Data Sheets
Browse our library of material data sheets below. If you don't see a material you are interested in, contact us and we'll get the information!
We strive to respond to all quotes within 24 hours or less
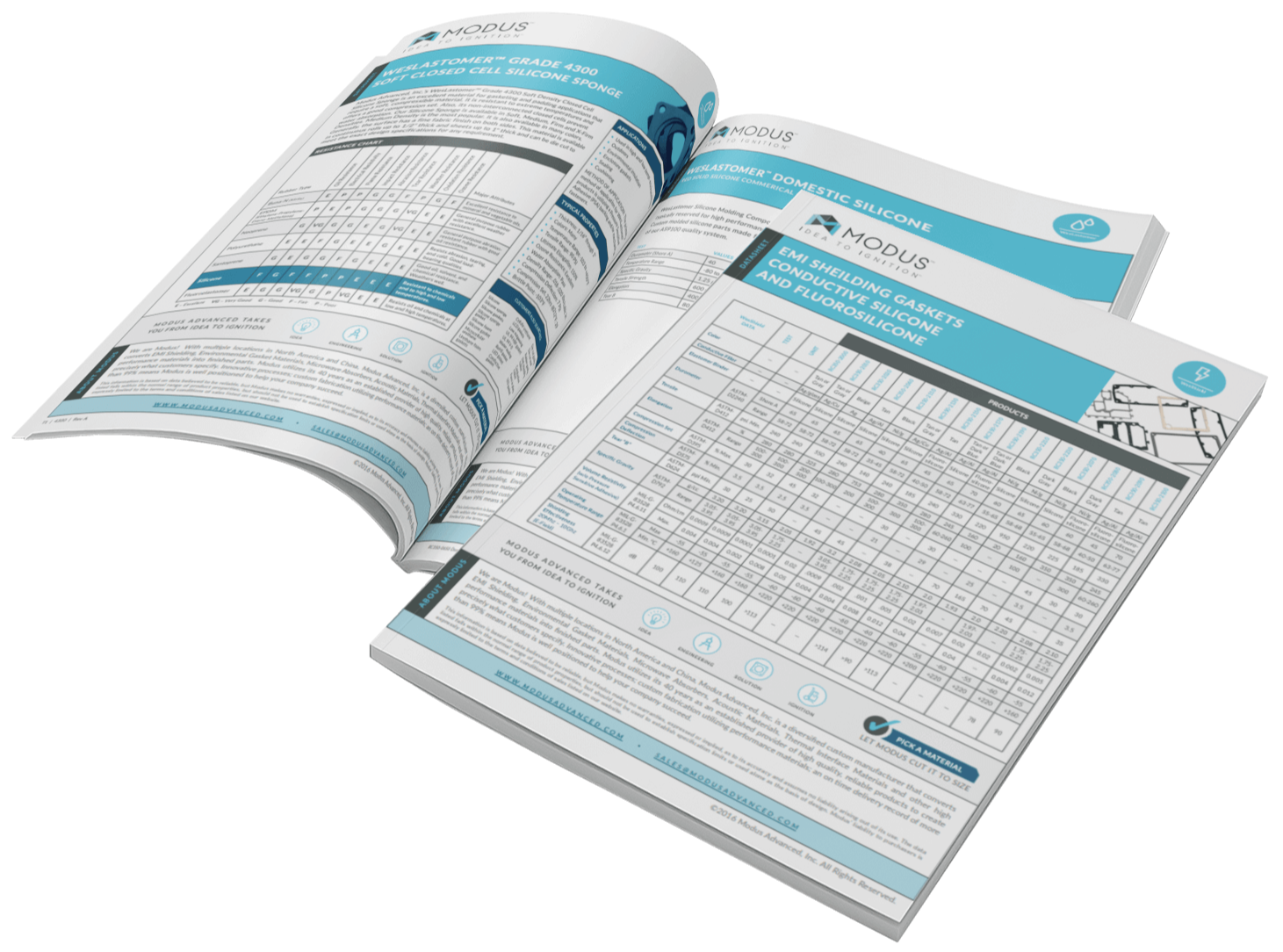
Table of Contents
BISCO® SILICONE FOAM
NOLATO TRISHIELD®
NOLATO TRISHIELD® 2.0
NOLATO COMPASHIELD® EXTRUSION
NOLATO COMPATHERM®
PORON®
ENVIRONMENTAL FIP GASKETS
WESLASTOMER™ SILICONE MOLDING
WESLASTOMER™ RUBBER MOLDING
CLASS 3B SILICONE
WESLASTOMER™ SOLID MATERIALS
WESLASTOMER™ SPONGE MATERIALS
CLASS 3B SILICONE FLEX
MOLDED EMI SHIELDING GASKETS
WESSHIELD™ EMI SHIELDING
THIN FILM THERMAL INTERFACE
HIMAG™ CAVITY RESONANCE ABSORBERS
HIMAG™ LOSSY FOAM ABSORBERS
HIMAG™ RETICULATED FOAM ABSORBERS
HIMAG™ SURFACE WAVE ABSORBERS
HIMAG™ LOW FREQUENCY ATTENUATION
HIMAG™ TUNED FREQUENCY ABSORBER
WESCOUSTIC™ ACOUSTICAL FOAM
SOUND DAMPING FLOORMATS
BISCO® SILICONE FOAM
Bisco Material
Property
Cell Structure
Deflection (psi)
Water Absorption (%)
UL Rating
Temp Rating (F)
Datasheet
Bisco Material:
HT-870
Property:
Soft
Cell Structure:
Open Cell
Deflection (psi):
4
Water Absorption (%):
5
UL Rating:
V-0
Temp Rating (F):
392
Bisco Material:
HT-840
Property:
Extra-Firm
Cell Structure:
Closed Cell
Deflection (psi):
22
Water Absorption (%):
5
UL Rating:
V-0
Temp Rating (F):
V-392
Bisco Material:
HT-820
Property:
Firm
Cell Structure:
Closed Cell
Deflection (psi):
16
Water Absorption (%):
5
UL Rating:
V-0
Temp Rating (F):
392
Bisco Material:
HT-800
Property:
Medium
Cell Structure:
Closed Cell
Deflection (psi):
9
Water Absorption (%):
5
UL Rating:
V-0
Temp Rating (F):
392
Bisco Material:
BF-2000
Property:
Ultra-Soft
Cell Structure:
Open Cell
Deflection (psi):
1.5
Water Absorption (%):
5
UL Rating:
V-0
Temp Rating (F):
392
NOLATO TRISHIELD®
Nolato Number
Conductive Filler
Production Process
Hardness "A"
Volume Resistivity
UL Rating
Datasheet
Nolato Number:
8800
Conductive Filler:
Silver / Nickel
Production Process:
Dispensing
Hardness "A":
55
Volume Resistivity:
15
UL Rating:
V-0
Nolato Number:
8812
Conductive Filler:
Nickel / Graphite
Production Process:
Dispensing
Hardness "A":
80
Volume Resistivity:
15
UL Rating:
V-0
Nolato Number:
8813
Conductive Filler:
Nickel / Graphite
Production Process:
Dispensing
Hardness "A":
73
Volume Resistivity:
25
UL Rating:
HB
NOLATO TRISHIELD® 2.0
Nolato Number
Conductive Filler
Production Process
Hardness ("A")
Volume Resistivity
UL Rating
Datasheet
Nolato Number:
8950
Conductive Filler:
Silicone
Production Process:
Dispensing
Hardness ("A"):
45
Volume Resistivity:
25
UL Rating:
V-0
Nolato Number:
8953
Conductive Filler:
Silicone
Production Process:
Dispensing
Hardness ("A"):
56
Volume Resistivity:
7
UL Rating:
V-0
NOLATO COMPASHIELD® EXTRUSION
Compound Number
Type of Rubber
Conductive Filler
Durometer (Shore A)
UL Rating
Tensile
Volume Resistivity
Shielding Effectiveness
Compression Set (EE version)
Datasheet
Compound Number:
1540
Type of Rubber:
Silicone
Conductive Filler:
N/A
Durometer (Shore A):
40
UL Rating:
V1
Tensile:
8.5
Volume Resistivity:
N/A
Shielding Effectiveness:
N/A
Compression Set (EE version):
10%
Compound Number:
8605
Type of Rubber:
Silicone
Conductive Filler:
Silver / Copper
Durometer (Shore A):
78
UL Rating:
V1
Tensile:
4.2
Volume Resistivity:
3
Shielding Effectiveness:
130
Compression Set (EE version):
35%
Compound Number:
8642
Type of Rubber:
Silicone
Conductive Filler:
Nickel / Carbon
Durometer (Shore A):
80
UL Rating:
V0
Tensile:
4.1
Volume Resistivity:
17
Shielding Effectiveness:
130
Compression Set (EE version):
35%
Compound Number:
8648
Type of Rubber:
Silicone
Conductive Filler:
Nickel / Graphite
Durometer (Shore A):
80
UL Rating:
V0
Tensile:
4.3
Volume Resistivity:
5.6
Shielding Effectiveness:
140
Compression Set (EE version):
10%
NOLATO COMPATHERM®
Nolato Number
Thermal Conductivity (W/m-K)
Hardness (Shore 00)
Density (g/cm3)
Breakdown Voltage (kV/mm)
Color
Datasheet
Nolato Number:
9410
Thermal Conductivity (W/m-K):
1
Hardness (Shore 00):
40
Density (g/cm3):
2.37
Breakdown Voltage (kV/mm):
5
Color:
Pink
Nolato Number:
9411
Thermal Conductivity (W/m-K):
1.3
Hardness (Shore 00):
9
Density (g/cm3):
2.5
Breakdown Voltage (kV/mm):
5
Color:
Light Blue
Nolato Number:
9420
Thermal Conductivity (W/m-K):
2
Hardness (Shore 00):
40
Density (g/cm3):
2.73
Breakdown Voltage (kV/mm):
5
Color:
Light Blue
Nolato Number:
9421
Thermal Conductivity (W/m-K):
2.5
Hardness (Shore 00):
40
Density (g/cm3):
2.70
Breakdown Voltage (kV/mm):
5
Color:
Light Brown
Nolato Number:
9422
Thermal Conductivity (W/m-K):
2
Hardness (Shore 00):
25
Density (g/cm3):
2.70
Breakdown Voltage (kV/mm):
5
Color:
Light Blue
Nolato Number:
9430
Thermal Conductivity (W/m-K):
