Understanding the Aerospace Manufacturing Industry: Trends, Challenges, and Opportunities
June 30, 2025
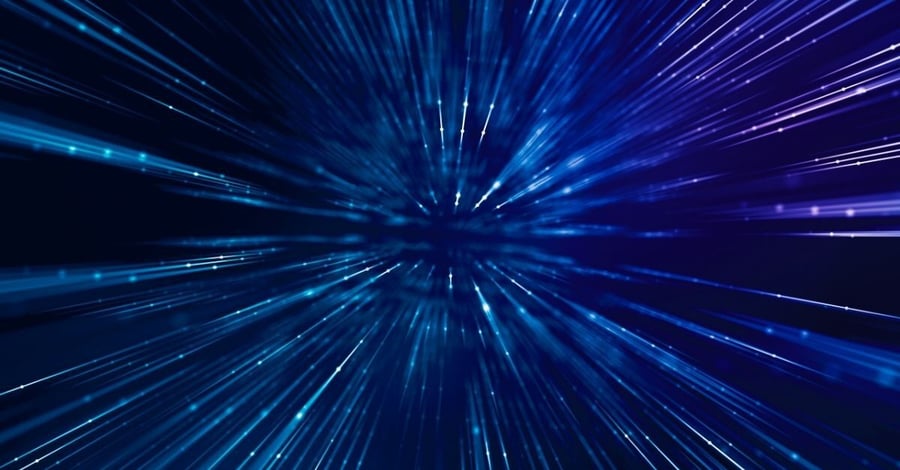
Manufactured with Speed and Precision
The manufacturing capabilities you need and the engineering support you want, all from a single partner.
Submit a DesignKey Points
The aerospace manufacturing industry stands at a critical inflection point as new technologies reshape traditional processes and emerging markets drive unprecedented demand. Engineers face complex challenges spanning supply chain resilience, advanced materials integration, and evolving regulatory frameworks.
Commercial space ventures are accelerating innovation cycles while defense modernization programs demand higher performance standards. Manufacturing partners must navigate these dynamics while maintaining the precision and reliability that lives depend on.
Understanding these industry forces helps engineers make informed decisions about technologies, partnerships, and strategic investments that will define the next decade of aerospace development.
What is the Aerospace Manufacturing Industry?
The aerospace manufacturing industry encompasses the design, development, production, and maintenance of aircraft, spacecraft, satellites, and related systems and components. This complex sector serves both commercial and defense markets, representing a cornerstone of modern engineering and technology that influences both economic and national security dynamics.
Aerospace manufacturing involves creating everything from commercial passenger aircraft and military jets to spacecraft, satellites, engines, avionics systems, and thousands of specialized components
Aerospace manufacturing involves creating everything from commercial passenger aircraft and military jets to spacecraft, satellites, engines, avionics systems, and thousands of specialized components. The industry combines advanced engineering disciplines including aerodynamics, materials science, structural engineering, and propulsion systems to produce vehicles capable of operating in the demanding environments of air and space.
The sector is characterized by stringent quality requirements, long development cycles, and substantial capital investments. Unlike many manufacturing industries, aerospace production must meet zero-defect standards where component failures can result in catastrophic consequences, making quality management and regulatory compliance fundamental to every aspect of operations.
The Current State of Aerospace Manufacturing
The aerospace manufacturing landscape has evolved dramatically over the past decade, driven by technological breakthroughs and shifting market demands. Traditional aerospace giants now compete alongside agile startups, while commercial space companies have fundamentally altered industry expectations for cost, speed, and innovation.
According to recent industry analysis, the global aerospace market size reached $373.61 billion in 2024 and is projected to grow to $791.78 billion by 2034, representing a compound annual growth rate (CAGR) of 7.8%. This substantial growth reflects recovering commercial aviation demand, increased defense spending, and the expanding commercial space sector.
Unlike many manufacturing industries, aerospace production must meet zero-defect standards where component failures can result in catastrophic consequences
Modern aerospace manufacturing encompasses everything from commercial aircraft production to satellite systems, military aircraft, and space exploration vehicles. Each segment faces unique technical requirements and regulatory challenges that shape manufacturing approaches and material selection.
The industry's emphasis on weight reduction, fuel efficiency, and performance optimization continues to push the boundaries of materials science and manufacturing processes. Engineers must balance these performance requirements with stringent safety standards and cost considerations across increasingly complex supply chains.
