Solving the Problem of an Aggressive Timeline: Quick-turn RF Shielding Components with FIP Gaskets
November 14, 2017
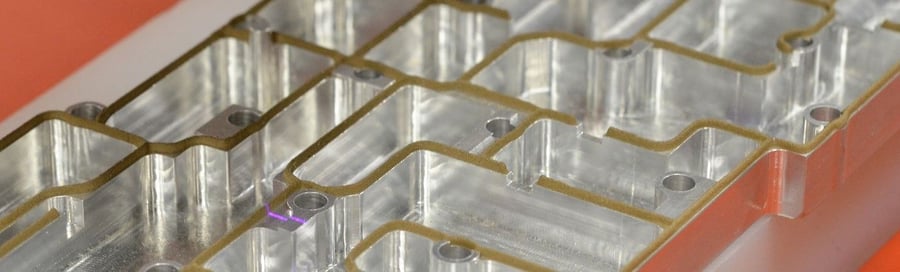
Manufactured with Speed and Precision
The manufacturing capabilities you need and the engineering support you want, all from a single partner.
Submit a DesignKey Points
- Vertical integration is crucial for producing quick-turn RF shielding parts, combining multiple manufacturing processes under one roof to save time and money.
- The benefits of working with a vertically integrated RF shield manufacturer include reduced transaction costs, shorter lead times, consistent quality control, easier revision management, and improved communication.
- For rapid RF shield production, key considerations include CNC programming capabilities, appropriate materials selection, proper tolerance specifications, equipment choices, plating processes, and in-house form-in-place gasketing.
- Aluminum 6061 is often ideal for RF shields due to its cost-effectiveness, lightweight properties, and machinability, while threaded stainless steel inserts can solve the threading challenges of aluminum components.
- Working with a single manufacturing partner that offers comprehensive services from design to production ("Idea to Ignition™") is the optimal solution for meeting aggressive timelines for RF shielding components.
When you have a need for speed, quick-turn parts can be your salvation!
The production of quick-turn parts necessitates both quality methodology and a single supply chain comprised of multiple manufacturing steps. Engineers can achieve both quality and quick-turn through vertical integration.
This approach combines the production of base RF shielding components and supporting processes all under one roof, saving time and money by shortening your supply chain to one manufacturer!
The benefits of contracting with a vertically integrated custom RF shield manufacturer include:
- Transaction cost savings through vendor reduction
- Reduction in lead time and shipping costs realized with a shorter supply chain
- Quality Assurance is controlled and guaranteed by a single vendor during each step of the RF shield manufacturing process
- Easier to process revision changes if necessary
- Close communication between the engineering and manufacturing teams increases project success rates
Read Everything You Need To Know About RF Shielding
However, vertical integration alone does not enable companies to produce quality quick-turn RF shielding parts. Not all methodologies are equal, and some added processes provide more benefit than others, especially in terms of quality and speed. This is particularly true in the manufacturing of RF or EMI shields with EMI shielding gaskets.
When considering a manufacturer for RF shields, what methodologies and processes should engineers expect or consider for a rapid turnaround?
Key considerations for quick-turn RF shields include:
- CNC programming
- Materials for housing
- Shield and gasket tolerances
- Equipment choice and spindle orientation
- Plating of the shield
- In-house form-in-place gasketing
Programming
The use of intelligent software that integrates both CAD and CAM streamlines development of part fixturing and machine set-up. Using robust software considers the geometry of the solid model, and supports most file types which are easily converted from the engineer’s layout to the manufacturer’s automated machines. An additional benefit to using intelligent software is the ability to make quick modifications to tolerances and design elements if needed.
Materials
Engineering teams must consider the ideal production material for each part. For example, in the development of RF shielding components, Aluminum 6061 is most useful because it is cost-effective, lightweight, and strong. RF shields do not typically need to withstand the higher impacts that make the more costly 7075 aluminum useful. As 7075 aluminum is one of the strongest alloys available, the sheer strength of the material can be an obstacle to milling. Because 6061 aluminum provides the same great versatility and is easier and faster to machine, it becomes a solid choice for quick-turn parts.
Here is a comparison of the two alloys.
