8 Important Design Considerations for Custom Gaskets
December 23, 2020
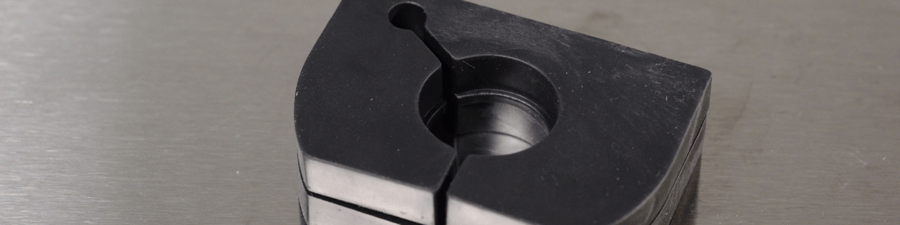
Manufactured with Speed and Precision
The manufacturing capabilities you need and the engineering support you want, all from a single partner.
Submit a DesignKey Points
- Custom gasket design requires careful consideration of 8 critical factors: function, regulatory requirements, environment, temperature range, substrate compatibility, material selection, manufacturability, and manufacturing method.
- Modus Advanced is a manufacturing partner with vertical integration capabilities, allowing them to handle multiple manufacturing processes under one roof; reducing lead times, lowering costs, and improving quality control.
- More than 10% of Modus Advanced's staff are engineers, providing customers with direct access to technical expertise throughout the design and manufacturing process.
- Choosing a quality-focused manufacturing partner like Modus Advanced helps prevent quality control issues that can cost up to 100 times the initial part cost to fix.
- Modus Advanced serves critical industries including aerospace & defense and medical devices, where precision, reliability, and faster time-to-market can literally save lives.
Designing a custom gasket is no easy task. There are thousands of different materials to choose from and many detailed design decisions you must make in the process.
Understanding what factors to consider at a high level is a good starting point in ensuring that you get your design right the first time, and don’t have to spend time or effort on costly redesigns down the road.
The 8 most important considerations for custom gasket design include:
Avoid frequent design mistakes in our free guide.
Function
You’ve got to start at the beginning. Defining the function of your custom gasket sets the stage for all of your design decisions and requirements. Trying to design a gasket without first answering this question is like trying to conduct surgery without first having a diagnosis for the ailment you are looking to fix.
Will your custom gasket be used to:
- Create an environmental or EMI seal between two surfaces
- Isolate vibration
- Simply fill space between two surfaces
In each case, you’ll have different requirements of the chemical composition, deflection tolerances, water absorption and temperature ratings of the materials you choose.
The Bottom Line: Know what your gasket needs to do before starting to jump into any major design decisions.
Regulatory Requirements
You’ll also want to make sure that you are well aware of any regulatory requirements within your industry or specific application. For instance, if you are building a custom gasket for an Aerospace application for the US Government, you may be required to use a vendor that meets CMMC requirements and manufactures in the US. Or, for Rail applications, you may be required to select materials that meet specific ASTM flame, smoke and toxicity control requirements.
The Bottom Line: Make sure you are well aware of compliance requirements before going too deep into the design process, and especially before you select a material.
Environment
Up next in the consideration set is the environment into which the gasket will be placed. Will your gasket be in a dynamic or static environment? Knowing what kind of seal will be required and what stresses the gasket will be subjected to is incredibly important in the design.
Some examples of different types of seals that may be required include:
- Static seals: Static seals are classified as a joining of two surfaces that have no relative motion between each other. Static seals fall into two sub-categories: axial and radial static seals.
- Axial static seals: Axial static seals are created by applying compression forces between the upper and lower surfaces being joined.
- Radial static seals: Radial static seals are created by applying compression forces between the inner and outer surfaces being joined.
- Dynamic seals: Dynamic seals exist when there is motion between the surfaces being sealed. Dynamic seals fall into three sub-categories: reciprocating, rotary and oscillating seals.
- Reciprocating dynamic seals: Reciprocating dynamic seals are required when there is reciprocating motion along a single axis between inner and outer surfaces.
- Rotary seals: Rotary seals are created when there is rotational motion between the surfaces being sealed.
- Oscillating seals: Oscillating seals are created when a shaft rotates through a specific number of turns around an axis, ultimately causing oscillation.
In addition, you should consider if your gasket will need to be reused multiple times, or if it will be clamped into place once and then never moved.
The Bottom Line: Know how your gasket will fit into its surrounding environment, as that will inform many design decisions down the line.
Temperature
While this fits into the “environment” category, it is so important, we’ve pulled it out as a separate consideration. The temperature range in which your gasket will be required to operate will be one of the driving factors in the material you choose for your gasket.
Some important things to consider with regards to temperature include:
- Make sure you are taking into account the entire temperature range your gasket will need to withstand (and not just thinking about just a single point in time).
- Materials designed to work well for one end of the spectrum (very high or very low temperatures) will be highly susceptible to failure on the other end of the spectrum.
- Generally, if you need your gasket to perform in a very wide range of temperatures, you’ll have to look towards higher end, or more expensive materials.
The Bottom Line: Know the entire temperature range you will need your gasket to work in before specifying the material.
Substrate
Up next in the list is your substrate. Knowing what materials you need your gasket to make a seal between will help you answer important design questions.
Certain substrates will work better with the addition of a pressure sensitive adhesive on your gasket, and help to create a more effective seal.
In addition to your substrate, it is critical to understand the compression forces that will be exerted on the seal.
The Bottom Line: Know what material your gasket will be applied to and what the compression forces will be.
Read Now: Guidance from start to finish on your custom gasket production.
Gasket Material Selection
Only once you’ve answered all of the questions above are you really able to jump into the most important part of the design process: material selection.
Getting your material right will be the hardest part of the design process, as there are thousands of materials, each with different properties and tolerances to choose from.
Some of the most common materials for making custom gaskets are detailed in this article.
The Bottom Line: This will be the most time consuming part of your design process.
Manufacturability
One of the most overlooked parts of the custom gasket design process is ensuring that you are designing for manufacturability.
You should know, during the design phase, how many of these gaskets you’ll want to make. If you only need a few, then you are pretty free to design as you’d like. If you know you’ll need your gaskets manufactured in large quantities, you’ll also want to ensure that you are considering how they will be manufactured as you design.
Designing with manufacturability in mind will help you create a custom gasket that not only meets your specifications, but can also be manufactured quickly and at the lowest possible cost.
This is all about taking your design from concept to a physical part. A good manufacturing partner will be able to help you get this right. We frequently see designs come in where we can provide small changes that significantly reduce lead time and costs for our customers.
The Bottom Line: You can definitely think about this early in the design process, but you should expect your manufacturing partner to really help you with this collaboratively.
Manufacturing Method
One of the most important parts of designing for manufacturability is what method will be required to manufacture your gasket.
There are multiple processes by which a custom gasket can be made, including:
The material you select and the design requirements will help to narrow down which process can be used to optimally manufacture your gasket.
And each process comes with different costs. For instance, waterjet cutting is typically much more expensive than die cutting but allows you to create gaskets with perfectly straight walls and almost no deflection. Understanding where you can change your design, and what is non-negotiable, may help you utilize different manufacturing processes to produce it.
The Bottom Line: Make sure you know where your design has room for changes when entering conversations with your manufacturing partner.
In Summary
As an engineer, you understand mechanical design. What you may not be as comfortable with is understanding how your design lends itself to manufacturability. In many cases, lead time and cost of manufacturing parts can be prohibitive in taking a design from concept to reality, so invest in making sure you get all of the factors discussed in this article into your design process.