3
Hardness (Shore 00):
60
Density (g/cm3):
2.65
Breakdown Voltage (kV/mm):
1
Color:
Grey
Nolato Number:
9431
Thermal Conductivity (W/m-K):
3
Hardness (Shore 00):
40
Density (g/cm3):
3.10
Breakdown Voltage (kV/mm):
>8
Color:
Blue
Nolato Number:
9432
Thermal Conductivity (W/m-K):
3
Hardness (Shore 00):
10
Density (g/cm3):
2.92
Breakdown Voltage (kV/mm):
7
Color:
Brown
Nolato Number:
9433
Thermal Conductivity (W/m-K):
3
Hardness (Shore 00):
28
Density (g/cm3):
2.65
Breakdown Voltage (kV/mm):
.4
Color:
Grey
Nolato Number:
9440
Thermal Conductivity (W/m-K):
4
Hardness (Shore 00):
40
Density (g/cm3):
3.10
Breakdown Voltage (kV/mm):
>8
Color:
Green
Nolato Number:
9450
Thermal Conductivity (W/m-K):
5
Hardness (Shore 00):
40
Density (g/cm3):
3.10
Breakdown Voltage (kV/mm):
7
Color:
Black
Nolato Number:
9451
Thermal Conductivity (W/m-K):
5
Hardness (Shore 00):
28
Density (g/cm3):
3.07
Breakdown Voltage (kV/mm):
>5
Color:
Grey
Nolato Number:
9470
Thermal Conductivity (W/m-K):
7
Hardness (Shore 00):
40
Density (g/cm3):
2.55
Breakdown Voltage (kV/mm):
1.5
Color:
Light Grey
Nolato Number:
9471
Thermal Conductivity (W/m-K):
7
Hardness (Shore 00):
40
Density (g/cm3):
3.10
Breakdown Voltage (kV/mm):
>8
Color:
Pink
Nolato Number:
9472
Thermal Conductivity (W/m-K):
7
Hardness (Shore 00):
20
Density (g/cm3):
2.55
Breakdown Voltage (kV/mm):
1.5
Color:
Light Grey
PORON®
Poron Number
Density (psi)
Thickness (inches)
Deflection (psi)
Durometer ("O")
Temperature (F)
UL 94 Rating
Datasheet
Poron Number:
4701-30
Density (psi):
15
Thickness (inches):
.188 to .500
Deflection (psi):
1 to 5
Durometer ("O"):
3
Temperature (F):
194
UL 94 Rating:
HBF (.188")
Poron Number:
4701-30
Density (psi):
20
Thickness (inches):
.062 to .125
Deflection (psi):
3 to 8
Durometer ("O"):
8
Temperature (F):
194
UL 94 Rating:
HBF (.093")
Poron Number:
4701-30
Density (psi):
25
Thickness (inches):
.031 to .045
Deflection (psi):
5 to 12
Durometer ("O"):
16
Temperature (F):
194
UL 94 Rating:
HBF (.062")
Poron Number:
4701-40
Density (psi):
15
Thickness (inches):
.188 to .500
Deflection (psi):
4 to 8
Durometer ("O"):
12
Temperature (F):
194
UL 94 Rating:
HBF (.188")
Poron Number:
4701-40
Density (psi):
20
Thickness (inches):
.062 to .125
Deflection (psi):
7 to 13
Durometer ("O"):
17
Temperature (F):
194
UL 94 Rating:
HBF (.062")
Poron Number:
4701-40
Density (psi):
30
Thickness (inches):
.031 to .045
Deflection (psi):
15 to 40
Durometer ("O"):
34
Temperature (F):
194
UL 94 Rating:
**
Poron Number:
4701-50
Density (psi):
15
Thickness (inches):
.188 to .500
Deflection (psi):
8 to 14
Durometer ("O"):
18
Temperature (F):
194
UL 94 Rating:
HBF (.188")
Poron Number:
4701-50
Density (psi):
20
Thickness (inches):
.062 to .125
Deflection (psi):
13 to 23
Durometer ("O"):
24
Temperature (F):
194
UL 94 Rating:
HBF (.062")
FORM-IN-PLACE ENVIRONMENTAL GASKETS AND SEALS
Part Number
Manufacturer
Manufacturer's Product ID
Durometer
Color
Elongation %
Dielectric Strength (kV/mm)
Non-Slump
UL Rating
Datasheet
Part Number:
AD-120-0301
Manufacturer:
MOMENTIVE
Manufacturer's Product ID:
IS803
Durometer:
23
Color:
Black
Elongation %:
450
Dielectric Strength (kV/mm):
20
Non-Slump:
N/A
UL Rating:
N/A
Part Number:
AD-120-0309
Manufacturer:
MOMENTIVE
Manufacturer's Product ID:
RTV5223
Durometer:
26
Color:
Black
Elongation %:
750
Dielectric Strength (kV/mm):
16.5
Non-Slump:
No
UL Rating:
N/A
Part Number:
AD-120-0404
Manufacturer:
DOW
Manufacturer's Product ID:
732
Durometer:
25
Color:
Black
Elongation %:
550
Dielectric Strength (kV/mm):
21.6
Non-Slump:
Yes
UL Rating:
N/A
Part Number:
AD-120-0414
Manufacturer:
DOW
Manufacturer's Product ID:
732
Durometer:
25
Color:
Aluminum
Elongation %:
550
Dielectric Strength (kV/mm):
21.6
Non-Slump:
Yes
UL Rating:
N/A
Part Number:
AD-120-0415
Manufacturer:
DOW
Manufacturer's Product ID:
732
Durometer:
25
Color:
Clear
Elongation %:
550
Dielectric Strength (kV/mm):
21.6
Non-Slump:
Yes
UL Rating:
N/A
Part Number:
CellAD-120-0416
Manufacturer:
DOW
Manufacturer's Product ID:
732
Durometer:
25
Color:
White
Elongation %:
550
Dielectric Strength (kV/mm):
21.6
Non-Slump:
Yes
UL Rating:
N/A
Part Number:
AD-120-0410
Manufacturer:
POLYMERIC SYSTEMS
Manufacturer's Product ID:
SILI-THANE 803
Durometer:
35
Color:
White
Elongation %:
450
Dielectric Strength (kV/mm):
N/A
Non-Slump:
No
UL Rating:
N/A
Part Number:
AD-120-0411
Manufacturer:
POLYMERIC SYSTEMS
Manufacturer's Product ID:
SILI-THANE 803
Durometer:
35
Color:
Gray
Elongation %:
450
Dielectric Strength (kV/mm):
N/A
Non-Slump:
No
UL Rating:
N/A
Part Number:
AD-120-0412
Manufacturer:
CellPOLYMERIC SYSTEMS
Manufacturer's Product ID:
SILI-THANE 803
Durometer:
35
Color:
Black
Elongation %:
450
Dielectric Strength (kV/mm):
