Mastering Form-in-Place (FIP) Gasket Design: A Comprehensive Guide
October 23, 2024
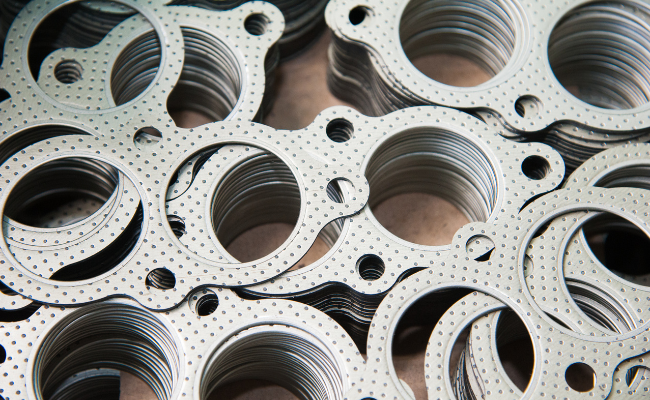
Manufactured with Speed and Precision
The manufacturing capabilities you need and the engineering support you want, all from a single partner.
Submit a DesignKey Points
- Superior Customization: Form-in-Place (FIP) gaskets offer superior customization and precision for complex designs, with benefits including no assembly needed, excellent positioning tolerances, and minimal scrap material.
- Critical Material Selection: Material selection is critical for FIP gasket design, with considerations including electrical conductivity, environmental factors, and the choice between conductive and non-conductive materials like nickel graphite-filled silicone.
- Proper Housing Design: Proper metal housing design is crucial for FIP gasket performance, including considerations for wall dimensions, surface flatness, and the use of compression stops instead of grooves.
- Partner With Experts: Partner with Modus Advanced for expert FIP gasket design and manufacturing, leveraging their vertically integrated capabilities to streamline your supply chain and reduce lead times from prototype to production.
In the world of engineering and manufacturing, the seemingly small details often make the biggest difference. One such detail that plays a crucial role in many products is the gasket - specifically, the Form-in-Place (FIP) gasket. This guide will walk you through the intricacies of FIP gasket design, helping you create more effective, efficient, and reliable products.
Everything you've ever wanted to know about FIP Gaskets - here!
Understanding FIP Gaskets
Form-in-Place gaskets are a modern solution to the age-old problem of sealing and protecting components. Unlike traditional pre-formed gaskets, FIP gaskets are applied directly onto the part as a liquid, which then cures in place to form a perfect seal. This method offers superior customization and precision, making it ideal for complex designs and high-performance applications.
Key Benefits of FIP Gaskets
- No assembly needed
- Superior flexibility to close any gap
- Allows for compartmentalized shielding
- Minimal scrap material
- Excellent positioning tolerances
- Can replace wire mesh, molded-in-place, or die-cut gaskets
Material Selection: The Foundation of Good Design
The heart of any FIP gasket is its material. Choosing the right material is not just important - it's critical to the success of your design. Here are some key considerations:
Electrical Conductivity
For applications requiring EMI shielding, electrically conductive gaskets are essential. These materials require precise compression to function correctly. It's crucial to ensure your design can apply the exact compression force specified for the material. Too little pressure, and you lose conductivity; too much, and you risk damaging the gasket or the components it's meant to protect.
Environmental Factors
Consider the environment in which your product will operate. Temperature extremes, chemical exposure, and moisture levels can all affect gasket performance. Some materials excel in high-temperature environments, while others offer superior chemical resistance. Match your material choice to your product's operational conditions.
Conductive vs. Non-Conductive Materials
Advancements in technology have led to a wide range of materials for FIP gaskets, including:
- Conductive and non-conductive silicone compounds
- Fluorosilicone compounds
These materials offer resistance to heat, cold, moisture, UV, ozone, galvanic corrosion, and pressure. For EMI/RFI shielding, electrically conductive fillers such as silver, copper, nickel, aluminum, ferrite, and graphite particles can be added.
