Design for Manufacturing Checklist: Manufacturing Readiness Assessment for Critical Applications
July 17, 2025
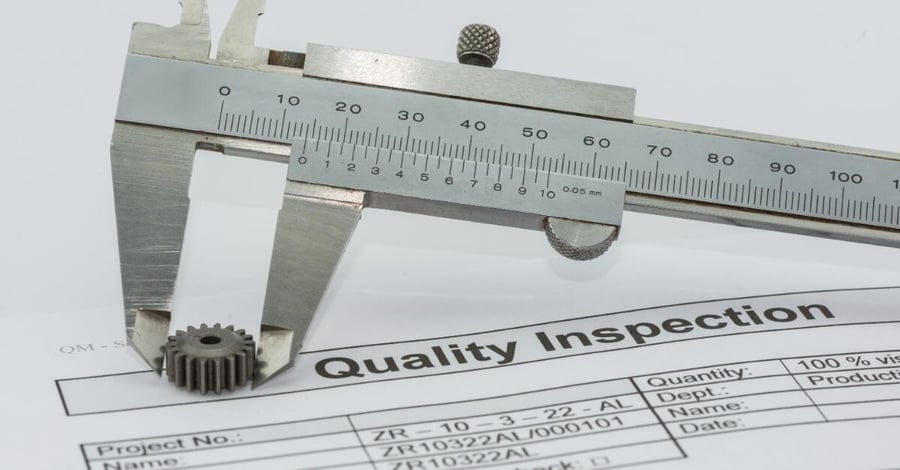
Manufactured with Speed and Precision
The manufacturing capabilities you need and the engineering support you want, all from a single partner.
Submit a DesignKey Points
- Manufacturing readiness assessment: A systematic design review process helps identify potential production challenges before they impact timelines and costs, ensuring designs transition smoothly from concept to production.
- Common design pitfalls: Engineers frequently over-design parts with unnecessary curves, tight tolerances, and complex geometries that significantly increase manufacturing time and cost without functional benefit.
- Process-specific considerations: Different manufacturing processes — machining, form-in-place gasket dispensing, and converting — each have unique design requirements that must be evaluated during the review phase.
- Quality and inspection impact: Design decisions directly influence inspection requirements, with overly complex specifications adding substantial lead time through increased quality control processes.
- Early collaboration advantage: Involving manufacturing partners in the design review phase prevents costly redesigns and accelerates time-to-market for critical applications.
Design for Manufacturing: The Critical Assessment Challenge
Product development teams face mounting pressure to deliver life-saving medical devices and mission-critical aerospace systems faster than ever. The difference between a design that looks perfect in CAD and one that manufacturers efficiently often determines whether innovations reach those who need them weeks or months sooner.
Design for manufacturing (DFM) assessment transforms this challenge into a systematic opportunity. Engineers can identify and resolve potential production issues during the design phase, when changes cost time measured in hours rather than weeks.
Read the full Design for Manufacturability guide.
Understanding Design for Manufacturing Fundamentals
Design for manufacturing assessment evaluates how design decisions impact production processes, lead times, and quality requirements. This evaluation considers three fundamental areas: geometric complexity, tolerance specifications, and process-specific manufacturing constraints.
The assessment process reveals hidden connections between design choices and manufacturing reality. A seemingly minor design feature — like specifying different radius values throughout a part — can triple machining time through increased tool changes and setup requirements.
Critical DFM Assessment Categories
The systematic evaluation of manufacturing readiness requires examining multiple interconnected factors that influence production success. Each category contributes essential insights for comprehensive design assessment.
- Geometric Design Elements: Evaluate how geometric features align with manufacturing capabilities, identifying complex curves and intricate details that may create production challenges without functional benefit.
- Tolerance and Quality Specifications: Examine whether specified tolerances serve functional requirements or simply reflect software defaults that increase manufacturing complexity unnecessarily.
- Process Integration Considerations: Assess how different manufacturing steps interact, considering the sequence and compatibility of machining, coating, and assembly operations.
- Material and Surface Requirements: Review material specifications and surface finish requirements to ensure compatibility with intended manufacturing processes.
Machining Design for Manufacturing Assessment
Machined components present unique design challenges that directly impact production efficiency and cost. The assessment process should systematically evaluate geometric features, tolerance specifications, and manufacturing approach compatibility.
Complex curved surfaces require extensive machining time and specialized tooling. Assessment teams should question whether aesthetic curves provide functional value or simply increase production cost and complexity.
Geometric Feature Evaluation for DFM
Sharp corners in machined cavities represent impossible manufacturing requirements. All internal corners require radius specifications, with larger radii enabling faster machining through bigger cutting tools and reduced setup time.
The assessment should identify opportunities to standardize radius values throughout the part. Using consistent radius specifications reduces tool changes and programming complexity, significantly decreasing lead times.
Parts designed for eventual casting but prototyped through machining present particular challenges. Draft angles and complex filleted surfaces optimize casting but create machining difficulties that can be avoided through prototype-specific design modifications.