N/A
Non-Slump:
No
UL Rating:
N/A
Part Number:
AD-120-0413
Manufacturer:
POLYMERIC SYSTEMS
Manufacturer's Product ID:
SILI-THANE 803
Durometer:
35
Color:
Limestone
Elongation %:
450
Dielectric Strength (kV/mm):
N/A
Non-Slump:
No
UL Rating:
N/A
WESLASTOMER™ SILICONE MOLDING COMPOUNDS -
DOMESTIC REFERENCE GUIDE
Compound Number
Type of Rubber
Durometer (Shore A)
Temperature Range (F)
Specific Gravity (g/cc)
Tensile Strength (psi)
Elongation (%)
Tear (PPI Die "B")
Datasheet
Compound Number:
RC350-0650
Type of Rubber:
Silicone
Durometer (Shore A):
40
Temperature Range (F):
-80 to +450
Specific Gravity (g/cc):
1.25
Tensile Strength (psi):
600
Elongation (%):
400
Tear (PPI Die "B"):
80
Compound Number:
RC350-0651
Type of Rubber:
Silicone
Durometer (Shore A):
50
Temperature Range (F):
-80 to +450
Specific Gravity (g/cc):
1.45
Tensile Strength (psi):
600
Elongation (%):
300
Tear (PPI Die "B"):
80
Compound Number:
RC350-0652
Type of Rubber:
Silicone
Durometer (Shore A):
60
Temperature Range (F):
-80 to +450
Specific Gravity (g/cc):
1.45
Tensile Strength (psi):
600
Elongation (%):
300
Tear (PPI Die "B"):
80
WESLASTOMER™ RUBBER MOLDING COMPOUNDS -
OVERSEAS REFERENCE GUIDE
Compound Number
Type of Rubber
Durometer (Shore A)
Temperature Range (C)
Specific Gravity (g/cc)
Tensile Strength (Mpa)
Elongation (%)
Tear Strength (KN/m)
Datasheet
Compound Number:
RC350-3100
Type of Rubber:
High Tear Strength Silicone
Durometer (Shore A):
40
Temperature Range (C):
-60 to +220
Specific Gravity (g/cc):
1.13
Tensile Strength (Mpa):
8
Elongation (%):
600
Tear Strength (KN/m):
35
Compound Number:
RC350-3110
Type of Rubber:
High Tear Strength Silicone
Durometer (Shore A):
50
Temperature Range (C):
-60 to +220
Specific Gravity (g/cc):
1.15
Tensile Strength (Mpa):
8.5
Elongation (%):
550
Tear Strength (KN/m):
35
Compound Number:
RC350-3120
Type of Rubber:
High Tear Strength Silicone
Durometer (Shore A):
60
Temperature Range (C):
-60 to +220
Specific Gravity (g/cc):
1.18
Tensile Strength (Mpa):
9
Elongation (%):
500
Tear Strength (KN/m):
40
Compound Number:
RC350-3130
Type of Rubber:
High Tear Strength Silicone
Durometer (Shore A):
70
Temperature Range (C):
-60 to +220
Specific Gravity (g/cc):
1.20
Tensile Strength (Mpa):
8
Elongation (%):
400
Tear Strength (KN/m):
35
Compound Number:
RC350-3200
Type of Rubber:
Commercial Silicone
Durometer (Shore A):
40
Temperature Range (C):
-60 to +220
Specific Gravity (g/cc):
1.13
Tensile Strength (Mpa):
6.5
Elongation (%):
400
Tear Strength (KN/m):
18
Compound Number:
RC350-3210
Type of Rubber:
Commercial Silicone
Durometer (Shore A):
50
Temperature Range (C):
-60 to +220
Specific Gravity (g/cc):
1.15
Tensile Strength (Mpa):
7
Elongation (%):
330
Tear Strength (KN/m):
19
Compound Number:
RC350-3220
Type of Rubber:
Commercial Silicone
Durometer (Shore A):
60
Temperature Range (C):
-60 to +220
Specific Gravity (g/cc):
1.19
Tensile Strength (Mpa):
7.5
Elongation (%):
270
Tear Strength (KN/m):
21
Compound Number:
RC350-3230
Type of Rubber:
Commercial Silicone
Durometer (Shore A):
70
Temperature Range (C):
-60 to +220
Specific Gravity (g/cc):
1.20
Tensile Strength (Mpa):
6.5
Elongation (%):
210
Tear Strength (KN/m):
18
Compound Number:
RC350-3300
Type of Rubber:
Peroxide Cured EPDM
Durometer (Shore A):
40
Temperature Range (C):
-55 to +150
Specific Gravity (g/cc):
1.11
Tensile Strength (Mpa):
5
Elongation (%):
600
Tear Strength (KN/m):
20
Compound Number:
RC350-3310
Type of Rubber:
Peroxide Cured EPDM
Durometer (Shore A):
50
Temperature Range (C):
-55 to +150
Specific Gravity (g/cc):
1.12
Tensile Strength (Mpa):
8
Elongation (%):
550
Tear Strength (KN/m):
25
Compound Number:
RC350-3220
Type of Rubber:
Peroxide Cured EPDM
Durometer (Shore A):
60
Temperature Range (C):
-55 to +150
Specific Gravity (g/cc):
1.14
Tensile Strength (Mpa):
10
Elongation (%):
450
Tear Strength (KN/m):
30
Compound Number:
RC350-3330
Type of Rubber:
Peroxide Cured EPDM
Durometer (Shore A):
70
Temperature Range (C):
-55 to +150
Specific Gravity (g/cc):
1.17
Tensile Strength (Mpa):
10
Elongation (%):
350
Tear Strength (KN/m):
30
Compound Number:
RC350-3400
Type of Rubber:
Commercial EPDM
Durometer (Shore A):
40
Temperature Range (C):
-50 to +130
Specific Gravity (g/cc):
1.11
Tensile Strength (Mpa):
5
Elongation (%):
550
Tear Strength (KN/m):
20
Compound Number:
RC350-3410
Type of Rubber:
Commercial EPDM
Durometer (Shore A):
50
Temperature Range (C):
-50 to +130
Specific Gravity (g/cc):
1.17
Tensile Strength (Mpa):
8
Elongation (%):
450
Tear Strength (KN/m):
25
Compound Number:
RC350-3420
Type of Rubber:
Commercial EPDM
Durometer (Shore A):
60
Temperature Range (C):
-50 to +130
Specific Gravity (g/cc):
1.22
Tensile Strength (Mpa):
