Design for Manufacturability Principles Every Engineer Should Know
July 17, 2025
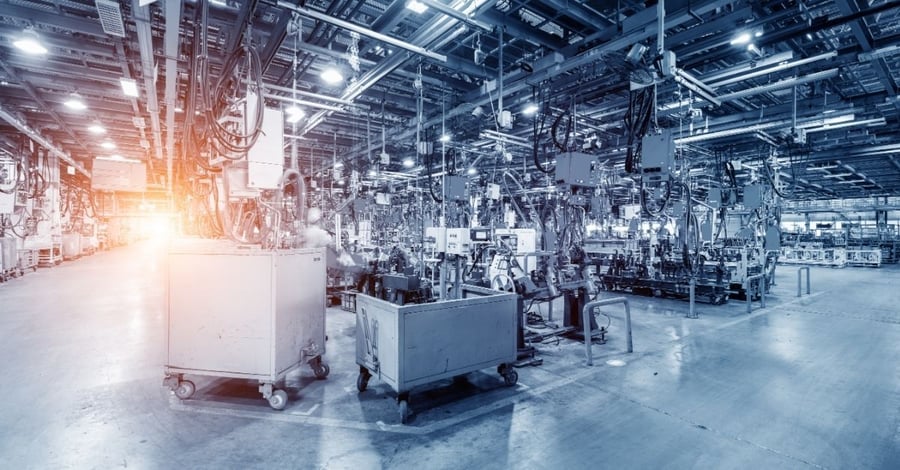
Manufactured with Speed and Precision
The manufacturing capabilities you need and the engineering support you want, all from a single partner.
Submit a DesignKey Points
- Simplification reduces complexity: Eliminate unnecessary features like excessive curves and non-functional design elements that increase machining time without adding value
- Material selection impacts process choice: Understanding manufacturing capabilities for different materials prevents costly redesigns and delays
- Tolerance optimization balances quality and cost: Appropriate tolerances reduce manufacturing time while maintaining functional requirements
- Feature standardization accelerates production: Using consistent radii, standard hardware, and common geometries streamlines manufacturing processes
- Early manufacturing input saves time and money: Involving manufacturing partners in the design phase prevents expensive changes during production
Design for manufacturability (DFM) principles have evolved from a nice-to-have consideration to an essential engineering discipline. Modern product development cycles demand faster time-to-market while maintaining stringent quality standards, especially in critical applications like medical devices and aerospace systems.
DFM reduces production costs without sacrificing performance by optimizing design choices during the early stages of product development. The cost of poor manufacturability decisions compounds throughout the product lifecycle. A design feature that looks elegant in CAD software might require specialized tooling, extended lead times, or precision machining that increases part costs significantly.
Understanding design for manufacturability principles from the start prevents these expensive surprises and enables engineers to create products that are easier to produce, assemble, and maintain.
Definition
What is Design for Manufacturability?
Design for manufacturability is the practice of designing products to optimize manufacturing processes, reduce costs, and improve quality. This engineering methodology involves considering manufacturing constraints, material properties, and production capabilities during the design phase rather than after completion.
The fundamental goal of DFM is to create designs that manufacturers can produce efficiently while meeting all functional requirements. This approach minimizes the number of manufacturing steps, reduces material waste, and eliminates features that complicate production without adding value.
Core DFM Principle: Simplification First
Eliminating Unnecessary Complexity
The most common manufacturing challenge engineers create is over-designing parts with features that provide no functional benefit. Complex curved surfaces, multiple varying radii, and decorative elements dramatically increase machining time and cost.
Consider a typical aluminum housing with rounded exterior corners. While aesthetically pleasing, these features often serve no functional purpose but require multiple tool changes, specialized programming, and extended machining time. The same part with sharp corners and chamfers can achieve identical performance at a fraction of the manufacturing cost.
Simplification strategies include:
- Geometric simplification: Replace complex curves with straight lines and standard radii where functionally acceptable
- Feature consolidation: Combine multiple small features into larger, easier-to-machine elements
- Orientation optimization: Align features with standard X, Y, and Z planes to minimize five-axis machining requirements
- Corner standardization: Use consistent radius values throughout the design to reduce tool changes
Read the full Design for Manufacturability guide.
