Designing for Manufacturing: When Casting Meets Machining in Production Strategy
July 7, 2025
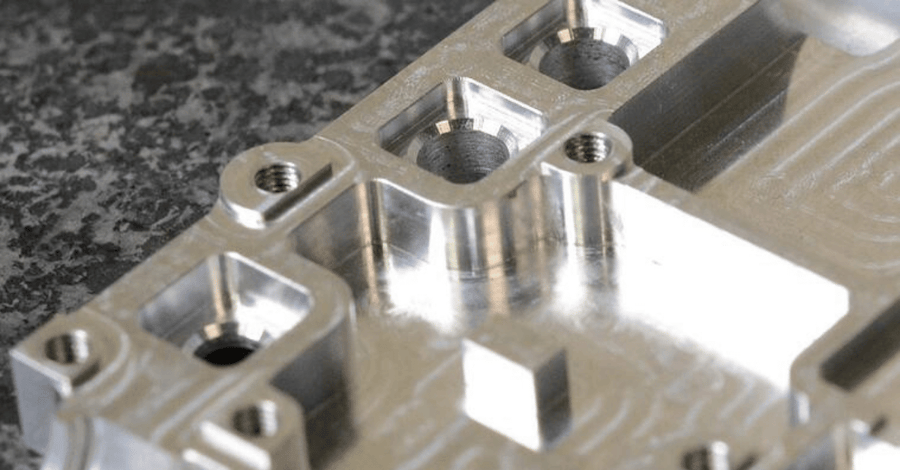
Manufactured with Speed and Precision
The manufacturing capabilities you need and the engineering support you want, all from a single partner.
Submit a DesignKey Points
Engineers developing new products face a critical decision that impacts both prototype development and long-term production success. Understanding the design differences between cast and machined parts can dramatically reduce lead times and manufacturing costs.
- Production method selection: Casting offers significant cost advantages for high-volume production, while machining provides faster prototyping capabilities
- Design feature compatibility: Cast parts require draft angles and generous radii, while machined parts can accommodate tighter tolerances and sharper features
- Timeline considerations: Machining delivers prototypes in weeks, while casting tooling requires 20-25 weeks but enables cost-effective mass production
- Cost implications: Individual machined parts can cost more than cast equivalents, but casting requires substantial upfront tooling investment
- Design optimization strategy: Creating separate designs for prototyping and production phases maximizes manufacturing efficiency and minimizes overall project costs
The Manufacturing Method Dilemma: Beyond Simple Economics
Product development teams often face pressure to choose a single manufacturing approach for both prototyping and production phases. This decision creates an unnecessary constraint that can significantly impact project timelines and costs.
The fundamental challenge lies in the conflicting requirements of these two manufacturing methods. Features that make sense, or are even required, for casting — such as draft angles and generous radii — create unnecessary complexity and extended lead times when machined. Conversely, the tight tolerances and sharp corners achievable through machining may be impossible or economically unfeasible in casting operations.
Understanding these trade-offs enables engineers to make informed decisions about when to optimize designs for each manufacturing method. The most successful product development strategies often involve creating distinct design variants tailored to their intended manufacturing process.
Read the full Design for Manufacturability guide.
Machining: The Prototyping Champion
Speed and Flexibility Advantages
Machining excels in prototype development due to its rapid setup capabilities and design flexibility. CNC machining can transform CAD files into physical parts within days, enabling quick design iterations and faster time-to-market for testing phases.
The absence of tooling requirements means design changes can be implemented immediately. This flexibility proves invaluable during the iterative design process where multiple revisions are common.
Design Considerations for Machined Parts
Machined parts benefit from specific design approaches that minimize manufacturing time and complexity. Sharp corners in internal cavities present the most significant challenge, as cutting tools cannot create true 90-degree internal corners.
Optimal machining design features include:
- Generous radii: Larger corner radii allow the use of bigger cutting tools, reducing machining time and improving surface finish
- Standard tool compatibility: Designs that work with commonly available tools eliminate special tooling lead times and costs
- Minimal feature complexity: Simple geometric features aligned with X, Y, and Z axes reduce the need for five-axis machining
- Accessible geometry: Features that can be reached with standard-length tools avoid the complications of extended-reach tooling
The most problematic design elements for machining include varying radii throughout the part, which require multiple tool changes and extended programming time. Features requiring specialized tools — such as specific thread cutting tools with multi-week lead times — can significantly impact project schedules.
