Sharp Corners on CNC Machined Parts: The Impossible Feature That's Killing Your Timeline
July 7, 2025
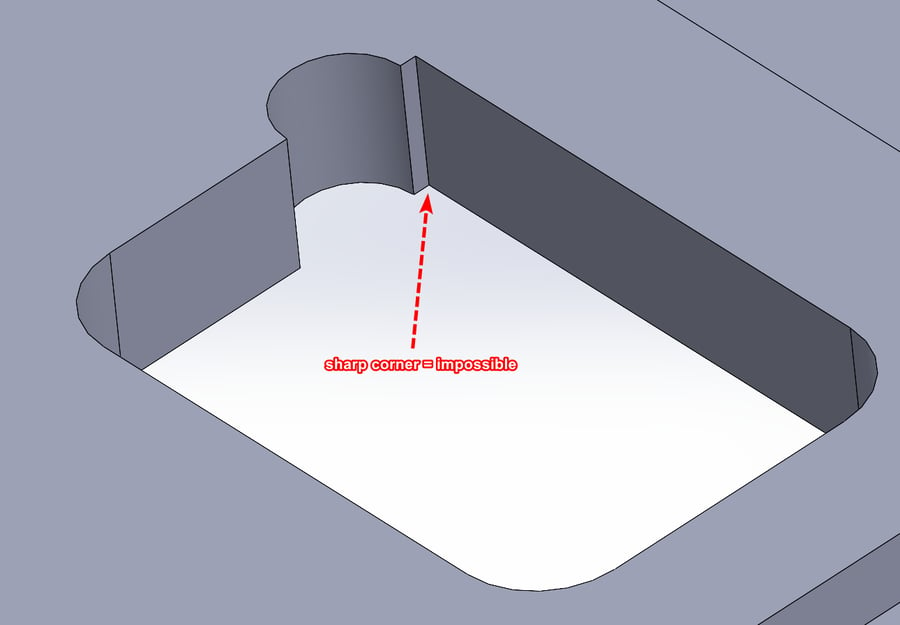
Manufactured with Speed and Precision
The manufacturing capabilities you need and the engineering support you want, all from a single partner.
Submit a DesignKey Points
- Sharp 90-degree corners in CNC machined parts cavities are physically impossible to create with rotating cutting tools
- Larger corner radii significantly reduce programming time, machining time, and inspection complexity
- The smallest achievable radius depends on tool size, with larger tools enabling faster material removal
- Proper radius specification prevents costly design revisions and manufacturing delays
- Understanding tool limitations during design prevents over-specification of impossible features
Why CNC Machined Parts Can't Have Sharp Internal Corners: The Physics Problem Every Engineer Needs to Understand
When you specify a sharp corner in a CNC machined parts cavity, you're asking for something that defies the fundamental physics of CNC machining. Every cutting tool is round, and round tools simply cannot create perfectly sharp internal corners.
This isn't a limitation of Modus Advanced's capabilities or equipment sophistication. It's a universal constraint that applies to every CNC machine shop on the planet. No matter how advanced the equipment or skilled the machinist, a rotating cutting tool will always leave some radius in internal corners.
The confusion often stems from external corners on CNC machined parts, which can appear sharp because material is removed from both sides. Internal corners, however, require the tool to plunge into material, leaving its circular profile as the defining geometry.
The Universal Truth About CNC Machining Limitations
According to industry manufacturing experts, "it is generally not possible to achieve a perfectly sharp angle on internal corners" in CNC machined parts. This limitation exists because cutting tools have a cylindrical shape and must rotate to provide the cutting mechanism.
Why Radius Size Matters More Than You Think for CNC Machined Parts
The size of the radius you specify for your CNC machined parts has cascading effects throughout the entire manufacturing process. Each decision about corner geometry impacts programming time, machining efficiency, and quality control procedures.
Programming complexity increases dramatically with smaller radii on CNC machined parts. CAM programmers must select smaller tools, create more complex toolpaths, and often program multiple operations where a single operation might suffice with larger radii.