Managing Draft Angles and Transitions
Parts designed for casting often include draft angles that create manufacturing challenges when prototyped through machining. A 1-degree draft angle on every surface, while necessary for casting, requires specialized tooling and precise programming for CNC machining.
Engineers should create separate design variants optimized for different manufacturing processes. A machining-optimized version eliminates draft angles and uses standard geometric features, while a casting-optimized version incorporates necessary draft and filleting requirements.
Weight Considerations Across Industries
Weight optimization requirements vary significantly between applications and directly impact DFM decisions. Aerospace and space applications often justify complex geometries for weight reduction, while ground-based systems may prioritize manufacturing simplicity.
Space applications frequently require extensive weight analysis before approving design modifications that add material. Even small radius additions for manufacturing optimization must be evaluated by mechanical teams to ensure payload requirements are maintained.
4 Essential Design for Manufacturability Principles
- Design Simplification: If a complex design feature isn't needed for a functional reason, it's adding unnecessary cost and production time.
- Material Selection and Manufacturing Process Alignment: Both of these key decisions have massive impacts on cost and lead times.
- Surface Finish and Adhesion Requirements: For parts with Form-in-Place gaskets, design decisions around adhesion drive important cost and time considerations.
- Standardization of Components: Standardize whenever possible.
Essential Design for Manufacturability Principles
1. Design Simplification
Simplification forms the foundation of effective DFM implementation. Reducing the total number of parts in an assembly decreases material costs, labor requirements, and potential failure points. Each additional component introduces assembly complexity and increases the probability of manufacturing errors.
Successful simplification involves combining multiple parts into single components where possible, eliminating redundant features, and standardizing hardware across the design. This approach reduces inventory requirements and streamlines production processes.
2. Material Selection and Manufacturing Process Alignment
Material selection directly impacts manufacturing feasibility, cost, and lead time. Each manufacturing process has optimal material characteristics, and misalignment between material properties and chosen processes creates unnecessary complexity.
Key material considerations by process:
- CNC Machining: Aluminum alloys machine easily with excellent surface finish, while hardened steels require specialized tooling and slower cutting speeds
- Converting/Die Cutting: Thin elastomers cut cleanly, while thick, dense materials may require waterjet cutting for precision
- Form-in-Place Dispensing: Surface treatments and coatings affect adhesion, requiring material-specific testing and validation
3. Surface Finish and Adhesion Requirements
Surface finish specifications significantly impact manufacturing processes and costs. Extremely smooth finishes can actually impair form-in-place gasket adhesion, requiring additional surface preparation or design modifications.
For applications requiring gasket dispensing, moderate surface roughness often provides better adhesion than mirror finishes. When smooth surfaces are required for other functional reasons, design features like scribe lines or shallow channels can improve gasket adhesion without compromising primary surface requirements.
4. Standardization of Components
Using standard hardware and common geometries throughout a design reduces tooling requirements and simplifies manufacturing setup. Standard fasteners, consistent radii, and common hole sizes enable manufacturers to optimize their processes and reduce changeover time.
Standardization extends to material specifications, where using fewer material grades simplifies procurement and inventory management. This approach also improves supply chain reliability by reducing dependence on specialized materials.
Visit our full Design for Manufacturability resource center.
Tolerance Optimization Strategies
Understanding Tolerance Impact on Manufacturing
Tolerance specifications drive manufacturing cost and lead time more than almost any other design parameter. Unnecessarily tight tolerances force manufacturers to use precision equipment, perform additional quality checks, and implement specialized processes.
The relationship between part size and achievable tolerance creates additional complexity. Large parts with extremely tight tolerances require temperature-controlled environments, stress relief processes, and specialized measurement equipment. Small parts can often achieve tighter tolerances with standard processes.
Tolerance guidelines by feature type:
Feature Type | Recommended Tolerance Range | Manufacturing Impact |
Overall dimensions | ±0.13 mm (±0.005") | Standard machining processes |
Hole locations | ±0.08 mm (±0.003") | Standard tooling and fixturing |
Surface profiles | ±0.05 mm (±0.002") | Precision machining required |
Form-in-place gasket height | ±0.10 mm (±0.004") | Standard dispensing processes |
Geometric Dimensioning and Tolerancing Best Practices
Proper datum structure in GD&T specifications reduces manufacturing complexity and improves part consistency. Features should reference nearby datums rather than distant reference points to minimize thermal expansion effects and measurement uncertainty.
