RF Blocking: RF Shields vs. RF Absorbers
April 12, 2022
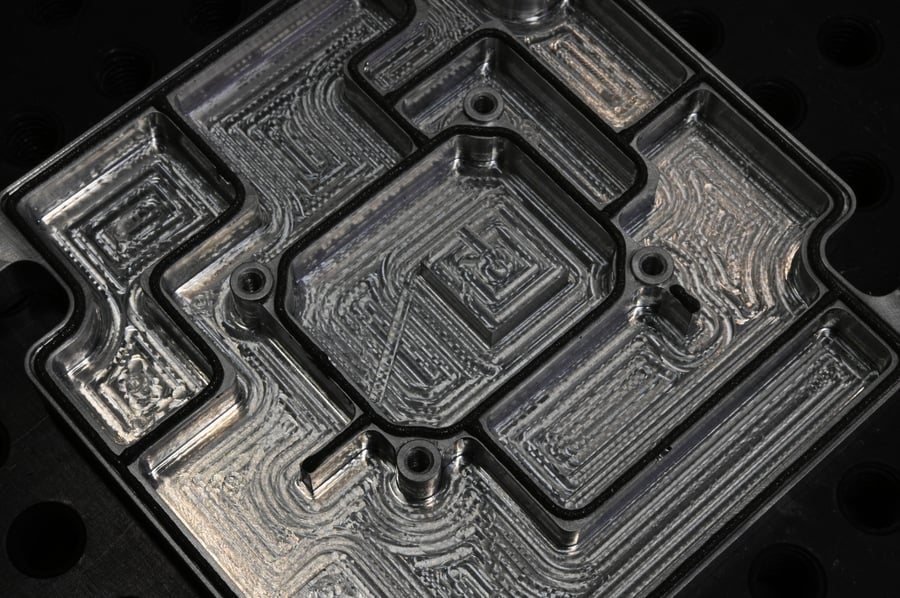
Manufactured with Speed and Precision
The manufacturing capabilities you need and the engineering support you want, all from a single partner.
Submit a DesignKey Points
- RF shields and RF absorbers serve different but complementary functions in managing radio frequency interference (RFI).
- RF shields create a protective barrier that blocks and redirects RF signals, while RF absorbers capture and dissipate RF energy.
- Material selection significantly impacts the effectiveness of both RF shields and RF absorbers.
- Many advanced applications combine both technologies for optimal RF blocking performance.
- Working with a manufacturing partner with extensive experience in RF technologies ensures proper implementation of your RF blocking solution.
Radio frequency (RF) signals surround us constantly in our modern world. Engineers designing sensitive electronic equipment understand that RF interference can compromise the integrity and functionality of their designs. When tasked with protecting components from unwanted RF energy, you have two primary options: RF shields and RF absorbers.
These two technologies, while often mentioned together, function in fundamentally different ways. Understanding these differences helps engineers create more effective designs for aerospace, defense, medical, and telecommunications applications where RF management is critical.
Let's explore the distinctions, applications, and implementation considerations for both RF shields and RF absorbers to help you determine the optimal solution for your specific engineering challenges.

Read Everything You Need To Know About RF Shielding
Definition
What is an RF Shield?
An RF shield is a device — usually made of metal but sometimes formed from plastic — that is designed with one purpose: RF blocking. It is typically formed to create a shielded enclosure that protects particularly RF-sensitive components within it. Alternatively, an RF shield may be formed around an RF-emitting device to block RF signals from escaping and interfering with nearby electronics.
An RF shield forms a protective enclosure that prevents radio frequency signals from entering or exiting a defined space. This three-dimensional barrier typically consists of conductive metals or metallized plastics designed to intercept and redirect electromagnetic energy.
RF shields function based on the principle of a Faraday cage, where external electromagnetic fields are redistributed around the conductive material rather than penetrating it. The effectiveness of an RF shield depends on its material composition, thickness, and the absence of gaps or seams that could allow signal leakage.
Common examples of RF shields include metal housings for electronic components, shielded rooms for MRI facilities, and even the mesh screen in your microwave door. In advanced applications, RF shields often incorporate specialized gaskets to maintain continuity across seams and openings.
Definition
What is an RF Absorber?
Generally, an RF absorber is a much simpler device than an RF shield. RF absorbers are typically formed from magnetic sheet stock and placed on a flat surface of a device much like a sticker.
RF absorbers consist of materials that capture radio frequency energy and convert it into negligible amounts of heat. Unlike shields that redirect signals, absorbers effectively remove the energy from the electromagnetic environment.
These materials typically take the form of flat sheets or specialty coatings containing magnetic or conductive particles that interact with RF fields. When radio waves encounter these materials, they create small electric currents within the particles, which dissipate the energy as minimal heat through resistance.
