Sourcing FIP Gaskets: Vertically-Integrated Manufacturer vs. Multi-Source Supply Chain
October 31, 2017
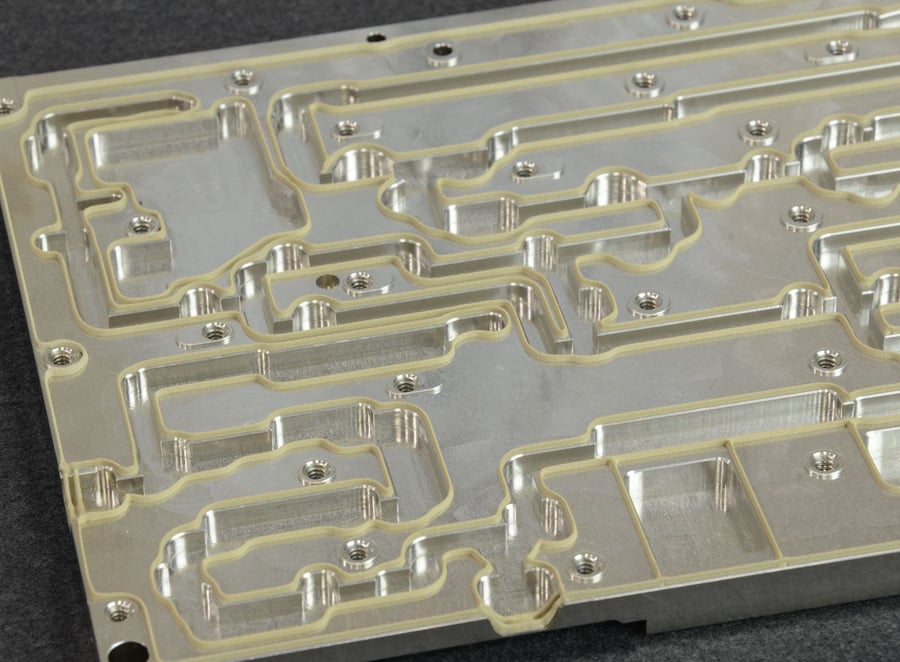
Manufactured with Speed and Precision
The manufacturing capabilities you need and the engineering support you want, all from a single partner.
Submit a DesignKey Points
- Mechanical Engineers face tight deadlines when designing RF shields with form-in-place gaskets, with standard multi-step manufacturing typically requiring 4-6 weeks lead time.
- Vertically-integrated manufacturers can reduce lead times to just 1-3 weeks by housing multiple processes under one roof, eliminating redundancies in quoting, purchasing, communication, and shipping.
- Vertical integration enables concurrent engineering practices where teams work simultaneously across specialties rather than waiting for each manufacturing step to complete before starting the next.
- Quality improves in vertically-integrated systems as components remain with the same team throughout production, giving manufacturers greater visibility and stake in the finished product.
- When managing cost, quality, speed, and risk in manufacturing projects, quality and risk maintenance are the most critical factors, and vertically-integrated manufacturing provides better control of these elements.
Mechanical Engineers often face tight deadlines when trying to design new RF shields with form in place gaskets. Projects that seem simple can quickly become complex when multiple components must come together in a timely manner to achieve production goals. Cost overruns, delays, defects, and poor risk control present significant barriers to project success.
One of the biggest challenges mechanical engineers face is the standard four to six-week lead times typical of multi-step CNC-milled RF shields. Component manufactures often view the standard lead times as necessary to mitigate risk and improve quality and cost. However, manufacturers that employ high-quality, vertically-integrated processes can create excellent quick-turn parts by reducing lead times to as little as one to three weeks.
Visit the Modus Form-in-Place Gasket Resource Center
What is high-quality vertically-integrated manufacturing and how can the concept optimize project success through quick-turn parts?
The Economist defines vertical integration as “the merging together of two businesses that are at different stages of production.“ In manufacturing, vertical integration includes combining the production of base components and additional processes for those same components all under one roof. Vertically-integrated manufacturing benefits engineers because it allows manufacturers to focus on two things: concurrent engineering practices and quality processes.
Concurrent Engineering Practices: Dr. David Anderson, author of Design for Manufacturability, describes concurrent engineering as the practice of simultaneously “developing products and their manufacturing processes in multifunctional teams with all specialties working together from the earliest stages.” Greater investment in team processes at the start, especially through engaging all production stakeholders, saves time and in the end, can decrease the total landed cost.
Concurrent engineering principles can also be applied to a manufacturing environment through vertical integration. Typically, non-integrated manufacturers will not begin secondary process work on a part until the part arrives at their shop and is placed in the queue. While it’s probably a best practice to wait until a part is in-house before programming the gasket for example, it does add to the total production time. However, in vertically integrated manufacturing, teams can work together across multiple specialties to create a faster, more integrated workflow and improved communication. For example, once the CNC milling programming and fixturing is done and a first article RF shield has been approved, the team can begin immediately developing the next step while the rest of the shields are milled. This substantially reduces lag time between parts and speeds up production.
