Design for Manufacturability: CNC Machined Metal Parts - Complete Engineering Guide
July 2, 2025
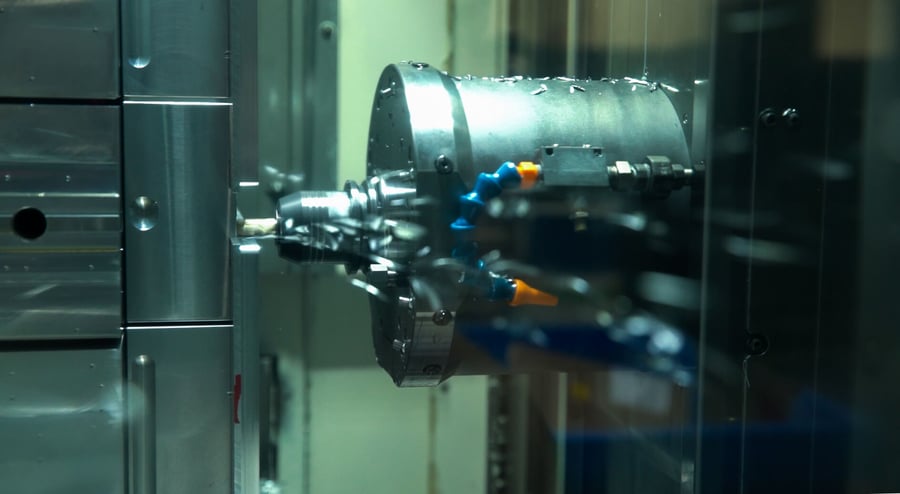
Manufactured with Speed and Precision
The manufacturing capabilities you need and the engineering support you want, all from a single partner.
Submit a DesignKey Points
- Design for manufacturability (DFM) decisions made during concept phase can increase manufacturing lead times by 25% to 1,480% and costs by 15% to 800%, with compound effects when multiple challenging features exist on one part
- Sharp internal corners are impossible to machine without radius features — specify 0.030" (0.76mm) minimum radius to enable standard tooling and reduce programming complexity
- Complex curves and varying radii can triple programming time and quadruple machining costs compared to simple, consistent geometry aligned with standard tooling capabilities
- Parts designed for casting but prototyped through machining require separate design versions to eliminate draft angles and filleted features that complicate CNC operations
- Five-axis machining operations can cost 300-600% more than three-axis alternatives — align all features with X, Y, and Z planes whenever functionally possible
- Tolerance specifications below ±0.002" (±0.05mm) require specialized equipment, temperature control, and stress relief operations that can triple manufacturing timelines
- 100% inspection requirements can increase quality control time by 700-1,480% compared to standard AQL sampling, often adding weeks to delivery schedules
- Profile tolerances on complex geometries require comprehensive surface scanning that takes 200-800% longer than simple dimensional measurements focused on critical features
Engineers face mounting pressure to bring innovative products to market faster while maintaining the precision and reliability that critical applications demand. Design for manufacturability (DFM) principles offer a direct path to achieving both goals simultaneously.
The choices made during the design phase ripple through every subsequent manufacturing step. A seemingly minor design decision — like specifying an unnecessary fillet or choosing an overly tight tolerance — can transform a straightforward CNC machining operation into a complex, time-intensive process that delays product launch by weeks.
This comprehensive guide examines the most common design challenges encountered in CNC machined parts and provides actionable strategies to optimize your designs for faster, more cost-effective manufacturing without compromising functionality.
Definition
What is Design for Manufacturability in CNC Machining?
Design for manufacturability (DFM) is a systematic approach to product design that optimizes parts for efficient, cost-effective manufacturing processes. In CNC machining, DFM principles focus on creating designs that minimize machining complexity, reduce programming time, and eliminate the need for specialized tooling or multiple setups.
