The Best Manufacturing Method To Prototype Custom Molded Rubber Parts
July 25, 2017
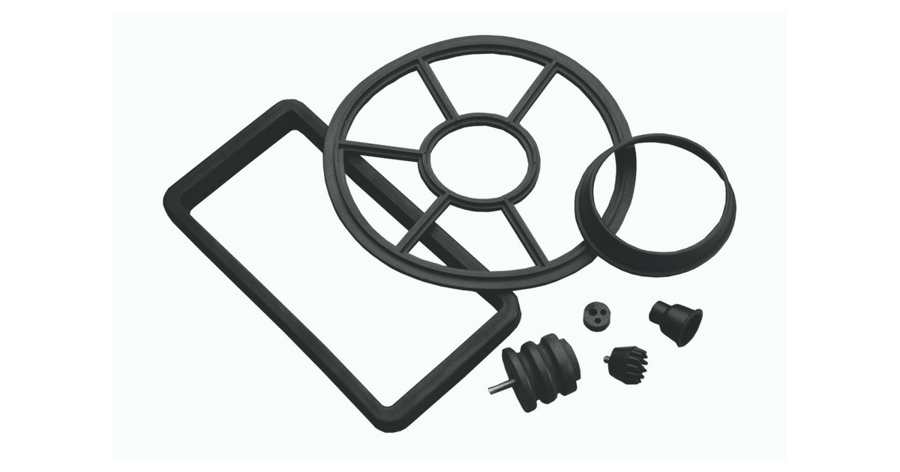
Manufactured with Speed and Precision
The manufacturing capabilities you need and the engineering support you want, all from a single partner.
Submit a DesignEarly on, in my career as a Tool Engineer, I had the opportunity to work extensively with compression molds and the compression molding process. At the time, rubber compression molding was an ideal way to produce the O-rings and seals made in the silicone, fluorosilicone, and nitrile elastomers that my customers wanted.
-- Article Continues Below --
Get all the information you need on custom molded rubber products in our informative guide!
The compression molds themselves were relatively inexpensive; they were fairly easy to operate; and they produced a very high-quality part. This is still true today!
For these same reasons, compression molding is still widely used to produce a variety of parts. Due to their simple construction, mold prices can easily cost less than $2500, and mold delivery times can be relatively short. All engineers know that timing is everything when trying to meet tight part prototype deadlines.
Image: Compression mold bottom plate
What is Rubber Compression Molding?
A basic compression mold, used to make a rubber product, is usually of two-piece construction consisting of a top plate and a bottom plate. Half of the part cavity is usually cut into each plate of the mold. Consequently, when the two-part mold is placed together, it forms the whole. Overflow grooves are then cut around each cavity to provide a trim area, and to allow excess rubber to flow out of the cavity. Compression molds are normally used between heated platens in a press. Uncured rubber pre-forms are loaded in the bottom cavities of the compression mold, and the top plate is placed into position. The press is then closed allowing the rubber to compress, and flow into the cavity. The mold is kept closed until the rubber is cured or at least partially cured. Parts normally come out of the mold interconnected, and usually require a trim operation to separate the parts from the overflow groove. In order to become fully cured, partially cured parts need an additional bake cycle in an oven.
When to use Compression Molding
The compression molding process is normally used to produce all-rubber parts that have a low profile, such as O-rings, seals, and gaskets. Since rubber pre-forms are loaded directly into the mold cavity, compression molding is an ideal method for manufacturing larger, flat, irregularly shaped parts as well. On occasion compression molding has been used to produce rubber parts that have cored-out areas, or for producing parts that require bonding rubber to a metallic or non-metallic component. Injection molding or transfer molding is better suited to produce these types of parts. Many types of elastomers, including natural rubber, neoprene, silicone, fluorosilicone and nitrile, can be used in the compression molding process. It is ideal for producing lower-quantity (low volume) prototype parts but with proper engineering can be used to produce much higher quantity production parts.
Image: Compression mold press
Mold Cost Comparison
Injection, transfer and compression molding are the main methods used to produce rubber parts. When comparing mold costs, compression molds are the least expensive of the three. Injection molds tend to have an intricate runner system that must be machined into the runner plate. An ejector system is normally required to remove parts from the mold. Transfer molds require an integral piston and well pot to transfer rubber. They also normally have an ejector system to remove parts from the mold. Heating sources must be incorporated in an injection or transfer mold.
A compression mold, on the other hand, is normally just two plates which do not require runners, a piston, well pot, or an intricate ejection system. Compressing molding is simply material placed in a mold between two heated platens in a molding press, resulting in a very cost-effective method of producing prototype or low volume rubber parts.
Image: Rubber part prototype
Summary
Compression molding is a great method for producing low-profile rubber parts. Compression molding can be used to produce either lower volume prototype parts or higher volume production parts. Due to its simple construction, mold costs are relatively inexpensive and delivery time is normally shorter compared to that of an injection or transfer mold. Compression molds are easy to operate. Uncured rubber is loaded directly into the mold cavity. This makes compression molding an ideal method for manufacturing large, flat, irregularly shaped parts. Compression molds are normally used between heated platens of a press. An ejection system is not usually required for part removal.
Compression molding does have some draw-backs. It is not always the best choice for producing parts with cored-out areas, or for bonding rubber to a metallic or non-metallic component. There are some steps to consider when engineering the compression molding process, such as preparing uncured rubber pre-forms, or trimming overflow grooved from the part after removal from the mold. Depending on what type of part is being manufactured, compression molding will always have its place in producing prototype or production rubber parts.