Key impacts of radius size decisions on CNC machined parts:
- Programming time scales inversely with radius size
- Smaller radii require specialized tooling and multiple operations
- Quality inspection complexity increases with tighter specifications
- Tool changes multiply with small-radius requirements
The Manufacturing Time Impact
Research from machining cost optimization studies indicates that "Sharp, 90-degree corners require machines to stop, the part to be rotated, and then the process continues," significantly increasing machining time and costs for CNC machined parts.
Read the full Design for Manufacturability guide.
The Tool Size Equation: Bigger Radius, Faster CNC Machined Parts Manufacturing
Understanding the relationship between tool size and corner radii helps you make informed design decisions for CNC machined parts. The radius in any internal corner cannot be smaller than the radius of the cutting tool used to create it.
A 6mm (0.25") end mill creates a minimum radius of 3mm (0.125") in CNC machined parts. A 12mm (0.5") end mill leaves a 6mm (0.25") radius. Using the largest possible tool for your application delivers the fastest manufacturing times and best surface finishes.
Tool Diameter | Minimum Radius | Relative Material Removal Rate | Typical Applications |
3mm (0.125") | 1.5mm (0.06") | 1x | Fine details, small features |
6mm (0.25") | 3mm (0.125") | 4x | General machining |
12mm (0.5") | 6mm (0.25") | 16x | Heavy material removal |
25mm (1.0") | 12.5mm (0.5") | 64x | Large cavity roughing |
Material removal rates scale dramatically with tool size for CNC machined parts. A 12mm end mill can remove material roughly four times faster than a 6mm end mill of similar geometry. This difference compounds across multiple features, potentially saving hours of machining time on complex parts.
Industry Data on Tool Size Impact
Manufacturing efficiency studies show that "larger tooling produces larger corner radii, but runs faster, which decreases the time it takes for the part to be machined."
Read our Complete Guide to CNC Machining
Design Guidelines That Actually Work for CNC Machined Parts
The most effective approach to corner radii on CNC machined parts involves specifying the largest radius your design can accommodate. Rather than defaulting to the smallest possible radius, start with larger values and only reduce them when absolutely necessary for fit, form, or function.
Radius optimization strategies for CNC machined parts:
- Use consistent radii across multiple features to minimize tool changes
- Prioritize functional requirements over aesthetic preferences
- Consider weight impact versus manufacturing time trade-offs
- Collaborate with manufacturing teams during design reviews
Consider the interaction between multiple features when specifying radii for CNC machined parts. If your part has several internal corners, using consistent radii across features allows the same tool to machine multiple operations.
Industry Best Practices for Corner Radius
CNC machining design experts recommend making "the radius slightly oversized from the intended tool diameter" to reduce contact area and achieve better surface finish on CNC machined parts.
Manufacturing Impact by Radius Size on CNC Machined Parts
Different radius sizes create distinct manufacturing challenges and opportunities for CNC machined parts. Understanding these relationships helps you balance design requirements with manufacturing efficiency.
Radius Range | Manufacturing Characteristics | Programming Impact | Quality Control |
0.5-1.5mm (0.02-0.06") | Specialized small tools required | Complex toolpaths, multiple passes | CMM inspection required |
1.5-3mm (0.06-0.125") | Standard small tooling | Moderate complexity | Specialized gauges needed |
3-6mm (0.125-0.25") | Standard tooling | Straightforward programming | Standard inspection methods |
6mm+ (0.25"+) | Large tools, aggressive cuts | Simple programming | Basic measurement tools |
Ultra-small radii dramatically increase machining time for CNC machined parts and may require multiple finishing passes to achieve acceptable surface finish. Quality inspection becomes more complex and time-consuming with specialized equipment requirements.
Quality Control Complexity
According to precision machining research, achieving extremely sharp corners may require specialized inspection methods, as "it's important to note that wire EDM machines are very slow, especially compared to CNC cutting tools."
