickly degrade both the RF gasket material and the housing components. This is particularly critical in naval and coastal defense installations.
Galvanic considerations include:
- Nickel-graphite filled materials offer excellent compatibility with aluminum
- Silver fillers may accelerate corrosion of aluminum in humid environments
- Protective platings affect galvanic interactions and must be considered
- Position in the galvanic series determines corrosion potential
Protective platings and coatings can mitigate galvanic concerns but must be factored into the overall shielding design. An RF gasket material that works perfectly with bare aluminum may perform poorly against chromate conversion coatings or specialized MIL-spec finishes.

Most Effective RF Gasket Materials for Defense Applications
The defense industry relies on several specialized materials that balance conductivity, environmental resistance, and longevity. Below is a comparison of the most commonly specified RF gasket materials for defense applications:
RF Gasket Material | Shielding Effectiveness | Temperature Range | Chemical Resistance | Relative Cost | Best Applications |
Silver-Filled Silicones | Excellent (10 kHz-40+ GHz) | -55°C to +125°C | Good | High | Mission-critical communications, EW systems, high-frequency applications |
Nickel-Graphite Compounds | Very Good (up to 18 GHz) | -55°C to +125°C | Very Good | Moderate | Aluminum housings, general defense electronics, cost-sensitive applications |
Fluorosilicone Elastomers | Very Good | -55°C to +135°C | Excellent | High | Fuel/solvent exposure, aircraft systems, naval applications |
Fabric-Reinforced Elastomers | Good | -40°C to +125°C | Good | Moderate | Large apertures, access panels, high mechanical stress areas |
Form-in-Place (FIP) | Very Good | -40°C to +125°C | Good to Excellent | Moderate | Complex geometries, miniaturized electronics, production efficiency |
Silver-Filled Silicones
Silver-filled silicone remains the gold standard for RF gasket materials in critical defense applications where maximum shielding effectiveness is required. These compounds typically contain 60-80% silver particles by weight.
Advantages include:
- Highest electrical conductivity of any metal filler
- Superior shielding across broad frequency range (10 kHz to 40+ GHz)
- Excellent aging characteristics
- Resistance to oxidation
The primary drawbacks include high cost and potential for silver sulfidation in high-sulfur environments. However, for mission-critical applications where performance outweighs cost considerations, silver-filled RF gasket materials remain unmatched.
Nickel-Graphite Compounds
Nickel-graphite compounds offer an excellent balance of performance and value for many defense applications. These RF gasket materials provide effective shielding up to 18 GHz while offering superior corrosion resistance.
Advantages include:
- Excellent galvanic compatibility with aluminum
- Superior corrosion resistance
- Cost-effective compared to silver-filled options
- Good shielding performance for most applications
Modern nickel-graphite formulations have dramatically improved their shielding performance, with some newer compounds approaching 90% of silver's effectiveness at a fraction of the cost. This makes them increasingly popular for defense applications where budget constraints exist without compromising mission requirements.
Fluorosilicone Elastomers
When defense systems face exposure to fuels, hydraulic fluids, and solvents, standard silicone-based RF gasket materials often fall short. Fluorosilicone compounds address this limitation while maintaining essential shielding properties.
Chemical Agent | Standard Silicone | Fluorosilicone |
Jet Fuel (JP-8) | Poor | Excellent |
Hydraulic Fluid | Poor | Excellent |
Cleaning Solvents | Poor to Fair | Good to Excellent |
Salt Spray | Good | Excellent |
UV Exposure | Good | Excellent |
The primary trade-off comes in slightly reduced compression set performance compared to standard silicones. However, advances in compound formulation have minimized this gap, making fluorosilicone-based RF gasket materials suitable for most defense applications requiring chemical resistance.
Visit the full resource center on everything RF Gaskets
Application-Specific Considerations for Defense
Beyond general material properties, defense applications often have specialized requirements that influence RF gasket material selection.
Airborne Systems
Airborne defense systems face unique challenges including rapid pressure changes, ozone exposure, and weight constraints. RF gasket material selection must account for all these factors.
