Design for Manufacturing Cost Reduction: Strategic Decisions That Transform Bottom Lines
July 17, 2025
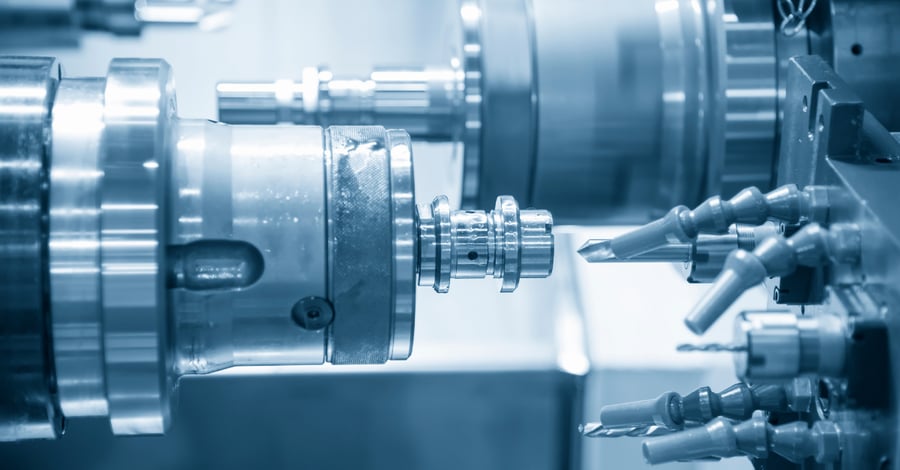
Manufactured with Speed and Precision
The manufacturing capabilities you need and the engineering support you want, all from a single partner.
Submit a DesignKey Points
- Over-engineering drives unnecessary costs: Complex geometries, tight tolerances, and excessive features can multiply manufacturing expenses without adding functional value
- Material and process selection impacts total cost: Early decisions about materials, manufacturing methods, and tolerances create cascading effects on tooling, lead times, and quality control
- Tolerance strategy affects the entire production chain: Unnecessarily tight tolerances increase machining time, inspection requirements, and potential for costly rework
- Design complexity multiplies across manufacturing processes: Features that look elegant in CAD can require specialized tooling, extended lead times, and complex quality procedures
- Early engineering collaboration prevents expensive redesigns: Involving manufacturing partners during design phases identifies cost-saving opportunities before tooling commitments
The Hidden Economics of Design Decisions
Manufacturing costs extend far beyond the price per part. Every design decision creates a ripple effect through tooling requirements, material utilization, production efficiency, and quality control processes.
Smart design for manufacturing (DFM) cost reduction starts with understanding how engineering choices impact total cost of ownership. Research shows that approximately 70% of manufacturing costs are determined during the design phase, making early optimization decisions critical for long-term profitability.
The difference between an optimized design and an over-engineered one can mean the difference between a $50 part and a $500 part — with identical functionality. Understanding these cost multiplication effects enables engineers to make informed decisions that maintain performance while controlling expenses.
Understanding the Cost Multiplication Effect
Geometry Complexity and Machining Economics
Complex geometries create exponential cost increases across multiple manufacturing phases. Curved surfaces with varying radii require multiple tool changes, extended programming time, and specialized inspection procedures.
Simple design modifications can dramatically reduce manufacturing complexity. Sharp corners in machined cavities require additional operations to achieve the necessary radii, while excessive curves demand specialized tooling and extended cycle times.
The most significant cost driver involves features that require five-axis machining instead of standard three-axis operations. Parts with features not aligned to X, Y, and Z planes necessitate either specialized equipment or complex fixturing solutions.
Common Geometry Cost Drivers:
- Varying radii: Multiple tool changes and programming complexity increase cycle times by 200-400%
- Sharp internal corners: Impossible to machine without radii, requiring design modifications and additional operations
- Non-orthogonal features: Force five-axis machining or complex fixturing, multiplying setup and programming time
- Excessive curves: Require specialized tooling and extended inspection procedures
Read the full Design for Manufacturability guide.
Tolerance Strategy and Production Economics for CNC Machined Parts
Tolerance decisions impact every aspect of the manufacturing process. Unnecessarily tight tolerances affect machining time, inspection requirements, and yield rates throughout production.
Manufacturing capabilities vary significantly based on tolerance requirements. Standard machining tolerances allow efficient production using conventional equipment and procedures. Precision tolerances require specialized equipment, environmental controls, and extended quality procedures.
The relationship between tolerance and cost follows an exponential curve. As tolerances tighten beyond ±0.13 mm (±0.005"), costs increase exponentially. Moving from standard tolerances to precision requirements can multiply part costs by factors of three to ten, depending on part complexity and size.