RF absorbers excel at reducing reflections and standing waves within enclosures. They work particularly well in applications where redirected signals from shields might cause secondary interference problems. Engineers often select specific absorber materials based on the target frequency ranges they need to manage.
Technical Comparison: Shields vs. Absorbers
Understanding the technical differences between RF shields and absorbers helps engineers select the appropriate solution for their specific applications. Let's examine how these technologies compare across various performance characteristics.
Blocking Mechanism
RF shields primarily reflect and redirect RF energy away from protected components. The conductive materials create a low-resistance path that channels electromagnetic fields around the shielded area rather than through it.
RF absorbers convert RF energy into negligible amounts of heat through resistive or magnetic losses. This absorption process effectively removes the energy from the environment rather than redirecting it elsewhere.
Frequency Range Effectiveness
RF shields generally provide broadband protection across wide frequency ranges. Metal shields can be effective from low RF frequencies up through microwave frequencies, though their effectiveness may vary based on material properties and thickness.
RF absorbers typically demonstrate frequency-selective performance. Materials are often engineered for specific frequency bands, with some high-performance absorbers effective from 500 MHz to 18 GHz. Different filler materials and thicknesses optimize performance for particular frequency ranges.
Attenuation Capabilities
RF shields can achieve high levels of attenuation, often providing 60-100 dB of shielding effectiveness in properly designed systems. The attenuation depends significantly on material conductivity, thickness, and the integrity of seams and gaskets.
RF absorbers typically provide 15-30 dB of absorption, though specialized materials can reach higher values in narrower frequency bands. Performance varies significantly based on material composition, thickness, and the specific frequencies involved.
Physical Implementation
RF shields require a complete enclosure with carefully managed seams and apertures. Any gaps can significantly reduce effectiveness, necessitating special attention to gaskets and conductive paths between components.
RF absorbers can be applied as sheets, coatings, or tiles to specific surfaces without needing to form a complete enclosure. This flexibility allows for targeted application where reflections or cavity resonances are problematic.
These technical distinctions highlight why many advanced applications combine both technologies - shields provide broad protection while absorbers manage internal reflections and specific frequency challenges.
Material Science in RF Blocking
The materials used in RF shields and absorbers significantly impact their performance characteristics. Engineers must consider these properties when selecting solutions for specific applications.
RF Shield Materials
Most RF shields utilize highly conductive metals or metallized materials. Each material offers different combinations of weight, cost, and shielding effectiveness:
- Aluminum: Lightweight, cost-effective, and provides good shielding with approximately 60-90 dB attenuation. Operates effectively in temperatures from -30°C to 400°C (-22°F to 752°F).
- Copper: Excellent conductivity and corrosion resistance with 80-100 dB typical attenuation. Functions reliably between -40°C to 350°C (-40°F to 662°F).
- Steel: Provides magnetic shielding properties along with RF shielding. Common in applications requiring both features. Maintains performance from -40°C to 550°C (-40°F to 1022°F).
- Nickel-silver alloys: Offer superior corrosion resistance and consistent performance in harsh environments. Typically provide 70-90 dB attenuation and perform well from -40°C to 400°C (-40°F to 752°F).
- Conductive plastics: Lightweight alternatives incorporating metal fibers or coatings. Provide 40-60 dB shielding while reducing weight and allowing complex molded shapes.
The thickness of these materials directly impacts shielding effectiveness, with thicker materials generally providing better attenuation but adding weight and volume to designs.
RF Absorber Materials
RF absorbers incorporate specialized materials that interact with electromagnetic fields at the molecular level:
- Silicone-based absorbers with ferrite fillers: Flexible, temperature-resistant materials effective from 500 MHz to 18 GHz. Operate reliably from -55°C to 160°C (-67°F to 320°F).
- Iron-loaded epoxy: Rigid absorbers providing high performance from 2-40 GHz. Maintain stability from -40°C to 125°C (-40°F to 257°F).
- Polyurethane foam with carbon loading: Lightweight, broadband absorbers for cavity applications. Function from -40°C to 85°C (-40°F to 185°F).
- Nickel-graphite composites: Provide both conductive and absorptive properties. Especially effective for shielded gaskets requiring both functions. Perform well from -55°C to 125°C (-67°F to 257°F).
- Silver-aluminum filled elastomers: Offer excellent conductivity with moderate absorption properties. Ideal for applications requiring environmental sealing and RF management. Operate effectively from -55°C to 125°C (-67°F to 257°F).
The thickness, particle density, and specific composition of these materials determine their absorption characteristics across different frequency ranges. Engineers must match these properties to their specific interference challenges.
Read the Complete RF Shielding Guide
Design Considerations for RF Blocking
Effective RF blocking requires careful consideration of multiple design factors. Making informed decisions early in the design process helps avoid costly modifications later.