Critical requirements for airborne rf gaskets:
- Weight optimization (low-density compounds preferred)
- Pressure differential sealing capability
- Ozone resistance at high altitudes
- Temperature cycling performance
- Vibration dampening during flight operations
For avionics operating at high altitudes, RF gasket materials must resist corona discharge and ozone attack. Specialized anti-ozone additives and proper material formulation prevent degradation in these conditions, extending operational life in airborne environments.
Ground Vehicle Electronics
Ground vehicles present challenges including extreme dust exposure, continuous vibration, and potentially explosive atmospheres. RFI gasket materials must remain effective under these harsh conditions.
Ground vehicle challenges include:
- Continuous shock and vibration
- Extreme dust and particulate exposure
- Wide temperature cycling
- Potential exposure to water fording
- EMI from vehicle electrical systems
Particle-filled form-in-place (FIP) gaskets often provide the best solution for intricate housings in ground vehicles. These RF gasket materials can be applied precisely to complex geometries while maintaining excellent environmental sealing properties.
Naval and Maritime Defense Equipment
Maritime environments combine salt spray, high humidity, and constant vibration, creating one of the most challenging scenarios for RF gasket materials.
Maritime environmental factors to consider:
- Constant salt spray exposure
- High humidity (up to 100% RH)
- Galvanic corrosion risk
- Fungal/microbial growth potential
- Temperature cycling with condensation
Fluorosilicone compounds with nickel-aluminum fillers provide excellent salt spray resistance while maintaining shielding effectiveness. This RF gasket material combination prevents the accelerated corrosion that can occur in maritime environments.
Working with an Engineering Partner
Selecting the right RF gasket material for defense applications often requires specialized expertise beyond what's available in-house. Working with an experienced engineering partner can accelerate development while ensuring compliance with military specifications.
Benefits of Engineering Partnership for RF Gasket Selection
Modus Advanced brings together extensive RF gasket material knowledge and defense industry experience. Our engineering team understands both the technical requirements and practical constraints of military applications, helping defense contractors select optimal materials for their specific needs.
Partnership Advantages:
- Access to materials expertise without maintaining in-house specialists
- Faster material selection through experienced guidance
- Design for Manufacturability (DfM) to prevent production issues
- Rapid prototyping capabilities for material testing
- Compliance guidance for military specifications
The Design for Manufacturability (DfM) process plays a crucial role in RF gasket material selection. By involving manufacturing engineers early in the design process, potential issues with material compatibility, manufacturing limitations, and long-term reliability can be identified and addressed before they impact production.
Key Questions When Selecting RF Gasket Materials
When evaluating RF gasket materials for defense applications, consider these critical questions:
- Environmental Exposure: What temperature extremes, chemicals, and environmental conditions will the gasket encounter?
- Shielding Requirements: What frequency range must be shielded, and to what attenuation level?
- Service Life: What is the expected operational lifetime of the system?
- Mechanical Factors: What compression forces are available, and will the gasket experience repeated compression cycles?
- Housing Materials: What materials will the gasket contact, and are there galvanic compatibility concerns?
- Manufacturing Process: Which process (die-cutting, molding, form-in-place) best suits your production volume and geometry?
- Military Specifications: Which specific MIL-STD requirements apply to your application?
- Cost Constraints: Does the application justify premium materials, or are cost-effective alternatives viable?
Answering these questions helps narrow the field of appropriate RF gasket materials for your specific defense application.
Ensuring Mission Success Through Optimal RF Gasket Material Selection
Selecting the right RF gasket material for defense applications requires balancing multiple factors including electrical performance, environmental resistance, mechanical properties, and compliance with military specifications.
At Modus Advanced, we understand that when lives depend on your technology, every component matters – including the RF gasket material that ensures your systems perform as designed, no matter what challenges they face. Our engineering team is ready to help you select and implement the optimal RF shielding solution for your specific defense application.
If you're working on a defense project requiring specialized RF gasket materials, contact our engineering team today. We'll help you navigate the complex landscape of material options to find the solution that meets your technical requirements, timeline, and budget.