What Happens During a SigShield™ DFM: a Design for Manufacturability Review and Consultation Service?
September 23, 2021
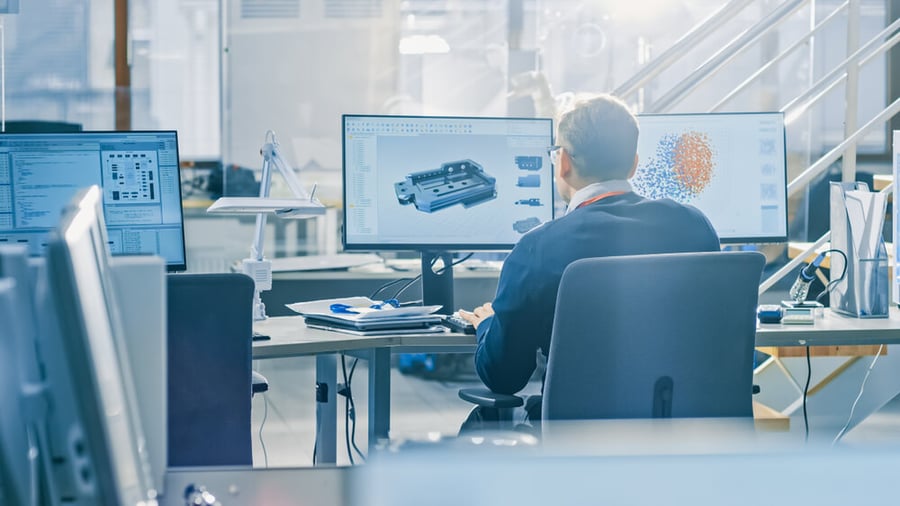
Manufactured with Speed and Precision
The manufacturing capabilities you need and the engineering support you want, all from a single partner.
Submit a DesignEver wanted to know what goes into the Design for Manufacturability (DFM) process for SigShield™ parts?
The DFM review is a business consulting service in which the experts on the Modus engineering team review your design and work with you collaboratively to design and develop solutions to realize and improve the manufacturability of your design, reduce your lead times for parts, and spare you any unnecessary manufacturing costs, using a vertically integrated design and manufacturing process.
Even if it hasn’t been the most burning question on your mind, as an engineer or procurement manager, understanding how this service works can be incredibly helpful.
We’ve found that there are plenty of misconceptions about the process, and we’ve given feedback on thousands of designs, so we drew on our past experiences to provide you some guidance on how the process works for us (and how we believe it should work anywhere).
--Article Continues Below--
Redefining the RF shield production process
Step 1: Gather Information
The very first step in any DFM process is to gather all necessary information from the customer that is pertinent to the SigShield™ order. This includes:
- The design of the metal housing
- The desired form-in-place-gasket dispense path
- Material selection
- Requirements for turnaround times
- Volume of parts needed (both in Prototype and Production situations)
The earlier you can involve us, your manufacturing partner, in the design process, the better off you’ll be! Having a partner like Modus, which offers a consultative review service, like the SigShield™ process, will ultimately save you significant amounts of both time and money throughout your part’s design, engineering, prototyping and production processes.
Step 2a: Can the Part be Made?
The first question that we address during the DFM process is the question of if the requested SigShield™ part can even be made. Our engineers will review the drawing and take a look at how the part is designed and inspect the required tolerances put forth in the design file.
Surprisingly often, we receive orders for parts that simply cannot be made according to the specifications outlined in the design. There are quite a few reasons why this happens, some of which include:
- Material tolerances for machined parts or form-in-place gaskets: Often we will see a specified tolerance that is not possible at all for a selected material, regardless of the method of production.
- Drawing issues for machined parts: There may be issues with stated tolerances for machined parts that are not achievable, or issues with selected reference points for measurements within the drawing.
- CAD issues: Sometimes CAD drawings will have radii or settings that are globally applied across a part, even in places where it makes the part impossible, or very difficult, to manufacture.
