Tolerance Design and Manufacturing Feasibility: Engineering Precision into Practice
July 17, 2025
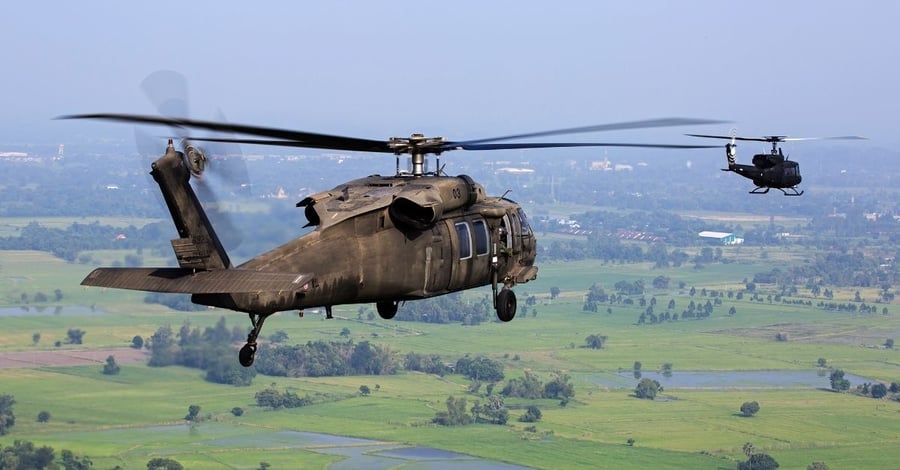
Manufactured with Speed and Precision
The manufacturing capabilities you need and the engineering support you want, all from a single partner.
Submit a DesignKey Points
- Tolerance stack-up analysis: Understanding how individual part tolerances combine to affect overall assembly performance prevents costly manufacturing delays and quality issues
- GD&T fundamentals: Geometric dimensioning and tolerancing provides a universal language for communicating design intent, but improper datum structure can create unnecessary manufacturing complexity
- Manufacturing process selection: Different manufacturing methods have inherent capability limitations — choosing the right process for your tolerance requirements optimizes both cost and lead time
- Material and geometry interactions: Part size, complexity, and material properties directly influence achievable tolerances and inspection requirements
- Quality system integration: Tolerance specification drives inspection methods, sampling plans, and overall manufacturing time — understanding this relationship is critical for project success
Understanding the Critical Connection
The relationship between design tolerances and manufacturing capabilities represents one of the most critical aspects of successful product development. Engineers often focus intensely on functional requirements while overlooking how tolerance specifications directly impact manufacturing feasibility, cost, and delivery timelines.
Understanding this relationship becomes essential when developing products for mission-critical applications. In aerospace, defense, and medical device industries, the stakes are particularly high — tolerance decisions made during design can determine whether a life-saving device reaches patients sooner or whether critical defense systems perform reliably in the field.
The Foundation of Tolerance Design
Starting with Purpose-Driven Specifications
Tolerance design begins with understanding the fundamental purpose behind each dimensional requirement. Every tolerance specification should serve a clear functional purpose rather than defaulting to arbitrary precision levels.
The most effective approach starts with tolerance stack-up analysis. This process examines how individual part tolerances accumulate across an assembly to affect overall performance. When engineers specify tolerances without considering the complete assembly, they often create impossible manufacturing scenarios or unnecessarily tight requirements that drive up costs.
Manufacturing Capability Integration
Manufacturing capability considerations must be integrated early in the tolerance design process. Different manufacturing methods have inherent precision limitations that cannot be overcome through improved tooling or process control alone. Understanding these capabilities prevents specification of unachievable requirements.
Read the full Design for Manufacturability guide.
Geometric Dimensioning and Tolerancing in Practice
GD&T as a Communication Tool
GD&T provides the standardized language for communicating design intent to manufacturing teams. However, the power of GD&T extends far beyond simple dimensional control — it enables engineers to specify exactly what matters for function while allowing manufacturing flexibility where it doesn't.
The foundation of effective GD&T implementation lies in proper datum structure. A datum establishes the reference framework from which all measurements originate. Poor datum selection creates manufacturing and inspection challenges that ripple through the entire production process.
Optimizing Datum Structure
Datum structure best practices include:
- Localized references: Position critical features relative to nearby datums rather than distant references to minimize thermal expansion and fixturing errors
- Functional alignment: Select datums that reflect how the part will be assembled and used in its final application
- Manufacturing accessibility: Ensure datum features can be reliably established during both manufacturing and inspection processes
Avoiding Common GD&T Pitfalls
Common GD&T mistakes often stem from software defaults rather than intentional design decisions. Many CAD systems automatically generate threaded hole specifications based on cut tap assumptions, while manufacturers may use roll taps that require different pre-drill sizes. This creates conflicts between drawing requirements and optimal manufacturing processes.