Key DFM principles for CNC machining include:
- Designing features that align with standard tooling capabilities
- Minimizing the number of machining operations required
- Specifying appropriate tolerances that balance function with manufacturability
- Optimizing part geometry to reduce material waste and machining time
- Creating designs that can be manufactured using common three-axis operations when possible
Effective DFM implementation can reduce manufacturing costs by 15-40% and cut lead times by 25-60% compared to non-optimized designs, making it essential for competitive product development in aerospace, defense, and medical device industries. Understanding key design considerations for custom components helps engineers optimize their approach from the initial concept phase.
Read the full Design for Manufacturability guide.
Why Design for Manufacturability Matters
Both lead time and cost considerations drive manufacturing decisions, though their relative importance varies by industry and project phase. In mission-critical industries, compressed development timelines often make speed the primary concern, while cost optimization becomes crucial for production scaling.
- Lead Time Reduction: Faster prototyping enables quicker design validation and market entry
- Cost Control: Efficient manufacturing reduces per-unit costs and overall project budgets
- Quality Assurance: Manufacturable designs reduce errors and improve reliability
- Risk Mitigation: Simplified manufacturing processes minimize production delays and quality issues
Industry-Specific Impacts
Aerospace and Defense: Weight restrictions and precision requirements create challenging trade-offs between optimal design and manufacturability. While speed often takes precedence during development phases — where getting a prototype into testing weeks earlier can accelerate critical system deployment — cost becomes equally important for production contracts where budget constraints directly impact program viability.
Medical Devices: Patient safety depends on reliable, repeatable manufacturing processes. Development speed ensures life-saving devices reach patients sooner, while cost efficiency makes these technologies accessible to broader patient populations who need them.
The Multiplier Effect: A single design decision — such as specifying an unnecessarily tight tolerance or complex geometry — can cascade through multiple manufacturing steps. What appears as a minor design choice can add days to programming time, require specialized tooling with extended lead times, and significantly increase per-unit costs through extended machining operations and complex inspection procedures.
Design for manufacturability transforms these potential bottlenecks into streamlined processes that accelerate your path from concept to life-changing innovation while keeping projects within budget constraints.
Read the Complete Guide to CNC Machining
Understanding the Impact of Design Decisions
The following table quantifies how specific design choices might affect manufacturing timelines and costs. These impacts often compound when multiple challenging features appear on the same part, making design for manufacturability principles essential for project success.
Use this reference to evaluate design trade-offs during the concept phase, when changes cost hours rather than weeks to implement.
Often the parts being sent our way need some of the design features stated, and this is totally fine! We are here to help support complex machining needs, however we find it is helpful to provide details about why these design features create such impacts to lead times and costs. Our goal is simply to support engineers in making the decisions on if the design features are necessary (and worth the trade-offs) or not.
Design Factor | Lead Time Impact | Cost Impact | Recommended Solution | Key Considerations |
Sharp Internal Corners | +50-100% programming time | +25-50% per feature | Add 0.030" (0.76mm) minimum radius | Requires specialized small tooling, multiple setups |
Knife Edges | +20-30% | +15-25% | Add 0.005-0.015" (0.13-0.38mm) outside fillet | Secondary deburring operations, handling damage risk |
Complex Curves/Varying Radii | +100-300% programming | +200-400% machining time | Use consistent radii, eliminate decorative curves | Multiple tool changes, specialized programming |
Five-Axis vs. Three-Axis Features | +200-500% | +300-600% | Align features with X, Y, Z axes | Equipment availability, setup complexity |
Cast-Optimized Prototypes | +150-250% | +100-200% | Create separate machining-optimized design | Draft angles require specialized tooling |
Extremely Tight Tolerances | +25% to +300%+ | +50% to +500%+ | Open tolerances to ±0.002" (±0.05mm) or larger | Temperature control, stress relief, specialized equipment |
Profile vs. Dimensional Tolerances | +200-800% inspection | +100-400% inspection | Use dimensional tolerances for non-critical geometry | Surface scanning vs. point measurement |
100% vs. AQL Inspection | +700% to +1,480% | +300-800% | Specify AQL sampling unless safety-critical | Statistical sampling vs. complete measurement |
Poor Datum Structure | +50-150% | +25-100% | Reference features from nearby, accessible datums | Measurement setup complexity, thermal effects |
Inaccessible Features | +100-200% | +50-150% | Design features accessible to standard probes | Specialized probes, multiple setups |
Surface Finish Requirements | +25-100% | +20-75% | Use standard machined finish (63-125 Ra) | Additional operations, specialized tooling |
Threading Specification Method | +10-50% | +15-30% | Specify thread class, avoid dictating drill sizes | Tool flexibility vs. rigid requirements |
Note: Impact percentages represent typical increases compared to manufacturing-optimized designs. Actual results vary based on part complexity, production volume, and specific geometric requirements. Multiple challenging features on a single part often create multiplicative effects that can dramatically exceed these individual impact ranges.