- Modeling issues: Another issue that comes up are organic shapes or artifacts that happen as a result of how the CAD software generates and applies design features to a part in the CAD modeling process. It is usually required that an engineer manually go back through and fix these artifacts during the design process, but they are occasionally missed or overlooked.
So, the first step of every SigShield™ DFM starts with: “Is it possible?”
Our engineers will review the design and consult with you regarding issues which would essentially make your design impossible to engineer or manufacture, so you can review and update the design with our input.
Step 2b: How Complex is the Part to Make?
Once we’ve passed the point of “is this possible?” it is time to consider: “Is this feasible?”
Usually, at the same time that we are reviewing the SigShield™ part to ensure that it is possible to engineer, we will also look for potential changes that can make the part less complex to manufacture. This will help bring down your total costs and lead times.
We often receive engineering drawings for parts that have specifications that would require incredibly lengthy or expensive methods for production. In most cases, these designs can be changed without sacrificing the quality or ability of the part to meet its functional requirements.
In this phase, we look for opportunities to make your SigShield™ part more efficient to produce and work directly with the engineers who designed it to understand what design factors have some wiggle room. The SigShield™ consulting service creates a back and forth between our engineering team and yours which will result in a part that is produced using the most efficient methods, will provide you the best lead times, and will still meet your quality requirements.
Step 3: How Will the Part be Manufactured?
Once both teams are happy with the design and requirements, we next step into defining how we will manufacture the part. This is where the process starts to look different depending upon what kind of part you are looking to build.
Two Dimensional Materials
For any two-dimensional materials outlined in the design, like thermal pads or RF absorbers, we’ll likely be choosing which method to use for manufacturing between die cutting, CNC or digital cutting, waterjet cutting, and potentially form-in-place (FIP) gasket dispensing. The factors that weigh heavily into this decision include both design considerations and production considerations.
Design considerations:
- Size and shape of the converted material
- Selected material
- Thickness of material and thickness of walls in the design
- Requested tolerances
Production considerations:
- Volume of parts required
- Requested lead time
- Cost considerations
- Ease of assembly
Each method for production provides different pros and cons. Our job is to consult with you to determine the best fit that meets your design requirements while minimizing both lead time and cost.
It might sound simple on the surface, but it is actually a pretty complex process because so many factors are involved which can easily affect each other. There are also plenty of creative ways to make the best use of each type of process.
Three Dimensional Gaskets
For the three-dimensional form-in-place gaskets in your design, we’ll be defining a final dispense path and helping ensure that the wall thickness of your machined housing will support a dispensed gasket.
For molded rubber parts, the DFM process will help determine if injection molding or compression molding is the right fit for your needs, weighing in lead times, costs and part volumes.
Machined Parts
If you are looking for a machined part, this phase is all about which machines and tools we will be using to build it.
Is it best fit for our horizontal, vertical or 5-axis milling machine? This determination is based upon the size and shape of your design, and how many faces of the part have machined features requiring a dedicated perpendicular tool orientation.
What kind of tooling is required? Based on the dimensions of different features in your design, we’ll need different size and shape tools to create it.
What is the required cycle time? Certain features of machined part designs will require them to run through multiple cycles within the milling machines. Understanding how many cycles, and how long the cycles will need to be is imperative in driving lead time and cost.
At the end of this phase, we’ll have a detailed breakdown of each step that needs to happen from start to finish in order to complete your machined part.
Step 4: It’s Time to Break Down the Details
All of these steps ultimately lead to what you’ve been waiting for, the final quote for your SigShield™ project!
Now that we’ve broken down the “how,” we can give you all the details about how long it will take and how much it will cost to complete.
The Bottom Line
SigShield’s™ consulting service for the design, engineering, and vertically integrated manufacturing of RF shields not only assists you in refining your design and ensures that your functional needs are met, but also reduces your long term costs and lead times.