Conductive Fabric Gaskets: Lightweight Solutions for Portable Military Equipment
April 21, 2025
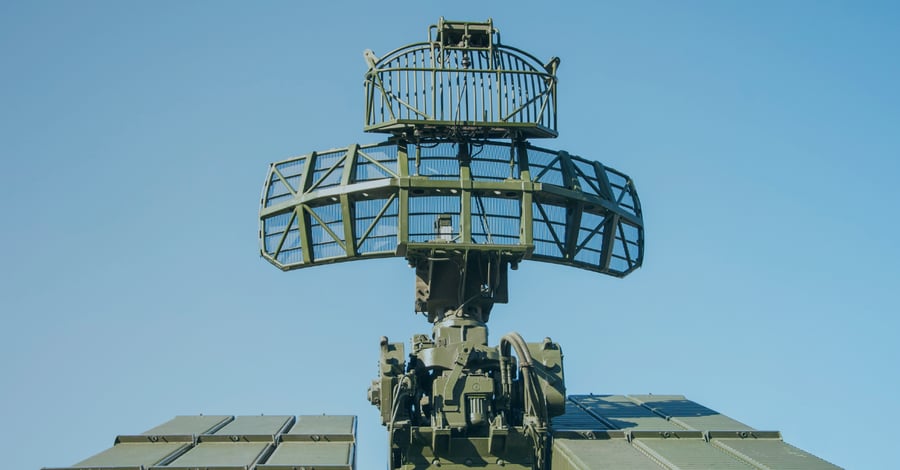
Manufactured with Speed and Precision
The manufacturing capabilities you need and the engineering support you want, all from a single partner.
Submit a DesignKey Points
- Critical Defense Applications: Conductive fabric gaskets provide essential EMI/RFI shielding for sensitive military electronics in field operations where interference could compromise mission success.
- Weight Reduction Advantages: The lightweight nature of conductive fabric gaskets makes them ideal for portable military equipment where every ounce matters for soldier mobility and aircraft payload optimization.
- Environmental Performance: These gaskets can be designed to withstand extreme temperatures, moisture, dust, and vibration commonly encountered in military field operations.
- Design Flexibility: Conductive fabric gaskets conform to irregular surfaces and complex geometries, making them suitable for the compact, multi-functional designs of modern military equipment.
- Galvanic Compatibility: When properly specified, conductive fabric gaskets minimize galvanic corrosion risk when used with the various metal alloys found in military hardware.
At Modus Advanced, we understand that military equipment engineers face unique challenges balancing electromagnetic shielding requirements with strict weight limitations for portable field equipment. The right EMI/RFI shielding solution can make the difference between mission success and failure when electronic systems must operate flawlessly in hostile environments.
This article explores how conductive fabric gaskets provide critical shielding capabilities while meeting the demanding weight and durability requirements of portable military equipment. We'll examine specific applications, key performance advantages, and critical selection factors for defense applications.
What Are Conductive Fabric Gaskets?
Conductive fabric gaskets, also known as fabric-over-foam (FOF) gaskets (or conductive foam gaskets), combine a conductive fabric exterior with a compressible foam core. This construction creates a lightweight, flexible EMI/RFI shielding solution that conforms to mating surfaces while providing reliable electrical conductivity.
The conductive fabric layer typically consists of a base fabric (often polyester or nylon) plated or woven with conductive metals such as nickel, copper, silver, or combinations thereof. This layer creates the electrical continuity needed for effective EMI/RFI shielding across the gasketed interface. The foam core, usually made from urethane, silicone rubber, or neoprene, provides the compression characteristics and resilience that maintain constant contact pressure.
For military applications, conductive fabric gaskets excel in high-frequency shielding scenarios where weight and compression force limitations make traditional all-metal gaskets or conductive elastomers impractical.
Critical Applications in Military Equipment
Portable military equipment demands shielding solutions that minimize weight while maximizing protection against both intentional and unintentional electromagnetic interference. Conductive fabric gaskets are increasingly specified in these applications due to their excellent performance-to-weight ratio.
Common applications where conductive fabric gaskets provide essential EMI/RFI protection include:
- Tactical Communications Systems: Radios, headsets, and field communication devices that must operate reliably in electromagnetically noisy combat environments
- Portable Computing Devices: Ruggedized laptops, tablets, and handheld command systems used for mission planning and tactical operations
- UAV Systems: Lightweight UAS and portable ground control stations where weight impacts flight time and portability
- Night Vision and Targeting Systems: Optical electronics that must function without interference from nearby communications equipment
- Soldier-Wearable Electronics: Batteries, communications nodes, and sensor packages integrated into modern infantry equipment
- Portable Medical Equipment: Field hospital diagnostic and treatment devices where electromagnetic interference could compromise patient care
These mission-critical applications all benefit from the lightweight and effective shielding provided by conductive fabric gaskets, especially compared to alternative shielding methods. Each application presents slightly different requirements for compression, durability, and frequency range protection.
Advantages for Portable Military Applications
The specific properties of conductive fabric gaskets make them particularly well-suited for weight-sensitive military applications. Understanding these advantages helps engineers select them appropriately for portable equipment designs.