Visit our CNC Machining Resource Center
Tolerance Capabilities and Limitations
Modern CNC machining can achieve remarkably tight tolerances, with some operations targeting profile tolerances as tight as 0.0004 inches (0.01 mm). However, achieving such precision requires careful attention to environmental factors including machine temperature, shop temperature, and thermal expansion considerations.
More practical tolerance ranges for typical machined parts fall within standard manufacturing capabilities. The relationship between part size and achievable tolerance becomes critical — large parts with extremely tight tolerances present exponentially greater challenges than smaller parts with equivalent precision requirements.
Casting: The Production Powerhouse
Economic Advantages at Scale
Casting transforms the economics of high-volume production by dramatically reducing per-unit costs. A part that costs $700 to machine individually might cost only $32 when cast, representing more than a 20-fold cost reduction.
This economic advantage comes with significant upfront investment and bulk production requirements. Casting tooling typically requires 20-25 weeks for development and is meant for making thousands of repeatable parts, representing a substantial initial timeline commitment that must be factored into overall project planning.
Design Requirements for Cast Parts
Cast part design follows fundamentally different principles than machined components. The casting process requires features that facilitate easy removal from molds and ensure consistent material flow during the casting process.
Essential casting design elements include:
- Draft angles: Every vertical surface requires 1-2 degree angles to enable mold release
- Generous radii: Internal and external corners need substantial radii to ensure proper material flow and mold durability
- Uniform wall thickness: Consistent material thickness prevents cooling irregularities and reduces defect potential
- Minimal undercuts: Complex geometries that would require side-action tooling significantly increase mold complexity and cost
The most challenging aspect of cast part design often involves balancing functional requirements with manufacturing constraints. Features that seem minor in CAD models — such as slight undercuts or varying wall thicknesses — can dramatically complicate mold design and increase production costs.
Material Considerations and Limitations
Casting materials behave differently than machined stock materials, particularly regarding internal stresses and grain structure. These differences can affect final part performance, particularly in applications requiring high strength or fatigue resistance.
Post-casting machining operations are often necessary to achieve final dimensional requirements or surface finish specifications. This hybrid approach requires careful consideration during the design phase to ensure adequate material allowances in critical areas.
Design Feature Comparison: Machining vs. Casting Requirements
Design Feature | Machining Optimal | Casting Optimal | Impact on Manufacturing |
Corner Radii | 0.5-2.0mm (0.02-0.08") | 3.0-6.0mm (0.12-0.24") | Smaller radii require specialized tools for machining |
Draft Angles | 0° (not required) | 1-2° minimum | Draft angles add unnecessary complexity to machined parts |
Wall Thickness | Variable acceptable | Uniform preferred | Uniform thickness prevents casting defects |
Feature Accessibility | Limited by tool reach | Flexible geometry | Deep pockets challenge both methods differently |
Undercuts | Achievable with planning | Avoided when possible | Undercuts require specialized tooling for both methods |
Production Strategy: Optimizing for Both Phases
The Two-Design Approach
The most effective manufacturing strategy often involves creating separate designs optimized for prototyping and production phases. This approach maximizes the advantages of each manufacturing method while minimizing their respective limitations.
Prototype designs should prioritize machinability features such as sharp corners, minimal draft angles, and tight tolerances where functionally necessary. These designs enable rapid iteration and testing without the geometric constraints imposed by casting requirements.
Production designs incorporate casting-friendly features including appropriate draft angles, generous radii, and optimized wall thicknesses. While these features may require additional validation testing, they enable the significant cost savings necessary for commercial viability.
Read our Complete CNC Machining Guide
Timeline Management Strategies
Successful product development requires careful coordination between prototype testing and production tooling development. The 20-25 week casting tooling timeline should begin in parallel with final prototype validation, not after prototype approval.
This parallel development approach requires confidence in the basic design concept while allowing for minor modifications based on prototype testing results. Changes that affect the overall part envelope or major features may require tooling modifications, but surface details and minor dimensional adjustments can often be accommodated.
Cost Analysis Framework
Here’s an example cost analysis for the same part with multiple volumes and processes considered. Keep in mind that the starting point for the part cost will be determined by the size and complexity of the part.