Poor datum structure creates measurement challenges where tight tolerances reference points far from the critical features. This approach introduces cumulative error and requires specialized fixturing for accurate inspection.
Industry-Specific Tolerance Requirements
Different industries have established tolerance expectations based on functional requirements and manufacturing capabilities. Space and defense applications typically demand tighter precision due to extreme operating conditions and critical performance requirements.
Medical device applications often emphasize consistency over absolute precision, focusing on repeatability and traceability throughout manufacturing processes. Understanding these industry-specific requirements helps optimize tolerance specifications for both performance and manufacturability.
Feature Design Guidelines
Corner Radii and Internal Features
Sharp internal corners are impossible to machine with rotating cutting tools. All internal corners require radii, and larger radii reduce manufacturing time by allowing larger cutting tools and faster machining speeds.
The optimal approach specifies the largest acceptable radius for each application. This gives manufacturers flexibility to select appropriate tooling while ensuring functional requirements are met.
Radius recommendations:
- Minimum internal radius: 0.4 mm (0.015") for standard machining
- Preferred internal radius: 1.5 mm (0.060") or larger for optimal tool life
- External radius: Specify maximum allowable rather than exact dimensions
Hardware Integration and Assembly Considerations
Thread specifications should focus on functional requirements rather than manufacturing methods. Specifying thread class and position allows manufacturers to select optimal tapping methods (cut tap vs. roll tap) based on their capabilities and material requirements.
Avoid specifying exact drill sizes for threaded holes unless absolutely necessary. Different tapping methods require different pre-drill sizes, and focusing on final thread quality provides better results with greater manufacturing flexibility.
Five-Axis vs. Three-Axis Feature Orientation
Features aligned with standard X, Y, and Z planes can be machined on three-axis equipment, reducing cost and lead time. Features requiring compound angles or complex orientations necessitate five-axis machining, which increases complexity and cost.
Design reviews should evaluate whether angled features provide functional benefits worth the manufacturing premium. Often, slight design modifications can eliminate five-axis requirements while maintaining performance.
Read our Complete CNC Machining Guide.
Design for Manufacturing and Assembly (DFMA) Integration
Assembly Optimization Principles
Design for assembly (DFA) complements DFM by focusing on ease of assembly and disassembly. Key considerations include minimizing the number of assembly operations, using self-locating features, and designing for single-direction assembly where possible.
Snap-fit connections, twist-lock mechanisms, and magnetic assemblies can eliminate fasteners and reduce assembly time. These approaches also simplify disassembly for maintenance and repair operations.
Modular Design Benefits
Modular design approaches enable parallel manufacturing of subassemblies, reducing overall production time. Modules can be tested independently before final assembly, improving quality control and reducing system-level debugging.
Standardized interfaces between modules also enable product customization without extensive redesign, supporting product family strategies and market segmentation.
Form-in-Place Gasket Design Integration
Dispensing Path Optimization
Form-in-place gasket designs benefit from simplified dispensing paths with minimal starts and stops. Complex path geometries with multiple convergent lines create dispensing challenges and inconsistent bead formation.
Path design recommendations:
- Minimize start/stop locations: Each start/stop creates dimensional variation in ±3 mm zones
- Avoid convergent paths: Multiple gasket lines meeting at single points create material buildup
- Consider wall clearance: Maintain minimum 0.6 mm (0.025") clearance between gasket path and adjacent walls
- Optimize for accessibility: Deep pockets require specialized needles and may limit material options
Surface Preparation Requirements
Gasket adhesion depends on appropriate surface conditions. Extremely smooth surfaces may require texture enhancement through scribe lines or shallow channels to improve adhesion reliability.
Material compatibility testing becomes critical for new surface treatments or coatings. Different gasket materials respond differently to various surface preparations, requiring validation testing during the design phase.
Extended Reach Dispensing Challenges
Gasket paths located more than 6 mm (0.25") below the part surface require specialized long-reach needles and additional process validation. Deep pocket dispensing becomes particularly challenging with particle-filled materials that can clog narrow needle passages.
