Custom RF Gasket Design for Missile Guidance Systems
April 29, 2025
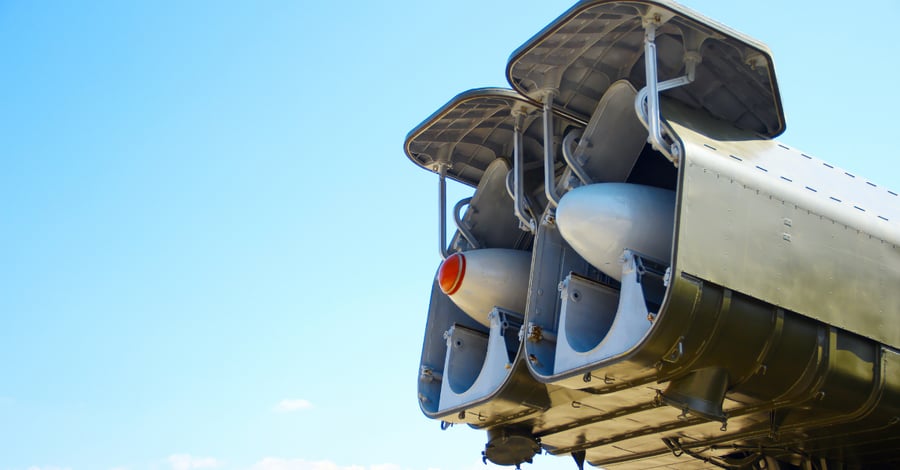
Manufactured with Speed and Precision
The manufacturing capabilities you need and the engineering support you want, all from a single partner.
Submit a Design
Key Points
- RF gaskets play a critical role in missile guidance systems by preventing electromagnetic interference that could compromise targeting accuracy and mission success
- Specialized RF gasket designs must account for extreme environmental conditions including temperature fluctuations, vibration, and potential chemical exposure
- Material selection for defense applications requires balancing conductivity, compression set resistance, and durability while meeting military specifications
- The design process for missile guidance RF gaskets involves close collaboration between engineering teams and manufacturing partners from initial concept through production
- Vertical integration of manufacturing processes significantly reduces lead times and quality risks for these mission-critical components
- Form-in-place (FIP) gasket technology offers precision advantages for the complex, miniaturized geometries common in modern missile guidance systems
Missile guidance systems represent one of the most demanding applications for electromagnetic shielding in the defense industry. These sophisticated electronic assemblies must operate with pinpoint precision while exposed to extreme environments and electromagnetic interference.
RF gaskets serve as the critical line of defense against signal degradation in these systems, ensuring that targeting data remains uncorrupted and communications stay secure. Without proper RF gasket implementation, a guidance system's effectiveness could be compromised, potentially resulting in mission failure with serious consequences.
The stakes couldn't be higher in missile guidance applications, where even momentary electronic failure is unacceptable. This article explores the specialized considerations for RF gasket design in this critical defense application, from material selection to manufacturing processes.
Learn everything you need to know about RF shielding here!
Environmental Challenges for RF Gaskets in Missile Applications
Missile guidance systems must operate across extreme environmental conditions that place exceptional demands on RF gasket performance. These environmental factors significantly influence gasket design and material selection decisions.
Temperature variations represent one of the most significant challenges, with missiles potentially exposed to temperatures ranging from arctic cold to the extreme heat generated during flight. An effective RF gasket must maintain its conductive properties and compression recovery across this entire temperature spectrum. Additionally, the gasket must withstand:
- Extreme vibration during launch and flight phases
- Potential exposure to fuels, hydraulic fluids, and other chemicals
- Rapid pressure changes from sea level to high altitude
- Shock from handling, transportation, and deployment
- Potential salt spray exposure in naval applications
Each of these environmental factors requires careful consideration in the RF gasket design process. For instance, materials that perform well in high temperatures might become brittle in extreme cold, while those with excellent chemical resistance might lack the necessary compression set characteristics for long-term storage.
The combination of these environmental challenges makes missile guidance systems one of the most demanding applications for RF gasket technology. Manufacturers must select materials and designs that provide reliable performance across all potential operating conditions. The military's specific testing and validation requirements further ensure that gaskets will perform as expected when lives and missions depend on them.
Material Selection for Defense-Grade RF Gaskets
Selecting the appropriate material for an RF or EMI gasket in missile guidance systems requires balancing electrical performance with mechanical durability and environmental resistance. The material must not only block electromagnetic interference effectively but also maintain its properties under extreme conditions.
Commonly used conductive fillers for RF gaskets in defense applications include:
Filler Type | Shielding Effectiveness | Environmental Resistance | Galvanic Compatibility |
Silver/Copper | Excellent (>90 dB) | Good | Limited with aluminum |
Silver/Aluminum | Very Good (>100 dB) | Excellent | Excellent with aluminum |
Silver/Nickel | Very Good (>100 dB) | Excellent | Very good |
Nickel/Graphite | Good (>90 dB) | Very Good | Excellent |
The base elastomer gasket material must also be considered carefully. Silicone remains the most common choice due to its temperature resistance and compression set characteristics, but fluorosilicone may be specified when increased resistance to fuels and hydraulic fluids is required.
Material selection also involves careful consideration of military specifications and standards. Most missile guidance systems require materials that comply with specific MIL-SPEC requirements regarding outgassing, flammability, and conductivity. RF gasket materials must not only perform well initially but maintain their properties throughout the system's operational life and storage periods.
Working with a manufacturing partner that understands these complex material requirements is essential for successful rfi gasket implementation in missile guidance systems. The right partner can recommend appropriate materials based on specific application requirements and ensure compliance with all relevant military standards.
