CNC Machining Design Guidelines: Five-Axis vs. Three-Axis CNC Machined Parts
July 17, 2025
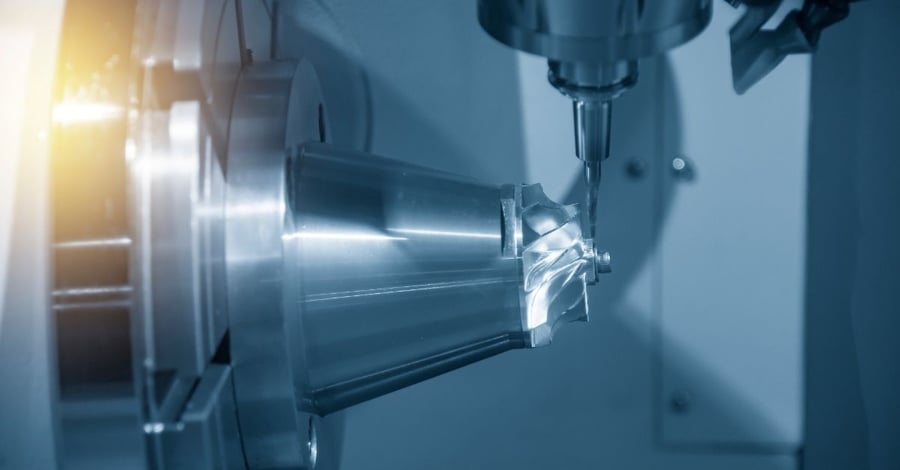
Manufactured with Speed and Precision
The manufacturing capabilities you need and the engineering support you want, all from a single partner.
Submit a DesignKey Points
- Feature alignment: Parts with features aligned to X, Y, and Z planes can be machined on three-axis equipment, while non-aligned features require five-axis capabilities
- Cost implications: Five-axis machining typically increases both lead times and costs compared to three-axis operations
- Design flexibility: Understanding axis limitations early in design prevents costly redesigns and manufacturing delays
- Complexity assessment: The number and orientation of machined surfaces directly determines manufacturing approach and timeline
- Strategic planning: Designers can optimize manufacturability by considering feature placement during initial design phases
Understanding CNC Machining Axis Systems for Optimal Design
Modern CNC machining centers operate on different axis configurations that directly impact what geometries they can produce. The distinction between three-axis and five-axis capabilities fundamentally changes how engineers should approach part design for optimal manufacturability.
Three-axis CNC machines move cutting tools along X, Y, and Z coordinates in straight-line motions. This configuration handles the majority of machining operations efficiently and cost-effectively. Five-axis machines add two rotational axes (typically A and B), allowing the cutting tool to approach the workpiece from virtually any angle.
The critical design decision centers on feature placement and orientation. When part features align with standard X, Y, and Z planes, three-axis machining provides optimal efficiency and reduces manufacturing costs.
Read the full Design for Manufacturability guide.
How Feature Alignment Determines CNC Manufacturing Approach
Feature placement drives the fundamental manufacturing strategy for any machined component. Parts designed with all critical features on surfaces that align with standard coordinate planes can utilize three-axis equipment throughout the entire machining process.
The manufacturing team evaluates each part design by analyzing which faces contain features requiring machining. Features located on the top, bottom, front, back, left, or right faces of a rectangular part envelope typically align with three-axis capabilities. Angled surfaces, compound curves, or features requiring simultaneous access from multiple directions necessitate five-axis positioning.
Consider a rectangular housing with mounting holes on the top surface and connector ports on the front face. This design allows complete machining using three-axis equipment with standard workholding and tool access. The same housing with angled connector ports or mounting features on a 30-degree chamfered surface would require five-axis capabilities.
Read the Complete Guide to CNC Machining.
Cost and Lead Time Implications of CNC Axis Selection
The choice between three-axis and five-axis machining creates significant differences in both project timeline and cost structure. Three-axis operations typically offer faster programming, shorter setup times, and lower hourly machine rates.
Five-axis machining introduces additional complexity that impacts project costs and schedules. Programming complexity increases substantially as five-axis tool paths require more sophisticated programming, increasing preparation time before machining begins. Setup requirements become more demanding when accommodating multiple tool approach angles during a single setup.
Tool selection considerations expand beyond standard end mills and drills. Five-axis operations may require specialized cutting tools with longer reach or specific geometries, potentially extending tool procurement lead times. Quality verification for five-axis parts often demands more comprehensive measurement strategies, adding inspection time to the overall project schedule.