The combination of small bead sizes, grainy materials, and deep pockets represents the most difficult dispensing scenario. These conditions often require single-pass dispensing rather than standard multi-pass techniques.
Read our complete Form-in-Place Gasket Guide.
Assembly and Integration Considerations
Tolerance Stack-Up Management
Multiple component assemblies require careful tolerance analysis to ensure proper fit and function. Tight individual tolerances can create stack-up conditions where parts cannot assemble despite meeting individual specifications.
Assembly tolerance strategies:
- Analyze worst-case scenarios: Calculate maximum and minimum material conditions for all mating features
- Design compression stops: Prevent over-compression of elastomeric components with mechanical stops
- Consider installation methodology: Small, delicate parts in deep pockets create assembly challenges and potential fallout
Pressure-Sensitive Adhesive Applications
PSA selection significantly impacts assembly processes and lead times. Different adhesive types require different curing conditions, from room temperature bonding to oven curing at elevated temperatures.
Part geometry affects PSA performance, with larger contact areas providing better adhesion reliability. Small, thin parts with PSA backing require careful handling during assembly to prevent adhesive contact with unintended surfaces.
PSA Type | Curing Requirements | Assembly Considerations |
Room temperature cure | 24 hours at 22°C (72°F) | Immediate handling possible |
Heat-activated | 30 minutes at 150°C (302°F) | Specialized curing equipment required |
UV-activated | Light exposure | Transparent substrates only |
Advanced Assembly Solutions
Complex assemblies with numerous small components benefit from specialized fixturing and automated installation techniques. Magnetic fixtures can reduce assembly time from hours to minutes for parts with ferromagnetic absorber materials.
These innovative solutions require early collaboration between design and manufacturing teams to identify opportunities for assembly optimization. Custom fixturing development adds initial cost but dramatically improves production efficiency and quality consistency.
Quality Requirements and Manufacturing Impact
Inspection Complexity Factors
Quality requirements directly impact manufacturing lead time and cost. Standard sampling plans provide adequate quality assurance for most applications, while 100% inspection requirements dramatically increase processing time.
Inspection impact factors:
- Sampling vs. 100% inspection: Sampling plans reduce inspection time compared to full inspection
- Feature accessibility: Complex internal features require specialized measurement equipment
- Custom inspection routines: Non-standard tolerance specifications necessitate custom measurement programs
- Documentation requirements: Increased reporting adds administrative time to each part
Industry-Specific Quality Standards
Different industries have varying tolerances for manufacturing optimization. Aerospace applications often prioritize weight reduction over manufacturing simplicity, while medical devices emphasize reliability and traceability.
Space applications typically push dimensional precision requirements due to extreme operating conditions and weight constraints. Military applications focus on durability and long-term reliability, often accepting manufacturing complexity to achieve performance goals.
Medical device applications require enhanced sampling rates and documentation, adding inspection burden rather than manufacturing complexity. This increased quality focus affects lead times more than manufacturing processes.
Common DFM Mistakes to Avoid
Over-Engineering Designs
Engineers often add features that provide minimal functional benefit while significantly increasing manufacturing complexity. Examples include unnecessary surface finishes, overly tight tolerances on non-critical dimensions, and complex geometries where simple shapes would suffice.
Each additional feature requires evaluation against its functional necessity and manufacturing impact. Features that cannot justify their cost through improved performance should be eliminated.
Ignoring Manufacturing Constraints
Designing without considering available manufacturing capabilities leads to costly surprises during production. Understanding equipment limitations, available tooling, and process capabilities prevents designs that cannot be efficiently manufactured.
Regular communication with manufacturing partners during design development ensures compatibility between design intent and production reality.
Late-Stage DFM Implementation
Implementing DFM principles after design completion limits optimization opportunities and increases redesign costs. Early engagement with manufacturing teams identifies potential issues when changes are still inexpensive to implement.
The most effective DFM implementations begin during concept development and continue throughout detailed design phases.
Implementation Strategy for DFM Success
Early Engagement Benefits
Involving manufacturing partners during the design phase prevents costly redesigns and reduces development timelines. Manufacturing input during concept development identifies potential issues before designs become fixed.
