3 Reasons to Choose Die Cut Gaskets
June 13, 2017
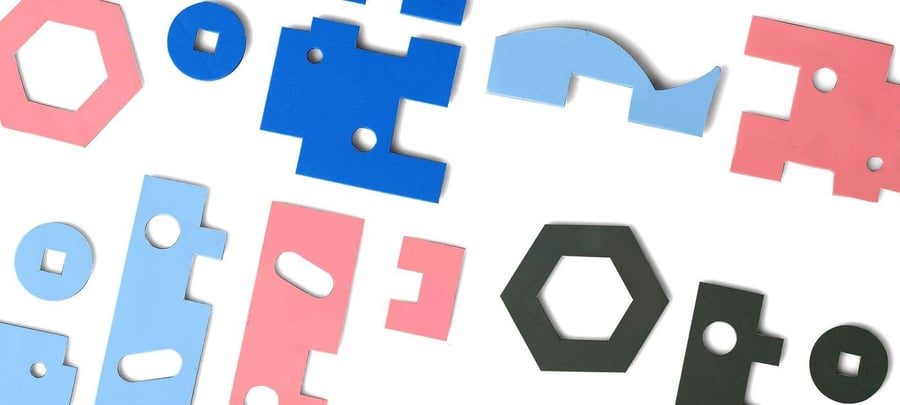
Manufactured with Speed and Precision
The manufacturing capabilities you need and the engineering support you want, all from a single partner.
Submit a DesignDie cut gaskets for EMI shielding and other applications is a reliable, cost-effective, and custom gasket manufacturing method. As a custom gasket manufacturing technique, die cutting combines proven technologies with efficient approaches to gasket fabrication. Specific die cutting techniques vary, but most methods involve two core components: a metal tool called the die, and the die cutting machine itself. Die cutting is a smart choice for connector gaskets, but it's also used to produce many other types of seal and insulation.
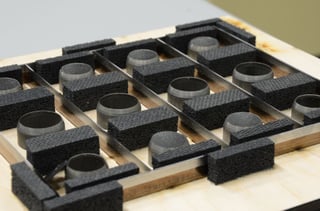
Die cutting can create a range of custom gasket sizes with tight tolerances. Part volumes can range from low-volume prototypes to high-volume production runs. Features such as clean edges and bolt holes with specific radii are readily achievable. Die cutting has many advantages, but there are three important reasons to choose a die cut gasket for your next project.
- Low setup costs
- Supply chain flexibility
- Design changes without major tooling expenses
Let's look at each one...
Looking for more information on Nolato products?
Click the link below to view product info from the Nolato Trishield Product Guide:
1. Low Setup Costs
Die cut gaskets are produced on rotary or flatbed equipment with features that help to reduce setup costs. Automated handling systems can replace manual material feeding. Tracking systems can detect variations in material thickness. Machine vision systems can support part registration and alignment. Your choice of a die can help control project costs, too. By balancing the tool type with the material type, part features, and gasket die cutting technique, you can source cost-effective die cut gaskets.
Image: Solid milled die and die cut sheets
Read the Guide: DESIGNING FOR SUCCESS –
DIE CUT GASKETS
Flatbed die cutting uses steel rule dies, solid milled dies, and male/female or compound dies to cut or punch sheets of gasket material . Steel rule dies are the least expensive type. They're a good choice for low-volume production, especially when you need dies in just a few days. Solid milled die costs more and takes longer to make, but they provide increased cutting accuracy with both larger and smaller parts. Male/female dies or compound dies are ideal when fine details and very tight tolerances are required.
Image: Die cut operator
Rotary die cutting is used mainly with rolls or webs of gasket materials. It's a great choice for high-volume gasket production, especially with thin-gauge materials such as foils, films, or papers. Rotary dies are more expensive than steel rule dies and solid milled dies, but remember that part costs fall as part volumes rise. Rotary dies for high-volume die cutting are comparable in price to male/female dies, but rotary equipment also reduces material waste while speeding production.
Digital die-less cutting doesn't use metal dies at all, but is worth mentioning because it's usually grouped with other die cutting techniques. To create gaskets with exceptional edge quality, digital die-less cutting uses reciprocating knives instead of metal dies. Die cutters who maintain a complete inventory of these knives don't have to order tooling. Customers who need quick-turn gaskets don't have to wait for tools to arrive either. Typically, digital die cutting is used with prototyping.
2. Supply Chain Flexibility
Die cutting is a global industry where customers can choose from companies in nearby communities, other U.S. states, or even different countries. Shorter supply chains can reduce some expenses, but many custom gasket cutters have similar material, labor, and overhead costs. Die cutters differ in terms of capabilities, however, and some offer services such as roll slitting, which converts large rolls into individual sheets that the die cutter can use with flatbed equipment.
Image: Rolls of material in inventory for custom gaskets
For design engineers, procurement managers, and other buyers of a gasket, the widespread availability of die cutting services is a sourcing advantage. For example, if you're an original equipment manufacturer (OEM) from Dallas, you don't need to limit yourself to die cutters in Texas or even other parts of the Southwest. Instead, you can source die gaskets from California, Ohio, Massachusetts, or even China. When the right vendor is selected, die cutting supports supply chain flexibility.
In Planning to Prevent Manufacturing Disruption , a recent article from Modus Advanced, Sara Solomon explained what to look for in a die cutting facility. For starters, it's important to pick a partner who checks quality at multiple points in the production process. Pre-production planning (PPP) can cut costs, so make sure that the gasket manufacturer you choose examines everything from order verification and engineering to purchasing and packaging.
3. Design Changes without Major Tooling Expenses
xcept for digital die-less cutting, die cut gaskets always requires tooling. Metal dies don't have to be expensive, however, especially compared to other parts production techniques. For example, a simple steel rule die typically costs under $300 (USD) to produce. You'll want to make smart design decisions, but the cost of a new die isn't so much that revisions will cause cost overruns. By comparison, the cost of an injection molding can exceed $50,000, making design changes extremely expensive.
Die cutting is great for high-volume production, but cost-effective dies also make it a smart choice for low-to-medium volume runs. For example, if you spread the cost of a $300 die across 3000 parts, the per-gasket cost for the die is just 10 cents. As many electronics manufacturers know, EMI gaskets that are made of silver-filled silicone rubber can be costly. So when you compare the total cost of an EMI gasket to the per-gasket cost of the steel rule die, $300 for tooling is insignificant.
If you need to test the form, fit, and function of a part before buying a die, consider ordering a prototype that's produced with water jet equipment or a CNC digital cutter. For connector gaskets and other parts, die cutting doesn't have to be an "either or" choice with other manufacturing techniques and this is why many companies describing themselves as die cutters also have water jet machines, digital die-less cutters, or other capabilities.
Image: Flow water jet machine
Die cutting for connector gaskets and other types of sealing and insulation provide many advantages. In addition to low setup costs and supply chain flexibility, design engineers and procurement personnel can employ design changes without major tooling expenses. If you need a custom die cut gasket for your next project, consider this reliable, cost-effective, custom gasket manufacturing method.