Spotlight on Nickel Graphite vs. Silver
While silver-aluminum has been a popular filler for shielding silicones, the fluctuating price of silver has made it less cost-effective. Nickel graphite filled silicone has emerged as an excellent alternative:
- Performs at shielding levels comparable to silver-aluminum filled products
- Significantly more cost-effective
- Meets stringent U.S. Military requirements
- Excellent salt spray and corrosion resistance properties
- Suitable for commercial applications in medical, automotive, and wireless technology sectors
Designing the Metal Housing
The design of the metal housing onto which the FIP gasket will be applied is just as crucial as the gasket itself. A well-designed housing ensures consistent gasket application and performance.
Wall Dimensions and Gasket Width
The width of the walls or flanges where the gasket will be applied is a critical factor. Narrower walls make dispensing more challenging and can affect gasket integrity. As a general rule, the wall should be at least 0.4 mm wider than the intended gasket width.
Preventing Gasket Overflow
Avoiding gasket overflow is crucial to prevent problems with circuitry and avoid longer lead and inspection times. If the housing's wall thickness doesn't match the width of the dispensed gasket, the fluid can spill over into the cavity, potentially causing shorting issues.
Design recommendations for metal housing:
- Aim for wider walls when possible
- Minimum recommended wall thickness:
- 0.8mm for metal
- 1.5mm for plastics
- Maintain consistent wall thickness to ensure easier and more centered gasket dispensing
Visit Our Complete Form-in-Place Gasket Resource Center
Surface Flatness
The flatness of the surface where the gasket will be applied is crucial for maintaining consistent gasket height and width. Aim for part-to-part flatness reproducibility within 0.4 mm. Avoid dispensing on curved surfaces or in grooves, as these can lead to inconsistent gasket dimensions.
Compression Stops vs. Grooves
Traditionally, many designs incorporated grooves for gasket placement. However, for FIP gaskets, compression stops are often a better choice:
Why Avoid Grooves?
- In narrow grooves, the dispensed fluid may contact the groove wall, causing the gasket to cure asymmetrically.
- This can lead to inconsistent compression forces and potentially ineffective sealing.
- Grooves can complicate the dispensing process and increase the risk of errors.
Benefits of Compression Stops
- Allow for more precise control of gasket height and compression
- Reduce the risk of asymmetrical curing
- Simplify the dispensing process
- Can be more cost-effective in terms of design and manufacturing
Compression stops are particularly vital when dealing with materials sensitive to overcompression. These stops prevent gasket rupture by limiting the maximum compression applied to the gasket.
Different materials have different compression tolerances to keep in mind, for instance:
- Nolato TriShield recommends a compression between 10% and 50%, with an ideal range of 20-30%.
- Parker Chomerics materials have varying compression ranges based on the specific product line.
Always include compression stops when there's a risk of exceeding the material's maximum compression limit.
Related: Design Considerations for Machined Parts
Get 13 design tips for your metal housing, ensuring the best adherence and performance for any FIP materials applied to them.
Learn MoreDeep Dive: 6 Tips for Designing a Form-in-Place EMI Gasket
Discover six proven engineering tips for designing form-in-place EMI gaskets that enhance electromagnetic shielding performance while reducing manufacturing complexity and production time.
