EMI Gaskets: Essential Components in Aircraft Avionics
March 28, 2025
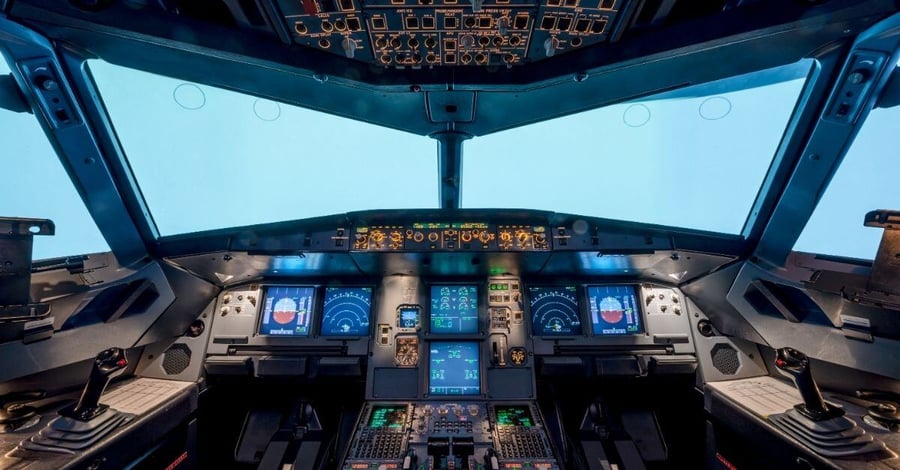
Manufactured with Speed and Precision
The manufacturing capabilities you need and the engineering support you want, all from a single partner.
Submit a DesignKey Points
- EMI gaskets play a critical role in protecting sensitive avionics equipment from electromagnetic interference, directly impacting flight safety and system reliability
- Material selection and design considerations are paramount for aerospace applications due to extreme environmental conditions
- Proper EMI gasket implementation requires understanding of both electrical and mechanical requirements specific to aircraft environments
- Testing and validation processes must align with strict aerospace industry standards and regulations
- Working with an AS9100-certified manufacturing partner ensures compliance and quality in EMI gasket production
When it comes to aircraft avionics, failure is not an option. Every component must perform flawlessly in challenging conditions, and EMI gaskets serve as critical guardians against electromagnetic interference that could compromise vital systems. Understanding their implementation in aerospace applications requires deep technical knowledge and careful consideration of multiple factors. We’re here to help – read on.
Learn everything you need to know about EMI Shielding.
The Critical Role of EMI Gaskets in Modern Aircraft
Modern aircraft rely on an intricate network of electronic systems, from navigation and communication equipment to flight control computers. These systems must operate with absolute reliability while packed into increasingly tight spaces.
EMI gaskets provide the essential shield between these sensitive components, preventing electromagnetic interference that could lead to system failures or degraded performance.
Common Sources of EMI in Aircraft
Aircraft face a complex electromagnetic environment both internally and externally. Before diving into specific EMI gasket solutions, it's important to understand the primary sources of interference:
- High-power radar systems
- Lightning strikes and static electricity
- Radio frequency communications equipment
- Power distribution systems
- Electric motor and actuator operations
- Digital processing equipment
The presence of these various EMI sources makes proper gasket selection and implementation crucial for system reliability.
Material Selection for Aerospace EMI Gaskets
Choosing the right material for an EMI gasket in aerospace applications requires careful consideration of both electrical and environmental factors. The selected material must maintain its shielding effectiveness while withstanding extreme conditions.
Key Material Properties
When selecting your EMI gasket material for aircraft applications, engineers must evaluate several critical properties:
Shielding Effectiveness
Shielding effectiveness across the relevant frequency range must meet or exceed the application's minimum attenuation requirements, typically 60-100 dB depending on the sensitivity of enclosed components. The material's performance should be validated across the entire operational frequency spectrum to ensure no unexpected gaps in protection.