RF Gasket Design Process for Missile Guidance Systems
Designing RF gaskets for missile guidance applications involves a methodical approach that balances electromagnetic performance with mechanical and environmental requirements. The design process typically follows these critical phases:
Requirements Analysis
The design process begins with a thorough understanding of the specific shielding requirements and operating environment. This involves analyzing:
- Frequency range requiring attenuation
- Required shielding effectiveness (typically 60-100+ dB)
- Operating temperature range
- Vibration and shock profiles
- Chemical exposure possibilities
- Service life expectations
- Size and weight constraints
Gathering comprehensive requirements at this stage prevents costly redesigns later in the process. This often requires close collaboration between the gasket manufacturer and the guidance system engineering team.
What’s the cost of poor quality? Find out here.
Design Development
Once requirements are established, the actual RF gasket design can begin. This phase focuses on:
- Determining optimal gasket cross-section and profile
- Selecting appropriate compression ratio
- Designing for manufacturability
- Calculating compression force requirements
- Planning for thermal expansion considerations
- Ensuring compatibility with mating surfaces
- Addressing any specialized mounting requirements
For missile guidance applications, designs often need to be extremely compact while still providing excellent shielding performance. Form-in-place (FIP) gasket technology frequently offers advantages in these scenarios, allowing precise application of conductive material directly to complex housing geometries.
Prototyping and Testing
Before full production, prototypes undergo rigorous testing to validate performance:
- Shielding effectiveness testing across the relevant frequency spectrum
- Environmental testing (temperature, humidity, salt spray)
- Compression and compression set testing
- Vibration and shock testing
- Accelerated aging tests
These tests often follow specific military testing protocols to ensure compliance with required standards. Testing may need to be conducted at specialized facilities with appropriate defense certifications.
Production Implementation
After design validation, the final phase involves scaling to production while maintaining strict quality controls:
- Establishing process controls for consistent manufacturing
- Implementing appropriate quality verification steps
- Creating documentation for military qualification
- Developing production test procedures
- Establishing traceability systems for materials and processes
Throughout the entire design process, maintaining close communication between the RF gasket manufacturer and the guidance system developer is essential. The complex nature of missile guidance systems requires this collaborative approach to ensure all requirements are met.
Manufacturing Methods for Precision RF Gaskets
The manufacturing method selected for RF gaskets significantly impacts performance in missile guidance applications. Several techniques are commonly employed, each with distinct advantages for different scenarios.
Form-in-Place (FIP) Gasket Dispensing
FIP dispensing has become increasingly important for missile guidance applications due to its ability to create precise, complex gasket geometries directly on housings. This process involves:
- Computer-controlled dispensing of conductive gasket elastomer material
- Direct application to metal housings or board shields
- Curing through heat or ambient conditions
- Highly automated process control for consistency
For miniaturized guidance components where traditional gaskets would be impractical, FIP technology offers significant advantages in precision and space efficiency. The ability to micro-dispense gaskets makes this technology particularly valuable for modern, compact missile systems.
CNC Machining for Housing Components
High-precision CNC machining is essential for creating the metal housing components that work in conjunction with RF gaskets. This manufacturing method:
- Creates precise mating surfaces for optimal gasket compression
- Maintains tight tolerances required for effective shielding
- Allows for complex design features like compression limiters
- Enables rapid prototyping and design iteration
The quality of the housing's machined surfaces directly impacts gasket performance, making this an essential part of the overall RF shielding solution.
Die Cutting for Traditional Gaskets
While FIP technology is increasingly common, traditional die-cut gaskets still play an important role in certain missile guidance applications:
- Suitable for larger, less complex geometries
- Can utilize specialized materials difficult to dispense via FIP
- Allows for very thin cross-sections when needed
- Often more economical for larger production volumes
The manufacturing method selected must align with the specific requirements of the application. Working with a manufacturing partner that offers multiple production techniques provides the flexibility to select the optimal approach for each unique requirement.
Vertical Integration Benefits for Defense Contractors
Defense contractors developing missile guidance systems face intense pressure to reduce lead times and ensure quality while maintaining strict security requirements. Vertical integration in the manufacturing supply chain offers significant advantages in addressing these challenges.
Working with a vertically integrated manufacturing partner provides several key benefits:
- Reduced lead times by eliminating shipping between multiple vendors
- Enhanced quality control through unified manufacturing processes
- Improved design collaboration across multiple manufacturing disciplines
- Stronger security through fewer external touchpoints
- Simplified quality documentation and traceability
For example, when a single manufacturer can handle RF housing machining, plating, FIP gasket dispensing, and final assembly, the entire production process becomes more streamlined and secure. This integrated approach is particularly valuable for defense applications where production delays can impact national security and mission readiness.
Vertical integration also reduces the risk of miscommunication between different manufacturing vendors, ensuring that the precision tolerances required for effective RF gaskets are maintained throughout the production process. For missile guidance systems, where the consequences of failure are unacceptable, this integrated approach provides significant risk mitigation benefits.
Engineering Reliable Defense Systems
RF gaskets represent a critical component in missile guidance systems, providing essential electromagnetic shielding that ensures these sophisticated electronic enclosure assemblies perform as intended under extreme conditions. From material selection to manufacturing processes, every aspect of the RF gasket design must be carefully considered to meet the demanding requirements of defense applications.
Working with a manufacturing partner that understands these requirements and offers vertically integrated production capabilities can significantly improve outcomes for defense contractors. By combining engineering expertise with advanced manufacturing processes, companies like Modus Advanced help ensure that these mission-critical systems perform reliably when it matters most.
For defense contractors developing next-generation missile guidance systems, partnering with RF gasket specialists early in the design process can prevent costly redesigns and accelerate time to deployment. When lives and mission success depend on electronic performance, having the right RF gasket solution is non-negotiable.