10
Elongation (%):
350
Tear Strength (KN/m):
28
Compound Number:
RC350-3430
Type of Rubber:
Commercial EPDM
Durometer (Shore A):
70
Temperature Range (C):
-50 to +130
Specific Gravity (g/cc):
1.23
Tensile Strength (Mpa):
10
Elongation (%):
280
Tear Strength (KN/m):
28
Compound Number:
RC350-3500
Type of Rubber:
Commercial Neoprene
Durometer (Shore A):
40
Temperature Range (C):
-40 to +110
Specific Gravity (g/cc):
1.25
Tensile Strength (Mpa):
7
Elongation (%):
500
Tear Strength (KN/m):
22
Compound Number:
RC350-3510
Type of Rubber:
Commercial Neoprene
Durometer (Shore A):
50
Temperature Range (C):
-40 to +110
Specific Gravity (g/cc):
1.30
Tensile Strength (Mpa):
10
Elongation (%):
400
Tear Strength (KN/m):
28
Compound Number:
RC350-3520
Type of Rubber:
Commercial Neoprene
Durometer (Shore A):
60
Temperature Range (C):
-40 to +110
Specific Gravity (g/cc):
1.35
Tensile Strength (Mpa):
10
Elongation (%):
300
Tear Strength (KN/m):
30
Compound Number:
RC350-3530
Type of Rubber:
Commercial Neoprene
Durometer (Shore A):
70
Temperature Range (C):
-40 to +110
Specific Gravity (g/cc):
1.37
Tensile Strength (Mpa):
10
Elongation (%):
280
Tear Strength (KN/m):
30
Compound Number:
RC350-3600
Type of Rubber:
Commercial Nitrile
Durometer (Shore A):
40
Temperature Range (C):
-40 to +120
Specific Gravity (g/cc):
1.15
Tensile Strength (Mpa):
6
Elongation (%):
500
Tear Strength (KN/m):
20
Compound Number:
RC350-3610
Type of Rubber:
Commercial Nitrile
Durometer (Shore A):
50
Temperature Range (C):
-40 to +120
Specific Gravity (g/cc):
1.23
Tensile Strength (Mpa):
8
Elongation (%):
400
Tear Strength (KN/m):
25
Compound Number:
RC350-3620
Type of Rubber:
Commercial Nitrile
Durometer (Shore A):
60
Temperature Range (C):
-40 to +120
Specific Gravity (g/cc):
1.33
Tensile Strength (Mpa):
10
Elongation (%):
300
Tear Strength (KN/m):
28
Compound Number:
RC350-3700
Type of Rubber:
Commercial SBR
Durometer (Shore A):
40
Temperature Range (C):
-40 to +80
Specific Gravity (g/cc):
1.15
Tensile Strength (Mpa):
6
Elongation (%):
450
Tear Strength (KN/m):
18
Compound Number:
RC350-3710
Type of Rubber:
Commercial SBR
Durometer (Shore A):
50
Temperature Range (C):
-40 to +80
Specific Gravity (g/cc):
1.20
Tensile Strength (Mpa):
8
Elongation (%):
400
Tear Strength (KN/m):
25
Compound Number:
RC350-3720
Type of Rubber:
Commercial SBR
Durometer (Shore A):
60
Temperature Range (C):
-40 to +80
Specific Gravity (g/cc):
1.25
Tensile Strength (Mpa):
10
Elongation (%):
300
Tear Strength (KN/m):
28
Compound Number:
RC350-3730
Type of Rubber:
Commercial SBR
Durometer (Shore A):
70
Temperature Range (C):
-40 to +80
Specific Gravity (g/cc):
1.30
Tensile Strength (Mpa):
10
Elongation (%):
280
Tear Strength (KN/m):
28
Compound Number:
RC350-3800
Type of Rubber:
High Grade TPE
Durometer (Shore A):
60
Temperature Range (C):
-40 to +105
Specific Gravity (g/cc):
1.22
Tensile Strength (Mpa):
12
Elongation (%):
420
Tear Strength (KN/m):
41
Compound Number:
RC350-3810
Type of Rubber:
High Grade TPE
Durometer (Shore A):
70
Temperature Range (C):
-40 to +105
Specific Gravity (g/cc):
1.25
Tensile Strength (Mpa):
14
Elongation (%):
360
Tear Strength (KN/m):
45
Compound Number:
RC350-3900
Type of Rubber:
Commercial TPE
Durometer (Shore A):
60
Temperature Range (C):
-40 to +95
Specific Gravity (g/cc):
.92
Tensile Strength (Mpa):
7
Elongation (%):
360
Tear Strength (KN/m):
38
A-A-59588, CLASS 3B SILICONE REFERENCE GUIDE
Compound Number
Color
Durometer
Low Temp Brittle Point @-70 C
Specific Gravity
Tensile Strength (psi)
Elongation (%)
Tear B (ppi)
HeaderFlex Resistance (140,000 cycles/inch)
Datasheet
Compound Number:
RC350-0250
Color:
Black
Durometer:
50
Low Temp Brittle Point @-70 C:
Pass
Specific Gravity:
1.15
Tensile Strength (psi):
1280
Elongation (%):
660
Tear B (ppi):
240
HeaderFlex Resistance (140,000 cycles/inch):
.42
Compound Number:
RC350-0251
Color:
Gray
Durometer:
50
Low Temp Brittle Point @-70 C:
Pass
Specific Gravity:
1.15
Tensile Strength (psi):
1280
Elongation (%):
660
Tear B (ppi):
240
HeaderFlex Resistance (140,000 cycles/inch):
.42
Compound Number:
RC350-0252
Color:
Red
Durometer:
50
Low Temp Brittle Point @-70 C:
Pass
Specific Gravity:
1.15
Tensile Strength (psi):
1280
Elongation (%):
660
Tear B (ppi):
240
HeaderFlex Resistance (140,000 cycles/inch):
.42
Compound Number:
RC350-0260
Color:
Black
Durometer:
60
Low Temp Brittle Point @-70 C:
Pass
Specific Gravity:
1.19
Tensile Strength (psi):
1280
Elongation (%):
650
Tear B (ppi):
240
HeaderFlex Resistance (140,000 cycles/inch):
.45
Compound Number:
RC350-0261
Color:
Gray
Durometer:
60
Low Temp Brittle Point @-70 C:
Pass
Specific Gravity:
1.19
Tensile Strength (psi):
1280
Elongation (%):
650
Tear B (ppi):
240
