Design for Manufacturability in Rapid Prototyping: Engineering Your Path from Concept to Production
July 17, 2025
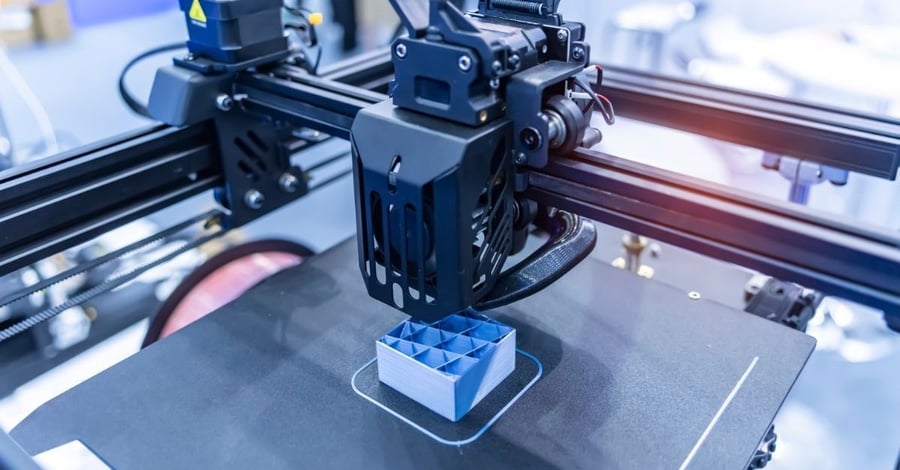
Manufactured with Speed and Precision
The manufacturing capabilities you need and the engineering support you want, all from a single partner.
Submit a DesignKey Points
- Material selection drives manufacturing process: Choose materials that align with both prototype requirements and intended production methods to avoid costly redesigns later
- Tolerance specifications impact lead times exponentially: Overly tight tolerances during prototyping can extend lead times unnecessarily when functional requirements don't demand precision
- Geometry simplification accelerates iteration cycles: Complex curves and features that look impressive in CAD often translate to weeks of additional machining time without functional benefit
- Surface finish affects downstream processes: Consider how prototype surface treatments will impact form-in-place gasket adhesion and other assembly operations
- Production scalability requires parallel design paths: Create separate design variants for prototyping and production manufacturing to optimize each phase appropriately
When Speed Meets Precision: The Prototyping Challenge
Rapid prototyping represents one of the most critical phases in product development, where engineering teams race against time to validate concepts while laying the groundwork for scalable production. The design decisions made during this phase ripple through every subsequent stage of manufacturing, making design for manufacturability (DFM) principles essential from day one.
Engineers often face a fundamental tension during prototyping: the need for speed versus the requirement for precision. This challenge becomes particularly acute when working with life-saving medical devices or mission-critical aerospace components, where prototype validation must happen quickly without compromising the quality standards that will define the final product.
Machining Considerations for Prototype Development
The Over-Engineering Trap
One of the most common challenges in rapid prototyping stems from engineers designing parts that look exceptional in CAD software but create significant manufacturing complexity. Complex curvature and ornate features often serve no functional purpose in prototype validation yet can multiply machining time significantly.
The aerospace industry frequently encounters this challenge when engineers design parts optimized for future casting operations but need machined prototypes immediately. These designs typically include draft angles of one degree on every face — a feature that facilitates casting but creates substantial machining complexity during the prototype phase.
Common over-engineering issues include:
- Excessive curvature: Multiple radius variations that require frequent tool changes and extended programming time
- Unnecessary draft angles: Features designed for casting that complicate machining operations
- Aesthetic refinements: Visual enhancements that provide no functional benefit during prototype validation
- Feature density: Too many design elements concentrated in small areas, increasing setup complexity
Geometry Optimization Guidelines
Smart geometry choices during the design phase can dramatically reduce prototype lead times while maintaining functional performance. Engineers should focus on features that support validation objectives rather than final production aesthetics.
Key optimization strategies include:
- Radius standardization: Use consistent radius sizes throughout the design to minimize tool changes
- Feature alignment: Orient features along standard X, Y, and Z planes to avoid five-axis machining requirements
- Wall thickness: Maintain adequate wall sections to prevent part distortion during machining operations
- Access clearance: Ensure sufficient clearance around features for standard tooling access
Design Feature | Prototype-Friendly Approach | Production Consideration |
Internal corners | 1.5mm (0.06") minimum radius | Optimize for final manufacturing method |
Wall thickness | 3mm (0.12") minimum for stability | Adjust for material and loading requirements |
Feature spacing | 5mm (0.20") minimum separation | Consider assembly and maintenance access |
Draft angles | Eliminate unless functionally required | Add for production casting operations |
Tolerance Strategy for Rapid Iteration
Tolerance specifications during prototyping should reflect functional requirements rather than production capabilities. Overly tight tolerances extend machining time exponentially while rarely providing additional validation value.