The Hidden Costs of Over-Specification in CNC Machined Parts
Specifying unnecessarily tight corner radii creates costs that extend far beyond the machining operation itself for CNC machined parts. Programming time increases as CAM operators must select appropriate tools and develop suitable cutting strategies for small features.
Hidden cost factors for CNC machined parts:
- Extended programming time for complex toolpath generation
- Increased tool inventory for specialized small end mills
- Higher tool replacement costs due to accelerated wear
- Additional quality control time and equipment requirements
Quality control complexity scales with radius requirements for CNC machined parts. Measuring small radii requires specialized inspection equipment and longer inspection times. Standard go/no-go gauges may not work effectively, requiring coordinate measuring machine (CMM) inspection for every part.
Cost Impact Data
Manufacturing cost analysis indicates that "smaller tools are also more limited in the feature depth (pocket depth) they can achieve" and "smaller tools remove only small amounts of materials in a single pass, you will need slow-speed multiple passes, increasing CNC machining time and cost."
Material Considerations for Corner Radii in CNC Machined Parts
Different materials respond differently to small radius machining operations in CNC machined parts. Harder materials like stainless steel or titanium create additional challenges when machining small radii, as cutting forces increase and tool life decreases dramatically with smaller tools.
Aluminum and other soft materials machine more forgivingly with small radii in CNC machined parts, but still benefit significantly from larger radii specifications. The time savings from using larger tools often outweighs any material property advantages.
Surface finish requirements may dictate minimum radius sizes in certain materials for CNC machined parts. Some materials produce better surface finishes with larger tools and higher cutting speeds, making small radii counterproductive to overall part quality.
Material-Specific Challenges
CNC machining material studies note that "machining composites with layered structures demands careful consideration of layer orientation, as it can significantly impact the precision of cutting sharp corners."
Visit our Complete CNC Machining Resource Center
When Sharp Corners Are Actually Required in CNC Machined Parts
Legitimate applications for the smallest possible radii do exist in precision manufacturing of CNC machined parts. Mating part considerations sometimes require specific radius sizes to ensure proper fit and seal compression in assembled products.
Valid reasons for small radii in CNC machined parts:
- Critical interface requirements with existing hardware
- Functional flow characteristics in fluid applications
- Weight-critical aerospace applications
- Precise fit requirements for gasket compression
Functional requirements may mandate small radii when CNC machined parts must interface with existing hardware or when specific flow characteristics are required in fluid applications. These functional requirements should be clearly documented and communicated during the design review process.
Alternative Solutions for Sharp Corner Requirements
Advanced manufacturing techniques offer solutions when sharp corners are essential: "Wire EDM can produce inside corners with a radius of as small as 0.05 mm, which is 'sharp' by all means" for specialized CNC machined parts applications.
Collaborative Solutions for Radius Optimization in CNC Machined Parts
The most effective radius optimization for CNC machined parts happens through early collaboration between design and manufacturing teams. Design reviews conducted before finalizing drawings can identify opportunities for radius increases that don't compromise part function.
Manufacturing feedback during the design phase often reveals alternative approaches to achieve the same functional requirements with more manufacturable geometries for CNC machined parts. This collaboration prevents costly design changes after manufacturing has begun.
Prototyping with optimized radii allows functional testing while maintaining manufacturing efficiency for CNC machined parts. This approach validates design assumptions while building parts that can transition seamlessly to production manufacturing.
Design for Manufacturability (DFM) Benefits
Research on CNC machining optimization shows that proper DFM analysis can "determine the fewest number of setups required" and reduce manual intervention for more efficient CNC machined parts production.
Quality Standards and Radius Verification for CNC Machined Parts
Corner radii verification requires appropriate inspection methods and equipment for CNC machined parts. Standard radius gauges work well for larger radii but become impractical for precise measurement of small features.
CMM inspection provides the most accurate radius measurement for CNC machined parts but requires programming time and specialized fixturing. The inspection method should be considered during the design phase to ensure compatibility with quality requirements.