HeaderFlex Resistance (140,000 cycles/inch):
.45
WESLASTOMER™ SOLID MATERIALS -
CUSTOM DIE CUT GASKETS REFERENCE GUIDE
WesLastomer Number
Type of Rubber
Specification
Oil Resistance
Electrical Resistivity
Impact Resistance
Abrasion Resistance
Weather Resistance
Datasheet
WesLastomer Number:
Grade 2100
Type of Rubber:
Silicone
Specification:
Commercial
Oil Resistance:
Fair
Electrical Resistivity:
Good
Impact Resistance:
Fair
Abrasion Resistance:
Poor
Weather Resistance:
Excellent
WesLastomer Number:
Grade 2200
Type of Rubber:
Silicone
Specification:
Translucent
Oil Resistance:
Fair
Electrical Resistivity:
Good
Impact Resistance:
Fair
Abrasion Resistance:
Poor
Weather Resistance:
Excellent
WesLastomer Number:
Grade 2300
Type of Rubber:
Fluorosilicone
Specification:
Performance
Oil Resistance:
Good
Electrical Resistivity:
Good
Impact Resistance:
Fair
Abrasion Resistance:
Poor
Weather Resistance:
Excellent
WesLastomer Number:
Grade 2400
Type of Rubber:
Silicone
Specification:
Performance
Oil Resistance:
Fair
Electrical Resistivity:
Good
Impact Resistance:
Fair
Abrasion Resistance:
Poor
Weather Resistance:
Excellent
WesLastomer Number:
Grade 2800
Type of Rubber:
Fiberglass / Silicone
Specification:
Performance
Oil Resistance:
Fair
Electrical Resistivity:
Good
Impact Resistance:
Fair
Abrasion Resistance:
Poor
Weather Resistance:
Excellent
WesLastomer Number:
Grade 3100
Type of Rubber:
Neoprene
Specification:
Commercial
Oil Resistance:
Good
Electrical Resistivity:
Very Good
Impact Resistance:
Good
Abrasion Resistance:
Excellent
Weather Resistance:
Very Good
WesLastomer Number:
Grade 3200
Type of Rubber:
Buna-N / Nitrile
Specification:
Commercial
Oil Resistance:
Excellent
Electrical Resistivity:
Poor
Impact Resistance:
Good
Abrasion Resistance:
Good
Weather Resistance:
Poor
WesLastomer Number:
Grade 3300
Type of Rubber:
EPDM
Specification:
Commercial
Oil Resistance:
Poor
Electrical Resistivity:
Excellent
Impact Resistance:
Good
Abrasion Resistance:
Good
Weather Resistance:
Very Good
WESLASTOMER™ SPONGE MATERIALS -
CUSTOM DIE CUT GASKETS REFERENCE GUIDE
WesLastomer Number
Type of Rubber
Density
Cell Structure
Temperature Range (F)
Impact Resistance
Abrasion Resistance
Weather Resistance
Datasheet
WesLastomer Number:
Grade 4300
Type of Rubber:
Silicone
Density:
Soft
Cell Structure:
Closed
Temperature Range (F):
-103 to +450
Impact Resistance:
Excellent
Abrasion Resistance:
Poor
Weather Resistance:
Excellent
WesLastomer Number:
Grade 4400
Type of Rubber:
Silicone
Density:
Medium
Cell Structure:
Closed
Temperature Range (F):
-103 to +450
Impact Resistance:
Excellent
Abrasion Resistance:
Poor
Weather Resistance:
Excellent
WesLastomer Number:
Grade 4500
Type of Rubber:
Silicone
Density:
Firm
Cell Structure:
Closed
Temperature Range (F):
-103 to +450
Impact Resistance:
Excellent
Abrasion Resistance:
Poor
Weather Resistance:
Excellent
WesLastomer Number:
Grade 4600
Type of Rubber:
Silicone
Density:
Extra-Firm
Cell Structure:
Closed
Temperature Range (F):
-103 to +450
Impact Resistance:
Excellent
Abrasion Resistance:
Poor
Weather Resistance:
Excellent
WesLastomer Number:
Grade 4800
Type of Rubber:
Neoprene Blend
Density:
Soft
Cell Structure:
Closed
Temperature Range (F):
-40 to +250
Impact Resistance:
Excellent
Abrasion Resistance:
Poor
Weather Resistance:
Fair
WesLastomer Number:
Grade 4900
Type of Rubber:
Neoprene Blend
Density:
Medium
Cell Structure:
Closed
Temperature Range (F):
-40 to +250
Impact Resistance:
Excellent
Abrasion Resistance:
Poor
Weather Resistance:
Fair
WesLastomer Number:
Grade 5000
Type of Rubber:
Neoprene Blend
Density:
Medium-Firm
Cell Structure:
Closed
Temperature Range (F):
-40 to +250
Impact Resistance:
Excellent
Abrasion Resistance:
Poor
Weather Resistance:
Fair
WesLastomer Number:
Grade 5100
Type of Rubber:
Neoprene Blend
Density:
Firm
Cell Structure:
Closed
Temperature Range (F):
-40 to +250
Impact Resistance:
Excellent
Abrasion Resistance:
Poor
Weather Resistance:
Fair
A-A-59588 CLASS 3B SILICONE FLEX-FATIGUE RESISTANT DIE CUT GASKETS REFERENCE GUIDE
Compound Number
Thickness (inches)
Durometer
Low Temp Brittle Point @ -70 C
Specific Gravity
Tensile Strength (psi)
Elongation (%)
Tear B (ppi)
Flex Resistance (50,000 cycles/inch)
Datasheet
Compound Number:
RX-230-6635
Thickness (inches):
.020
Durometer:
50
Low Temp Brittle Point @ -70 C:
Pass
Specific Gravity:
1.15
Tensile Strength (psi):
1280
Elongation (%):
660
Tear B (ppi):
240
Flex Resistance (50,000 cycles/inch):
0.42
Compound Number:
RX-230-6636
Thickness (inches):
.032
Durometer:
50
Low Temp Brittle Point @ -70 C:
Pass
Specific Gravity:
1.15
Tensile Strength (psi):
1280
Elongation (%):
660
Tear B (ppi):
240
Flex Resistance (50,000 cycles/inch):