The cost difference between three-axis and five-axis machining can be substantial, making design optimization crucial for cost-effective manufacturing.
Strategic Design Considerations for CNC Manufacturability
Engineers can significantly impact manufacturing efficiency through strategic feature placement decisions. The goal involves maximizing three-axis compatibility while maintaining design functionality and performance requirements.
Feature consolidation represents one of the most effective strategies for optimizing manufacturability. Grouping multiple features on the same face reduces the number of setups required and maintains three-axis compatibility. Surface selection plays an equally important role — placing critical features on primary orthogonal surfaces enables efficient three-axis machining.
Access planning ensures adequate tool clearance for standard end mills and drills, eliminating the need for specialized five-axis tooling. Tolerance distribution strategies that apply tight tolerances to features machined in a single setup improve accuracy while controlling costs. The engineering team should evaluate whether angled or complex features provide essential functionality or represent aesthetic preferences that increase manufacturing complexity unnecessarily.
Visit the Complete CNC Machining Resource Center.
CNC Machining Axis Comparison Analysis
Aspect | Three-Axis CNC | Five-Axis CNC |
Feature Alignment | X, Y, Z planes only | Any orientation |
Setup Complexity | Standard workholding | Advanced fixturing required |
Programming Time | Shorter preparation | Extended programming |
Tool Requirements | Standard end mills/drills | Specialized tooling possible |
Lead Time Impact | Baseline timeline | Extended timeline |
Quality Control | Standard inspection | Complex measurement protocols |
CNC Tool Requirements by Machining Configuration
Tool Category | Three-Axis Applications | Five-Axis Applications |
End Mills | Standard length, 2-4 flute | Extended reach, specialized geometry |
Drill Bits | Conventional twist drills | Angled drilling capabilities |
Cutting Speeds | Optimized for standard approach | Variable for complex angles |
Tool Changes | Minimal during operation | Frequent for angle variations |
Holder Systems | Standard CAT/BT holders | Specialized extended holders |
Inspection Tools | Basic probe systems | Multi-angle probe configurations |
Common Design Features That Drive Five-Axis Requirements
Certain geometric features consistently require five-axis machining capabilities regardless of overall part design. Understanding these features helps engineers make informed decisions about design complexity versus manufacturing efficiency.
Angled surfaces with machined features present immediate five-axis requirements. Connector housings with ports on angled faces, mounting brackets with holes on sloped surfaces, or heat sinks with angled fins typically require five-axis access. Compound curves that include spherical surfaces, complex contours, or flowing transitions between surfaces exceed three-axis capabilities completely.
Undercuts and complex pockets represent another category demanding five-axis positioning. Features that require tool access from multiple angles simultaneously, such as turbine blade profiles or complex mold cavities, cannot be completed with standard three-axis equipment. Intersecting hole patterns where holes meet at angles or require precise angular relationships often need five-axis positioning for accuracy.
The aerospace and defense industries frequently specify these complex geometries for weight reduction, aerodynamic performance, or packaging constraints. Medical device applications may require organic shapes that interface with human anatomy.
Design Guidelines for Three-Axis CNC Optimization
Systematic design practices optimize CNC machining efficiency while maintaining part functionality. These guidelines help engineers navigate the trade-offs between design complexity and manufacturing practicality.
Primary surface utilization strategies involve locating critical features on the six primary orthogonal surfaces whenever possible to maximize three-axis compatibility. Feature grouping consolidates related features on the same surface to minimize setups and maintain consistent machining approaches.
Access evaluation ensures adequate clearance for standard cutting tools and conventional workholding systems. Tolerance strategy considerations apply the tightest tolerances to features that can be machined in a single setup to optimize accuracy and efficiency. Material considerations account for material properties and machining characteristics when planning feature placement and complexity.
Practical CNC Design Implementation Guidelines
These key areas focus on implementing three-axis optimization:
- Surface orientation: Keep holes, slots, and pockets on orthogonal faces
- Feature spacing: Maintain adequate clearance for standard tooling
- Geometric simplicity: Avoid unnecessary curves and angled transitions
- Tolerance placement: Concentrate tight tolerances on single-setup features
- Material removal: Design for efficient chip evacuation and tool access
Visit our full Design for Manufacturability resource center.
Fixture and Workholding Considerations for CNC Machining
The relationship between part geometry and workholding strategy significantly impacts axis requirements. Three-axis machining relies on standard vises, clamps, and fixtures that provide rigid support while allowing tool access from above.
Five-axis operations demand more sophisticated workholding solutions. Parts must remain secure while the machine head rotates around them, accessing features from multiple angles. This requirement often necessitates custom fixture design and longer setup procedures.