Read our Complete CNC Machining Guide.
Manufacturing Process Tolerance Capabilities
CNC Machining Precision Boundaries
Different manufacturing processes offer distinct tolerance capabilities that directly influence part design feasibility. Understanding these limitations enables engineers to select appropriate processes and specify realistic requirements.
CNC Machining Tolerance Factors:
Process Factor | Typical Capability | Key Considerations |
Standard machining tolerances | ±0.025mm (±0.001") | Part size and complexity dependent |
Tight tolerance machining | ±0.005mm (±0.0002") | Requires environmental controls |
Ultra-precision work | ±0.0025mm (±0.0001") | Specialized equipment and procedures |
Surface finish capability | 0.1-3.2 μm Ra | Process and tooling dependent |
Machining tolerance achievement depends heavily on part geometry and size. Large parts with tight tolerances present particular challenges due to thermal expansion, machine deflection, and fixturing limitations. Temperature control becomes critical when working with tolerances below ±0.01mm (±0.0004").
Design features that can dramatically impact machining complexity require careful consideration during the tolerance specification phase.
Form-in-Place Gasket Specifications
FIP tolerances should be defined primarily by your chosen material. Below see examples for suggested standard tolerances recommended for CHO-FORM materials as an example.
Form-in-Place (FIP) Gasket Tolerances:
CHO-FORM | Tolerance +/- | Additional Start/Stop/T-Joints |
Bead Height .018 - .034" | .004" | .006" |
Bead Height .035 -.062" | .006" | .006" |
Bead Width .022 -.040" | .006" | .006" |
Bead Width .035 -.062" | .006" | .008" |
| Max |
|
Initiation gap at wall | .030" |
|
Termination gap at wall | .060" |
|
FIP gasket tolerances follow material manufacturer recommendations, with Parker Chomerics suggesting ±0.08mm (±0.003") as the minimum practical height tolerance for single-pass dispensing. Tighter tolerances significantly increase inspection time and manufacturing complexity.
Understanding key design considerations for successful form-in-place gasket implementation helps engineers specify appropriate tolerances that balance functional requirements with manufacturing capability.
Read our Complete Form-in-Place Gasket Guide.
Converting Process Standards
Converting processes for elastomeric materials follow American Rubber Converter Association (ARCA) standards. These standards establish tolerance ranges based on material thickness and part geometry complexity.
The key consideration for converted parts lies in understanding that complex geometries combined with tight tolerances create exponential manufacturing difficulty. Simple rectangular cuts can achieve much tighter tolerances than intricate curved profiles.
Setting tolerances for elastomeric materials requires understanding material behavior and manufacturing process limitations.
Die Cut, Water Jet, CNC Knife Tolerances
Imperial (Inches) Tolerance Table
Dimension Range | Film (BL1) | Solid or Dense (BL2) | Sponge or Foam (BL3) |
---|---|---|---|
For thicknesses up to 0.25" | |||
Under 1.0" | ±0.010" | ±0.015" | ±0.025" |
1.0" to 6.3" | ±0.015" | ±0.025" | ±0.032" |
Over 6.3" | Multiply by 0.004 | Multiply by 0.01 | Multiply by 0.0063 |
For thicknesses from 0.25" to 0.50" | |||
Under 1.0" | N/A | ±0.030" | ±0.040" |
1.0" to 6.3" | N/A | ±0.040" | ±0.050" |
Over 6.3" | N/A | Multiply by 0.005 | Multiply by 0.0063 |
For thickness over 0.50" | |||
Under 1.0" | N/A | N/A | ±0.050" |
1.0" to 6.3" | N/A | N/A | ±0.070" |
Over 6.3" | N/A | N/A | Multiply by 0.01 |
Metric (Millimeters) Tolerance Table
Dimension Range | Film (BL1) | Solid or Dense (BL2) | Sponge or Foam (BL3) |
---|---|---|---|
For thicknesses up to 6.3mm | |||
Under 25mm | ±0.25mm | ±0.38mm | ±0.63mm |
25mm to 160mm | ±0.38mm | ±0.63mm | ±0.81mm |
Over 160mm | Multiply by 0.004 | Multiply by 0.01 | Multiply by 0.0063 |
For thicknesses from 6.3mm to 12.7mm | |||
Under 25mm | N/A | ±0.76mm | ±1.02mm |
25mm to 160mm | N/A | ±1.02mm | ±1.27mm |
Over 160mm | N/A | Multiply by 0.005 | Multiply by 0.0063 |
For thickness over 12.7mm | |||
Under 25mm | N/A | N/A | ±1.27mm |
25mm to 160mm | N/A | N/A | ±1.78mm |
Over 160mm | N/A | N/A | Multiply by 0.01 |
Material Classification Notes
- Film (BL1): Thin, flexible sheet materials
Solid or Dense (BL2): Dense rubber and similar solid materials
Sponge or Foam (BL3): Cellular and foam materials
Important Considerations:
The "dish effect" becomes more pronounced as material thickness increases during die-cutting operations. This concavity of die-cut edges results from the compression force of the cutting die, causing the width (or length) at the top and bottom surfaces to be slightly greater than the width at the center.