Common DFM Challenges in CNC Machining
The Over-Engineering Challenge
Complex geometries often stem from aesthetic preferences, or lack of understanding around how those geometries affect timelines and costs for manufacturing, rather than functional requirements. Engineers frequently incorporate elaborate curves, varying radii, and ornate features that look impressive in CAD models but create significant manufacturing bottlenecks.
Manufacturing Impact of Complex Curves:
- Increased programming time for CNC operations
- Multiple tool changes requiring different cutting geometries
- Extended setup and inspection procedures
- Higher probability of manufacturing errors
Consider the difference between a housing with consistent, simple geometry versus one featuring multiple varying radii and complex curves. The simpler design can often be programmed and machined in hours, while the complex version may require days of programming and multiple machining setups. This design for manufacturability principle becomes critical when prototype timelines are measured in days, not weeks.
The solution involves questioning every geometric feature during the design phase: does this curve or complex shape serve a specific functional purpose, or is it purely aesthetic?
Visit the CNC Machining Resource Center
Critical Geometry Guidelines for CNC Machining
Knife Edges
Knife edges occur where two surfaces meet at an extremely acute angle, creating a sharp, fragile feature that's problematic for both manufacturing and part durability. These features create significant challenges during machining operations.
Manufacturing Issues with Knife Edges:
- Impossible to achieve true sharp edges with standard tooling
- Creates burrs that require secondary deburring operations
- Fragile features prone to chipping during handling
- Inconsistent edge quality affecting part aesthetics
Design Solution
Add small outside fillets (0.005-0.015"/0.13-0.38mm radius) to eliminate knife edges. This design for manufacturability modification provides a controlled, consistent edge that machines cleanly and remains durable throughout handling and assembly operations.
Manufacturing teams typically add these fillets during production regardless of drawing specifications, making it more efficient to include them in the original design.
Sharp Corners
Sharp internal corners represent one of the most common and problematic design issues in machined parts. End mills cannot create true 90-degree internal corners due to their cylindrical geometry.
Corner Radius Requirements:
Feature Type | Minimum Radius | Recommended Radius | Manufacturing Benefit |
Internal corners | 0.005" (0.13mm) | 0.030" (0.76mm) | Standard tooling compatibility |
Deep pockets | 0.010" (0.25mm) | 0.060" (1.52mm) | Reduced tool deflection |
Thin wall features | 0.020" (0.51mm) | 0.080" (2.03mm) | Improved rigidity during cutting |
Design Optimization Strategy
Specify the largest radius your design can accommodate for any given feature. Larger radii enable the use of larger, more rigid cutting tools that resist deflection and provide superior surface finishes. They also reduce programming complexity and eliminate the need for specialized small-diameter tooling with extended lead times.
The design for manufacturability principle here directly impacts both quality and delivery: larger radii mean faster programming, more reliable machining, and shorter lead times.
Curved or Rounded Surfaces
Complex curves and varying radii significantly increase manufacturing complexity, often without providing functional benefits. These features require specialized programming, multiple tool changes, and extended machining times.
