RF Shielded Enclosures: Designing & Manufacturing for Success
April 30, 2025
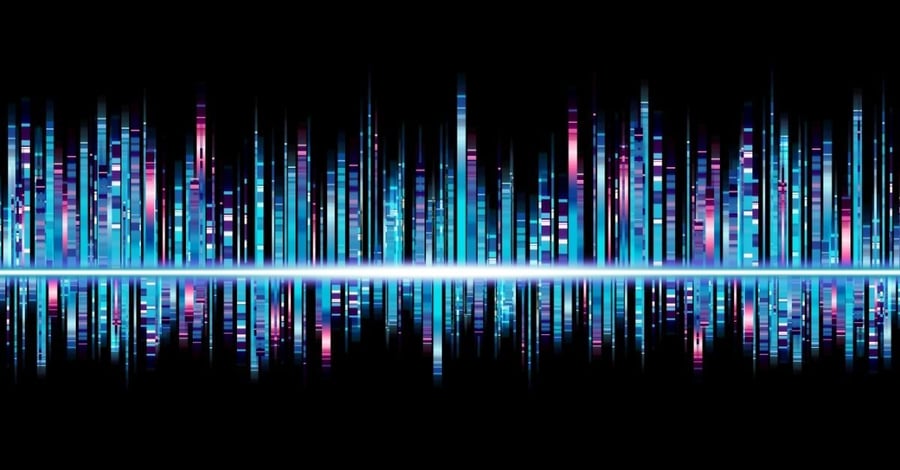
Manufactured with Speed and Precision
The manufacturing capabilities you need and the engineering support you want, all from a single partner.
Submit a DesignKey Points
- RF shielded enclosures are essential in numerous industries to protect sensitive electronics from interference while containing emissions within the enclosure.
- Proper material selection significantly impacts shielding effectiveness, with different metals offering varying levels of protection and galvanic compatibility.
- Design considerations like corner radii, wall thickness, and gasket integration dramatically affect both manufacturing cost and shielding performance.
- Working with manufacturing partners early in the design process can prevent costly redesigns and accelerate time to market for critical applications.
- Vertical integration of manufacturing processes reduces lead times and quality risks when producing complex RF shielded enclosures.
- Proper testing protocols ensure your RF shielded enclosure meets required standards before deployment in the field.
Definition
What is an RF Shielded Enclosure?
An RF shielded enclosure is a specialized housing designed to block electromagnetic interference by preventing radio frequency signals from entering or exiting the enclosed space. It typically consists of a conductive metal structure with carefully designed seams, gaskets, and apertures that work together to create a Faraday cage effect, protecting sensitive electronics inside from external interference or containing emissions from radiating outward.

Visit the Modus RF Shielding Resource Center
Why RF Shielded Enclosures Matter More Than Ever
In today's hyper-connected world, electromagnetic interference poses an increasing threat to sensitive electronic equipment. RF shielded enclosures serve as the critical defense mechanism that protects vital systems from external signals while containing potentially disruptive emissions within a controlled space.
Engineers across aerospace, defense, medical device, and telecommunications industries face the challenge of designing RF shielded enclosures that meet stringent performance requirements while remaining manufacturable at reasonable costs. The stakes couldn't be higher – in medical devices, interference could compromise patient safety; in defense applications, it could jeopardize mission success.
At Modus Advanced, we've manufactured thousands of RF shielded enclosures across multiple industries, giving us unique insight into what makes for successful designs. This comprehensive guide will walk you through everything you need to know about designing and manufacturing effective RF shielded enclosures.
Understanding the Fundamentals of RF Shielding
Before diving into design specifics, it's crucial to understand how RF shielded enclosures actually work. An RF shielded enclosure operates on the principle of creating a conductive barrier that interrupts electromagnetic fields. This Faraday cage effect relies on the enclosure's ability to reflect, absorb, or redirect electromagnetic energy.
