SigShield™ vs. Traditional RF Shield Production
May 10, 2021
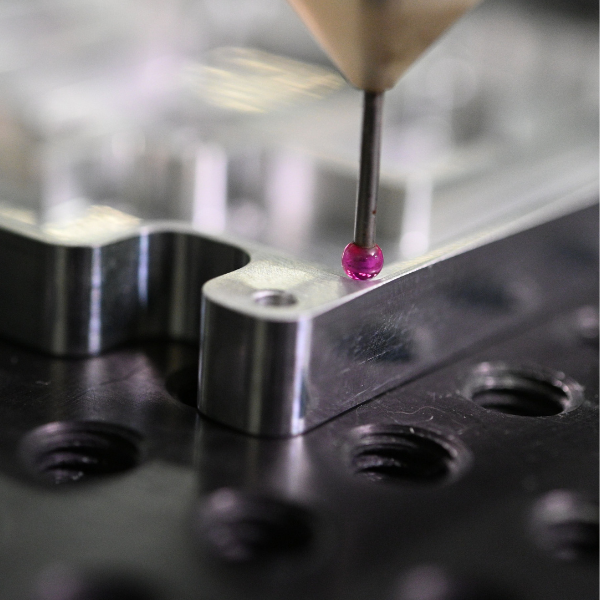
Manufactured with Speed and Precision
The manufacturing capabilities you need and the engineering support you want, all from a single partner.
Submit a DesignKey Points
- SigShield™ offers a vertically integrated RF shield production process that combines four manufacturing processes under one roof: CNC machining, plating/coating, form-in-place gasket dispensing, and addition of thermal materials/RF absorbers.
- Traditional RF shield production typically requires multiple vendors for different processes, resulting in longer lead times, higher shipping costs, and increased project management complexity.
- SigShield™ delivers completed RF shields weeks faster than the traditional route for procuring a completed RF shield.
- The streamlined SigShield™ process reduces shipping costs to approximately 1/4 of traditional methods by eliminating multiple shipments between vendors.
- Working with a single manufacturing partner for RF shield production eliminates communication issues between vendors, reduces quality control problems, and minimizes schedule disruptions that commonly occur in multi-vendor processes.
We are often asked to explain what makes our SigShield™ process different than traditional RF shield production. It can be hard to compare the two head to head when just looking at a quote because the process we’ve built is so unique that most people don’t even know something like it exists.
So, without further ado: What does a SigShield quote get you when compared with a traditional RF shield production quote?
- 4x the Manufacturing Processes Under One Roof (machined RF shield, FIP gasket, and thermal pads and RF absorbers as needed)
- Shorter than Typical Lead Times
- 1/4 the Freight Cost
- 100% Fewer Headaches
- Design for Manufacturability
- Reduced Risk
4x the Manufacturing Processes Under One Roof
Simply put, a SigShield quote covers four times more than most other quotes you see for RF shields. At Modus, we have built a vertically integrated process that results in a turnkey RF shield, ultimately, saving you time and money.
A SigShield quote includes the following manufacturing processes:
- CNC machined part
- Plating and other coatings
- Form-in-place (FIP) gasket dispensing
- Addition of optional thermal materials, RF absorbers, inserts and/or helicoils, as needed in your design
You will likely be comparing this quote to other vendors who are quoting just a single step in the process.
This means that most of the time you’ll have to add four separate quotes from other vendors together to actually compare the cost of production to that of the SigShield quote.
SigShield: So Much More than RF Shielding.
Shorter than Typical Lead Times
The traditional process for producing RF shields can take up to 2-3 months. At Modus, we've been able to deliver a complete product weeks faster. With this said, complexity of the part will drive lead time.
The graphic above shows the two timelines stacked up next to each other for a more visual reference.
Under the traditional method, a typical timeline to produce a final product may look something like this:
- CNC Machining: Vendor #1 is responsible for CNC machining of an RF shield. If this is their first time running a part, they will need to set everything up which can take upwards of a week. Once the part is ready to run, the machining can be done in a matter of a few days depending on the complexity of the part and machine capacity.
- Transition: Vendor #1 sends the parts to vendor #2 for plating.