Manufacturing Impact of Complex Curves:
- Increased programming time for CNC operations
- Increased costs due to the need for multiple unique tools to cut different geometries
- Extended setup and inspection procedures
- Higher probability of manufacturing errors
Curve Optimization Guidelines:
- Use consistent radii wherever possible to minimize tool changes
- Eliminate ornamental curves that don't serve functional purposes
- Consider breaking complex curves into simpler geometric segments
- Align curved features with standard tooling capabilities
Functional vs. Aesthetic Evaluation: Question every curved feature during design: does this geometry serve a specific functional purpose, or is it purely aesthetic? Weight reduction curves may justify complexity in aerospace applications, but decorative features rarely warrant the manufacturing overhead they create.
Simple, consistent geometry machines faster and more reliably than complex curved surfaces, making this a critical design for manufacturability consideration for rapid prototyping and production efficiency.
Five-Axis vs. Three-Axis Considerations
Feature orientation significantly impacts manufacturing complexity and cost. Parts requiring five-axis machining operations cost substantially more and take longer to produce than those manageable on standard three-axis equipment.
Features Requiring Five-Axis Machining:
- Angled holes or slots not aligned with primary axes
- Complex compound angles on multiple surfaces
- Undercut features accessible only from non-standard orientations
- Deep cavities with feature access from multiple angles
Design Optimization Strategies:
- Align all features with X, Y, or Z axes when possible
- Minimize the number of faces requiring machined features
- Group angled features to reduce setup changes
- Consider redesigning undercuts as through-features
Manufacturing efficiency improves dramatically when parts can be completed in three-axis operations with minimal setups. For applications requiring complex geometry, alternative cutting methods like waterjet may provide more efficient solutions for certain feature types.
Drill Tapping, Threading and Hardware Specifications
Software default specifications for threaded holes often create unnecessary manufacturing constraints. CAD programs typically default to cut tap specifications, while manufacturers may prefer roll tapping for improved thread quality and tool life.
Recommended Threading Callouts:
- Specify thread class and position requirements
- Avoid dictating specific drill sizes or tap types
- Focus on functional requirements (thread engagement, strength)
- Allow manufacturers flexibility in process selection
This approach enables manufacturers to optimize their processes while ensuring your functional requirements are met.
Pay Attention to Pre-Drill Tapping Depth:
The drilling depths in your design for CNC machining must be deeper than the tapping depths. When you're designing, keep in mind that every tap on the market has a certain amount of thread lead-in:
- Bottoming tap: 1 to 1.5 thread lead-in
- Plug tap: 3 to 5 thread lead-in
- Taper tap: 8 to 10 thread lead-in
Design Optimization Strategies
You can avoid production hangups by ensuring that you’ve allowed for enough tapping depth and the drill depth necessary to produce full threads to the required thread depth.
If you are having trouble accommodating the necessary depth, consider making it a through-hole that allows us to drill straight through. This saves on time and cost.
Give Tapped Holes Some Wall Clearance:
Check the location of the tapped holes in your design. Are any close to the inside of a pocket? This creates a high likelihood that the tapped hole will break through the inside wall when the part is machine made. Breakout will cost time and money to fix.
Design Optimization Strategy
You can avoid breakout by creating more wall clearance between the tapped hole and the inside wall. Move the hole further from the side wall or use a smaller thread to create a tapped hole with a smaller diameter to machine.
Casting vs. Machining Design Considerations
Many parts are initially designed for casting but require machined prototypes for early testing and validation. This creates a fundamental design for manufacturability conflict that significantly impacts manufacturing efficiency.
