4 Considerations for EMI Shielding in Electric Vehicles
November 10, 2021
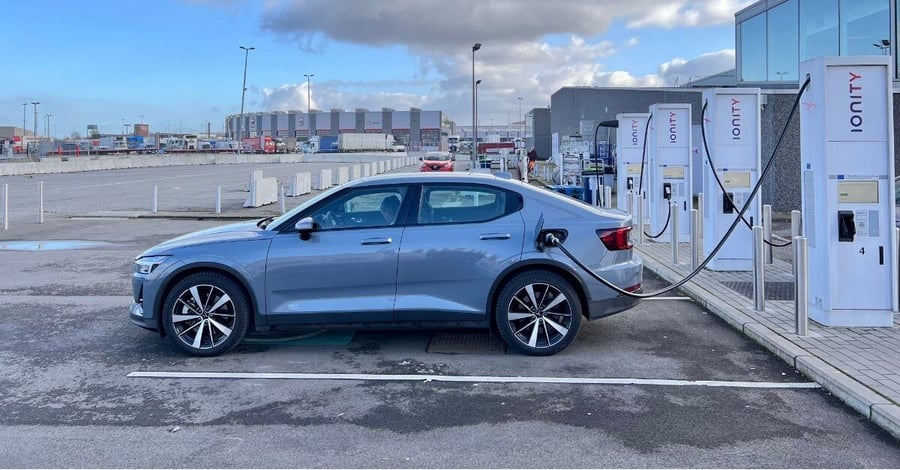
Manufactured with Speed and Precision
The manufacturing capabilities you need and the engineering support you want, all from a single partner.
Submit a DesignKey Points
- The rapid growth of electric vehicles (from 17,000 in 2010 to 7.2 million in 2019) creates new engineering challenges for EMI shielding, as EVs contain both powerful sources of electromagnetic interference and sensitive electronics that need protection.
- Passenger safety is a critical concern when designing EMI shielding for electric vehicles, as large battery packs emit electromagnetic radiation that can interfere with other vehicle systems.
- Conductive extrusions are typically the preferred manufacturing method for EMI gaskets in EVs over form-in-place (FIP) gaskets, offering better scalability for large shielding components and faster production speeds.
- Production efficiency is essential when manufacturing EMI shielding for mass-produced electric vehicles; extrusion can produce material at 3-5 feet per minute compared to much slower alternatives.
- EMI shielding in EVs must often perform double-duty by providing both electromagnetic interference protection and environmental sealing against weather conditions, especially for outdoor charging infrastructure.
The roads of the world were home to roughly 17,000 electric vehicles (EVs) in 2010. By 2019, that figure was closer to 7.2 million. All signs suggest that this number is only going to continue to go up as motorists ditch gas guzzlers for EVs in the name of cost-savings, the environment and tech-mindedness.
That means automakers have an enormous opportunity to get in on the EV ground floor and ride this wave to banner profits. And many are starting to do exactly that. The engineers and designers at those companies are now faced with the challenge of developing EVs that are reliable and well-built. This process brings up a concern: Electromagnetic interference shielding for electric vehicles.
And it’s a big concern. With an ever-increasing number of sources of electromagnetic interference (EMI), EV makers have to design vehicles that will be shielded from external EMI sources and internal ones, such as the massive battery packs that keep EVs moving. In this post, we’re going to share with you four key considerations for EMI shielding in electric vehicles. Read on to learn more.
Technology, engineering and manufacturing change all the time, but one thing stays consistent: the need for quality. By putting quality at the top of our list of concerns, Modus Advanced stays ahead of the curve to position itself as the top manufacturing partner to EV designers. Want to work with us? Get in touch.
Read our full guide on EMI Shielding
EMI Shielding for Electric Vehicles: 4 Key Tips
EVs face a unique set of concerns when it comes to EMI. That means you can’t just slap an EMI shielding material onto your EV design and call it a day. You have to approach proper EMI shielding for electric vehicles with care and a few key considerations. See below.
1. Passenger Safety Is Key
It should be pretty obvious to most people at this point that EVs are powered by a battery pack. But what might not be obvious is just how enormous the batteries in EVs actually are. They are huge — and if you think about it, it makes sense. To move an entire passenger vehicle, you need something a lot bigger than a handful of AAA batteries or even your standard car battery.
When you apply the EMI lens to this topic, that huge battery presents a safety problem. That’s because passengers are essentially sitting on top of this enormous battery that is constantly emitting electromagnetic radiation. And this can interfere with other electrical implements on the vehicle. To prevent this potential passenger safety issue, you’re going to have to have an EMI shielding enclosure surrounding the vehicle’s battery.
Visit our complete EMI shielding resource center.
2. Conductive Extrusions for EMI Shielding in Electric Vehicles
You may be well past the stage of realizing that you need to create an EMI shield to surround the EV’s battery. You’re more than likely at the stage in which you begin to design your EMI gaskets and O-rings. So, how do you plan to manufacture those parts?
At Modus, we’re pretty big fans of form-in-place (FIP) gaskets for a lot of applications in the automotive industry, but EMI shielding for electric vehicles is not an ideal application for FIP. That’s because we’re talking about very large EMI gaskets, while FIP is typically best for smaller or more intricate gaskets.
What you’ll really want to consider is extrusion. This is the manufacturing process of pushing your EMI shielding material through a die to cut it into the profile you need. From there, you lay the extruded EMI gasket into the groove of the enclosure. There are a few key reasons why conductive extrusions are typically best for EMI shielding in EVs:
- You’re typically going to be creating a hollow cord with a nickel aluminum or nickel graphite filler material, and that’s difficult to do (while remaining within spec) with molding or FIP.
- The mold and press required for such a large gasket would be enormous, presenting safety hazards and unnecessary difficulty for those who have to handle them.
- For this application, extrusion is going to make it easier than FIP or molding to create both an environmental seal and EMI shield.
3. Production Speed Matters
In most cases, EVs are meant to be mass-produced. You might need to manufacture thousands of the EMI gaskets you’re currently designing in order to produce the desired number of vehicles. That means your ability to produce these implements quickly is going to have a direct effect on budget and the bottom line.
This is yet another reason that extrusion is the ideal manufacturing method for EMI shielding in electric vehicles. EMI shielding material can flow through the extrusion process quickly — maybe three to five feet per minute — so you get the gasket length you need for a single vehicle in a couple of minutes. Compare that to molding, which can produce the requisite amount of shaped material in 10 to 15 minutes. Also, FIP gasket dispensers move much more slowly than extrusion typically does.
4. Environmental Seals Can Come Into Play
An effective EMI shielding gasket does not necessarily provide an effective environmental seal, but you’re probably going to need both. On the EVs themselves, sensitive implements need to be shielded not only from EMI, but also from the weather while they’re operating — especially in the harsher outdoor environments of colder, snowier areas.
That’s not where the need for environmental seals stops, though. You also have to consider EV charging stations. For at-home, in-garage chargers, this is often not an issue, but outdoor, public chargers have to be shielded from both EMI and the elements. This means you need to have a deep understanding of the properties of the gasket materials you select. Make sure they’ll provide the proper EMI resistance and a strong environmental seal.
Shielding EVs from EMI: Modus Advanced
The above points are a really long way of saying that EMI shielding for electric vehicles is a big deal, and it’s going to become a bigger deal as time passes. If you’re in the business of creating EVs, you need to be in business with Modus Advanced if you want to ensure your products have effective, efficient EMI shields.
We’re ready to help you with that. Just give us a call at (925) 960-8700 or reach out to us online. We’re looking forward to working with you.