Temperature Resistance
Temperature resistance from -55°C to +125°C is typically required for aerospace applications, ensuring the emi shielding gasket maintains its mechanical and electrical properties throughout extreme environmental conditions encountered at various altitudes. Materials must withstand thermal cycling without degradation of their shielding capabilities or physical properties.
Compression Set Resistance
Compression set resistance determines how well a gasket returns to its original thickness after compression, directly impacting its ability to maintain consistent contact and electrical conductivity over thousands of operational cycles. High-performance aerospace gaskets should exhibit minimal compression set even after prolonged compression at elevated temperatures.
Galvanic Compatibility
Galvanic compatibility with mating surfaces is essential to prevent accelerated corrosion that can compromise both the gasket and the housing materials in the presence of moisture. Engineers must carefully evaluate the galvanic potential between conductive fillers and housing materials to prevent premature system failure.
Fluid And Chemical Resistance
Fluid and chemical resistance to aviation fuels, hydraulic fluids, de-icing agents, and cleaning solvents ensures the gasket maintains its integrity throughout the aircraft's service life. Material compatibility testing with all fluids potentially encountered during operation is critical for certification.
Fire Retardancy And Smoke Toxicity Compliance
Fire retardancy and smoke toxicity compliance with aerospace standards such as FAR 25.853 and ABD0031 is non-negotiable for materials used in commercial and military aircraft applications. Materials must self-extinguish quickly and produce minimal smoke and toxic gases when exposed to flame.
The right combination of these properties ensures long-term performance and reliability in demanding aerospace environments.
-- Article Continues Below --
Visit the full resource center here
Environmental Considerations for Aircraft EMI Gaskets
The aerospace environment presents unique challenges that directly impact EMI gasket performance. These environmental factors must be carefully considered during the design phase to ensure long-term reliability and effectiveness of the EMI gasket installation.
Learn more about our Design for Manufacturability process here
Temperature Extremes
Aircraft EMI gaskets must maintain their protective properties across dramatic temperature variations. Consider these critical factors when designing for thermal conditions:
- Thermal cycling effects on gasket compression
- Material expansion and contraction rates
- Heat aging resistance
- Low-temperature flexibility
- Interface pressure maintenance across temperature range
The ability to maintain consistent performance across these temperature variations is essential for flight safety.
Design Best Practices for Aircraft EMI Gaskets
Proper EMI gasket design requires careful attention to both electrical and mechanical aspects. The gasket must provide consistent EMI shielding while maintaining a reliable seal under all operating conditions.
Flange Design Considerations
The mating flange design plays a crucial role in EMI gasket performance. A well-designed flange should incorporate these elements:
Sufficient Surface Flatness
Sufficient surface flatness ensures consistent contact between the gasket and mating surfaces, preventing gaps that can lead to EMI leakage and environmental ingress. For aerospace applications, a flatness specification of 0.003 inches per foot is typically recommended, though critical applications may require even tighter tolerances.
Appropriate Surface Finish
Appropriate surface finish balances the need for good electrical contact with preventing excessive wear on the gasket material during compression cycles. A surface roughness of 32-64 microinches RMS provides optimal electrical conductivity while minimizing abrasion damage to conductive elastomer gaskets.
Adequate Gasket Compression
Adequate gasket compression stops prevent over-compression that could permanently damage the gasket or create excessive stresses on the housing. Properly designed compression stops maintain the gasket within its optimal compression range, typically 10-30% of the original height depending on the specific material.
Proper Bolt Spacing
Proper bolt spacing ensures uniform compression pressure along the entire gasket length, eliminating potential leak paths. The maximum spacing between fasteners should generally not exceed 2-4 inches for aerospace applications, with closer spacing required for applications with high vibration or pressure differentials.
Galvanically Compatible Plating
Galvanically compatible plating prevents accelerated corrosion between the flange material and the conductive elements in the gasket. Nickel plating on aluminum housings, for example, provides excellent galvanic compatibility with silver-aluminum filled gaskets commonly used in aerospace applications.