Recommended tolerance approaches:
- Functional zones: Apply tight tolerances only to critical mating surfaces and functional features
- Non-critical areas: Use standard machining tolerances (±0.1mm or ±0.004") for non-functional surfaces
- Assembly interfaces: Focus precision on features that affect part assembly and testing
- Future refinement: Plan tolerance tightening during production design optimization
Tolerance Range | Machining Impact | Prototype Application |
±0.05mm (±0.002") | Requires precision setups | Critical functional features only |
±0.1mm (±0.004") | Standard machining capability | General dimensional control |
±0.2mm (±0.008") | Efficient production | Non-critical features |
Read our Complete CNC Machining Guide.
Form-in-Place Gasket Integration
Dispensing Design Principles
Form-in-place (FIP) gasket applications during prototyping require careful consideration of dispensing complexity and material behavior. Poor dispensing path design can create manufacturing challenges that delay prototype delivery and compromise sealing performance.
Critical design considerations include:
- Path convergence: Avoid multiple gasket lines meeting at single points to prevent material blob formation
- Dispensing accessibility: Maintain adequate clearance for needle access, especially in deep pockets
- Start/stop locations: Position gasket endpoints in areas that support consistent bead formation
- Material compatibility: Consider how gasket materials interact with substrate surface finishes
Extended Reach Limitations
Gasket dispensing in deep pockets or recessed areas presents additional complexity during prototype development. Operations requiring needle reach beyond 6mm (0.25") demand specialized techniques that can affect quality and consistency.
Design solutions for accessibility challenges:
- Pocket depth reduction: Minimize recess depth to improve dispensing access
- Alternative routing: Provide dispensing access from multiple angles when possible
- Material selection: Choose less viscous materials for deep-reach applications
- Fixture design: Plan for specialized holding fixtures that improve access angles
Understanding successful form-in-place gasket design principles early in prototyping ensures smooth transitions to production dispensing operations.
Pocket Depth | Dispensing Complexity | Recommended Approach |
<6mm (0.25") | Standard operations | Normal dispensing procedures |
6-15mm (0.25"-0.6") | Increased complexity | Longer needles, material evaluation |
>15mm (\>0.6") | Specialized techniques | Design modification recommended |
Read our Complete Form-in-Place Gasket Guide.
Converting and Assembly Considerations
Tolerance Standards for Elastomeric Materials
Converted parts in prototype applications often receive tolerance specifications derived from machining standards, creating unnecessary complexity and cost. Elastomeric materials behave differently than metals, requiring material-appropriate tolerance specifications.
Industry-standard tolerance guidelines:
- Thickness variations: Follow American Rubber Converter Association standards based on material thickness
- Linear dimensions: Account for material compression and recovery characteristics
- Complex geometry: Prioritize overall dimensional control over detailed feature precision
- Functional requirements: Focus tolerances on sealing surfaces and critical interfaces
Die Cut, Water Jet, CNC Knife Tolerances
Imperial (Inches) Tolerance Table
Dimension Range | Film (BL1) | Solid or Dense (BL2) | Sponge or Foam (BL3) |
---|---|---|---|
For thicknesses up to 0.25" | |||
Under 1.0" | ±0.010" | ±0.015" | ±0.025" |
1.0" to 6.3" | ±0.015" | ±0.025" | ±0.032" |
Over 6.3" | Multiply by 0.004 | Multiply by 0.01 | Multiply by 0.0063 |
For thicknesses from 0.25" to 0.50" | |||
Under 1.0" | N/A | ±0.030" | ±0.040" |
1.0" to 6.3" | N/A | ±0.040" | ±0.050" |
Over 6.3" | N/A | Multiply by 0.005 | Multiply by 0.0063 |
For thickness over 0.50" | |||
Under 1.0" | N/A | N/A | ±0.050" |
1.0" to 6.3" | N/A | N/A | ±0.070" |
Over 6.3" | N/A | N/A | Multiply by 0.01 |
Metric (Millimeters) Tolerance Table
Dimension Range | Film (BL1) | Solid or Dense (BL2) | Sponge or Foam (BL3) |
---|---|---|---|
For thicknesses up to 6.3mm | |||
Under 25mm | ±0.25mm | ±0.38mm | ±0.63mm |
25mm to 160mm | ±0.38mm | ±0.63mm | ±0.81mm |
Over 160mm | Multiply by 0.004 | Multiply by 0.01 | Multiply by 0.0063 |
For thicknesses from 6.3mm to 12.7mm | |||
Under 25mm | N/A | ±0.76mm | ±1.02mm |
25mm to 160mm | N/A | ±1.02mm | ±1.27mm |
Over 160mm | N/A | Multiply by 0.005 | Multiply by 0.0063 |
For thickness over 12.7mm | |||
Under 25mm | N/A | N/A | ±1.27mm |
25mm to 160mm | N/A | N/A | ±1.78mm |
Over 160mm | N/A | N/A | Multiply by 0.01 |
Read our Custom Gasket Production Guide.