- Plating and/or Coating: This process usually takes the vendor about one week to complete. Vendor #2 then sends the plated parts back to Vendor #1 for inspection. Transition: Now comes an additional transition between vendors to move to the next step in the process. Vendor #1 will send the parts to vendor #3 for gasketing.
- Form-In-Place Gasket Dispensing: Vendor #3 is now responsible for dispensing FIP gaskets onto the machined part. This process will usually take a vendor about 1-2 weeks to complete.
- Transition: Up next we have another transition phase in which vendor #3 ships the parts back to vendor #1 for inspection.
- Addition of Thermal Materials and/or RF Absorbers: This step may or may not be needed depending upon your design. But in the cases where it is needed, usually a fourth vendor will be responsible for cutting the materials to size and shipping to either Vendor #1 or the final customer for assembly. Most of the time if you order the materials you need early in the process you can have them ready as soon as you are ready for this process to start (we recommend making sure you have the materials ordered by your manufacturing partner at least four weeks in advance). This process usually takes the vendor about a week to cut, package and ship the materials.
- Final Shipping: Once vendor #1 has complete parts they finally ship to the end customer where an additional inspection is done.
Visit the Modus RF Shielding Resource Center
When you add up all the steps, and factor in all of the shipping and transition times, this process often takes upwards of 3 months.
And now let’s take a look at what is different with the SigShield™ process timeline:
- CNC Machining: We will start with CNC machining of part. Similar to above: If this is our first time running a part, we will need to set everything up which can take upwards of a week. Once the part is ready to run the machining can be done in a matter of a few days depending on complexity and capacity..
- Plating and/or Coating: The parts then move to plating. Similar to the timeline above, this process usually takes about a week to complete.
- Form-In-Place Gasket Dispensing: Once the machining and plating are completed, we do an internal inspection before moving it directly to FIP dispensing. Because we already have everything we need during the machining process, we can actually be programming the FIP dispensing machines while CNC machining is happening. This means that when we shift gears to dispensing form-in-place gaskets, it only takes us a couple of days to complete (rather than the 1-2 weeks mentioned in the timeline above).
- Addition of Thermal Materials and/or RF Absorbers: In the cases where this step is needed, we can prepare the materials while the previous steps are in progress and assemble them directly into the final part in a matter of two or three days after FIP dispensing has been completed.
- Quality Inspections: We do detailed quality inspections, that are built to adhere to your standards, between each step in the process and before the final part is shipped to you.
- Final Shipping: We ship a complete part to you with all required documentation!
The SigShield™ process can usually be completed weeks faster than the traditional route, depending upon part complexity, and order volume.
Read Everything You Need To Know About RF Shielding
1/4 the Freight Cost
Returning to the graphic above, each time a shipping step is introduced into the process, you add costs to your total project.
Essentially the traditional method involves shipping at a minimum of four times throughout the process (once between each manufacturing step). In many cases, customers actually ship the product back to their own facility to complete an inspection in between each step, which actually means you are shipping parts upwards of eight times across the life of the process.
With SigShield™ you pay for shipping one time, at the end of your project. This means that you are saving at minimum 1/4 of the freight cost and potentially up to 1/8 of the freight cost over the total life of production.
100% Fewer Headaches
One of the biggest problems with the traditional method to produce a finished RF shield is the amount of effort required for you to manage every step in the process. The more vendors you have involved in production, the more headaches and frustration you’ll run into.
We saw the traditional way RF shields were being manufactured and we created SigShield specifically because we saw how much frustration it was causing our customers. We regularly saw issues like:
- CNC machined housing that wasn’t up to quality standards, and thus we had to send it back to the previous vendor for fixes before we could begin the process of form-in-place gasket dispensing.
- Missed deadlines by one of the vendors in the process, throwing off the production schedule for all the following vendors in the chain, significantly increasing lead times.
- Miscommunications between vendors, or bottlenecks in communications as the customer had to manage all the moving pieces between vendors.
Ultimately, the fewer vendors involved, the faster we can move. Our SigShield process delivers a turnkey solution with speed and precision, while at the same time, greatly reducing risk.
The Bottom Line
Ultimately, the SigShield™ process saves you time, money and stress. And who wouldn’t want all of that from a single vendor?