RF Leakage: Understanding, Detecting, and Preventing Electromagnetic Escape
April 23, 2025
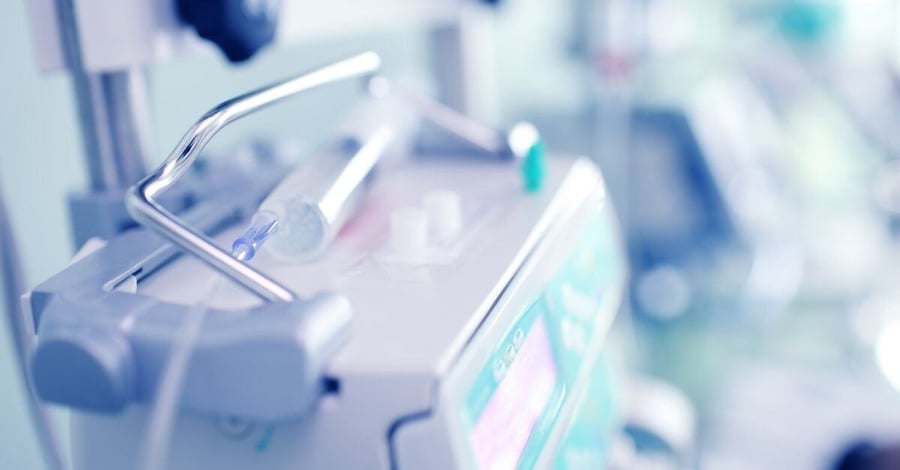
Manufactured with Speed and Precision
The manufacturing capabilities you need and the engineering support you want, all from a single partner.
Submit a DesignKey Points
- RF leakage occurs when electromagnetic radiation escapes from or penetrates into shielded enclosures, potentially causing interference with nearby electronics and compromising device functionality
- Common sources of RF leakage include improperly designed enclosures, gaps in shielding, poorly attached connectors, and damaged cables
- Testing for RF leakage requires specialized equipment like spectrum analyzers and near-field probes to measure and locate electromagnetic emissions
- Prevention strategies include proper enclosure design, using appropriate shielding materials, implementing form-in-place gaskets, and following EMI/EMC best practices
- For mission-critical applications in aerospace, defense, and medical devices, addressing RF leakage is essential for maintaining device performance, security, and regulatory compliance
Definition
RF Leakage Definition
RF leakage occurs when radiofrequency electromagnetic energy escapes from or penetrates into systems designed to contain or block it, creating unintended signal paths through enclosures, cables, connectors or other components. This electromagnetic escape can compromise device performance, trigger malfunctions in nearby equipment, and create compliance issues with regulatory standards in aerospace, defense, and medical applications.
The Hidden Threat of Electromagnetic Escape
RF leakage presents a critical challenge for engineers designing electronic systems where reliability isn't just a preference—it's an absolute necessity. This invisible threat can compromise performance, trigger malfunctions, and even render mission-critical systems inoperable at the most crucial moments.
When electromagnetic radiation escapes from or penetrates into a shielded enclosure, the resulting interference can cascade into serious problems, particularly in aerospace, defense, and medical applications where precision and reliability directly impact human safety. Understanding the fundamentals of RF leakage helps engineers develop more robust designs that maintain electromagnetic integrity even in harsh operational environments.
What Exactly Is RF Leakage?
RF leakage occurs when radiofrequency electromagnetic energy escapes from or penetrates into a system that was designed to contain or block it. This electromagnetic escape happens through unintended paths in enclosures, cables, connectors, or other components.
In high-performance electronics, RF leakage typically manifests in several forms. Radiated emissions occur when electromagnetic energy radiates outward from an enclosure or cable, potentially interfering with nearby devices. Conversely, susceptibility problems arise when external electromagnetic fields penetrate shielding and affect internal components.
The severity of RF leakage depends on several factors including the frequency and power of the signals involved, the quality of shielding, the size of apertures in enclosures, and the proximity of potential victims or sources of interference. Unlike simple electrical leakage, RF leakage can occur without direct contact, propagating through space and penetrating materials that would typically block electrical current.
Why Engineers Should Care About RF Leakage
Engineers working in precision-dependent industries need to give RF leakage serious attention. The implications extend far beyond simple performance degradation.