0.42
Compound Number:
RX-230-6637
Thickness (inches):
.062
Durometer:
50
Low Temp Brittle Point @ -70 C:
Pass
Specific Gravity:
1.15
Tensile Strength (psi):
1280
Elongation (%):
660
Tear B (ppi):
240
Flex Resistance (50,000 cycles/inch):
0.42
Compound Number:
RX-230-6638
Thickness (inches):
.093
Durometer:
50
Low Temp Brittle Point @ -70 C:
Pass
Specific Gravity:
1.15
Tensile Strength (psi):
1280
Elongation (%):
660
Tear B (ppi):
240
Flex Resistance (50,000 cycles/inch):
0.42
Compound Number:
RX-230-6639
Thickness (inches):
.125
Durometer:
50
Low Temp Brittle Point @ -70 C:
Pass
Specific Gravity:
1.15
Tensile Strength (psi):
1280
Elongation (%):
660
Tear B (ppi):
240
Flex Resistance (50,000 cycles/inch):
0.42
Compound Number:
RX-230-6640
Thickness (inches):
.020
Durometer:
60
Low Temp Brittle Point @ -70 C:
Pass
Specific Gravity:
1.19
Tensile Strength (psi):
1280
Elongation (%):
650
Tear B (ppi):
240
Flex Resistance (50,000 cycles/inch):
0.45
Compound Number:
RX-230-6641
Thickness (inches):
.032
Durometer:
60
Low Temp Brittle Point @ -70 C:
Pass
Specific Gravity:
1.19
Tensile Strength (psi):
1280
Elongation (%):
650
Tear B (ppi):
240
Flex Resistance (50,000 cycles/inch):
0.45
Compound Number:
RX-230-6642
Thickness (inches):
.062
Durometer:
60
Low Temp Brittle Point @ -70 C:
Pass
Specific Gravity:
1.19
Tensile Strength (psi):
1280
Elongation (%):
650
Tear B (ppi):
240
Flex Resistance (50,000 cycles/inch):
0.45
Compound Number:
RX-230-6643
Thickness (inches):
.093
Durometer:
60
Low Temp Brittle Point @ -70 C:
Pass
Specific Gravity:
1.19
Tensile Strength (psi):
1280
Elongation (%):
650
Tear B (ppi):
240
Flex Resistance (50,000 cycles/inch):
0.45
WESSHIELD™ CUSTOM MOLDED EMI SHIELDING GASKETS REFERENCE GUIDE
Compound Number
Type of Rubber
Conductive Filler
Durometer (Shore A)
Tensile
Volume Resistivity
Shielding Effectiveness
Datasheet
Compound Number:
RC350-2110
Type of Rubber:
Silicone
Conductive Filler:
Nickel / Graphite
Durometer (Shore A):
45
Tensile:
150
Volume Resistivity:
.03
Shielding Effectiveness:
115
Compound Number:
RC350-2130
Type of Rubber:
Silicone
Conductive Filler:
Silver / Copper
Durometer (Shore A):
65
Tensile:
240
Volume Resistivity:
.0009
Shielding Effectiveness:
113
Compound Number:
RC350-2150
Type of Rubber:
Fluorosilicone
Conductive Filler:
Silver / Aluminum
Durometer (Shore A):
45
Tensile:
185
Volume Resistivity:
.002
Shielding Effectiveness:
125
Compound Number:
RC350-2170
Type of Rubber:
Silicone
Conductive Filler:
Silver / Aluminum
Durometer (Shore A):
65
Tensile:
240
Volume Resistivity:
.001
Shielding Effectiveness:
114
Compound Number:
RC350-2190
Type of Rubber:
Fluorosilicone
Conductive Filler:
Silver / Aluminum
Durometer (Shore A):
70
Tensile:
330
Volume Resistivity:
.005
Shielding Effectiveness:
90
WESSHIELD™ DIE CUT EMI SHIELDING GASKETS REFERENCE GUIDE
Manufacturer
Types of Rubber
EMI Shielding
Thickness (inches)
Durometer (Shore A)
Volume Resistivity
Shielding Effectiveness
PSA Available
Datasheet
WESTHERM™ THIN FILM THERMAL INTERFACE MATERIALS
WesTherm Number
Conductivity (W/m-K)
Thickness
Color
UL Rating
Temperature Rating (F)
Film Carrier
Volume Resistivity
Availability
Datasheet
WesTherm Number:
FILM-HB
Conductivity (W/m-K):
1.6
Thickness:
.009
Color:
Pink
UL Rating:
UL94-V0
Temperature Rating (F):
-75 to 350
Film Carrier:
Fiberglass
Volume Resistivity:
1010
Availability:
Die Cut to Size
WesTherm Number:
FILM-FM
Conductivity (W/m-K):
1
Thickness:
.15 mm
Color:
Green / Gray
UL Rating:
UL94-V0
Temperature Rating (F):
-76 to 356
Film Carrier:
Fiberglass
Volume Resistivity:
107
Availability:
Die Cut to Size
WesTherm Number:
FILM-FM
Conductivity (W/m-K):
1
Thickness:
.20 mm
Color:
Green / Gray
UL Rating:
UL94-V0
Temperature Rating (F):
-76 to 356
Film Carrier:
Fiberglass
Volume Resistivity:
107
Availability:
Die Cut to Size
WesTherm Number:
FILM-FM
Conductivity (W/m-K):
1
Thickness:
.30 mm
Color:
Green / Gray
UL Rating:
UL94-V0
Temperature Rating (F):
-76 to 356
Film Carrier:
Fiberglass
Volume Resistivity:
107
Availability:
Die Cut to Size
WesTherm Number:
FILM-GP
Conductivity (W/m-K):
.9
Thickness:
.007
Color:
Gray
UL Rating:
UL94-V0
Temperature Rating (F):
-76 to 356
Film Carrier:
Fiberglass
Volume Resistivity:
1011
Availability:
Die Cut to Size
HIMAG™ CAVITY RESONANCE ABSORBERS REFERENCE GUIDE
Part Number
Frequency (GHz)
Thickness (inches)
Operating Temp (F)
PSA Available
Format
Datasheet
Part Number:
AB340-0058
Frequency (GHz):
14 to 18
Thickness (inches):
.02
Operating Temp (F):
-60 to 375
PSA Available:
Yes
Format:
Die Cut to Print
Part Number:
AB340-0542
Frequency (GHz):
13 to 17
Thickness (inches):
.03
Operating Temp (F):
-60 to 375
PSA Available:
Yes
Format:
