Guidance for Designing an EMI Shielded Enclosure
November 8, 2021
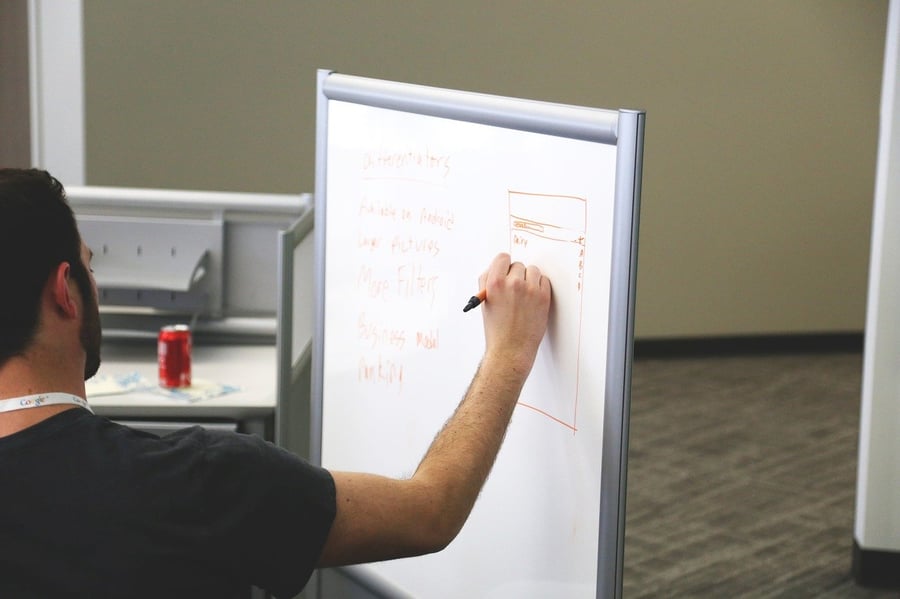
Manufactured with Speed and Precision
The manufacturing capabilities you need and the engineering support you want, all from a single partner.
Submit a DesignKey Points
- EMI shielded enclosures are often needed to protect specific components within devices rather than shielding entire systems, making their design critical to overall device functionality.
- Material selection is crucial when designing EMI shielded enclosures - options like silver, aluminum, nickel, and copper each offer different balances of effectiveness and cost that must be evaluated based on your application requirements.
- Galvanic compatibility between your enclosure materials and device housing must be considered to prevent corrosion that could compromise shield integrity over time.
- Gasket manufacturing method significantly impacts shield effectiveness - form-in-place (FIP) gaskets excel for intricate designs and small enclosures, while providing material efficiency benefits.
- Design considerations like using compression stops instead of grooves can prevent uneven gasket curing that might compromise shielding effectiveness.
- Working with an experienced manufacturing partner like Modus Advanced can help navigate these complex design decisions, potentially saving time and budget while ensuring optimal shielding performance.
Shielding sensitive devices from electromagnetic interference (EMI) is a critical consideration, but it doesn’t often require you to shield your entire device from EMI. More often, you just have to shield a particular part within the device, regardless of whether the potential EMI is coming from external sources or another source within the device. This is exactly what EMI shielded enclosures are meant for.
If you’ve reached the step in the design process in which you realize that you need an enclosure that can shield from EMI, you’re at a critical junction. The effectiveness of this enclosure will very likely determine the entire device’s ability to function properly. You have to make it perfect while also keeping in mind your budget and any external design specifications you have to satisfy.
In other words, you probably need some guidance. And you’re in the right place. The expert team at Modus Advanced has put together this quick and simple list of tips for designing an EMI shielded enclosure to help you avoid critical mistakes that can sink your entire design. Read on.
We’re proud of the EMI shields the Modus team is able to produce. Our near-perfect results are the product of decades of experience, hard work and a healthy helping of engineering and manufacturing expertise. If you want some of all of that for your design, reach out.
Read the Complete EMI Shielding Guide.
5 Tips for Designing a Perfect EMI Shielding Enclosure
If your EMI shielded enclosure isn’t right, you’re faced with the expensive and time-consuming task of taking it back to the drawing board to figure out what went wrong. Otherwise, you’ll have an ineffective or possibly even dangerous device on your hands. We’re here to make sure none of that happens to you. Start with the five key tips below.
1. Select the Right Materials for Your EMI Shielded Enclosure
Unless you’re very new to the EMI shielding world, you understand that you have several EMI shielding materials to choose from. These are typically metals like silver, aluminum, nickel and copper — sometimes alone and sometimes in combination with one another.
You might as well pick a shielding material out of a hat, right? Wrong. When you’ve specifically designed an EMI shielded enclosure, you have to consider several factors as you select shielding materials.
