How Additive Manufacturing Could Transform the Rubber Industry
March 27, 2018
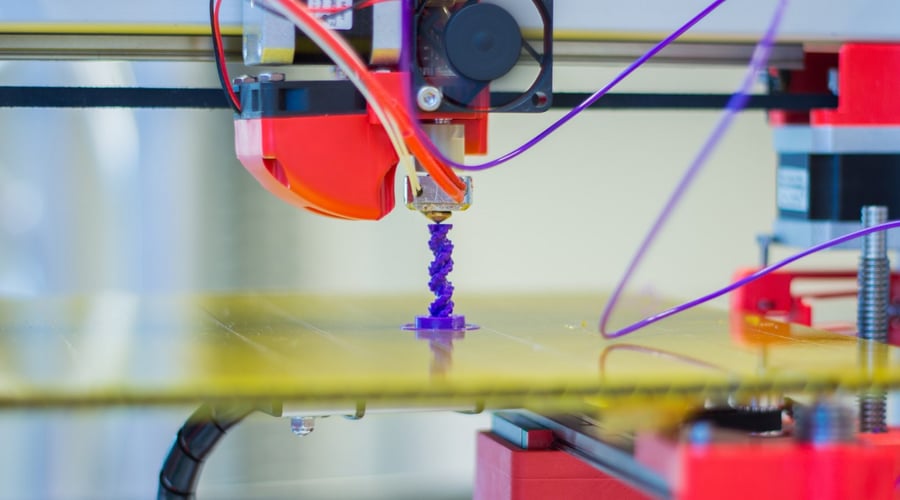
Manufactured with Speed and Precision
The manufacturing capabilities you need and the engineering support you want, all from a single partner.
Submit a DesignAdditive manufacturing (AM), or three-dimensional (3D) printing, is the process of creating a 3D solid object of nearly any shape from a digital model. The technology has lead to innovations in a vast array of industries since the 1980s. The process has widely contributed to the biomedical field with the creation of biocompatible veins, to national security with the production of unique parts for the U.S. nuclear weapons stockpile, and to aerospace applications by more rapidly and simply generating products needed for unmanned aerial vehicles and satellites, among other notable applications. While already impressive, AM technology only continues to mature and diversify.
What is the current rubber part manufacturing process?
Modus Advanced, Inc., has been producing rubber and silicone parts for more than 40 years, using traditional methods such as custom molding. The three primary molding techniques are compression, injection and transfer molding, which have different cost levels and accomplish different technical aspects of molding. The process begins with the design concept for a specific part and is sent to a manufacturer like Modus. The manufacturer then machines the part’s negative shape to produce a metal mold. Next, a rubber or silicone material is either placed, injected or transferred into the mold. The material is cured in a molding press for approximately 8-10 minutes, depending on a various factors including the size of the part. Finally, the mold is removed from the press and taken apart to retrieve the part.
While the process may seem complex, there are a number of key benefits to creating custom molded rubber parts, including:
- A large number of potential sources for custom molded rubber parts
- The ability to draw on decades of rubber compound applications experience to increase project success rates
- Material customization potential
- Prototypes are created, examined and approved prior to mass production
- Complex shapes and sizes are possible to produce
However, building a custom mold often requires 6–10 weeks of lead time alone. “Fortunately, the tooling or mold pays for itself pretty quickly,” says Mike Carson, Field Applications Engineer at Modus. “Producing a mold is a just one-time charge, and the additional costs are labor and material.” This means that once the mold has been created, the production of the actual part afterwards will be much faster.
It’s important to keep in mind that the molding process can be expensive, especially if a customer isn’t confident in their initial specifications or design. For example, if a customer waits the initial 6–10 weeks to receive the first part and isn’t completely satisfied with it—whether the part doesn’t work or design and specifications have changed—a great amount of time and money would be lost. The mold would then have to be refined or even completely remade, adding even more time, money and resources to the process. Timing is everything when trying to meet strict part prototype deadlines. Therefore, it’s crucial to ensure that your part specifications, design and requirements are communicated before the molding process begins.
How does AM work?