Die Cut to Print
Part Number:
AB340-0060
Frequency (GHz):
9 to 12
Thickness (inches):
.04
Operating Temp (F):
-60 to 375
PSA Available:
Yes
Format:
Die Cut to Print
Part Number:
AB340-0061
Frequency (GHz):
6 to 11
Thickness (inches):
.05
Operating Temp (F):
-60 to 375
PSA Available:
Yes
Format:
Die Cut to Print
Part Number:
AB340-0062
Frequency (GHz):
5 to 9
Thickness (inches):
.06
Operating Temp (F):
-60 to 375
PSA Available:
Yes
Format:
Die Cut to Print
Part Number:
AB340-0063
Frequency (GHz):
4 to 7
Thickness (inches):
.07
Operating Temp (F):
-60 to 375
PSA Available:
Yes
Format:
Die Cut to Print
Part Number:
AB340-0064
Frequency (GHz):
3 to 7
Thickness (inches):
.08
Operating Temp (F):
-60 to 375
PSA Available:
Yes
Format:
Die Cut to Print
Part Number:
AB340-0065
Frequency (GHz):
2 to 5
Thickness (inches):
.09
Operating Temp (F):
-60 to 375
PSA Available:
Yes
Format:
Die Cut to Print
Part Number:
AB340-0066
Frequency (GHz):
2 to 5
Thickness (inches):
.10
Operating Temp (F):
-60 to 375
PSA Available:
Yes
Format:
Die Cut to Print
HIMAG™ LOSSY FOAM ABSORBERS REFERENCE GUIDE
Part Number
Frequency (GHz)
dB Loss (@10 GHz)
Thickness (inches)
Operating Temp (F)
PSA Available
Format
Datasheet
Part Number:
AB-340-0083
Frequency (GHz):
2 to 18
dB Loss (@10 GHz):
-8
Thickness (inches):
.125
Operating Temp (F):
-60 to 250
PSA Available:
Yes
Format:
Die Cut to Print
Part Number:
AB-340-0084
Frequency (GHz):
2 to 18
dB Loss (@10 GHz):
-21.5
Thickness (inches):
.25
Operating Temp (F):
-60 to 250
PSA Available:
Yes
Format:
Die Cut to Print
Part Number:
AB-340-0085
Frequency (GHz):
2 to 18
dB Loss (@10 GHz):
-35
Thickness (inches):
.5
Operating Temp (F):
-60 to 250
PSA Available:
Yes
Format:
Die Cut to Print
HIMAG™ RETICULATED FOAM ABSORBERS REFERENCE GUIDE
Part Number
Frequency (GHz)
Thickness (inches)
Operating Temp (F)
PSA Available
Format
Datasheet
Part Number:
AB340-0078
Frequency (GHz):
8 to18
Thickness (inches):
.375
Operating Temp (F):
-60 to 250
PSA Available:
Yes
Format:
Die Cut to Print
Part Number:
AB340-0079
Frequency (GHz):
8 to 40
Thickness (inches):
.5
Operating Temp (F):
-60 to 250
PSA Available:
Yes
Format:
Die Cut to Print
Part Number:
AB340-0081
Frequency (GHz):
5 to 40
Thickness (inches):
1
Operating Temp (F):
-60 to 250
PSA Available:
Yes
Format:
Die Cut to Print
HIMAG™ SURFACE WAVE ABSORBERS REFERENCE GUIDE
Part Number
Frequency (GHz)
Thickness (inches)
Operating Temp (F)
PSA Available
Format
Datasheet
Part Number:
AB340-0068
Frequency (GHz):
14 to 18
Thickness (inches):
0.02
Operating Temp (F):
-60 to 375
PSA Available:
Yes
Format:
Die Cut to Print
Part Number:
AB340-0069
Frequency (GHz):
10 to 14
Thickness (inches):
0.03
Operating Temp (F):
-60 to 375
PSA Available:
Yes
Format:
Die Cut to Print
Part Number:
AB340-0070
Frequency (GHz):
8 to 12
Thickness (inches):
0.04
Operating Temp (F):
-60 to 375
PSA Available:
Yes
Format:
Die Cut to Print
Part Number:
AB340-0071
Frequency (GHz):
5 to 8
Thickness (inches):
0.05
Operating Temp (F):
-60 to 375
PSA Available:
Yes
Format:
Die Cut to Print
Part Number:
AB340-0072
Frequency (GHz):
4 to 7
Thickness (inches):
0.06
Operating Temp (F):
-60 to 375
PSA Available:
Yes
Format:
Die Cut to Print
Part Number:
AB340-0073
Frequency (GHz):
3 to 6
Thickness (inches):
0.07
Operating Temp (F):
-60 to 375
PSA Available:
Yes
Format:
Die Cut to Print
Part Number:
AB340-0074
Frequency (GHz):
3 to 6
Thickness (inches):
0.08
Operating Temp (F):
-60 to 375
PSA Available:
Yes
Format:
Die Cut to Print
Part Number:
AB340-0075
Frequency (GHz):
2 to 4
Thickness (inches):
0.09
Operating Temp (F):
-60 to 375
PSA Available:
Yes
Format:
Die Cut to Print
Part Number:
AB340-0076
Frequency (GHz):
2 to 4
Thickness (inches):
0.10
Operating Temp (F):
-60 to 375
PSA Available:
Yes
Format:
Die Cut to Print
HIMAG™ LOW FREQUENCY ATTENUATION REFERENCE GUIDE
Part Number
Frequency
Permeability (@ 100MHz)
Thickness (inches)
PSA Available
Format
Datasheet
Part Number:
AB340-0105
Frequency:
1 MHz to 3 GHz
Permeability (@ 100MHz):
μ’ = 32
Thickness (inches):
0.005
PSA Available:
Yes
Format:
Die Cut to Print
Part Number:
AB340-0110
Frequency:
1 MHz to 3 GHz
Permeability (@ 100MHz):
μ’ = 32
Thickness (inches):
0.01
PSA Available:
Yes
Format:
Die Cut to Print
Part Number:
AB340-0120
Frequency:
1 MHz to 3 GHz
Permeability (@ 100MHz):
μ’ = 32
Thickness (inches):
0.02
PSA Available:
Yes
Format:
Die Cut to Print
HIMAG™ TUNED FREQUENCY ABSORBER REFERENCE GUIDE
Part Number
Frequency (GHz)
Frequency (GHz)
Operating Temp (F)
PSA Available
Format
Datasheet
Part Number:
AB340-0041
Frequency (GHz):
2.00
Frequency (GHz):
0.12
Operating Temp (F):
-60 to 375
PSA Available:
Yes
Format:
Die Cut to Print
Part Number:
AB340-0045