Early engagement advantages:
- Process selection optimization: Choose manufacturing methods best suited to design requirements
- Material validation: Confirm material availability and processing characteristics
- Tooling requirements: Identify specialized tooling needs early in development
- Cost optimization: Balance performance requirements with manufacturing constraints
Collaborative Design Reviews
Regular design considerations reviews with manufacturing teams identify optimization opportunities throughout development. These reviews should focus on functional requirements rather than specific manufacturing methods, allowing process experts to recommend optimal approaches.
Manufacturing feedback often reveals alternative approaches that maintain performance while reducing complexity. Simple design modifications can eliminate five-axis machining requirements, reduce tool changes, or improve quality consistency.
Documentation and Communication Standards
Clear communication between design and manufacturing teams requires standardized documentation practices. Drawings should clearly indicate which document takes precedence when discrepancies exist between CAD models and engineering drawings.
Ambiguous documentation creates delays as manufacturing teams seek clarification on conflicting specifications. Establishing clear precedence rules eliminates these delays and reduces the risk of manufacturing errors.
Measuring DFM Success
Key Performance Indicators
Successful DFM implementation delivers measurable improvements in manufacturing metrics. Lead time reduction, cost optimization, and quality improvement provide quantifiable benefits from DFM practices.
DFM success metrics:
- Lead time reduction: Well-designed parts often achieve faster delivery
- Quality improvement: Optimized designs reduce manufacturing defects and rework
- Cost optimization: DFM practices can reduce part costs without performance compromise
- Manufacturability index: Ratio of actual to estimated manufacturing time
Continuous Improvement Integration
DFM principles should integrate with broader continuous improvement initiatives. Manufacturing feedback from production runs identifies additional optimization opportunities for future design iterations.
Post-production reviews capture lessons learned and refine DFM guidelines for future projects. This iterative approach builds organizational DFM capability and improves design quality over time.
Industry-Specific DFM Applications
Medical Device Manufacturing
Medical device DFM emphasizes biocompatibility, sterilization compatibility, and regulatory compliance. Design features must accommodate cleaning requirements, sterilization processes, and traceability needs.
Surface finish requirements for medical devices often exceed those for other industries, requiring specialized manufacturing processes and quality control measures. FDA regulations also mandate extensive documentation and validation throughout the manufacturing process.
Aerospace and Defense Applications
Aerospace DFM balances weight optimization with manufacturing efficiency. Material selection focuses on high-strength-to-weight ratios while considering machining characteristics and availability.
Defense applications require additional considerations for security, supply chain validation, and long-term supportability. Design features must accommodate specialized testing requirements and quality documentation.
Partnering with Manufacturing Experts
Selecting Manufacturing Partners with DFM Expertise
Manufacturing partners with engineering expertise provide valuable design feedback and optimization recommendations. Look for partners with dedicated engineering resources and demonstrated experience in design collaboration.
Vertically integrated manufacturers offer comprehensive DFM support across multiple processes under one roof. This integration eliminates coordination challenges between multiple vendors and provides holistic design optimization.
Leveraging Engineering Expertise for Design Optimization
Manufacturing partners with substantial engineering resources can provide design feedback that prevents costly mistakes and optimization opportunities. Engineering-focused manufacturers understand both functional requirements and manufacturing constraints.
The most effective partnerships involve early engagement during the design phase, when modifications can still be implemented without significant cost or schedule impact. This collaborative approach ensures designs are optimized for both performance and manufacturability.
At Modus Advanced, our engineering team — comprising more than 10% of our staff — works directly with customers to optimize designs for manufacturing efficiency. Our AS9100, ISO 9001, and ITAR certifications ensure we meet the quality and security standards required for critical applications in aerospace, defense, and medical device industries.
Our vertically integrated capabilities allow us to optimize designs across machining, form-in-place dispensing, converting, and assembly processes simultaneously. This comprehensive approach reduces lead times while maintaining the precision quality that lives depend on.
Whether you're developing life-saving medical devices or mission-critical aerospace systems, partnering with manufacturing experts who understand DFM principles accelerates your path to market. Because when lives are at stake, one day matters.