Manufacturing Approach Compatibility Assessment
Features aligned with standard X, Y, and Z planes enable efficient three-axis machining. Non-standard orientations force five-axis operations or complex fixturing, substantially increasing setup time and cost.
Assessment should identify whether angled features serve critical functions or represent design preferences that could be modified for manufacturing efficiency. Deep pockets and narrow channels may require specialized CNC machining with extended lead times.
Read our Complete CNC Machining Guide.
Form-in-Place Gasket DFM Assessment
Form-in-place (FIP) gasket applications require specialized design assessment focusing on dispensing path optimization and material adhesion considerations. The evaluation process must consider both the gasket geometry and the housing design that supports it.
Multiple gasket lines converging at single points create dispensing challenges and potential quality issues. Assessment should identify opportunities to simplify dispensing patterns while maintaining sealing effectiveness.
Dispensing Path Analysis for Manufacturing
Complex dispensing paths with numerous starts, stops, and T-joints increase both manufacturing time and quality variation. The review process should evaluate whether simplified geometries could provide equivalent performance.
Assessment teams should examine the following dispensing considerations:
- Start and Stop Optimization: Minimize the number of dispensing interruptions to reduce potential quality variations and manufacturing complexity.
- Path Continuity: Design continuous dispensing routes wherever possible to maintain consistent bead characteristics and reduce setup time.
- Access Requirements: Ensure adequate clearance for dispensing equipment, particularly in deep pockets or confined spaces.
- Material Flow Considerations: Account for material viscosity and flow characteristics when designing dispensing paths and pocket geometries.
Surface Preparation Manufacturing Requirements
Extremely smooth surface finishes can create FIP adhesion challenges, particularly with certain coating combinations. The assessment should identify potential adhesion issues and recommend surface modifications if necessary.
Surface preparation requirements vary significantly based on coating type and FIP material selection. Assessment teams should understand these interactions to prevent adhesion failures during production.
Steel dowel pins and other ferromagnetic hardware can interfere with magnetically-formed gaskets during the forming process. Assessment should identify potential interference issues and recommend installation sequence modifications.
Read the Complete Form-in-Place Gasket Guide.
Converting and Assembly DFM Assessment
Converted parts — those manufactured through die cutting, waterjet cutting, or digital cutting — require assessment focused on geometry complexity, tolerance achievability, and assembly considerations.
Converting processes have inherent limitations based on material properties and cutting method capabilities. The assessment should align geometric requirements with process capabilities to ensure successful production.
Die Cut, Water Jet, CNC Knife Tolerances
Imperial (Inches) Tolerance Table
Dimension Range | Film (BL1) | Solid or Dense (BL2) | Sponge or Foam (BL3) |
---|---|---|---|
For thicknesses up to 0.25" | |||
Under 1.0" | ±0.010" | ±0.015" | ±0.025" |
1.0" to 6.3" | ±0.015" | ±0.025" | ±0.032" |
Over 6.3" | Multiply by 0.004 | Multiply by 0.01 | Multiply by 0.0063 |
For thicknesses from 0.25" to 0.50" | |||
Under 1.0" | N/A | ±0.030" | ±0.040" |
1.0" to 6.3" | N/A | ±0.040" | ±0.050" |
Over 6.3" | N/A | Multiply by 0.005 | Multiply by 0.0063 |
For thickness over 0.50" | |||
Under 1.0" | N/A | N/A | ±0.050" |
1.0" to 6.3" | N/A | N/A | ±0.070" |
Over 6.3" | N/A | N/A | Multiply by 0.01 |
Metric (Millimeters) Tolerance Table
Dimension Range | Film (BL1) | Solid or Dense (BL2) | Sponge or Foam (BL3) |
---|---|---|---|
For thicknesses up to 6.3mm | |||
Under 25mm | ±0.25mm | ±0.38mm | ±0.63mm |
25mm to 160mm | ±0.38mm | ±0.63mm | ±0.81mm |
Over 160mm | Multiply by 0.004 | Multiply by 0.01 | Multiply by 0.0063 |
For thicknesses from 6.3mm to 12.7mm | |||
Under 25mm | N/A | ±0.76mm | ±1.02mm |
25mm to 160mm | N/A | ±1.02mm | ±1.27mm |
Over 160mm | N/A | Multiply by 0.005 | Multiply by 0.0063 |
For thickness over 12.7mm | |||
Under 25mm | N/A | N/A | ±1.27mm |
25mm to 160mm | N/A | N/A | ±1.78mm |
Over 160mm | N/A | N/A | Multiply by 0.01 |
Material Classification Notes
- Film (BL1): Thin, flexible sheet materials
- Solid or Dense (BL2): Dense rubber and similar solid materials
- Sponge or Foam (BL3): Cellular and foam materials
Important Considerations
The "dish effect" becomes more pronounced as material thickness increases during die-cutting operations. This concavity of die-cut edges results from the compression force of the cutting die, causing the width (or length) at the top and bottom surfaces to be slightly greater than the width at the center.
