RF Absorber Sheets vs. Dispensed RF Absorbers
September 21, 2022
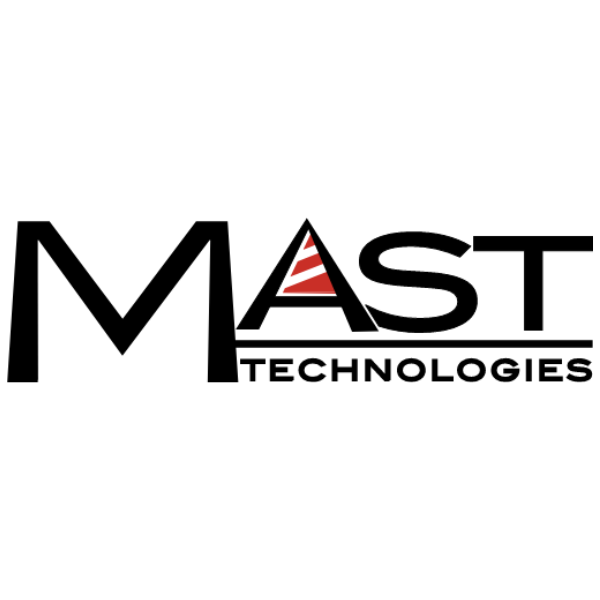
Manufactured with Speed and Precision
The manufacturing capabilities you need and the engineering support you want, all from a single partner.
Submit a DesignInnovation and automation are always on our minds here at Modus Advanced. To hold true to our promise of speed and precision, we’re always on the lookout for new innovations and automation potential. So what’s next you might ask?
Dispensed radiofrequency (RF) absorbers.
Wait, what?
We’ve partnered with MAST Technologies, which designs, develops, and manufactures innovative RF, microwave, and EMI absorbing materials for integration into defense and commercial solutions. They’ve created a cutting-edge dispensable RF absorber material that we are excited to incorporate into our vertically integrated host of manufacturing processes.
Without further ado:
What Is an RF Absorber?
When speaking about RF mitigation, we often see the terms “RF shield” and “RF absorber” used interchangeably, but they aren’t the same. While they do often work in concert with each other and are similar, they execute two distinct functions.
Generally, an RF absorber is a much simpler device than an RF shield. RF absorbers are typically formed from magnetic sheet stock and placed on a flat surface of a device much like a sticker. An RF shield is just that, a shield that encompasses sensitive technology from radiofrequency energy.
Using either magnetic stock material or elastomeric material filled with conductive and ferromagnetic particles, RF absorbers create a sort of electrical field around themselves. They rely on the electric field from metal filler particles or the magnetic field from magnetic materials to polarize incoming radiation, which causes it to remain in the electric field of the absorber. This creates the effect of “absorbing” or “attenuating” the incoming RF energy.
-- Article Continues Below --
Difference Between RF Absorber Sheets and Dispensed RF Absorbers
Before we dig into why one is a better fit than the other, here is a brief overview of the two absorber material options at hand.
RF Absorber Sheets
RF absorber sheets are quite literally sheets of material that have RF absorbing properties, that can be cut to fit the specifications of the cavities in your part. The sheets have an adhesive backing that is manually removed and then carefully placed, by hand, into the cavity per the specifications of your part.
Dispensed RF Absorbers
Much like form-in-place (FIP), the RF absorber compound from MAST Technologies is dispensed using a CNC machine that is programmed to meet your specifications by our expert team of engineers. The process is so precise that surfaces less than 1mm wide can still receive dispensed RF absorber application.
Think of it like filling an oddly shaped decorative bowl with guacamole (perhaps one your grandmother might have brought out on special occasions). The bowl has imperfections, grooves, and dips. If you were to cut a piece of foam to fill the shape of that bowl, it may have gaps or spaces, leading to a suboptimal seal.
Now, imagine filling that bowl with guacamole. Because it is a liquid (albeit chunky and delicious), it touches every bump, dimple, and curve of the bowl leading to a far superior coverage, resulting in a stronger, more durable defense against RFI.
Guacamole has never sounded so cool.
Considerations When Selecting RF Absorber Sheets vs. Dispensed RF Absorbers
We’re of the opinion that dispensed RF absorbers are a great choice for nearly every project that requires RF absorbers, especially in the aerospace and defense industry, and medical device industries. However, there are some considerations to keep in mind as you’re making the decision for your part.
Assembly Requirements
Depending upon the volume of parts you are producing, you may want to weigh the considerations of assembly.
As we mentioned above, an RF absorber sheet is a die-cut piece that is manually applied to the part. On complex and intricate parts with many pieces of RF absorber material needing to be placed, this often means a team member is painstakingly using a pair of tweezers to remove the backing and carefully attach the absorber in its proper position.
There is also the risk here of the adhesive not bonding properly or the absorber slipping from its position. Add in the need for high volume and this becomes incredibly cumbersome and time-consuming.
In highly-intricate scenarios, quality becomes a concern. If the material is not applied precisely and correctly, it could affect the ability of your final part to correctly absorb RF energy.
-- Article Continues Below --
Product Waste
Die-cutting the RF absorber sheet leads to a significant amount of product waste, and while that may not sound like a significant concern, we are cognizant of our responsibility in managing and reducing that waste. Dispensing the RF absorber material is significantly less wasteful as the product is only intentionally dispensed, and leaves no additional scrap product behind. This also has the potential to reduce the overall cost of the project.
You can learn more about our sustainability efforts, learn about our waste-water recycling system, and our investment in solar panels, all on the blog.
Common Misconceptions
Without a doubt, dispensed RF absorbers make sense in many applications. But if you’re looking at two quotes side by side, one for RF absorber sheets and one for dispensed RF absorbers, you may be taken aback by the cost difference.
Before you go looking for a less expensive material as a knee-jerk reaction, let’s break it down.
To start, the material cost of the dispensed RF absorber is higher than the cost of the RF absorber sheets. Die-cutting the RF absorber sheets is a relatively inexpensive manufacturing process, and compared to the material cost of the dispensing liquid, this can come as a shock.
This is the perfect opportunity to zoom out and review the quote from a 10,000 foot view. Similarly to our SigShield™ quotes, once we review the quote in its entirety, customers are able to see that while the material cost is significantly different, your total part cost is decreased.
How so?
The cost savings the customer will see is a decreased labor cost (whether we do the placement of the RF absorber sheets in-house, or you do), and a decreased lead time, which means you can take your product to market sooner. Manual placement can take weeks to complete and costs a significant amount of money in labor. With the increased speed and precision of the dispensed RF absorber, we can cut that time significantly, while ensuring the highest quality is maintained.
Final Thoughts
Ultimately choosing between RF absorber sheets and dispensed RF absorber comes down to a part-by-part discussion. For customers who are already investing in our proprietary SigShield™ product realization process, it is an easy decision.
By partnering with MAST Technologies, we are bringing added value to our customers here at Modus Advanced. We are continually leveraging innovation to meet the challenges our customers have surrounding RF absorbers including labor costs, subpar absorber performance, and product waste, just to name a few.
To get started on your next project, reach out to our team today. Give us a call at 925-960-8700 or contact us online.