The effectiveness of an RF shielded enclosure depends on several key factors:
- Material conductivity: Higher conductivity materials generally provide better shielding
- Material thickness: Thicker materials typically offer improved attenuation
- Enclosure continuity: Any gaps, seams or apertures can compromise shielding effectiveness
- Frequency range: Different designs perform better at specific frequency ranges
- Gasket performance: The quality of conductive gaskets determines how well seams and openings are sealed
Understanding these fundamentals allows engineers to make informed decisions when designing RF shielded enclosures for specific applications.
RF Shielding: Everything You Need to Know
Material Selection for Optimal RF Shielded Enclosures
The material you select for your RF shielded enclosure significantly impacts both performance and manufacturability. Different metals offer varying levels of shielding effectiveness across frequency ranges.
Here's a comparison of common materials used in RF shielded enclosures:
Material | Shielding Effectiveness | Weight Considerations | Corrosion Resistance | Cost |
Aluminum | Good (60-90 dB) | Lightweight | Good with proper finishing | Moderate |
Steel | Very Good (80-110 dB) | Heavy | Fair to Good | Low to Moderate |
Copper | Excellent (90-120 dB) | Heavy | Poor without plating | High |
Nickel-Silver | Very Good (80-100 dB) | Moderate | Excellent | High |
Zinc | Good (60-80 dB) | Moderate | Good | Moderate |
When selecting materials, consider not just shielding performance but also:
- Galvanic compatibility: Ensure materials won't cause corrosion when in contact with other metals
- Environmental conditions: Temperature extremes, humidity, and chemical exposure impact material longevity
- Weight constraints: Particularly important in aerospace applications
- Manufacturability: Some materials are easier to machine or form than others
The proper material selection forms the foundation of an effective RF shielded enclosure design. Consult with your manufacturing partner early in the design process to ensure your material choice aligns with both performance requirements and manufacturing capabilities.
Key RF Shielding Materials for Effective Enclosures
When designing an RF shielded enclosure, material selection significantly impacts both performance and cost-effectiveness. Each material offers different shielding properties, manufacturing characteristics, and environmental resilience. Understanding these differences helps engineers make informed decisions based on their specific application requirements.
The following materials are commonly used in RF shielded enclosures:
- Aluminum: Lightweight with good shielding effectiveness, excellent machinability, and cost-effectiveness for most applications. Different alloys provide varying combinations of strength and workability.
- Copper: Superior electrical conductivity providing excellent shielding across a wide frequency range. While heavier and more expensive than aluminum, copper is often used in high-performance applications where maximum shielding is required.
- Steel: Provides strong mechanical properties alongside good shielding effectiveness. Various steel alloys offer different combinations of strength, magnetic permeability, and corrosion resistance.
- Nickel-Silver Alloys: Offer excellent corrosion resistance and good shielding properties. These alloys are particularly valuable in harsh environments where galvanic corrosion could be an issue.
- Conductive Elastomers: Essential for gasketing applications, these materials combine elasticity with electrical conductivity through metal particle fillers like silver-aluminum, silver-copper, or nickel-graphite.
- Conductive Coatings: Applied to non-conductive substrates to provide shielding capabilities. Options include nickel, silver, and copper-based coatings with varying performance characteristics.
- MuMetal & High-Permeability Alloys: Specialized materials for low-frequency magnetic shielding applications, which can complement traditional RF shielding materials in certain scenarios.
Each material category includes numerous specific formulations optimized for different applications, environmental conditions, and manufacturing methods. Working with a knowledgeable manufacturing partner helps ensure you select the optimal material for your specific RF shielded enclosure requirements.
For a comprehensive breakdown of material properties, selection guidelines, and application-specific recommendations, refer to our complete RF Shielding Materials Guide.