-- Article Continues Below --

Visit the RF Shielding Resource Center
The Real-World Impact of RF Leakage
For aerospace and defense applications, RF leakage can:
- Compromise radar system accuracy
- Disrupt critical communication systems
- Trigger false alarms in detection equipment
- Create security vulnerabilities for classified communications
- Cause navigation system errors with potentially catastrophic results
In medical device engineering, RF leakage presents equally serious concerns:
- Interference with patient monitoring equipment
- Disruption of diagnostic data accuracy
- Potential malfunction of life-support systems
- Creation of safety hazards during procedures
- Compromised reliability of emergency equipment
Beyond these immediate functional impacts, RF leakage often creates compliance issues with regulatory standards including FCC regulations, MIL-STD-461, and medical device EMC requirements. Addressing RF leakage isn't just best practice—it's often legally required.
Common Sources of RF Leakage
Understanding where RF leakage typically occurs helps engineers address vulnerabilities before they become problems. RF leakage doesn't just happen randomly; specific design weaknesses and component issues create predictable points of failure.
Design Vulnerabilities
Several common design elements frequently contribute to RF leakage issues:
- Seams between enclosure panels
- Access panels and doors
- Ventilation openings
- Control penetrations
- Cable entry points
- Display and indicator openings
Each of these necessary features creates potential paths for RF energy to escape or enter. Proper shielding design accounts for these vulnerabilities from the beginning rather than attempting to patch problems after they emerge.
Component Issues
Even with good design, component-level problems can create RF leakage:
- Damaged or degraded shielding materials
- Improperly terminated cable shields
- Loose connector attachments
- Oxidized or contaminated contact surfaces
- Aging gaskets with reduced conductivity
- Cracked solder joints on shield connections
The gradual degradation of shielding effectiveness often happens as components age, environmental exposure takes its toll, or mechanical stress damages critical connections. This makes regular testing essential for systems where continued shielding integrity is mission-critical.
Detecting RF Leakage: Testing Methods and Equipment
Effective RF leakage management requires appropriate testing approaches and specialized equipment. Testing for RF leakage involves more than simple electrical continuity checks.
Standard Testing Methods
Several standardized testing approaches help identify and quantify RF leakage:
- MIL-STD-285 Shield Effectiveness Testing
- IEEE 299 Shielding Effectiveness Measurements
- CISPR 11/22 Radiated Emissions Testing
- Immunity Testing per IEC 61000-4-3
- Near-Field Scanning
These methods provide structured approaches for evaluating different aspects of electromagnetic containment in various applications and frequency ranges.
Essential Equipment
Properly detecting RF leakage requires specialized test equipment:
Equipment Type | Function | Typical Applications |
Spectrum Analyzer | Measures signal strength across frequency range | Identifying specific frequencies where leakage occurs |
Near-Field Probe Set | Locates specific emission sources | Pinpointing exact leakage locations on enclosures |
EMI Receiver | Performs standards-compliant measurements | Formal compliance testing |
Anechoic Chamber | Eliminates environmental interference | Precise measurement of low-level emissions |
Current Injection Probe | Tests cable shielding | Evaluating cable shield effectiveness |
When selecting test equipment, engineers must consider the frequency range of interest, the required measurement sensitivity, and the specific standards that apply to their application.
Prevention Strategies: Engineering Solutions to RF Leakage
Preventing RF leakage requires thoughtful design and appropriate material selection. The most effective approach combines multiple techniques tailored to the specific application requirements.
Enclosure Design Best Practices
The foundation of RF leakage prevention starts with proper enclosure design:
- Minimize seam lengths where possible: Reducing the overall length of seams in an enclosure decreases the potential areas where RF energy can leak through gaps or discontinuities in the shielding.
- Use overlapping seams rather than butt joints: Overlapping seams create better electrical contact and a longer path for RF energy to travel, significantly reducing leakage compared to simple butt joints where two edges merely touch.
- Implement proper grounding at all seams: Ensuring consistent, low-impedance electrical connections between all enclosure sections maintains shield continuity and prevents RF currents from finding alternative paths.
- Design with appropriate conductive gaskets at all interfaces: Conductive gaskets fill gaps between mating surfaces while maintaining electrical continuity, preventing RF leakage through what would otherwise be open pathways.