Standard workholding limitations become apparent when conventional vises and clamps interfere with rotating spindle heads or extended cutting tools required for five-axis operations. Access clearance requirements mean five-axis machining requires adequate clearance around the entire part envelope to accommodate head rotation and tool movement. Rigidity maintenance challenges arise as complex workholding systems must maintain part rigidity while allowing access from multiple directions.
Engineers should consider workholding requirements during initial design phases. Simple geometric envelopes with standard clamping surfaces enable efficient three-axis workholding and reduce manufacturing complexity.
Quality Control and Inspection Implications
The axis configuration used for machining directly influences quality control procedures and inspection requirements. Three-axis operations typically produce features that align with standard coordinate measuring machine (CMM) setups and conventional inspection techniques.
Five-axis machined features often require more sophisticated measurement approaches. Angled surfaces, compound curves, and complex geometries may need specialized probe configurations or optical measurement systems. Measurement accessibility becomes challenging when features machined with five-axis equipment prove difficult to access with standard CMM probes.
Reference establishment complications arise as complex geometries can complicate the establishment of measurement datums and reference systems. Tolerance verification challenges emerge when geometric dimensioning and tolerancing (GD&T) callouts for five-axis features require advanced measurement capabilities.
Manufacturing teams must factor inspection complexity into project timelines and cost estimates. Parts with extensive five-axis features may require extended quality control procedures and specialized measurement equipment.
When Five-Axis Complexity Provides Value
Despite increased complexity and cost, five-axis machining delivers essential capabilities for specific applications. The key involves identifying when this complexity provides genuine value versus unnecessary sophistication.
Weight-critical applications in aerospace require complex geometries for weight reduction that cannot be achieved with simpler designs. Performance optimization needs for fluid flow components, heat exchangers, and aerodynamic surfaces may demand complex shapes for optimal performance. Packaging constraints in electronic enclosures and medical devices sometimes require complex geometries to fit within tight space envelopes.
Manufacturing consolidation opportunities arise when five-axis capabilities can eliminate secondary operations or assembly requirements, offsetting increased machining complexity. The decision should balance design requirements against manufacturing efficiency. Simple geometric modifications often provide equivalent functionality while enabling three-axis machining.
Strategic Evaluation Criteria for CNC Machining
Consider these factors when evaluating five-axis necessity:
- Functional necessity: Does the complex geometry provide essential performance benefits?
- Weight savings: Are the weight reductions critical to application success?
- Assembly elimination: Can five-axis features reduce part count or assembly operations?
- Performance gains: Do complex surfaces provide measurable performance improvements?
- Cost justification: Does the functional benefit justify increased manufacturing complexity?
Frequently Asked Questions About CNC Machining Design Guidelines
What is the main difference between three-axis and five-axis CNC machining?
Three-axis CNC machines move cutting tools along X, Y, and Z coordinates only, while five-axis machines add two rotational axes (A and B) for approaching workpieces from multiple angles. This difference directly affects which geometries can be efficiently machined.
How do I know if my part requires five-axis machining?
Parts with features on angled surfaces, compound curves, or complex undercuts typically require five-axis capabilities. If all features align with standard X, Y, and Z planes, three-axis machining is usually sufficient and more cost-effective.
What are the cost implications of choosing five-axis over three-axis machining?
Five-axis machining typically increases costs due to longer programming time, more complex setups, specialized tooling requirements, and extended quality control procedures compared to three-axis operations.
Can I modify my design to use three-axis machining instead of five-axis?
Often yes. Strategic feature placement, surface orientation changes, and design simplification can frequently enable three-axis compatibility while maintaining functionality.
Partner with CNC Machining Experts
Effective CNC machining design requires deep understanding of manufacturing capabilities and constraints. The Modus Advanced engineering team brings extensive experience in both three-axis and five-axis machining operations, helping customers optimize designs for efficiency and quality.
Our AS9100 and ISO 9001 certifications demonstrate our commitment to aerospace and defense quality standards. With over 10% of our staff consisting of degreed engineers, we provide comprehensive design for manufacturability reviews that identify optimization opportunities early in the development process.
Our vertically integrated capabilities include advanced CNC machining centers capable of handling both simple three-axis operations and complex five-axis requirements. This flexibility allows us to recommend the optimal manufacturing approach for each unique application.
When your design demands precision CNC machining, partner with a team that understands how feature placement drives manufacturing complexity. Contact Modus Advanced to discuss your project requirements and discover how strategic design decisions can optimize both performance and manufacturability.