Our AS9100 and ISO 9001 certified quality systems ensure consistent radius verification across all CNC machined parts, but measurement complexity increases with smaller radius specifications.
Industry Quality Standards
According to precision manufacturing standards, "the minimum internal sharp corner radius obtainable with CNC equals the radius of the cutting tool" for all CNC machined parts applications.
Making Smart Radius Decisions for CNC Machined Parts
Effective radius specification for CNC machined parts starts with understanding your actual functional requirements versus aesthetic preferences. Many radius specifications stem from visual preferences rather than functional necessities, creating unnecessary manufacturing complexity.
Decision-making framework for CNC machined parts:
- Identify true functional requirements versus preferences
- Evaluate manufacturing process implications
- Consider entire product lifecycle costs
- Validate assumptions through prototyping when critical
Consider the entire manufacturing process when specifying radii for CNC machined parts. A slightly larger radius might enable single-operation machining where a smaller radius requires multiple setups, dramatically affecting lead times and costs.
For aerospace and defense applications, understanding tolerance requirements becomes especially critical when balancing functional requirements with manufacturing capabilities.
Cost-Benefit Analysis
Manufacturing economics research emphasizes that "avoiding design features like sharp internal corners can simplify the manufacturing process and reduce machining time and costs" for CNC machined parts.
Partner with Manufacturing Experts Who Understand CNC Machined Parts Trade-offs
Modus Advanced's engineering team brings over 10% of our workforce to bear on design optimization challenges for CNC machined parts. Our engineers understand both the functional requirements driving your designs and the manufacturing realities that affect cost and lead times.
Our vertically integrated capabilities allow us to optimize radius specifications across multiple manufacturing processes simultaneously for CNC machined parts. When your part requires machining, form-in-place gasket dispensing, and assembly operations, we can balance radius requirements across all processes for optimal overall efficiency.
Working with a manufacturing partner who understands both engineering principles and production realities ensures your CNC machined parts achieve functional requirements while maintaining reasonable manufacturing timelines and costs.
For defense contractors specifically, partnering with experienced manufacturers who understand both ITAR requirements and precision machining capabilities becomes essential for mission-critical applications.
When aggressive timelines are involved, our quick-turn capabilities can accommodate urgent requirements while maintaining quality standards for complex geometries.
Our comprehensive approach to CNC machining services encompasses everything from initial design consultation through final inspection, ensuring your parts meet specifications while optimizing manufacturability.
Modus Advanced Advantage
With AS9100 and ISO 9001 certifications, our quality systems ensure every CNC machined part meets stringent aerospace and defense requirements. Our engineering-first approach means you get expert guidance from day one, helping you avoid costly design revisions and manufacturing delays.
What to expect from your manufacturing partner includes comprehensive design support, accurate quoting, and consistent quality delivery – capabilities that become especially important when dealing with precision radius requirements.
Frequently Asked Questions About CNC Machined Parts Corner Radii
What is the minimum corner radius possible in CNC machined parts?
The minimum corner radius equals the radius of the cutting tool used. A 6mm end mill creates a minimum 3mm radius in CNC machined parts.
Why do sharp corners increase costs for CNC machined parts?
Sharp corners require smaller tools, multiple passes, slower speeds, and complex programming, significantly increasing manufacturing time and costs for CNC machined parts.
Can any manufacturing process create truly sharp internal corners?
Wire EDM can achieve radii as small as 0.05mm in CNC machined parts, though this process is much slower and more expensive than conventional machining.
How do I determine the optimal corner radius for my CNC machined parts?
Start with the largest radius your design allows, then work with manufacturing engineers to balance functional requirements with production efficiency.
What's the impact of corner radius on manufacturing timeline for CNC machined parts?
Larger radii enable faster cutting speeds, fewer tool changes, and simpler programming, potentially reducing manufacturing time by 30-50% for complex CNC machined parts.