When to Use RF Shields
RF shields prove most effective in these scenarios:
- When broad spectrum protection is required across multiple frequency bands
- For protecting highly sensitive components from external RF sources
- When containing RF emissions from noisy components to prevent interference with other systems
- In applications where a complete physical barrier is needed between RF environments
- When compliance with regulatory emissions standards requires comprehensive shielding
RF shields excel in applications requiring high levels of attenuation across broad frequency ranges. They provide the most comprehensive protection but require careful attention to enclosure integrity.
When to Use RF Absorbers
RF absorbers work best in these situations:
- When reflections within an enclosure create standing waves or resonances
- For reducing cavity resonance in equipment housings
- When specific problematic frequencies need targeted attenuation
- In radar applications where reflection reduction is critical
- When adding shields would create space or weight challenges
RF absorbers provide elegant solutions for managing specific RF challenges without requiring complete enclosures. They complement shields by addressing problems that reflection-based shielding might actually worsen.
Implementation Considerations
Several practical factors influence the selection and implementation of RF blocking solutions:
- Weight constraints: Aerospace and portable applications may require lightweight absorbers instead of heavier metal shields
- Space limitations: Thin absorbers may fit where shields would consume too much volume
- Environmental factors: Temperature, humidity, and chemical exposure affect material selection
- Accessibility requirements: Components requiring frequent access may benefit from targeted absorbers rather than sealed shields
- Cost considerations: Balancing material and manufacturing costs against required performance
- Manufacturing complexity: Form-in-place gaskets for shields require specialized equipment but provide superior performance compared to pre-cut gaskets
Engineers must weigh these practical considerations alongside technical requirements when selecting RF blocking solutions. Working with an experienced manufacturing partner can provide valuable insight into these design decisions.
Visit our Form-in-Place Gasket Resource Center
Combining Shields and Absorbers for Optimal Performance
Many advanced applications benefit from using both RF shields and absorbers together. This combined approach leverages the strengths of each technology to create more effective RF blocking systems.
Complementary Functions
RF shields and absorbers address different aspects of the RF management challenge. Shields provide the primary barrier against external interference, while absorbers manage the internal RF environment. Together, they create a more controlled electromagnetic space.
When external signals penetrate a shield (even minimally), absorbers can capture this energy before it reaches sensitive components. Similarly, absorbers can prevent internal reflections from creating standing waves that might amplify interference within a shielded enclosure.
Implementation Strategies
Effective combined implementations typically follow these approaches:
- Lining the interior of RF shields with absorber material to reduce internal reflections
- Placing targeted absorbers near particularly sensitive components within a shielded enclosure
- Using absorptive gaskets that provide both conductive paths for shielding and absorption properties
- Creating layered shields with absorptive materials between conductive layers for enhanced performance
- Employing absorbers to address specific frequency challenges within a broadly shielded environment
This integrated approach often delivers superior performance compared to either technology alone, especially in complex systems with multiple potential interference sources.
Manufacturing Methods for RF Blocking Solutions
The manufacturing process significantly impacts the performance and reliability of RF blocking solutions. Different technologies require specialized production methods to ensure consistent results.
RF Shield Manufacturing
RF shields require precise manufacturing techniques to maintain their integrity:
- CNC machining: Creates precise metal housings with tight tolerances. This process excels for prototyping and custom designs without requiring hard tooling.
- Custom gasket production: Produces complex shield shapes in high volumes with consistent quality. This method works well for established designs requiring large quantities.
- Form-in-place (FIP) gasket dispensing: Creates precise, custom gaskets directly on shield housings. This specialized process ensures continuity across seams and openings.
- Conductive coating application: Applies metallic layers to plastic components for lightweight shielding. This method enables complex geometries while reducing weight.
The integrity of seams and junctions between shield components critically affects overall performance. Manufacturing processes must account for these potential weak points.
RF Absorber Manufacturing
RF absorbers utilize different production techniques suited to their materials:
- Sheet extrusion: Creates uniform absorber sheets with consistent thickness and material distribution. This process supports high volume production of standard absorber materials.
- Die cutting: Shapes absorber sheets to fit specific applications with precise dimensions. This method creates custom absorber forms from standard sheet stock.
- Injection molding: Forms complex, three-dimensional absorber shapes with embedded particles. This approach suits specialized absorbers requiring particular geometries.
- Spray application: Applies absorptive coatings to irregular surfaces or complex components. This flexible method allows targeted application where pre-formed absorbers wouldn't fit.
- Compression molding: Creates high-density absorbers with carefully controlled particle distribution for enhanced performance in critical applications.
