The Best Process for Building a Custom RF Shield
May 16, 2022
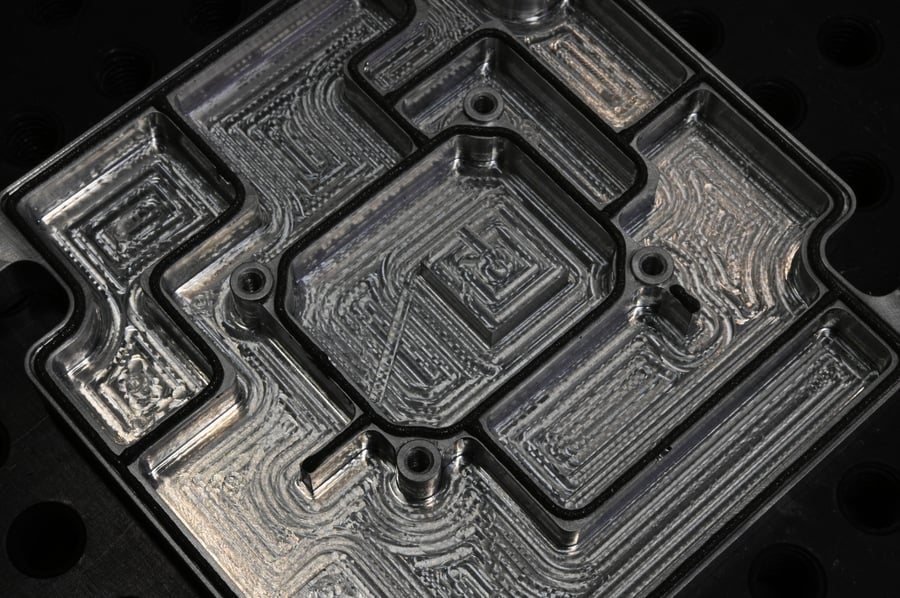
Manufactured with Speed and Precision
The manufacturing capabilities you need and the engineering support you want, all from a single partner.
Submit a DesignKey Points
- Building a custom RF shield can look a few different ways.
- The most efficient process is working with a vertically integrated RF shield manufacturer.
- Modus combines four manufacturing processes to deliver the best process for building a custom RF shield.
There is more than one way to do a lot of things, and that’s certainly true for building a custom radio frequency (RF) shield. Most engineers who deal with RF shield design are familiar with the traditional process — the one that involves multiple vendors, a lot of steps, long lead times, high freight costs and a ton of headaches. But is there a better way?
There certainly is, and we’ve found it. The best process for building a custom RF shield is working with a vertically integrated RF shield manufacturer. In this post, we’re going to explore what that looks like and why vertical integration offers such a superior manufacturing process. Read on to learn more.
Modus Advanced has vertically integrated its RF shield manufacturing processes to deliver shorter lead times and fewer headaches to our customers. It works like a charm. Want to get in on this? Reach out to our team.

Visit the Modus RF Shielding Resource Center
Traditional RF Shield Manufacturing vs. a Vertically Integrated Process
When you’re manufacturing a custom RF shield, you have a few choices when it comes to the manufacturing process: CNC machining, die cutting, form-in-place (FIP) and more. We have opinions on and experience with all of those, but for this discussion, we’re zooming out a bit. We’re discussing the overall process for getting the job done — the logistics and the tasks involved, rather than the specific tools used.
In that respect, you have two basic choices: the traditional process or the vertically integrated process Modus has implemented. Here’s why vertical integration offers the best process for building a custom RF shield.
More Steps Completed Under One Roof
By vertically integrating the CNC machining of metal housing, FIP gasket dispensing, plating and coating application and the application of thermal materials and RF absorbers, we eliminate several junctures at which mistakes can be made.
Thanks to vertical integration, all of those processes happen under one roof. That means colleagues communicate with one another about your part, as opposed to disparate companies that have no interest in one another’s success.
Shorter Lead Times
The traditional RF shield manufacturing process involves a lot of stopping and starting. When the CNC machining company is done with the metal housing, they send it back to you. Then, you send it to the gasket dispensing company, and they send it back to you. You then send it to a separate company to have platings and coatings applied, and you might have to do it all over again to apply thermal materials and RF absorbers.
All of that adds up to a lot of lead time. Typically, the lead time for the traditional process is between two and three months. Now, let’s compare that to the vertically integrated version. We don’t see any of that stopping and starting — one step is done, and that team moves the part along to the next team with no delay. That translates to a lead time that can be as short as two weeks.
Having to wait for less time for your RF shield to be manufactured is almost always a good thing. But when you’re working on a tight timeline, a short lead time can make a world of difference.
Read Everything You Need To Know About RF Shielding
Reduced Freight Costs
The fact that you don’t have to keep sending your sensitive and yet-to-be-completed RF shield from company to company doesn’t just shorten your lead times. It also directly reduces your freight costs.
Instead of having your RF shield shipped to you four separate times, you get it shipped to you one time, and that’s at the very end of the process. Because shipping these parts is more than a matter of tossing them in a box and taking them to UPS, it costs a lot. And having to do it fewer times reduces your costs. In fact, our vertically integrated process typically results in one quarter of the typical freight costs.
Higher Quality
In custom RF shield manufacturing, vertical integration means higher quality. The reason why is clear: Stakeholders in various parts of the manufacturing process work on the same team and in the same place. They can communicate the intricate details of their processes and their thinking, and they can go to one another for clarification.
Compare that to the traditional process. Separate companies are not likely to be able to read each other’s minds, and they may not reach out to each other for clarification on particular aspects of your part as they are completing their part of the process. Lower quality isn’t guaranteed with this process, but it is certainly more likely that mistakes will be made.
Why Choose Modus for Your RF Shielding Needs?
When your critical applications require reliable RF shielding, partnering with a manufacturing expert can make the difference between a device that performs flawlessly and one that fails in the field. Modus Advanced combines engineering expertise with vertical integration to deliver RF shields that meet the most demanding requirements in aerospace, defense, and medical device applications.
- Engineering-First Approach: With over 10% of our staff being engineers, we provide expert design feedback that improves manufacturability and performance
- Vertical Integration: From machining to FIP gasket dispensing, plating, and assembly, all under one roof, reducing lead times and risk
- Quality Systems: AS9100 and ISO 9001 certified processes ensure consistent, high-quality RF shields that perform when lives depend on them
- Prototype to Production Partner: Support throughout your entire product lifecycle, from rapid prototype turnaround in days to efficient scaling for ongoing production volumes with consistent quality and performance
- Materials Expertise: Access to the full spectrum of RF shielding materials with guidance on selecting the optimal solution for your specific application
Partner with Modus Advanced to accelerate your path to market with RF shields manufactured to the highest standards of quality and precision; because when one day matters, having the right manufacturing partner is the obvious choice.
RF Shield ManufacturingWork with the Best in Custom RF Shield Manufacturing
In our minds — and those of the customers for whom we have built RF shields — vertical integration offers the best process for building a custom RF shield. But you really don’t have to take our word for it; you just have to look at the numbers: Modus Advanced’s SigShield process results in four times the manufacturing processes under one roof, half the lead time, a quarter of the freight costs and 100% fewer headaches.
That’s hard to beat. The good news is that you don’t have to beat it. To get all the benefits of vertical integration, you just have to work with Modus Advanced when you’re building a custom RF shield. Ready to get started? Reach out to our expert team by calling 925-960-8700 or contacting us online today.