Additive manufacturing builds 3D structures and components by layering material from the bottom up. First developed in the 1970s, the AM technique has been adopted more widely in recent years, thanks to advances in materials, sensors, micromechanics, computational modeling and simulation. A precise yet flexible method, AM allows researchers and technicians to customize microstructures and behaviors and engineer materials with novel combinations of properties.
Common to AM technologies is the use of a computer, 3D modeling software (Computer Aided Design or CAD), manufacturing equipment, and layering material. Once a CAD model is produced, the AM equipment reads the data from the file and in most cases lays down or adds successive layers of liquid, powder, sheet material or other materials in a layer-upon-layer fashion to fabricate a 3D object. Please note, the process flow described above has been simplified for purposes of this article.
The term AM encompasses many technologies, including subsets like 3D Printing, Rapid Prototyping (RP), Direct Digital Manufacturing (DDM), layered manufacturing and additive fabrication.
Some people envision AM as a complement to foundational subtractive manufacturing (removing material like drilling out material) and, to lesser degree, forming (like forging). Regardless, AM may offer consumers and professionals alike the ability to create, customize and/or repair a product, and in the process, redefine current production technology.
How can AM be leveraged in the rubber industry?
Additive manufacturing is already being exploited by the rubber industry for some products to drastically reduce product development and production timelines, particularly for low-volume specialty parts and tooling. Modus uses form-in-place (FIP) dispensing to produce gaskets, which is a form of AM. Traditional EMI shielding gaskets are die-cut from a separate piece of material to form a seal between surfaces, but the Nolato Trishield® EMI shielding form-in-place gasket process dispenses a precise string of electrically conductive silicone rubber directly onto one of the surfaces. The electrically conductive Trishield is then cured and formed into its characteristic triangular shape. The resulting EMI shielding gasket requires lower compression force and is typically less expensive than a traditional die cut EMI shielding gasket.
The use of thermoplastic elastomers (TPE’s) to produce rubber-like products to test design concepts is another way design engineers are leveraging AM in the rubber industry. A new generation of rubber-like materials makes it possible to produce parts in as little as one day. Why go to the effort of building a mold to test fit, form and function when a part can be printed in a matter of days?
Key benefits to using AM in the rubber industry include:
- Fast turnaround times
- Less expensive low-volume production
- Multiple material options
- Design rework on the fly
- Reduced waste
Predictions for the Future as They Relate to AM
Modus Advanced's President, Rick MacKirdy, provides insightful predictions into how additive manufacturing will transform the rubber industry in the future.
"The beauty of predictions is that they’re simply educated guesses! So if I were to summarize how AM will transform the rubber industry in the future, I would say AM will dramatically change the rubber manufacturing landscape in a variety of ways. In the near term, AM will have the biggest impact on prototype development as noted above. The advantage of simply printing a part is undeniably the most transformative impact today.
As design engineers continue to migrate towards printed rubber-like prototypes, there’s going to be a natural pull towards using the same manufacturing techniques and materials in production designs. The concept of using the same materials in prototypes and production reduces risk and results in better outcomes.
The demand for higher performance rubber-like materials will probably be satisfied in a couple of ways. Existing AM material suppliers will try to satisfy the demand by introducing products that mimic the physical properties seen in today’s general industrial rubber compounds. Printed rubber-like parts could, and actually are already replacing genuine rubber products in a number of applications.
On the other side of the coin, we’re probably going to see entrenched rubber compounding companies introduce ready to print genuine rubber materials. Wacker Chemie AG recently introduced a technology to print silicone. It’s only a matter of time until other genuine rubber compounds are introduced.
At some point in the near future, my guess is the design freedoms and efficiencies gained from AM will accelerate the introduction of new materials and manufacturing methods. Design engineers will also drive the adoption of AM by giving preference to materials that can be printed. The preference for printing will drive even more innovation in materials and processes to meet the increasing demand!"
Interested in learning more about how Modus Advanced can help create custom molded rubber products for your company? Download our latest guide, Keys to Designing Custom Molded Rubber Products, to see how we take your idea to ignition.