Cast Part Features That Complicate Machining:
- Draft angles (typically 1-3 degrees) on all vertical surfaces
- Large radii and filleted transitions between surfaces
- Wall thickness variations optimized for casting flow
- Complex internal geometries designed for mold extraction
Draft angles present particular challenges in machining operations. The one-degree tapers common in cast designs require specialized tooling or complex programming to achieve acceptable surface finishes. Standard end mills struggle to maintain consistent surface quality on angled surfaces, often necessitating custom tooling with corresponding lead times and costs.
Recommended Approach
Create separate design versions for prototype machining and production casting. The machined version should eliminate draft angles, use consistent wall thicknesses, and feature geometric simplifications that align with standard machining capabilities. This design for manufacturability strategy enables rapid prototyping while maintaining the cast design's production advantages.
When transitioning from prototypes to production, engineers should also consider whether alternative manufacturing processes might offer advantages for specific component requirements or production volumes.
CNC Machining Tolerance and Inspection Considerations
Geometric Dimensioning and Tolerancing (GD&T) Best Practices
GD&T: A symbolic language used on engineering drawings to communicate design intent regarding the geometry of parts, including form, orientation, location, and runout characteristics.
GD&T BasicsPoor datum structure represents one of the most costly tolerance-related design errors. Datum selection determines how parts are fixtured and measured during manufacturing, directly impacting achievable accuracy and inspection complexity.
Datum Structure Guidelines:
- Reference critical features from nearby datums rather than distant reference points
- Minimize temperature and thermal expansion effects by keeping datum distances short
- Ensure datum features are easily accessible for measurement equipment
- Consider manufacturing setup requirements when selecting datum references
CNC Machining Tolerance Specification Impact:
Tolerance Range | Manufacturing Impact | Lead Time Effect |
±0.005" (±0.13mm) | Standard operations | Baseline |
±0.002" (±0.05mm) | Increased precision requirements | +25-50% |
±0.0005" (±0.013mm) | Specialized equipment/environment | +100-200% |
±0.0002" (±0.005mm) | Temperature control, stress relief | +300%+ |
Extremely tight tolerances (under 0.001"/0.025mm) introduce manufacturing variables typically ignored in standard operations. Temperature control, machine warm-up procedures, and stress relief operations become critical factors, significantly extending manufacturing timelines.
Quality Control Planning
Inspection requirements significantly impact manufacturing lead times and costs. The difference between standard statistical sampling (AQL - Acceptable Quality Level) and 100% inspection can add weeks to delivery schedules.
Inspection Time Impact:
- Standard AQL sampling: Minimal lead time impact
- 100% inspection: Can equal or exceed manufacturing time and incur significant costs
- Complex profile tolerances: Require extensive measurement programming
AQL vs. 100% Inspection Guidelines:
Order Quantity | Standard AQL Sample Size | 100% Inspection Impact |
100 parts | 13 parts measured | 100 parts measured (+700% inspection time) |
1,000 parts | 80 parts measured | 1,000 parts measured (+1,150% inspection time) |
5,000 parts | 315 parts measured | 5,000 parts measured (+1,480% inspection time) |
Design for manufacturability extends beyond geometry to include realistic quality control expectations. Unless safety-critical applications mandate 100% inspection, standard statistical sampling provides equivalent quality assurance with dramatically reduced lead times and costs.
Inspection Equipment Limitations
Manufacturing capability represents only half the tolerance equation — measurement capability determines whether specified tolerances can be verified. Quality control equipment has distinct limitations that may prevent accurate measurement of extremely tight tolerances.
Measurement Considerations for Machined Parts:
- Coordinate measuring machines (CMMs) have specific accuracy ranges for dimensional measurement
- Complex 3D geometries require specialized measurement programming and extended setup times
- Profile tolerances on curved surfaces demand comprehensive measurement routines
- Deep cavities or internal features may require specialized probe configurations
Measurement vs. Manufacturing Capability: For machined parts, measurement equipment must achieve significantly higher accuracy than the manufacturing tolerance to provide reliable verification. A general rule requires measurement equipment accuracy of 10:1 compared to the specified tolerance.