Frequency (GHz):
6.00
Frequency (GHz):
0.07
Operating Temp (F):
-60 to 375
PSA Available:
Yes
Format:
Die Cut to Print
Part Number:
AB340-0048
Frequency (GHz):
9.00
Frequency (GHz):
0.047
Operating Temp (F):
-60 to 375
PSA Available:
Yes
Format:
Die Cut to Print
Part Number:
AB340-0200
Frequency (GHz):
3.13
Frequency (GHz):
0.095
Operating Temp (F):
-60 to 375
PSA Available:
Yes
Format:
Die Cut to Print
Part Number:
AB340-0201
Frequency (GHz):
4.25
Frequency (GHz):
0.076
Operating Temp (F):
-60 to 375
PSA Available:
Yes
Format:
Die Cut to Print
Part Number:
AB340-0202
Frequency (GHz):
5.15
Frequency (GHz):
0.02
Operating Temp (F):
-60 to 375
PSA Available:
Yes
Format:
Die Cut to Print
Part Number:
AB340-0203
Frequency (GHz):
6.25
Frequency (GHz):
0.068
Operating Temp (F):
-60 to 375
PSA Available:
Yes
Format:
Die Cut to Print
Part Number:
AB340-0204
Frequency (GHz):
8.25
Frequency (GHz):
0.057
Operating Temp (F):
-60 to 375
PSA Available:
Yes
Format:
Die Cut to Print
Part Number:
AB340-0205
Frequency (GHz):
8.50
Frequency (GHz):
0.057
Operating Temp (F):
-60 to 375
PSA Available:
Yes
Format:
Die Cut to Print
Part Number:
AB340-0206
Frequency (GHz):
9.38
Frequency (GHz):
0.057
Operating Temp (F):
-60 to 375
PSA Available:
Yes
Format:
Die Cut to Print
Part Number:
AB340-0207
Frequency (GHz):
10.30
Frequency (GHz):
0.063
Operating Temp (F):
-60 to 375
PSA Available:
Yes
Format:
Die Cut to Print
Part Number:
AB340-0208
Frequency (GHz):
12.50
Frequency (GHz):
0.053
Operating Temp (F):
-60 to 375
PSA Available:
Yes
Format:
Die Cut to Print
Part Number:
AB340-0209
Frequency (GHz):
15.35
Frequency (GHz):
0.043
Operating Temp (F):
-60 to 375
PSA Available:
Yes
Format:
Die Cut to Print
Part Number:
AB340-0210
Frequency (GHz):
20.60
Frequency (GHz):
0.043
Operating Temp (F):
-60 to 375
PSA Available:
Yes
Format:
Die Cut to Print
Part Number:
AB340-0211
Frequency (GHz):
25.00
Frequency (GHz):
0.037
Operating Temp (F):
-60 to 375
PSA Available:
Yes
Format:
Die Cut to Print
Part Number:
AB340-0212
Frequency (GHz):
30.9
Frequency (GHz):
0.032
Operating Temp (F):
-60 to 375
PSA Available:
Yes
Format:
Die Cut to Print
WESCOUSTIC™ ACOUSTICAL FOAM - PERFORATED VINYL FACE REFERENCE GUIDE
Part Number
Thickness (inches)
Facing Color
Barrier
Adhesive
Flammability
Temperature (F)
Custom Kits
Datasheet
Part Number:
SP250-0984
Thickness (inches):
1/2
Facing Color:
Black
Barrier:
Yes
Adhesive:
Yes
Flammability:
MVSS 302
Temperature (F):
-30 to +200
Custom Kits:
Yes
Part Number:
SP250-0595
Thickness (inches):
1
Facing Color:
Black
Barrier:
Yes
Adhesive:
Yes
Flammability:
MVSS 302
Temperature (F):
-30 to +200
Custom Kits:
Yes
Part Number:
SP250-1025
Thickness (inches):
1.5
Facing Color:
Black
Barrier:
Yes
Adhesive:
Yes
Flammability:
MVSS 302
Temperature (F):
-30 to +200
Custom Kits:
Yes
Part Number:
SP250-0985
Thickness (inches):
1/2
Facing Color:
Black
Barrier:
No
Adhesive:
Yes
Flammability:
MVSS 302
Temperature (F):
-30 to +200
Custom Kits:
Yes
Part Number:
SP250-0587
Thickness (inches):
1.5
Facing Color:
Black
Barrier:
No
Adhesive:
Yes
Flammability:
MVSS 302
Temperature (F):
-30 to +200
Custom Kits:
Yes
Part Number:
SP250-1032
Thickness (inches):
1
Facing Color:
Black
Barrier:
No
Adhesive:
No
Flammability:
MVSS 302
Temperature (F):
-30 to +200
Custom Kits:
Yes
WESCOUSTIC™ ACOUSTICAL FOAM - ALUMINIZED POLYESTER FACE REFERENCE GUIDE
WESCOUSTIC™ ACOUSTICAL FOAM - URETHANE FILM FACE REFERENCE GUIDE
Part Number
Thickness (inches)
Facing Color
Barrier
Adhesive
Flammability
Temperature (F)
Custom Kits
Datasheet
Part Number:
SP250-1035
Thickness (inches):
3/8
Facing Color:
Black
Barrier:
No
Adhesive:
Yes
Flammability:
MVSS 302
Temperature (F):
-40 to +225
Custom Kits:
Yes
Part Number:
SP250-1030
Thickness (inches):
5/8
Facing Color:
Black
Barrier:
No
Adhesive:
Yes
Flammability:
MVSS 302
Temperature (F):
-40 to +225
Custom Kits:
Yes
Part Number:
SP250-1040
Thickness (inches):
1/4
Facing Color:
Black
Barrier:
No
Adhesive:
No
Flammability:
MVSS 302
Temperature (F):
-40 to +225
Custom Kits:
Yes
Part Number:
SP250-1034
Thickness (inches):
3/8
Facing Color:
Black
Barrier:
No
Adhesive:
No
Flammability:
MVSS 302
Temperature (F):
-40 to +225
Custom Kits:
Yes
WESCOUSTIC™ SOUND DAMPING FLOORMATS REFERENCE GUIDE
Part Number
Thickness (inches)
Facing Pattern
Barrier
Adhesive
Flammability
Temperature (F)
Custom Kits
Datasheet
Part Number:
RX230-6166
Thickness (inches):
3/8
Facing Pattern:
Pebble
Barrier:
Yes
Adhesive:
Yes
Flammability:
MVSS 302
Temperature (F):
-40 to +250
Custom Kits:
Yes
Part Number:
RX230-1063
Thickness (inches):
3/8
Facing Pattern:
Diamond
Barrier:
Yes
Adhesive:
Yes
Flammability:
MVSS 302
Temperature (F):
-40 to +250
Custom Kits:
Yes