Emerging Trends Reshaping Aerospace Manufacturing
Advanced Materials Integration
Composite materials have become the backbone of modern aerospace design, offering superior strength-to-weight ratios compared to traditional metals. Carbon fiber reinforced polymers (CFRP) now account for significant portions of aircraft structures, while ceramic matrix composites (CMCs) enable higher operating temperatures in engine applications.
Additive manufacturing has opened new possibilities for complex geometries previously impossible with conventional machining. Metal 3D printing allows for lightweight lattice structures and integrated cooling channels that optimize both performance and manufacturing efficiency.
These material advances require specialized manufacturing expertise and quality control systems that can ensure consistent properties across production runs. Understanding how different materials behave in manufacturing processes becomes critical for aerospace applications.
Digital Manufacturing and Industry 4.0
Smart manufacturing systems integrate sensors, data analytics, and machine learning to optimize production processes in real-time. Predictive maintenance algorithms reduce downtime while quality monitoring systems detect defects before they impact final products.
Digital twins enable virtual testing and optimization before physical prototyping, reducing development cycles and material waste. These technologies particularly benefit complex assemblies where traditional testing methods are time-consuming or destructive.
Manufacturing execution systems (MES) now provide end-to-end traceability that meets aerospace quality requirements while improving operational efficiency. The spending on digitalization by aerospace manufacturers is projected to grow from $33.6 billion in 2024 to $53.8 billion by 2034, at a CAGR of 4.8%.
Supply Chain Transformation
Aerospace manufacturers are reshoring critical production capabilities to reduce supply chain vulnerabilities exposed during recent global disruptions. This shift requires significant investment in domestic manufacturing capacity and workforce development.
Strategic partnerships between prime contractors and specialized suppliers have become more important as technical requirements increase in complexity. Suppliers who can provide engineering support and rapid prototyping capabilities offer competitive advantages in fast-moving programs.
Vertical integration strategies help manufacturers control quality and delivery schedules for critical components while reducing dependency on external suppliers.
International markets add complexity with varying certification requirements from European Aviation Safety Agency (EASA), Transport Canada, and other regulatory bodies. Manufacturers must design products and processes that can meet multiple regulatory frameworks simultaneously.
Military and defense applications introduce additional requirements including International Traffic in Arms Regulations (ITAR) compliance and Cybersecurity Maturity Model Certification (CMMC) standards that affect manufacturing processes and data handling.
The following table outlines key regulatory frameworks affecting aerospace manufacturing:
Regulatory Body | Primary Focus | Key Requirements |
FAA | Commercial Aviation | Part 21, Part 145, AS9100 |
EASA | European Aviation | Part 21, Part 145, EN 9100 |
DoD | Defense Systems | DFARS, ITAR, CMMC |
NASA | Space Systems | NPR 8735.2, AS9100 |
Quality and Reliability Standards
Aerospace applications demand zero-defect manufacturing where component failures can result in catastrophic consequences. Quality management systems must provide complete traceability from raw materials through final assembly and field service.
Statistical process control and capability studies (Cpk) ensure manufacturing processes consistently produce parts within specification limits. Many aerospace components require Cpk values of 1.67 or higher, significantly exceeding standards in other industries.
Non-destructive testing methods including ultrasonic inspection, X-ray analysis, and fluorescent penetrant inspection verify internal integrity without damaging finished parts. These testing requirements add time and cost to manufacturing processes while ensuring critical safety standards.
Supply Chain Vulnerabilities and Materials Shortages
The average US commercial aerospace OEM has more than 200 tier 1 suppliers and 12,000 tier 2 or tier 3 suppliers, creating vulnerability to disruptions anywhere in the chain
Supply chain disruptions, talent shortages, and inflation represent the biggest challenges for the aviation industry. Key components like semiconductors, electronics, and basic raw materials like aluminum and titanium are in short supply, causing delays that ripple through production lines.
The average US commercial aerospace OEM has more than 200 tier 1 suppliers and 12,000 tier 2 or tier 3 suppliers. This complex supply network creates vulnerability to disruptions anywhere in the chain.
The situation is further exacerbated by competing demands of OEMs needing parts for new builds and maintenance providers seeking the same components for repairs and overhauls. Case studies show how deep materials knowledge can help combat these supply chain challenges, demonstrating the value of working with experienced manufacturing partners.