Quality control throughout these manufacturing processes ensures consistent performance across production batches - a critical factor for aerospace, defense, and medical applications.
Testing and Validation of RF Blocking Solutions
Proper testing ensures that RF blocking solutions perform as expected in real-world conditions. Standard methodologies provide consistent metrics for evaluating effectiveness.
Shielding Effectiveness Testing
Industry-standard tests measure how well shields block RF energy:
- MIL-STD-285: Measures attenuation across a standardized frequency range using antennas and signal generators
- IEEE 299: Provides a comprehensive evaluation methodology for larger shielded enclosures
- ASTM D4935: Tests the shielding effectiveness of flat materials and thin sheets
- IEC 61000-4-3: Evaluates immunity of equipment to radiated RF electromagnetic fields
These tests typically express performance in decibels (dB) of attenuation, with higher numbers indicating better shielding effectiveness.
Troubleshooting RF Blocking Issues
Even with careful design and implementation, RF blocking systems sometimes encounter challenges. Understanding common problems and their solutions helps engineers quickly address issues.
Common RF Shield Problems
Several issues frequently affect shield performance:
- Seam leakage: Gaps between shield components allow RF penetration. Solution: Implement proper gaskets or conductive adhesives at all seams.
- Aperture issues: Necessary openings for cooling, displays, or connections compromise shielding. Solution: Add shielded vents, conductive windows, or filtered connectors.
- Grounding problems: Improper grounding reduces shield effectiveness. Solution: Ensure low-impedance connections between shield components and ground.
- Material degradation: Environmental factors may reduce shield performance over time. Solution: Select materials appropriate for the operating environment with suitable corrosion resistance.
- Mechanical stress: Vibration or thermal cycling can create gaps in shields. Solution: Design with flexible gaskets and sufficient mechanical support.
Regular testing helps identify these issues before they cause system failures in critical applications.
Absorber Performance Issues
RF absorbers face different challenges:
- Frequency mismatch: Selected absorbers may not target the problematic frequencies. Solution: Characterize the actual interference spectrum and select appropriate materials.
- Thickness limitations: Space constraints may limit absorber thickness and effectiveness. Solution: Consider multi-layer or higher-performance materials where space permits.
- Environmental degradation: Heat, humidity, or chemicals may affect absorber performance. Solution: Choose materials rated for the operating environment or add protective coverings.
- Delamination: Absorber materials may separate from mounting surfaces. Solution: Implement proper surface preparation and adhesive selection.
- Improper placement: Absorbers must be positioned where RF energy is highest. Solution: Analyze the RF field distribution and place absorbers accordingly.
Addressing these issues early prevents performance degradation in deployed systems and ensures reliable operation throughout the product lifecycle.
Partnering with RF Blocking Experts
Selecting the right manufacturing partner significantly impacts the success of your RF blocking implementation. The right partner brings valuable expertise to complement your design capabilities.
What to Look for in a Manufacturing Partner
Key attributes distinguish high-quality RF blocking manufacturers:
- Technical expertise: Engineers who understand both RF theory and practical implementation challenges
- Vertical integration: Multiple manufacturing capabilities under one roof to reduce complexity and lead times
- Quality systems: AS9100 and ISO 9001 certifications demonstrating commitment to consistent quality
- Experience breadth: Familiarity with your specific industry and application challenges
- Design collaboration: Willingness to engage early in the design process to improve manufacturability
- Testing capabilities: In-house facilities to verify performance against specifications
These characteristics ensure your manufacturing partner can deliver not just components, but comprehensive solutions to your RF blocking challenges.
RF Shield ManufacturingThe Modus Advanced Advantage
Designing effective RF blocking solutions requires both theoretical knowledge and practical manufacturing expertise. At Modus Advanced, we combine deep engineering knowledge with advanced manufacturing capabilities to deliver RF shields and absorbers that perform precisely as specified.
Our engineering team includes experts in RF technology who understand the complex interactions between electronic systems and electromagnetic environments. With over 10% of our staff holding engineering degrees, we provide technical guidance throughout your design process.
Our vertically integrated manufacturing approach brings together multiple capabilities under one roof:
- CNC machining for precision metal housings
- Form-in-place gasket dispensing for reliable RF seals
- RF absorber application and integration
- Comprehensive testing and validation
This integration reduces lead times by up to 50% compared to traditional multi-vendor approaches while maintaining rigorous quality standards. For aerospace, defense, and medical device applications where performance is non-negotiable, this comprehensive approach delivers consistent results.
When lives depend on your technology performing flawlessly, partner with Modus Advanced to ensure your RF blocking solutions meet the highest standards of reliability and performance. Because one day matters.
Ready to discuss your RF blocking needs? Contact our engineering team today for a consultation on your specific application challenges. Call 925-960-8700 or request a quote online.