For example, you need to consider your project budget. Silver is a highly effective shielding material, but it’s expensive. On the other hand, graphite is more affordable, but you may sacrifice a little on the shielding effectiveness side. That sacrifice can pose a huge problem in designs meant for military applications, for which you must meet the military standard for EMI shielding: MIL-STD-285.
2. Keep Galvanic Compatibility in Mind
The materials that make up your EMI shielded enclosure are ostensibly going to come into contact with other parts of your device, such as the metal or plastic housing. That’s no problem until galvanic corrosion becomes a concern.
Galvanic corrosion occurs when two metals touch each other and exchange electrons. If you’re dealing with a metal housing and metal filler material, you’re going to need to know whether the two metals involved are galvanically compatible. Otherwise, you risk selecting an EMI shielding material that will degrade the metal housing surrounding your enclosure.
3. Choose the Right Gasket Manufacturing Method
You’ll need a gasket to seal the two sides of your enclosure, making it a critical component in determining the shielding effectiveness of the enclosure as a whole.
Form-in-place (FIP), extrusion, die cutting — there are plenty of ways to manufacture gaskets and similar EMI shielding implements. But which is right for your unique design? You’re going to need to know the answer as you design your EMI shielding enclosure.
FIP, in which EMI gaskets are dispensed directly onto their housing in liquid form, is typically ideal for intricate and/or very small applications, including small or complex EMI enclosures. This method also cuts down on material waste, possibly making room in the budget for a more expensive shielding material like silver. However, extrusion and die-cutting have their place in shielding enclosure design, too — especially for larger enclosures or those that will be sealed and unsealed frequently.
Learn how Modus is redefining the traditional supplier relationship
4. Where Possible, Opt for Compression Stops, Not Grooves
As you’re designing your EMI shielding enclosure, you may find yourself leaning heavily on grooves in which an FIP EMI gasket will be dispensed. This might be a mistake.
That’s because dispensing EMI gaskets into narrow grooves can cause the liquid gasket material to cure more toward one side of the groove than the other, creating a potentially ineffective seal and subpar shield. The quick fix? Opt for compression stops instead of grooves whenever possible in your enclosure design.
Deep Dive: 6 Tips for Designing a Form-in-Place EMI Gasket
Discover six proven engineering tips for designing form-in-place EMI gaskets that enhance electromagnetic shielding performance while reducing manufacturing complexity and production time.
Learn MoreRelated: Design Considerations for Machined Parts
Get 13 design tips for your metal housing, ensuring the best adherence and performance for any FIP materials applied to them.
Learn More5. Pick a Sufficient Dispensing Length
If you’re including an FIP EMI gasket in your EMI shielded enclosure design, you need to make sure the intended dispensing length is long enough to make sense for this manufacturing method. Really, you don’t want extremely short segments. This can cause problems during dispensing and make your design much more difficult to manufacture on the whole.
Visit our complete EMI shielding resource center.
Bonus Tip: Work with Modus Advanced
This is a blog post on the Modus website, so we’re willing to bet you’re not surprised to find out that we think we are a pretty good partner for producing EMI shielded enclosures and gaskets.
But believe us when we tell you the suggestion to work with our expert manufacturing and engineering team on your EMI shielded enclosure could be the most valuable tip there is to give. We’re here to quite literally make the difference between an ineffective and costly enclosure and one that works exactly as intended and squarely within your budget.
Why Choose Modus for Your EMI and RF Shielding Needs?
When your critical applications require reliable EMI shielding, partnering with a manufacturing expert can make the difference between a device that performs flawlessly and one that fails in the field. Modus Advanced combines engineering expertise with vertical integration to deliver RF shields that meet the most demanding requirements in aerospace, defense, and medical device applications.
- Engineering-First Approach: With over 10% of our staff being engineers, we provide expert design feedback that improves manufacturability and performance
- Vertical Integration: From machining to FIP gasket dispensing, plating, and assembly, all under one roof, reducing lead times and risk
- Quality Systems: AS9100 and ISO 9001 certified processes ensure consistent, high-quality RF shields that perform when lives depend on them
- Prototype to Production Partner: Support throughout your entire product lifecycle, from rapid prototype turnaround in days to efficient scaling for ongoing production volumes with consistent quality and performance
- Materials Expertise: Access to the full spectrum of RF shielding materials with guidance on selecting the optimal solution for your specific application
Partner with Modus Advanced to accelerate your path to market with RF shields manufactured to the highest standards of quality and precision; because when one day matters, having the right manufacturing partner is the obvious choice.
RF Shield ManufacturingIt’s what we do, plain and simple. And we can do it for you, too. Ready to learn more about how the Modus team can help you get your EMI shielding enclosure exactly right? We’ve got plenty to say about that. Just give us a call at (925) 960-8700 or contact us online to get started.