Assembly Process Assessment in Manufacturing
Small, delicate components with pressure-sensitive adhesive (PSA) backing present assembly challenges that increase with geometric complexity. Assessment should evaluate whether component consolidation or alternative attachment methods could simplify assembly.
The assessment should consider whether converted components could be replaced with dispensed alternatives for complex geometries. Dispensable thermal materials and RF absorbers can eliminate assembly challenges associated with small, precisely-positioned components.
Visit our full Design for Manufacturability resource center.
Quality and Inspection Impact in DFM Assessment
Design specifications directly determine inspection requirements and quality control complexity. The assessment process must evaluate how design decisions translate into quality control time and cost implications.
Profile tolerances and complex geometric specifications require comprehensive inspection routines that significantly increase quality control time. Assessment should distinguish between functional requirements and unnecessarily complex specifications.
Specification Impact Analysis for DFM
Sampling versus 100% inspection requirements depend on specification criticality and customer requirements. Assessment teams should understand how inspection frequency requirements impact overall lead times.
Design features must be accessible for measurement and verification. Complex internal geometries or deep pockets may require specialized measurement equipment or techniques that increase inspection time and cost.
Assessment should evaluate the following inspection considerations:
- Measurement Accessibility: Ensure critical features can be measured with standard equipment and techniques.
- Sampling Strategy Compatibility: Design specifications should align with appropriate sampling strategies for the intended application.
- Documentation Requirements: Consider how design complexity affects required documentation and traceability.
- Equipment Capability: Verify that specified tolerances align with available measurement equipment capabilities.
Industry-Specific DFM Assessment Considerations
Different industries present unique design assessment challenges based on their specific requirements and constraints. Understanding these differences ensures appropriate evaluation criteria for each application.
Weight optimization drives many design decisions in aerospace applications, creating tension between manufacturing efficiency and performance requirements. Coating and surface treatment requirements add complexity layers that must be considered during assessment.
Aerospace and Defense DFM Applications
Aerospace and defense components typically push manufacturing limits through extremely tight tolerances and complex geometries. These applications often require specialized materials and processes that influence design feasibility.
Assessment teams should consider mission-critical performance requirements while identifying opportunities for manufacturing optimization. Design for manufacturing principles become even more critical when components must perform in life-critical situations.
Medical Device DFM Applications
Medical device designs must balance manufacturing efficiency with stringent quality requirements. These applications typically involve higher inspection frequencies and documentation requirements that impact lead times regardless of design complexity.
Biocompatibility material requirements may limit manufacturing process options, requiring assessment teams to understand material-process interactions for successful production. Sterilization method compatibility adds another layer of design constraint consideration.
Implementing Effective DFM Review Processes
Manufacturing readiness assessment requires structured collaboration between design teams and manufacturing partners. Early engagement prevents costly redesigns and ensures designs optimize for both function and manufacturability.
Assessment should begin during initial concept development, not after design completion. Early evaluation identifies major manufacturing challenges when design flexibility remains highest.
Design for Manufacturing Review Timing and Frequency
Iterative assessment throughout the design process ensures modifications maintain manufacturing feasibility while meeting performance requirements. The assessment schedule should align with project milestones and design freeze deadlines.
Key assessment checkpoints include:
- Concept Phase: Evaluate fundamental manufacturing approach and identify potential showstoppers.
- Preliminary Design: Review detailed geometries and tolerance specifications for manufacturability.
- Final Design: Confirm manufacturing readiness and finalize production specifications.
- Pre-Production: Validate manufacturing processes and quality control procedures.
DFM Collaboration Framework
Effective assessment requires input from design engineers, manufacturing engineers, and quality professionals. Each perspective contributes essential insights for comprehensive evaluation.
Manufacturing partners with relevant certifications — AS9100 for aerospace applications, ISO 9001 for quality management, and ITAR compliance for defense applications — bring specialized knowledge essential for thorough assessment. Clear communication protocols ensure assessment feedback integrates effectively into design decisions.
The assessment process should establish precedence between CAD models and engineering drawings when discrepancies exist, preventing manufacturing delays due to conflicting specifications. Documented rationale for recommendations enables informed trade-off decisions between manufacturing efficiency and design preferences.
Maximizing DFM Assessment Value Through Partnership
Manufacturing readiness assessment delivers maximum value when conducted with experienced manufacturing partners who understand both design intent and production realities. This collaboration accelerates innovation delivery while ensuring manufacturing feasibility.
Engineering teams benefit from partners who combine manufacturing expertise with engineering knowledge — organizations where engineers comprise significant portions of staff bring both perspectives to the assessment process. This dual expertise enables nuanced evaluation that considers both functional requirements and manufacturing constraints.
The assessment process ultimately serves the critical mission of delivering life-changing innovations faster. Whether developing custom gaskets that save lives or aerospace systems that ensure mission success, thorough manufacturing readiness assessment helps engineering teams bring their innovations to those who need them sooner.