Skills Gap and Workforce Development
The aerospace industry faces a significant shortage of skilled manufacturing professionals as experienced workers retire and new technologies require updated skill sets. Over 67% of respondents in the National Association of Manufacturers' outlook survey for the second quarter of 2024 identified "attracting and retaining a quality workforce" as a primary business challenge.
One leading global aerospace OEM estimates that the commercial aerospace segment in the United States alone could require an additional 123,000 technicians in the next two decades. Training programs must address both traditional machining skills and emerging technologies like additive manufacturing and digital quality systems.
Engineering roles increasingly require interdisciplinary knowledge spanning materials science, manufacturing processes, and digital systems. Universities and industry partnerships work to develop curricula that prepare engineers for these evolving requirements.
Market Opportunities and Growth Drivers
Commercial Space Expansion
The commercial space sector has experienced explosive growth as launch costs decrease and satellite applications expand. Small satellite constellations require high-volume manufacturing approaches previously uncommon in aerospace applications.
Public and private investment in space surged again in 2024, with satellite, launch and deep space missions all seeing sharp increases. The convergence of national security imperatives and commercial opportunity is accelerating innovation, though funding clarity and regulatory frameworks remain emerging challenges.
Space tourism and commercial space stations create new markets for life support systems, thermal management, and human-rated components. Advanced thermal management solutions become critical for these applications which often require innovative approaches to traditional aerospace manufacturing challenges.
Launch vehicle reusability has shifted focus from single-use reliability to systems designed for multiple flights, introducing new requirements for refurbishment and lifecycle management.
Defense Modernization Programs
Military modernization efforts emphasize advanced materials, stealth technologies, and integrated sensor systems that require specialized manufacturing capabilities. These programs often provide stable, long-term funding for technology development and production scale-up.
Over the last decade, the DoD budget requests for procurement and R&D related to missiles and munitions have increased by 340%, reaching $30.6 billion in fiscal 2024 from $9 billion in fiscal 2015. These investments indicate continued growth in the global solid rocket market through 2025.
Hypersonic vehicles and directed energy systems push material and manufacturing limits while requiring rapid development cycles to maintain technological advantages. Advanced EMI shielding solutions become critical enablers for these cutting-edge applications.
Unmanned systems across air, land, and sea domains create opportunities for manufacturers who can provide cost-effective solutions while meeting military performance and reliability standards.
Sustainable Aviation Initiatives
Environmental regulations and customer demands drive development of more fuel-efficient aircraft and alternative propulsion systems. The aerospace industry is investing heavily in Sustainable Aviation Fuel (SAF), hybrid-electric propulsion systems, and hydrogen-powered aircraft.
Electric and hybrid-electric aircraft require new approaches to power systems, thermal management, and weight optimization. These technologies often require specialized materials and manufacturing processes.
Sustainable aviation fuels and hydrogen propulsion systems create opportunities for manufacturers who can adapt existing technologies or develop new solutions for alternative energy systems. These technologies often require specialized materials and manufacturing processes.
Lifecycle assessment and circular economy principles influence design decisions, creating opportunities for manufacturers who can provide sustainable solutions throughout product lifecycles.
Technology Integration Challenges
Materials and Manufacturing Process Compatibility
Advanced materials often require specialized manufacturing processes that may not be compatible with existing production systems. Thermoplastic composites offer recyclability advantages but require different processing equipment compared to traditional thermoset materials.
Temperature-sensitive materials demand precise environmental controls throughout manufacturing processes. Clean room environments and controlled atmosphere processing add complexity and cost while ensuring material properties meet specifications.
Quality control methods must evolve to address new material characteristics and failure modes. Traditional inspection techniques may not detect defects in advanced composite structures or additively manufactured components.
Design for Manufacturing (DFM) Considerations
Complex geometries enabled by additive manufacturing create new design possibilities while introducing challenges for post-processing and quality verification. Support material removal and surface finishing can significantly impact production timelines and costs.
Multi-material assemblies require careful consideration of thermal expansion, galvanic corrosion, and interface bonding to ensure long-term reliability. Understanding how different materials bond together becomes critical for manufacturing processes that must accommodate these material interactions while maintaining assembly tolerances.
Standardization efforts help reduce complexity while allowing design flexibility for specific applications. Industry organizations work to develop guidelines that balance innovation with manufacturing practicality.