Read our Custom Gasket Production Guide.
Design Features That Impact Manufacturing Feasibility
Common Machining Challenges
Specific design features consistently create manufacturing challenges across different processes. Understanding these common issues enables engineers to make informed decisions about when such features are truly necessary.
Problematic machining features include sharp internal corners, which are physically impossible to create with rotary cutting tools. All internal corners require radii, and larger radii significantly reduce manufacturing time by allowing larger cutting tools and faster machining operations.
Complex Geometry Considerations
Complex curvature presents another common challenge. Parts designed for eventual casting often include draft angles and complex filleted surfaces that dramatically increase machining time when prototypes must be machined. Understanding when casting meets machining optimizes both processes.
Five-axis machining requirements arise when part features don't align with standard X, Y, and Z planes. While five-axis capability provides tremendous design flexibility, it also increases setup time, programming complexity, and overall manufacturing cost.
FIP Gasket Design Optimization
FIP gasket design considerations center on dispense path optimization. Multiple gasket lines converging in small areas create "blob" formations that compromise sealing effectiveness. Similarly, gasket paths in deep pockets require extended-reach needles that can complicate dispensing with particle-filled materials.
Comprehensive FIP dispensing design guidelines help engineers optimize both function and manufacturability.
Quality Requirements and Manufacturing Impact
Inspection Strategy Decisions
Quality specifications often drive manufacturing time more significantly than part complexity itself. Understanding how different quality requirements translate to manufacturing processes helps engineers balance functional needs with practical constraints.
Inspection sampling plans represent a critical decision point. One hundred percent inspection versus statistical sampling can change manufacturing timelines by orders of magnitude. Space industry customers frequently require 100% inspection, while other industries may accept statistical sampling approaches.
Building robust quality systems that support both functional requirements and manufacturing efficiency requires careful consideration of inspection strategies.
Surface Finish and Adhesion Interactions
Surface finish specifications create particular challenges when combined with FIP gasket applications. Extremely smooth surfaces can compromise gasket adhesion, requiring design modifications like scribe lines or textured areas to ensure proper bonding.
Tolerance verification methods also impact manufacturing feasibility. Profile tolerances require complete surface scanning, while simple dimensional checks can be performed much more quickly. The inspection method specified on drawings directly determines quality control time and cost.
Understanding how quality requirements determine lead times and costs enables engineers to make informed decisions about specification levels.
Visit our full Design for Manufacturability resource center.
Optimizing Tolerance Design for Manufacturing Success
Material and Process Selection
Successful tolerance design requires balancing functional requirements with manufacturing realities. The most effective approach involves early collaboration between design and manufacturing teams to identify optimal solutions.
Material selection impacts extend beyond basic properties to include tolerance capability. Some materials machine to tighter tolerances than others, while certain elastomers provide better dimensional stability for converted parts.
Optimizing converted parts and custom gaskets for manufacturing requires understanding material and tolerance interactions.
Assembly and Process Considerations
Assembly considerations often drive the tightest tolerance requirements. Understanding how parts mate and function together enables engineers to specify tight tolerances only where truly necessary for assembly success.
Process sequence optimization can significantly improve tolerance achievement. Operations performed in specific orders, material stress relief requirements, and thermal considerations all influence final part accuracy.
Cost reduction strategies through design decisions help engineers balance functional requirements with manufacturing efficiency.
Engineering Manufacturing Success
The Optimization Approach
Tolerance design represents a critical intersection between engineering function and manufacturing reality. Success requires understanding both the functional requirements driving tolerance needs and the manufacturing capabilities available to achieve them.
The most effective approach treats tolerance specification as an engineering optimization problem. Each tolerance should serve a clear functional purpose, reflect manufacturing capabilities, and consider the complete assembly context.
Understanding why tighter tolerances aren't always better helps engineers make more informed specification decisions.
Partnership for Success
When engineers partner with manufacturing teams early in the design process, they create opportunities to optimize both function and manufacturability. This collaboration enables faster development cycles, reduced costs, and more reliable production outcomes.
At Modus Advanced, our engineering team works directly with customers during the design phase to ensure tolerance specifications align with manufacturing capabilities. With AS9100 and ISO 9001 certifications, plus ITAR compliance for defense applications, we understand the quality requirements across critical industries while maintaining focus on practical manufacturability.
The result is parts that not only meet functional requirements but can be manufactured consistently, efficiently, and with confidence. Because when lives depend on your innovation, tolerance design becomes more than an engineering exercise — it becomes a commitment to reliability and performance.