Learn MoreThe Dispensing Process: Ensuring Precision
The actual process of dispensing the FIP gasket requires careful consideration of several factors:
Part Positioning
Accurate and repeatable positioning of the part during dispensing is crucial. Consider incorporating features like:
- Through-holes for pin positioners
- Well-defined corners without gate marks for guiding
- Vacuum hold-down capabilities in your fixture design
Dimensional Reproducibility
Consistency is key in FIP gasket application. Aim for:
- X and Y dimensions reproducible within 0.2 mm
- Z dimension (flatness) reproducible within 0.4 mm
Dispensing Path Considerations
The path along which the gasket will be dispensed needs careful planning:
- Avoid dispensing on surfaces angled more than 45 degrees from horizontal
- Maintain a minimum clearance of 0.25 mm between the gasket and any obstructions
- Try to avoid short gasket segments with open ends, as these can lead to height inconsistencies
Tolerances and Quality Control
As with any precision component, tolerances are critical in FIP gasket design. Here are some key specifications to consider:
- Height Tolerances:
- < 1mm: ±0.10mm
- 1-1.5mm: ±0.15mm
- 1.5mm: +0.25mm, -0.15mm
- Adhesion: Typically specified as a minimum of 0.6 N/mm² in shear force
- Electrical Resistance (for conductive gaskets):
- Ni/Sn surface: max 50 mohm
- Al or passivated Al surface: 200-600 mohm
Consistently monitoring these parameters ensures a stable and reliable production process when it comes to FIP dispensing.
Streamlining the Supply Chain
One of the most significant advantages of FIP gaskets is the potential for a streamlined supply chain. By working with a "one-stop shop" custom manufacturer, you can:
- Submit your design
- Have housing precisely machined
- Have FIP gaskets meticulously applied
- Receive completed parts ready for use
This approach eliminates multiple shipping steps, reduces packaging and labor costs, minimizes quality control issues from excessive handling, and simplifies inventory management.
Design Checklist: Your Path to Success
Before finalizing your FIP gasket design, run through this checklist to ensure you've covered all bases:
- Material Selection: Have you chosen the most appropriate material for your application?
- Wall Design: Are your walls wide enough to accommodate the gasket without overflow?
- Compression Control: Have you incorporated compression stops instead of grooves?
- Part Positioning: Can the part be precisely positioned in the dispensing fixture?
- Dimensional Reproducibility: Are X, Y, and Z dimensions consistently reproducible within tolerance?
- Surface Flatness: Is the dispensing surface flat and free of obstructions?
- Dispensing Path: Have you eliminated dispensing in problematic areas like highly sloped surfaces?
- Clearance: Is there sufficient clearance around the dispensing path?
- Material Considerations: Have you accounted for any ferromagnetic materials that could interfere with gasket formation?
- Quality Control: Are your tolerance specifications clear and measurable?
- Supply Chain: Have you considered working with a "one-stop shop" manufacturer?
Bringing It All Together
Why Choose Modus Advanced for Your FIP Gasket Dispensing?
At Modus Advanced, we've mastered the art and science of FIP gasket dispensing while offering a complete manufacturing ecosystem that accelerates your path to market. Our engineering-first approach means your critical components receive expert attention at every stage.
With Modus, you gain:
- Vertical integration that eliminates shipping between vendors and reduces lead times
- Concurrent manufacturing processes including machining, plating, and thermal material application
- Engineering expertise with over 10% of our staff being engineers who understand your technical challenges
- Enhanced quality control through a single quality system governing the entire process
- Simplified communication with one partner instead of multiple vendors
When one day matters—and we believe it does—our vertically integrated approach doesn't just save time; it helps your innovations reach the field faster, whether that's life-saving medical devices or mission-critical defense systems.
FIP Dispensing ServicesDesigning an effective FIP gasket system requires a holistic approach. From material selection to housing design, each element plays a crucial role in the final performance of your product. By carefully considering each aspect outlined in this guide, you'll be well on your way to creating a robust, reliable sealing solution.
Remember, the key to success lies in the details. Don't hesitate to consult with material suppliers and dispensing experts early in your design process. Their expertise can help you avoid common pitfalls and optimize your design for manufacturability and performance.
As technology continues to advance, FIP gaskets are likely to play an even more significant role in product design across various industries. By mastering the art and science of FIP gasket design now, you're not just solving today's engineering challenges - you're preparing for the innovations of tomorrow.
Whether you're working on consumer electronics, automotive components, or industrial machinery, the principles outlined in this guide will help you create better, more reliable products. So, take these insights, apply them to your next design project, and watch as your FIP gaskets seal the deal on your product's success.