Tolerance Category | Typical Range | Cost Multiplier | Additional Requirements |
Standard | ±0.13 mm (±0.005") | 1x | Standard equipment, sampling inspection |
Precision | ±0.025 mm (±0.001") | 3-5x | Specialized tooling, environmental control |
Ultra-Precision | ±0.010 mm (±0.0004") | 8-15x | Specialized equipment, 100% inspection, stress relief |
Optimizing Design for Cost Efficiency
Strategic Tolerance Management
Effective tolerance management requires understanding which dimensions truly impact part function. Over-constraining features that don't affect performance wastes manufacturing resources and increases production costs.
Datum structure plays a critical role in tolerance economics. Poor datum selection creates measurement complexity and increases the probability of tolerance stack-up issues that lead to expensive rework.
Smart engineers specify the loosest tolerances that maintain part functionality. This approach minimizes manufacturing complexity while ensuring performance requirements are met consistently.
Tolerance Optimization Guidelines:
- Functional analysis: Identify which dimensions actually impact part performance and assembly
- Datum optimization: Reference critical features to nearby elements rather than distant part features
- Stack-up analysis: Ensure tolerance combinations don't create impossible manufacturing conditions
- Process capability alignment: Match tolerance requirements to manufacturing process capabilities
Geometry Simplification Strategies
Simplifying part geometry often improves both manufacturability and functionality. Removing unnecessary features reduces tooling costs, cycle times, and quality control complexity.
Standard machining practices favor simple geometries with consistent radii and orthogonal features. Designs that align with standard tooling and conventional machining practices achieve the best cost-performance balance.
Feature consolidation can eliminate multiple operations and reduce part complexity. Combining features where possible reduces setup requirements and improves production efficiency.
Surface Finish Economics
Surface finish requirements significantly impact manufacturing costs and processing complexity. Specifying appropriate surface finishes based on functional requirements prevents unnecessary processing steps.
Standard machined finishes prove adequate for most applications and require no additional processing. Precision finishes demand additional operations, specialized tooling, and extended quality procedures.
Surface finish affects subsequent processes like coating adhesion and gasket application. Some applications require specific surface textures to ensure proper adhesion, while others benefit from smoother finishes.
Surface Finish | Ra Value | Typical Applications | Cost Impact |
Standard Machined | 1.6-3.2 μm | General applications, non-critical surfaces | Baseline |
Fine Machined | 0.8-1.6 μm | Sealing surfaces, bearing contacts | 50-100% increase |
Ground | 0.2-0.8 μm | Precision surfaces, optical components | 200-400% increase |
Polished | 0.05-0.2 μm | Critical sealing, aesthetic surfaces | 500-1000% increase |
Process Selection and Cost Optimization
Manufacturing Method Economics
Different manufacturing processes suit different production requirements and cost structures. Understanding process capabilities and limitations enables optimal method selection for specific applications.
CNC machining excels for complex geometries and tight tolerances but carries higher per-part costs for large quantities. Die cutting proves efficient for high-volume production of simple geometries but requires tooling investment.
Process selection affects lead times, tooling requirements, and quality capabilities. Smart process selection balances production requirements with cost constraints and delivery schedules.
Process Selection Criteria:
- Volume requirements: High volumes favor dedicated tooling; low volumes suit flexible processes
- Geometry complexity: Complex features may require specialized manufacturing methods
- Tolerance requirements: Precision applications demand process capabilities that match requirements
- Material compatibility: Some materials require specific processing methods or environmental controls
Part Count Reduction and Standardization
Minimizing part counts dramatically affects manufacturing economics. Fewer unique parts increase individual part volumes, which directly impacts unit costs. A part costing $20.00 per unit at 100 units can drop to $2.00 per unit at 5,000 units due to volume economies.
Standardization across product lines creates additional volume benefits. Using identical fasteners, brackets, or components across multiple products increases total volumes and reduces inventory complexity.
Standard off-the-shelf components often cost less than custom parts. Before designing custom components, engineers should search for existing solutions that meet functional requirements.
Tooling Strategy and Investment
Tooling decisions create long-term cost implications that extend far beyond initial investment. Standard tooling reduces costs and lead times, while specialized tooling enables unique capabilities at higher expense.
Tool life and replacement costs affect ongoing production economics. Designs that utilize standard, readily available tooling minimize both initial costs and long-term maintenance requirements.
Complex geometries may require specialized tooling with limited life spans and high replacement costs. Simplifying designs to use standard tooling often proves more economical over the product lifecycle.
Quality and Inspection Economics
Quality requirements significantly impact production costs through inspection procedures, sampling plans, and testing requirements. Balancing quality needs with cost constraints requires understanding which characteristics truly impact product performance.
Sampling inspection proves economical for stable processes and non-critical dimensions. Full inspection becomes necessary for critical characteristics or when process capability doesn't match requirements.
Custom inspection procedures require programming, fixturing, and equipment setup that multiplies quality costs. Standard inspection methods prove more economical when they meet application requirements.
Visit our full Design for Manufacturability resource center.