Quality Processes: In vertically-integrated systems, components remain with the same team for more, if not all, of production. Manufacturers who are performing multiple processes have greater visibility of product realization. They also have more of a stake in the finished product. Manufacturing production teams can anticipate problems up and downstream and troubleshoot early in the process with customer engineers. Greater control allows manufacturers to reduce errors and improved methodology. Sound methodology becomes the focus in vertically-integrated manufacturing. Quality improves and risk is reduced.
Conventional manufacturing gives engineering teams two production route options: Teams can contract directly with multiple vendors (Option A) or teams can work with one primary vendor who subcontracts out to all secondary vendors (Option B). With vertical integration (Option C), one vendor directly performs multiple production processes. Compare traditional, non-integrated parts production environments against a vertically-integrated one to see how the effects add up:
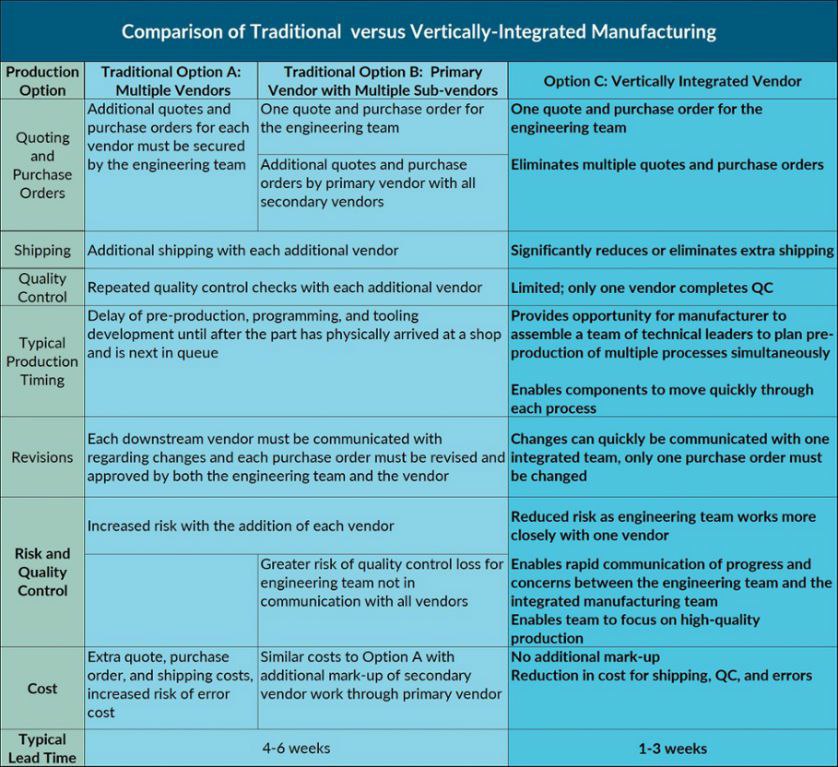
An example workflow is diagrammed below to demonstrate the comparisons in action. Time lost through additional processes is highlighted through dashed lines.
In an article written for the Harvard Kennedy School of Business, Dr. Paul Dorsey notes management of cost, quality, speed, and risk is vital to project success. Dr. Dorsey states, “It is not possible to have the best of all four factors. Specifically, you cannot have a system built inexpensively, of high quality, built quickly, and with little or no risk of failure.” He argues a system can achieve any two of the four aspects well, leaving the other two to be managed. Of the four factors, quality and risk maintenance are the most critical.
By housing multiple processes all under the same roof, vertically-integrated manufacturers are able to be intimately involved in and control the production process from start to finish. These single-source vendors eliminate redundancy in quoting, purchase orders, communication, and quality control along with extra shipping and lead time in production. Additionally, direct control over manufacturing means they have the ability to control quality and risk, and ultimately, cost. Those benefits are passed along to the engineering teams, allowing engineers to optimize project success.
What additional processes can a vertically-integrated RF shield manufacturer provide to add value to their in-house supply chain?
Why Choose Modus Advanced for Your FIP Gasket Dispensing
At Modus Advanced, we've mastered the art and science of FIP gasket dispensing while offering a complete manufacturing ecosystem that accelerates your path to market. Our engineering-first approach means your critical components receive expert attention at every stage.
With Modus, you gain:
- Vertical integration that eliminates shipping between vendors and reduces lead times
- Concurrent manufacturing processes including machining, plating, and thermal material application
- Engineering expertise with over 10% of our staff being engineers who understand your technical challenges
- Enhanced quality control through a single quality system governing the entire process
- Simplified communication with one partner instead of multiple vendors
When one day matters—and we believe it does—our vertically integrated approach doesn't just save time; it helps your innovations reach the field faster, whether that's life-saving medical devices or mission-critical defense systems.
FIP Dispensing Services