- Ensure critical features are accessible to standard measurement probes
- Avoid specifying profile tolerances on complex curves unless functionally necessary
- Design reference surfaces that provide stable measurement datum points
- Consider measurement accessibility when designing internal cavities or deep pockets
Best Fit Limitations for Machined Parts: Unlike flexible materials, machined parts require true geometric measurement rather than "best fit" approaches. Critical dimensions, especially those affecting mating parts or assembly interfaces, must be measured accurately without statistical manipulation.
Design for manufacturability principles suggest specifying tolerances that align with both manufacturing and measurement capabilities to avoid unnecessary complications and ensure reliable quality control.
Drawing Specification Impact on Inspection
How engineers specify tolerances and measurements on drawings directly affects inspection complexity and lead times. Small changes in drawing callouts can dramatically reduce quality control requirements without impacting part function.
Measurement Specification Guidelines:
Profile vs. Dimensional Tolerances: Profile tolerances require measuring entire geometric surfaces, while dimensional tolerances focus on specific features. A complex curved part with a profile callout demands comprehensive surface scanning, but the same part with simple dimensional tolerances (overall length, width, height) can be inspected in minutes rather than hours.
Functional vs. Complete Measurement: Consider what actually needs verification for proper function. A gasket pocket may only require overall dimensions to ensure proper fit, not complete geometric profiling of decorative curves or non-functional features.
Measurement Accessibility Callouts:
- Specify tolerances only on features that affect fit, form, or function
- Avoid profile tolerances on complex geometries unless geometrically critical
- Use basic dimensional tolerances for features where overall size matters more than exact shape
- Group related features to minimize measurement setups
Drawing Clarity for Inspection:
- Clearly indicate which features are critical vs. reference only
- Specify measurement methods when non-standard approaches are acceptable
- Distinguish between features requiring precision measurement and those suitable for go/no-go gauging
Design for Manufacturability Principle: Ask whether each tolerance callout serves a functional purpose or simply reflects design intent. Eliminating unnecessary measurement requirements can reduce inspection time by 50-80% while maintaining all critical part functions.
This approach allows quality control teams to focus measurement efforts on truly critical features rather than documenting every geometric detail.
Material and Surface Finish Interactions
Surface finish specifications significantly impact both manufacturing processes and subsequent operations like form-in-place gasket dispensing. Extremely smooth finishes can actually impair adhesion for certain gasket materials.
Surface Finish Considerations:
- Standard machined finishes (63-125 Ra) provide excellent adhesion for most gasket materials
- Mirror finishes may require surface texture enhancement for reliable gasket adhesion
- Consider downstream assembly requirements when specifying finish
When surface finish creates adhesion challenges, some design solutions include (though these can add cycle time):
- Adding scribe lines along gasket paths for mechanical retention
- Creating shallow channels (0.002-0.005"/0.05-0.13mm deep) for gasket positioning
- Specifying textured finishes in gasket contact areas while maintaining smooth finishes elsewhere
If possible, adding a primer can be a solution which solves the adhesion problem and doesn’t increase cycle time.
These design for manufacturability modifications provide mechanical retention without compromising the part's primary function.
Industry-Specific Design Considerations
Aerospace and Defense Applications
Weight constraints in aerospace applications often conflict with design for manufacturability principles. Every gram matters in flight applications, making seemingly simple modifications like larger radii subject to extensive analysis.
Aerospace Design Challenges:
- Weight optimization versus manufacturability trade-offs
- Extremely tight tolerances for precision assemblies
- Material removal limitations due to weight targets
- Complex inspection requirements increasing lead times
Many aerospace applications also require EMI shielding considerations that can further complicate machined housing designs when integrating electronic systems.
Medical Device Applications
Medical applications typically allow greater design flexibility regarding weight and complex geometry, focusing instead on biocompatibility and reliability. Manufacturing constraints center on documentation and quality control rather than geometric limitations.