The success of an EMI gasket installation largely depends on proper flange design considerations.
Form-in-Place vs. Traditional Gaskets for Aerospace Applications
Choosing between form-in-place (FIP) gaskets and traditional pre-formed gaskets is a critical decision for aerospace applications.
FIP gaskets excel in applications with complex geometries, miniaturized components, and intricate flange paths where traditional gaskets would be difficult to install or require multiple parts. Their ability to be precisely dispensed in continuous beads as narrow as 0.020 inches makes them ideal for increasingly dense avionics packages where space is at a premium.
Traditional pre-formed gaskets offer advantages in standardized layouts, high-volume production, and applications requiring extremely high compression forces or where replacement in the field may be necessary. Their well-established performance history provides confidence for traditional aerospace applications with predictable geometries.
FIP gaskets provide significant weight reduction potential – a critical consideration in aerospace – by eliminating the need for bulky retention hardware and allowing for optimized flange designs. A single FIP gasket can replace multiple pre-formed parts, reducing weight by up to 40% compared to traditional approaches in complex geometries.
FIP technology enables designers to reduce flange widths to as little as 0.030 inches, compared to the minimum 0.120 inches typically required for traditional gaskets, resulting in significant space and weight savings. This capability is particularly valuable in next-generation aerospace designs where every fraction of an ounce matters.
Maintenance considerations favor FIP gaskets for permanent assemblies and traditional gaskets for components requiring field service or regular inspection. The application's service requirements should guide this aspect of the selection process.
Compression Force Management
EMI gaskets require specific compression forces to function effectively. Consider these key aspects when designing for compression:
- Minimum compression force requirements
- Maximum allowable compression
- Compression set resistance
- Load deflection characteristics
- Long-term stress relaxation effects
Proper compression management ensures consistent EMI gasket performance throughout the service life.
Manufacturing Considerations for Aerospace EMI Gaskets
The manufacturing process for aerospace EMI gaskets demands precision and adherence to strict quality standards. Working with an AS9100-certified manufacturer ensures compliance with aerospace requirements and consistent quality.
Quality Control Requirements
Quality control for aerospace EMI gaskets involves rigorous testing and validation:
- Material certification and traceability
- Dimensional verification
- Shielding effectiveness testing
- Environmental testing
- Compression force testing
- Surface conductivity verification
These quality measures help ensure reliable performance in critical aerospace applications.
Integration with Aircraft Systems
EMI gaskets must be properly integrated with various aircraft systems to provide effective shielding. This integration requires careful consideration of system interfaces and installation requirements.
System Interface Requirements
When integrating EMI gaskets into aircraft systems, consider these critical factors:
- Connector interface requirements
- Access panel considerations
- Maintenance requirements
- System grounding requirements
- EMI shield continuity
Proper system integration ensures effective EMI protection across all aircraft systems.
Maintenance and Inspection
Regular maintenance and inspection of EMI gaskets are crucial for ensuring continued protection of aircraft systems. A well-designed maintenance program helps identify potential issues before they impact system performance.
Regular EMI gasket inspections should include:
- Visual inspection for damage or deterioration
- Compression set verification
- Conductivity testing
- Surface finish evaluation
- Fastener torque verification
Proper maintenance ensures continued EMI gasket effectiveness throughout the aircraft's service life.
Working with a Manufacturing Partner
Selecting the right manufacturing partner is crucial for ensuring EMI gasket quality and performance. At Modus Advanced, our engineering-first approach and AS9100 certification ensure we meet the exacting standards required for aerospace applications.
When lives depend on your innovation, you need a partner who understands what's at stake. Our team of engineers works closely with aerospace customers to ensure EMI gaskets meet all performance requirements while maintaining the fastest possible time to market.
Ready to discuss your EMI gasket needs? Contact our engineering team today at (925) 960-8700 or visit our website to learn more about our aerospace manufacturing capabilities.