Implementation Strategies for Cost-Effective Design
Early Collaboration Benefits
Involving manufacturing partners during design phases identifies cost-saving opportunities before tooling commitments. Early collaboration prevents expensive redesigns and enables optimization throughout the development process.
Manufacturing expertise provides insights into process capabilities, material limitations, and design alternatives that maintain functionality while reducing costs. This collaboration often reveals innovative solutions that improve both performance and manufacturability.
Design reviews with manufacturing partners should occur early in the development process when changes can still be implemented cost-effectively. Late-stage design changes often prove expensive and may compromise optimal solutions.
Design Review Framework
Systematic design reviews ensure cost optimization receives appropriate attention throughout development. Structured reviews identify potential issues before they become expensive manufacturing problems.
Effective reviews examine tolerance requirements, material selection, geometry complexity, and manufacturing method compatibility. This comprehensive analysis prevents costly surprises during production startup.
Documentation of design decisions and their rationale enables future optimization and prevents regression to less efficient approaches in subsequent design iterations.
Design Review Checklist:
- Tolerance analysis: Verify all specified tolerances serve functional requirements
- Geometry assessment: Identify opportunities for simplification without performance impact
- Material optimization: Confirm material selection balances performance with processing requirements
- Process compatibility: Ensure manufacturing methods align with design requirements and cost targets
- Quality planning: Develop inspection strategies that balance requirements with cost constraints
Change Management Protocols
Establishing clear protocols for design changes prevents scope creep and maintains cost control throughout development. Change management procedures should evaluate both immediate costs and long-term implications.
Design freeze points protect manufacturing preparations while allowing controlled modifications when absolutely necessary. These checkpoints balance flexibility with cost containment throughout the development process.
Communication protocols ensure all stakeholders understand cost implications of proposed changes. This transparency enables informed decision-making and prevents unexpected budget impacts.
Measuring Success and Continuous Improvement
Cost Tracking Methodologies
Effective cost management requires tracking expenses across the entire manufacturing process. Direct costs include materials, tooling, and processing time, while indirect costs encompass setup, inspection, and overhead allocation.
Understanding cost drivers enables targeted improvement efforts that address the most significant expense categories. Regular cost analysis identifies trends and opportunities for ongoing optimization.
Benchmark data from similar projects provides context for evaluating design efficiency and identifying improvement opportunities. This comparative analysis guides future design decisions and process improvements.
Performance Metrics and Analysis
Key performance indicators should track both cost and quality metrics throughout production. Monitoring these metrics enables rapid identification of issues and implementation of corrective actions.
Cost per part trends reveal the effectiveness of design optimization efforts and identify opportunities for further improvement. Quality metrics ensure cost reduction efforts don't compromise product performance.
Regular metric reviews enable continuous improvement and help maintain optimal balance between cost and quality throughout the product lifecycle.
Long-Term Optimization Strategies
Sustainable cost reduction requires ongoing attention to design efficiency and manufacturing optimization. Regular reviews of production data identify opportunities for continuous improvement and cost reduction.
Material and process innovations create new opportunities for cost optimization that weren't previously available. Staying current with manufacturing capabilities enables designers to leverage new technologies and methods.
Supplier partnerships provide access to specialized expertise and innovative solutions that internal teams might not develop independently. These relationships often prove valuable for complex applications or specialized materials.
Frequently Asked Questions About Design for Manufacturing Cost Reduction
When should DFM cost reduction strategies be implemented?
DFM should begin during the earliest design phases, ideally before tooling decisions are made. The design phase has the greatest effect on cost, making early implementation critical for maximum savings.
What are the most common cost drivers in manufacturing?
The primary cost drivers include overly tight tolerances, complex geometries requiring specialized tooling, excessive part counts, premium materials, and non-standard components that require custom manufacturing processes.
How much can effective DFM reduce manufacturing costs?
While results vary by application, effective DFM implementation typically reduces manufacturing costs by 15-30% without compromising functionality. Some companies report even higher savings through comprehensive optimization programs.
What role does tolerance optimization play in cost reduction?
Tolerance optimization is critical because costs increase exponentially as tolerances tighten beyond standard manufacturing capabilities. Specifying appropriate tolerances based on functional requirements can reduce costs by 20-50% in precision applications.
Your Partner in Cost-Effective Manufacturing
Modus Advanced brings engineering expertise and manufacturing capability together to optimize designs for cost efficiency. Our team of engineers — representing more than 10% of our staff — collaborates with customers throughout the design process to identify cost-saving opportunities.
Our AS9100 and ISO 9001 certifications ensure consistent quality while our vertically integrated processes minimize costs and lead times. With capabilities spanning CNC machining, form-in-place gasket dispensing, waterjet cutting, and precision assembly, we provide comprehensive solutions under one roof.
When your design requires both performance and cost efficiency, partner with a manufacturer who understands engineering requirements and manufacturing economics. Contact our team to discuss how smart design decisions can reduce your total cost of ownership while maintaining the quality your applications demand.