Volume Range | Machining Cost/Part | Casting Cost/Part | Break-Even Analysis |
1-10 parts | $200-$1000 | N/A (tooling cost prohibitive) | Machining only viable option |
10-100 parts | $200-$1000 | $150-$300 (including amortized tooling) | Depends on tooling complexity |
100-1000 parts | $200-$1000 | $50-$150 | Casting becomes cost-effective |
1000+ parts | $200-$1000 | $10-$50 | Casting provides significant savings |
Tooling Investment | $500-$5,000 (fixtures/programs) | $25,000-$150,000 (molds) | Volume determines ROI timeline |
Cost-Benefit Analysis Framework
The decision between casting and machining involves multiple cost factors beyond simple per-unit pricing. Tooling costs, volume requirements, timeline constraints, and design complexity all influence the optimal manufacturing strategy.
Key decision factors include:
- Production volume: Higher volumes favor casting due to amortized tooling costs
- Timeline urgency: Tight development schedules may favor machining despite higher unit costs
- Design complexity: Complex geometries may be more easily achieved through machining
- Material requirements: Specific material properties may dictate manufacturing method selection
Quality and Tolerance Considerations
Achievable Precision Comparison
Machining generally offers superior dimensional precision and surface finish capabilities compared to casting. However, modern casting techniques can achieve surprisingly tight tolerances when properly designed and controlled.
The key difference lies in the capability to hold tolerances across different feature types. Machining excels at maintaining precise dimensional relationships between disparate features, while casting performs best when tolerances are localized to specific areas of the part.
Inspection and Quality Control Implications
Different manufacturing methods require different quality control approaches. Machined parts can be measured using conventional coordinate measuring machines (CMMs) and standard inspection techniques.
Cast parts often require specialized inspection approaches due to their complex geometries and the potential for casting defects. The inspection strategy should be considered during the design phase to ensure all critical features can be properly verified.
Advanced Considerations for Complex Projects
Hybrid Manufacturing Approaches
Some projects benefit from hybrid approaches that combine casting and machining operations. Cast parts can provide the basic geometry at low cost, while machining operations achieve final dimensions and surface finishes where required.
This approach requires careful design consideration to ensure adequate material allowances in areas requiring machining. The additional operations add complexity but can optimize both cost and performance characteristics.
Material Selection Impact
The choice between casting and machining often influences material selection options. Cast materials may have different mechanical properties than wrought materials, affecting part performance and design requirements.
Engineers should consider these material differences early in the design process, as they may influence feature sizing, safety factors, and overall part architecture.
Visit our full Design for Manufacturability resource center.
Making the Right Choice for Your Project
Decision Matrix Development
Successful manufacturing method selection requires systematic evaluation of project requirements against manufacturing capabilities. Weight, cost, timeline, and performance requirements should all factor into the decision process.
Create a decision matrix that quantifies the relative importance of different project factors. This structured approach helps ensure that all stakeholders understand the trade-offs involved in manufacturing method selection.
Working with Manufacturing Partners
Early engagement with manufacturing partners provides valuable insight into design optimization opportunities. Experienced manufacturers can identify potential issues and suggest design modifications that improve manufacturability without compromising functionality.
At Modus Advanced, our engineering team works with customers during the design phase to optimize parts for their intended manufacturing method. This collaborative approach helps identify potential issues before they impact project timelines or costs.
Our AS9100 and ISO 9001 certifications ensure that quality considerations are integrated throughout the design and manufacturing process. Whether developing prototypes through machining or transitioning to cast production parts, our comprehensive manufacturing capabilities support projects from concept through production.
Overall Manufacturing Method Comparison
Factor | Machining | Casting |
Setup Time | A few weeks | 20-25 weeks (tooling) |
Unit Cost Range | $200-$1000+ | $10-$100 |
Typical Tolerances | ±0.005" (±0.13mm) | ±0.015" (±0.38mm) |
Minimum Volume | 1 piece | 100-1000 pieces |
Design Changes | Immediate | Requires tooling modification |
Material Waste | Moderate to high | Minimal |
Partner with Manufacturing Experts Who Understand Design Optimization
When your innovation demands both rapid prototyping and cost-effective production, choose a manufacturing partner who understands the intricacies of both processes. Modus Advanced's engineering team provides design optimization guidance that accelerates your path from concept to market while ensuring manufacturing efficiency at every stage.