Property | Advantage for Military Equipment | Practical Impact |
Low Weight | Reduces overall equipment weight | Improves soldier mobility, extends UAV flight time, increases portable equipment capacity |
Low Compression Force | Requires minimal fastener pressure | Allows for lighter enclosure designs, reduces structural requirements |
Conformability | Adapts to irregular surfaces | Accommodates complex geometries in space-constrained portable equipment |
High-Frequency Shielding | Effective at GHz frequencies | Protects against modern communications and radar interference |
Vibration Dampening | Absorbs mechanical energy | Reduces equipment damage during transport and operation |
Fast Recovery | Returns to original shape quickly | Maintains protection when equipment is opened and closed repeatedly in field |
These combined advantages make conductive fabric gaskets an excellent choice for engineers designing equipment that must balance protection with portability. The weight advantages alone can make significant differences in operational capabilities when multiplied across all the equipment a modern soldier carries.
Environmental Considerations for Military Use
Military equipment operates in some of the world's most challenging environments. When selecting conductive fabric gaskets for these applications, environmental performance becomes a critical factor in gasket specification.
Conductive fabric gaskets for military use must often address:
- Temperature Extremes: From arctic to desert conditions (-40°C to 85°C or beyond)
- Moisture and Humidity: Protection against condensation, rain, and immersion
- Dust and Particulates: Prevention of ingress in desert and field conditions
- Salt Spray Exposure: Corrosion resistance for naval and coastal operations
- UV Exposure: Material stability during prolonged outdoor deployment
- Chemical Exposure: Resistance to fuels, lubricants, and decontamination agents
Engineers should carefully evaluate the environmental requirements and specify conductive fabric gaskets with appropriate materials and finishes to ensure long-term performance. Many manufacturers offer specialized military-grade conductive fabric gaskets with enhanced environmental resistance specifically designed for defense applications.
The selection of base materials and plating types can dramatically impact environmental performance. Silver-plated fabrics offer excellent conductivity but may tarnish in certain environments, while nickel-copper combinations provide better corrosion resistance for demanding field conditions.
Visit the full resource center on everything RF Gaskets
Selection Criteria for Military Applications
Selecting the right conductive fabric gasket for military equipment requires careful consideration of multiple factors beyond basic shielding performance. Engineers should evaluate these key criteria when specifying gaskets for portable military equipment:
Shielding Performance
Shielding effectiveness requirements will vary based on the sensitivity of protected components and the electromagnetic environment. Military equipment often faces sophisticated electronic warfare threats requiring superior protection.
Conductive fabric gaskets typically provide 60-100+ dB of shielding effectiveness across frequencies from 10 MHz to 18 GHz. Higher-performance gaskets using silver-based conductors may offer enhanced shielding at higher frequencies particularly relevant to modern military communications and sensing systems.
Different conductive materials provide varying levels of performance across frequency ranges. Testing to military standards such as MIL-STD-461 should guide selection for critical applications.
Material Compatibility
Military equipment often utilizes specialized alloys and surface treatments that must be compatible with the conductive fabric gasket to prevent galvanic corrosion and ensure long-term performance.
Consider these material compatibility factors:
- Galvanic potential between gasket plating and enclosure materials
- Chemical compatibility with conformal coatings and sealants
- Outgassing characteristics in sealed enclosures
- Flame retardancy requirements per applicable military standards
Selecting compatible materials ensures that the conductive fabric gasket will maintain its performance throughout the equipment's service life without causing deterioration of adjacent components.
Physical Requirements
The physical constraints of portable military equipment often dictate specific dimensional and compression characteristics for conductive fabric gaskets.
Key physical specifications include:
- Compressed thickness (typically 50-80% of original height)
- Compression force (typically 1-10 lbs/inch for fabric-over-foam designs)
- Compression set (recovery after prolonged compression)
- Mounting method (adhesive-backed, mechanical retention, etc.)
- Cut tolerance requirements
Properly specified physical characteristics ensure reliable sealing and shielding performance while maintaining the weight advantages that make conductive fabric gaskets an excellent choice for portable equipment.
The Modus Approach to Military-Grade Conductive Fabric Gaskets
At Modus Advanced, we understand that military equipment isn't just another application – it's gear that service members' lives may depend on. Our approach to conductive fabric gaskets for defense applications combines technical precision with an engineering-first mindset.
We support defense contractors and military equipment manufacturers with:
- Comprehensive material selection guidance with a focus on military environmental requirements
- Design for Manufacturing (DfM) reviews to optimize gasket design for manufacturing and performance
- AS9100 and ISO 9001 certified manufacturing processes
- ITAR compliance for sensitive defense applications
- CMMC compliance
- Vertical integration that reduces lead times for fast-track military programs
- Engineering expertise from a team where over 10% of our staff are degreed engineers
When specifying conductive fabric gaskets for your next portable military equipment design, partner with a manufacturer who understands what's at stake. One day matters when you're designing equipment that protects and enables those who serve.
Contact our engineering team today to discuss your specific conductive fabric gasket requirements for military applications.