Critical Design Considerations for RF Shielded Enclosures
Designing an effective RF shielded enclosure requires balancing electromagnetic performance with practical manufacturing considerations. The following design elements significantly impact both shielding effectiveness and manufacturability:
Corner Radii and Internal Features
Inside corners with larger radii are significantly easier to manufacture using standard CNC machining techniques. Sharp inside corners often require specialized manufacturing processes like EDM (Electrical Discharge Machining), increasing both cost and lead time.
When designing your RF shielded enclosure, consider these guidelines for internal features:
- Maintain inside corner radii of at least 0.125" whenever possible
- Design pocket depths no greater than 4:1 depth-to-width ratio
- Allow for standard tool access to all features
- Avoid extremely deep, narrow pockets that require specialized tooling
These design choices significantly impact manufacturability without compromising shielding performance. Your manufacturing partner can provide specific recommendations based on their equipment capabilities.
Wall Thickness and Structural Integrity
The walls of your RF shielded enclosure must balance between sufficient thickness for mechanical stability and practical manufacturing constraints. Floor thickness is particularly important as it affects both rigidity and machining requirements.
Consider these guidelines when determining wall thickness:
- Maintain minimum wall thickness of 0.060" for aluminum enclosures
- Consider 0.080" or greater for larger enclosures requiring more structural integrity
- Design floor thickness to prevent warping during machining (typically minimum 0.100")
- Account for any post-processing requirements like plating that may affect final dimensions
These considerations ensure your RF shielded enclosure remains structurally sound while meeting electromagnetic requirements. Strategic design choices can significantly reduce manufacturing complexity.
Gasketing and Seam Treatment
Even the most perfectly machined RF shielded enclosure requires proper gasket integration to maintain shielding effectiveness. Seams, joints, and removable access panels represent potential points of failure in your shielding design.
Form-in-place (FIP) gaskets provide excellent solutions for complex RF shielded enclosures. These gaskets:
- Conform perfectly to surface irregularities
- Can be applied in precise, narrow beads
- Allow for complex gasket patterns
- Provide consistent compression force when properly designed
- Maintain shielding effectiveness across the operational lifetime
When designing for gasket integration, consider these critical factors:
- Provide adequate flange width for gasket application (typically minimum 0.060")
- Design for appropriate compression stops to prevent over-compression
- Account for gasket height in your overall dimensional specifications
- Consider accessibility for gasket application during manufacturing
- Specify appropriate conductive filler materials based on frequency requirements
Proper gasket integration is often the difference between a marginally effective RF shielded enclosure and one that meets the most stringent requirements. Work with your manufacturing partner to select the optimal gasket solution for your specific application.
Manufacturing Methods for RF Shielded Enclosures
The manufacturing approach for your RF shielded enclosure significantly impacts final performance, lead time, and cost. Understanding the pros and cons of different manufacturing methods helps you make informed design decisions.
CNC Machining for RF Shielded Enclosures
CNC machining remains the most common method for manufacturing RF shielded enclosures due to its precision and flexibility. This approach involves removing material from solid stock to create the final enclosure shape.
The advantages of CNC machining for RF shielded enclosures include:
- No hard tooling requirements, reducing upfront costs
- Excellent dimensional accuracy and consistency
- Ability to create complex geometries with proper design
- Fast turnaround for prototypes and small production runs
- Wide range of machinable materials suitable for RF shielding
When designing for CNC machining, consider these factors to optimize manufacturability:
- Minimize the number of setups required by designing for simple fixturing
- Account for standard tooling capabilities when specifying features
- Design for standard material stock sizes to reduce material waste
- Specify appropriate tolerances based on shielding requirements
CNC machining provides an excellent balance of performance and cost for most RF shielded enclosure applications. Your manufacturing partner can help optimize your design for their specific equipment capabilities.
Die Casting for Higher Volume Applications
For very high-volume production of RF shielded enclosures, die casting offers significant advantages in terms of unit cost and production speed. This process involves injecting molten metal into a die cavity to form the enclosure.