- Maintain fastener spacing at less than 1/20th wavelength of highest frequency: Closely spaced fasteners prevent RF waves from escaping through the gaps between attachment points, as wavelengths longer than the gap spacing cannot effectively propagate through the opening.
- Control aperture dimensions to prevent wavelength resonance: Carefully sizing necessary openings (like ventilation holes) prevents them from acting as efficient antennas that can radiate or receive specific problematic frequencies.
These design principles create the mechanical foundation for effective electromagnetic containment. They work best when implemented early in the design process rather than retrofitted after problems emerge.

RF Shielding: Everything You Need to Know
Material Selection for RF Shielding
Choosing the right materials dramatically impacts shielding effectiveness:
- Conductive metals (aluminum, copper, steel)
- Conductive coatings for plastic enclosures
- Specialized EMI gaskets with appropriate filler materials
- Shielded cables with proper coverage percentage
- Ferrite materials for specific frequency absorption
- Conductive adhesives for assembly
Different materials offer varying advantages in terms of weight, cost, corrosion resistance, and shielding effectiveness across frequency ranges. Material selection should align with the specific requirements of the application rather than defaulting to a one-size-fits-all approach.
Form-in-Place Gasket Solutions
For complex geometries and high-performance requirements, form-in-place (FIP) gaskets offer particular advantages in preventing RF leakage:
- Custom application directly to enclosure surfaces
- Ability to follow intricate paths and tight corners
- Consistent compression force across varied surfaces
- Available in various conductivity options
- Excellent environmental sealing properties
- Automation-friendly application process
FIP gaskets represent a significant advancement over traditional pre-cut gaskets, especially for complex enclosures where maintaining continuous shielding presents mechanical challenges.
The Regulatory Landscape: RF Leakage Standards
RF leakage isn't just an engineering concern—it's increasingly a regulatory requirement across multiple industries. Understanding the relevant standards helps engineers design compliant systems from the beginning.
Key Standards by Industry
Different industries focus on specific aspects of RF leakage:
Industry | Key Standards | Focus Areas |
Medical Devices | IEC 60601-1-2, FDA EMC | Patient safety, device functionality |
Defense | MIL-STD-461, MIL-STD-464 | Mission assurance, TEMPEST requirements |
Aerospace | DO-160, Boeing D6-16050 | Aircraft systems compatibility |
Commercial Electronics | FCC Part 15, CISPR 22/32 | Consumer protection, spectrum management |
Compliance with these standards isn't optional—it's a requirement for market access and legal operation in regulated environments. Early consideration of regulatory requirements prevents costly redesigns and certification delays.
Engineering Success: Partnering for RF Integrity
Effective RF leakage prevention requires expertise across multiple disciplines. While internal engineering teams typically understand their product's functional requirements, partnering with specialists in electromagnetic shielding often produces superior results more efficiently.
Look for partners who bring:
- Deep expertise in materials science related to shielding
- Experience with industry-specific regulatory requirements
- Advanced manufacturing capabilities for precision components
- Engineering resources dedicated to shielding design
- Testing capabilities for validating solutions
- Track record in your specific industry or application
When lives and missions depend on electronic system reliability, the right manufacturing partner becomes an extension of your engineering team rather than simply a component supplier.
Visit our Glossary for more definitions of key manufacturing terms.
The Bottom Line on RF Leakage
RF leakage represents a significant challenge for engineers developing mission-critical systems where reliability, security, and performance cannot be compromised. Understanding the fundamentals of RF leakage, implementing appropriate testing protocols, and applying effective prevention strategies helps ensure that electromagnetic interference doesn't undermine system functionality.
For aerospace, defense, and medical device applications, where failures can have life-or-death consequences, addressing RF leakage isn't just good engineering—it's an essential aspect of responsible design. By incorporating proper shielding approaches from the earliest design phases and working with knowledgeable manufacturing partners, engineers can create systems that maintain their electromagnetic integrity even in the most demanding environments.
At Modus Advanced, our engineering team understands the critical nature of RF shielding in your applications. Our vertically integrated manufacturing capabilities—including precision CNC machining, form-in-place gasket dispensing, and RF shielding expertise—deliver solutions that maintain integrity when failure isn't an option. Contact our engineering team to discuss your specific RF leakage prevention needs.