Assembly Process Optimization
Assembly operations during prototyping can reveal design issues that affect production scalability. Engineers should consider assembly complexity during the design phase to prevent late-stage modifications.
Assembly optimization strategies include:
- Component accessibility: Ensure adequate clearance for assembly tooling and procedures
- Tolerance stack-up: Verify that combined tolerances support reliable assembly operations
- Material handling: Consider component fragility and handling requirements during assembly
- Adhesive applications: Plan for pressure-sensitive adhesive (PSA) placement and curing requirements
Adhesive selection considerations:
- Tack level: Match adhesive properties to assembly procedure requirements
- Curing method: Consider room temperature versus thermal curing based on prototype schedule
- Removability: Plan for disassembly requirements during prototype testing phases
- Surface preparation: Ensure substrate compatibility with selected adhesive systems
Production Scalability Planning
Parallel Design Development Strategy
Successful rapid prototyping often requires creating separate design variants optimized for different manufacturing methods. This approach enables faster prototype iterations while maintaining clear production pathways.
Development track considerations:
- Prototype optimization: Design specifically for rapid manufacturing methods and materials
- Production preparation: Maintain parallel designs optimized for high-volume manufacturing
- Feature translation: Plan how prototype features will translate to production manufacturing methods
- Material transitions: Consider how material changes will affect design requirements
When working with custom molded rubber parts, understanding the best prototyping approaches can significantly impact development timelines.
Manufacturing Method | Prototype Advantages | Production Considerations |
CNC Machining | Fast iteration, design flexibility | Higher per-unit costs at volume |
Die Cutting | Quick turnaround for soft materials | Tooling investment for production |
Waterjet Cutting | Material versatility, no tooling | Slower cycle times for volume |
Form-in-Place Dispensing | Complex geometries, no tooling | Material cost optimization needed |
Quality Requirements and Lead Time Impact
Inspection Strategy Development
Quality requirements specified during prototyping often carry forward into production, making early specification decisions critical for long-term success. Strategic inspection planning balances validation needs with prototype schedule requirements.
Inspection optimization approaches:
- Functional focus: Prioritize inspection of features critical to prototype validation objectives
- Sampling strategies: Use statistical sampling rather than 100% inspection when appropriate
- Documentation levels: Match documentation requirements to prototype phase objectives
- Measurement accessibility: Ensure specified features can be efficiently measured with available equipment
Critical quality decisions:
- Geometric dimensioning and tolerancing (GD&T): Apply only where functional requirements demand precision
- Surface finish specifications: Focus on areas affecting subsequent operations or performance
- Material certifications: Match certification requirements to prototype validation needs
- Traceability requirements: Plan documentation levels appropriate to prototype phase
Visit our full Design for Manufacturability resource center.
Engineering Partnership for Prototype Success
Successful rapid prototyping requires close collaboration between design teams and manufacturing partners throughout the development process. Early manufacturing engagement enables design optimization that prevents costly iterations while maintaining aggressive prototype schedules.
Understanding the broader cost reduction strategies available through strategic design choices helps optimize both prototype and production phases.
Modus Advanced's engineering team — representing more than 10% of our staff — provides dedicated design for manufacturability support during prototype development. Our AS9100 and ISO 9001 certifications ensure quality systems that support both rapid prototyping requirements and production scalability planning.
Our vertically integrated capabilities enable concurrent prototype development across multiple manufacturing processes, reducing lead times while providing comprehensive design feedback that accelerates the path from concept to production-ready designs.