Die casting considerations for RF shielded enclosures include:
- Significant upfront tooling costs must be amortized over production volume
- Design must account for draft angles, parting lines, and ejection requirements
- Secondary machining operations often needed for critical features
- Material options more limited than with CNC machining
- Consistent part quality once process is established
For applications requiring thousands of identical RF shielded enclosures, die casting may provide the most cost-effective manufacturing solution. However, the high initial investment makes this approach less suitable for lower volumes or designs likely to change.
Testing and Validation of RF Shielded Enclosures
No RF shielded enclosure design is complete without proper testing and validation protocols. Testing ensures your enclosure meets the required performance specifications before deployment in the field.
Common testing methods for RF shielded enclosures include:
- Shielding effectiveness testing: Measures the enclosure's ability to attenuate electromagnetic fields across frequency ranges
- EMI/EMC compliance testing: Verifies the enclosure meets regulatory requirements
- Environmental testing: Ensures performance under temperature, humidity, and vibration conditions
- Physical testing: Verifies dimensional accuracy and mechanical properties
Working with an experienced manufacturing partner can streamline the testing process by identifying potential issues early in the design phase. Many manufacturers offer in-house testing capabilities or can coordinate with third-party testing facilities.
Proper documentation of test results not only validates current designs but also provides valuable data for future RF shielded enclosure projects.
The Advantages of Vertical Integration in Manufacturing
One of the most significant challenges in producing RF shielded enclosures is the coordination between multiple manufacturing processes. Traditional approaches often involve sending parts to different vendors for machining, plating, gasket application, and assembly – adding time, cost, and quality risks at each transition.
Vertically integrated manufacturing offers significant advantages for RF shielded enclosures:
- Reduced lead times: Eliminates shipping between vendors for different processes
- Improved quality control: Consistent standards across all manufacturing steps
- Enhanced communication: Single point of contact throughout the process
- Design optimization: Comprehensive feedback on manufacturability across processes
- Cost efficiency: Lower overhead and simplified project management
At Modus Advanced, our SigShield process exemplifies the benefits of vertical integration. We handle everything from metal machining to form-in-place gasket dispensing, plating, and final assembly – all under one roof. This approach dramatically reduces lead times while ensuring consistent quality across every step of the manufacturing process.
Working with the Right Manufacturing Partner
The success of your RF shielded enclosure design ultimately depends on selecting the right manufacturing partner. Look for these key attributes when evaluating potential partners:
- Engineering expertise: Partners with on-staff engineers provide valuable design feedback
- Quality certifications: Look for AS9100, ISO 9001, and industry-specific certifications
- Vertical integration: The ability to handle multiple manufacturing processes in-house
- Experience with RF shielding: Demonstrated success with similar applications
- Collaboration approach: Willingness to engage early in the design process
- Testing capabilities: In-house or coordinated testing services
The right manufacturing partner brings more than just production capabilities – they contribute valuable expertise that improves your RF shielded enclosure design and accelerates your time to market.
From Design to Reality: The Path Forward
Creating effective RF shielded enclosures requires balancing technical performance with practical manufacturing considerations. By following the guidelines in this article and engaging with experienced manufacturing partners early in the design process, you can develop RF shielded enclosures that meet the most demanding requirements.
Remember that every design decision impacts both performance and manufacturability. Simple choices like corner radii, wall thickness, and gasket integration can make the difference between a straightforward manufacturing process and one filled with expensive complications.
At Modus Advanced, we specialize in manufacturing high-performance RF shielded enclosures for the most demanding applications in medical, defense, and aerospace industries. Our team of engineers works directly with customers to optimize designs for both performance and manufacturability, ensuring you get the exact RF shielded enclosure you need when you need it.
Ready to turn your RF shielded enclosure design into reality? Contact our team today to learn how our vertically integrated manufacturing approach can accelerate your path to market while ensuring the highest quality standards.