Strategic Manufacturing Partnerships
Supplier Selection Criteria
Aerospace manufacturers increasingly value suppliers who can provide engineering support throughout product development cycles. Design for manufacturability expertise helps optimize designs for production efficiency while maintaining performance requirements.
Vertical integration capabilities allow suppliers to control quality and delivery schedules across multiple manufacturing processes, reducing supply chain risks while enabling faster response to design changes
Vertical integration capabilities allow suppliers to control quality and delivery schedules across multiple manufacturing processes. This integration reduces supply chain risks while enabling faster response to design changes or production adjustments.
Investment in advanced manufacturing technologies demonstrates supplier commitment to continuous improvement and future capability development. Suppliers who adopt new technologies early often provide competitive advantages to their aerospace customers.
Partnership Models and Collaboration
Risk-sharing partnerships align supplier and customer interests while enabling access to advanced technologies and manufacturing capabilities. These arrangements often include shared development costs and long-term production commitments.
Technical collaboration programs facilitate knowledge transfer and joint problem-solving for complex manufacturing challenges. Regular technical reviews and continuous improvement initiatives strengthen these partnerships over time.
Strategic sourcing initiatives help aerospace manufacturers consolidate suppliers while building deeper relationships with key partners who can support multiple product lines and technologies.
Quality Systems and Compliance in Aerospace Manufacturing
AS9100 and Industry Standards
AS9100 quality management systems provide the foundation for aerospace manufacturing operations, building on ISO 9001 with aerospace-specific requirements. Configuration management, risk assessment, and continuous improvement processes ensure consistent quality across all operations.
First article inspection (FAI) procedures verify that manufacturing processes can consistently produce parts meeting all design requirements. These inspections document dimensional accuracy, material properties, and surface finish characteristics before production approval.
Corrective and preventive action (CAPA) systems address quality issues while preventing recurrence through root cause analysis and process improvements. These systems provide regulatory compliance while driving operational excellence.
ITAR Compliance and Security Requirements
The International Traffic in Arms Regulations (ITAR) controls the export and import of defense-related articles and services. Companies working in aerospace and defense must ensure that their processes and products comply with ITAR to prevent unauthorized access to sensitive technologies.
ITAR compliance involves rigorous vetting of employees, secure handling of information, and strict adherence to documentation and reporting requirements. Failure to comply with ITAR regulations can lead to serious fines, revoked contracts, and potentially criminal charges.
Aerospace manufacturers subject to ITAR regulations must register with the U.S. Department of State's Directorate of Defense Trade Controls (DDTC) and obtain necessary licenses or approvals for the export of defense-related articles and services.
Measurement and Testing Technologies
Coordinate measuring machines (CMM) and optical measurement systems provide dimensional verification with micron-level accuracy. These systems often integrate with manufacturing processes to provide real-time feedback for process control.
Material testing laboratories verify chemical composition, mechanical properties, and microstructural characteristics for incoming materials and finished components. Automated testing systems increase throughput while maintaining consistent test conditions.
Environmental testing simulates operating conditions including temperature cycling, vibration, and humidity exposure to verify component reliability before field deployment. Understanding why specific materials are used for vibration isolation helps engineers select appropriate testing methods and acceptance criteria.
The following table summarizes key measurement technologies in aerospace manufacturing:
Technology | Application | Typical Accuracy |
CMM | Dimensional inspection | ±0.001 inch |
Optical scanning | Complex geometry verification | ±0.0005 inch |
Ultrasonic testing | Internal defect detection | 1mm flaw detection |
X-ray inspection | Porosity and crack detection | 0.1mm flaw detection |
Future Outlook and Recommendations for the Aerospace Manufacturing Industry
Technology Investment Priorities
Additive manufacturing capabilities will become increasingly important as designs optimize for these production methods. Investment in metal printing systems and post-processing equipment enables access to high-value applications while reducing material waste.
Digital manufacturing systems provide competitive advantages through improved efficiency and quality control. Integration of sensors, data analytics, and machine learning creates opportunities for process optimization and predictive maintenance.
AI and automation are playing a significant role in aerospace manufacturing, flight operations, and air traffic management. AI-powered predictive maintenance is reducing aircraft downtime, while autonomous systems and AI-assisted processes are improving safety and efficiency.