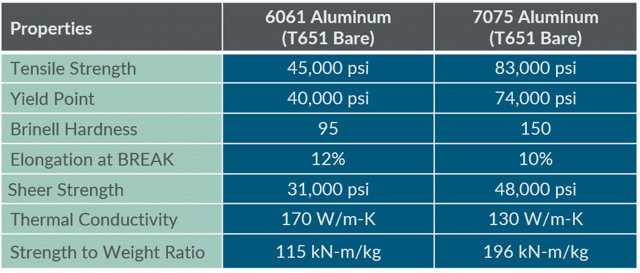
Threading Materials
Because aluminum offers excellent shielding effectiveness, it makes a great shielding material, is both lightweight and inexpensive compared to other electromagnetic shielding materials, and is also softer. This can be a disadvantage when attaching it to other components as the parts can easily be stripped of their threads.
Threaded stainless steel inserts solve this problem by allowing engineers to maintain torque strength while still making light, economic parts. With vertical integration, part milling and installation of threaded inserts become a one-step process performed in-house with Quality Control validation built-in.
Tolerances
The error tolerance on a given part depends on the end use of the part or enclosure. Manufacturers can often achieve a wide range of tolerances, depending on customer specifications and requirements. A wide range of tolerances can be found in the milling of aluminum, with tighter tolerances requiring more skill and time to manufacture. Standard tolerances for RF shields are typically at .005 inches.
Though tighter tolerances can be achieved when necessary, engineers typically seek only the highest tolerance appropriate for the specified application. This is especially important when designing quick-turn parts or those destined for larger-scale production.
Machining Equipment
Quick-turn milled parts are best accomplished with extremely fast, high speed, reliable CNC machining equipment, such as the Fanuc Robodrill. A 24,000 rpm spindle speed is ideal for quickly milling aluminum when building a shielded enclosure. Vertically integrated manufacturers typically employ multiple CNC machines allowing for simultaneous milling by one operator.
Shrinking lead times and costs is obviously the goal, however the in-house benefit is that as groups of parts are milled, they are inspected for quality and moved on to the next in-house process. The "need for speed" is accomplished efficiently and quickly as each milled group of parts is released to the next processing step. There is no need to wait for a completed order and shipment to the next vendor in the supply chain.
Visit the Modus RF Shielding Resource Center
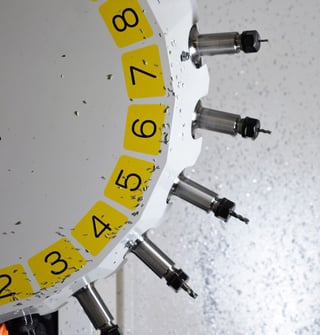
Spindle Orientation
Standard CNC Milling machines utilize either vertically or horizontally oriented spindles. Vertical spindle orientation is ideal for quick-turn parts because it allows for faster programming and fixturing set-up.
Horizontal spindles are ideal for heavier and longer pieces or larger quantities of production, however their fixturing takes significantly longer to develop. This might make them impractical for short-run quick-turn parts.
Plating
Even vertically-integrated manufacturers may rely on outside platers. It is therefore important, when plating is required, that quick-turn parts manufacturers have strong relationships with multiple platers located with a close geographic proximity to the milling operation. With reliable relationships in place, these manufacturers can count on their order being a very high priority and perhaps moved to the top of the plater’s queue. This alone can prevent multi-day delays!
In-house Gasketing
In-house dispensing of form in place gaskets under the same roof as the milling operation obviously has benefits. When talking about quick-turn manufacturing, think about eliminating multiple inspection points, redundant packaging operations and of course shipping delays. Ideally, look for a manufacturer who utilizes premium dispensing equipment to ensure accurate placement of the gasket bead. Laser and / or vision equipment is ideal for bead inspection.
Summary
Engineers who have a need for quick-turn parts turn those manufacturers, which can “do it all”, into their preferred vendors. At the top of their short list is the “full service” manufacturer who has the ability, capacity, experience and controls in place to provide “in house” the multiple processes their designs require. They understand the benefits of: communication with a single vendor; design collaboration between only two teams; a single P/O; knowing their quality assured, multi-processed order will arrive “just-in-time”.
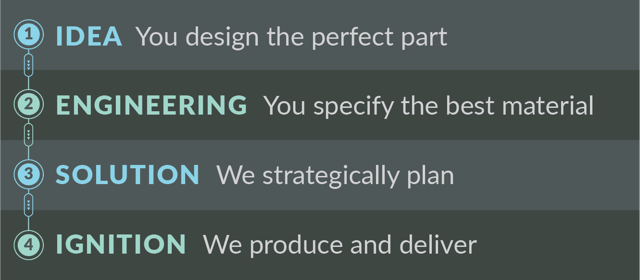
From “Idea to Ignition™” your trusted custom manufacturing vertically integrated partner is completely equipped to solve your aggressive timeline problem!