Medical Design Considerations:
- Enhanced inspection and sampling requirements
- Material traceability and certification needs
- Biocompatibility requirements affecting material and process selection
- Quality system compliance impacting manufacturing documentation
Medical device manufacturers often specify more conservative tolerances to ensure reliable function, allowing design for manufacturability principles to focus on geometry optimization rather than extreme precision requirements. Understanding material selection for medical applications becomes critical when designing housings that may contact biological systems or require specific sterilization procedures.
Documentation and Communication Best Practices
Clear communication between design and manufacturing teams prevents costly misunderstandings and design iterations. Establishing precedence between CAD models and engineering drawings eliminates ambiguity during manufacturing.
Essential Documentation Elements:
- Clear precedence statement (CAD or drawing takes priority for conflicts)
- Functional requirement explanations for critical features
- Material specifications with acceptable alternatives
- Assembly and mating part information affecting tolerance requirements
Design Review Collaboration: Early manufacturing input during design phases identifies potential issues before they become costly problems. Engaging manufacturing partners during initial design iterations enables optimization for both function and manufacturability.
Modus's DfM Review ProcessFor companies committed to quality manufacturing, understanding the benefits of manufacturing in the USA can provide additional advantages in communication, lead times, and supply chain control during the design optimization process.
Frequently Asked Questions About Design for Manufacturability
What is design for manufacturability in CNC machining?
Design for manufacturability (DFM) in CNC machining is the practice of designing parts that can be efficiently manufactured using CNC equipment. It involves optimizing geometry, tolerances, and features to minimize machining time, reduce tool changes, and eliminate the need for specialized equipment or complex setups.
How much can DFM reduce manufacturing costs?
Effective DFM implementation can reduce manufacturing costs by 15-40% and cut lead times by 25-60% compared to non-optimized designs. The exact savings depend on part complexity and the specific DFM improvements implemented.
What tolerance should I specify for CNC machined parts?
For standard CNC machining, ±0.005" (±0.13mm) is the typical baseline tolerance. Tighter tolerances like ±0.002" (±0.05mm) increase costs by 25-50% and should only be specified when functionally necessary.
Why do sharp internal corners increase machining costs?
Sharp internal corners require specialized small-diameter tooling and additional machining operations because standard end mills cannot create true 90-degree internal corners due to their cylindrical geometry. Adding a 0.030" radius can reduce programming time by 50-100%.
When should I use five-axis instead of three-axis machining?
Use five-axis machining only when part geometry absolutely requires it, as it costs 300-600% more than three-axis operations. Most parts can be designed to use three-axis machining by aligning features with X, Y, and Z planes.
Optimizing Your Manufacturing Success
Design for manufacturability principles transform complex, time-intensive manufacturing challenges into streamlined production processes. The strategies outlined here — from radius optimization to tolerance rationalization — directly impact your ability to bring products to market quickly while maintaining the quality standards critical applications demand.
Every design decision represents an opportunity to either simplify or complicate manufacturing operations. Understanding how these choices affect programming time, tooling requirements, setup complexity, and inspection procedures enables you to make informed trade-offs between design aesthetics and manufacturing efficiency.
Learning from machining experience and implementing proven design features that reduce lead times and costs becomes critical for accelerating product development. When avoiding quality control issues and selecting the right manufacturing partner, these principles ensure faster time-to-market without compromising the reliability that critical applications demand.
For projects requiring integrated solutions, consider exploring SigShield turnkey RF shield manufacturing as an example of how vertically integrated processes can streamline complex multi-step manufacturing operations while maintaining design for manufacturability principles.
When lives depend on your innovation, choosing manufacturing partners who understand these principles and can guide design optimization becomes critical. Partner with experts who recognize that one day matters — because faster, more efficient manufacturing means life-changing technologies reach the people who need them sooner.
Ready to optimize your designs for manufacturability? Contact Modus Advanced today for expert DFM analysis and precision CNC machining services that help you bring life-changing innovations to market faster.