Advanced materials processing capabilities position manufacturers for next-generation applications requiring improved performance characteristics. Investment in specialized equipment and training ensures readiness for emerging material technologies.
Strategic Positioning for Growth
Market diversification across commercial, defense, and space applications provides stability while accessing different growth opportunities. Each market segment offers unique technical challenges and business models that can strengthen overall capabilities.
Geographic expansion into international markets requires understanding of local regulations and certification requirements. Partnerships with local suppliers and engineering services can facilitate market entry while managing compliance risks.
Workforce development programs ensure access to skilled professionals capable of operating advanced manufacturing systems. Partnerships with educational institutions and professional organizations support long-term talent pipeline development.
Supply Chain Resilience Strategies
Companies are looking to source components from multiple suppliers to reduce their dependency on a single source, as the COVID-19 pandemic highlighted the importance of diversifying suppliers
Companies are looking to source components from multiple suppliers to reduce their dependency on a single source. The COVID-19 pandemic highlighted the importance of diversifying suppliers, as many aerospace manufacturers faced supply chain disruptions due to factory closures and transportation restrictions.
Investment in flexible supply chain management systems that support real-time tracking and inventory control becomes necessary. Advanced analytics and forecasting tools assist suppliers with dynamic insights into market trends and demand patterns.
Digital supply chain platforms enable greater visibility and control across complex supplier networks. These systems help manufacturers manage risk while optimizing costs and delivery performance.
Frequently Asked Questions About Aerospace Manufacturing
What are the main sectors within aerospace manufacturing?
Aerospace manufacturing includes commercial aviation (passenger and cargo aircraft), defense and military systems (fighter jets, bombers, missiles), space systems (satellites, launch vehicles, spacecraft), and general aviation (private and business aircraft). Each sector has unique requirements for materials, processes, and regulatory compliance.
How long does it typically take to certify a new aerospace component?
Certification timelines vary significantly based on component complexity and application. Simple components may take 6-12 months, while complex systems like new aircraft engines can require 3-7 years for full certification. The process involves extensive testing, documentation, and regulatory review to ensure safety and performance standards.
What are the most critical quality standards in aerospace manufacturing?
AS9100 is the primary quality management standard for aerospace, building on ISO 9001 with aerospace-specific requirements. Additional critical standards include AS9102 for first article inspection, ITAR for defense-related items, and various FAA, EASA, and other regulatory certifications depending on the application and market.
How is sustainability being addressed in aerospace manufacturing?
The industry is implementing multiple sustainability initiatives including development of sustainable aviation fuels (SAF), electric and hybrid-electric propulsion systems, lightweight materials to improve fuel efficiency, additive manufacturing to reduce waste, and circular economy principles for component lifecycle management.
Partnering for Aerospace Manufacturing Excellence
The aerospace manufacturing industry demands partners who understand the critical nature of every component and system. Mission success often depends on manufacturing precision, quality consistency, and delivery reliability across complex supply chains.
Modus Advanced brings AS9100 certification and ITAR compliance to ensure we meet the stringent requirements your applications demand, with over 10% of our staff consisting of engineers providing technical expertise
“Modus reviews designs, gives feedback, and provides priceless recommendations. On many occasions, their feedback has helped save time, improve our designs, and ultimately allows us to bring quality products to market faster.”
Lead Product Engineer
Telecommunications Company
Modus Advanced brings deep aerospace manufacturing expertise to support engineers developing next-generation aircraft, spacecraft, and defense systems. Our AS9100 certification and ITAR compliance ensure we meet the stringent requirements your applications demand.
Our vertically integrated capabilities, from CNC machining to form-in-place gasket dispensing, enable us to support multiple aspects of aerospace manufacturing under one roof. This integration reduces supply chain risks while accelerating development timelines for critical programs.
With over 10% of our staff consisting of engineers, we provide the technical expertise and collaborative approach that aerospace projects require. Our Design for Manufacturability process helps optimize designs for production efficiency while maintaining the performance characteristics that aerospace applications demand.
When your aerospace innovations must perform flawlessly in the harshest environments, choose a manufacturing partner who understands what's at stake. Contact us to learn how we can accelerate your path to aerospace manufacturing excellence.
aerospace specifications.
Tech-Etch specializes in precision fabrication of EMI shielding components including shields, gaskets, and specialized hardware. The company converts raw materials into finished components through photochemical etching, stamping, and forming processes.