The Hidden Cost of Tight Tolerance: Why 'Tighter' Isn't Always Better in Manufacturing
July 17, 2025
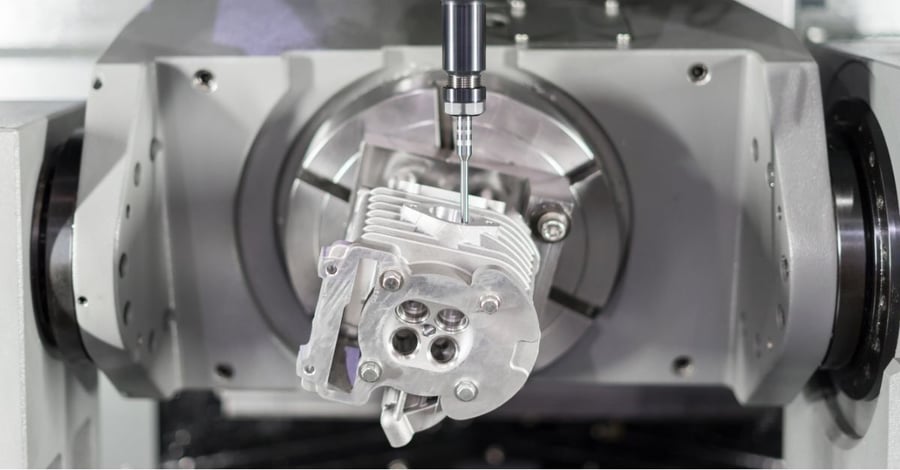
Manufactured with Speed and Precision
The manufacturing capabilities you need and the engineering support you want, all from a single partner.
Submit a DesignKey Points
- Cost Impact: Engineers often default to the tightest tolerances possible, but this approach can significantly increase manufacturing costs and lead times without improving functionality across both machined and converted parts
- Process Understanding: Understanding when precision matters — and when it's overkill — is crucial for efficient design for manufacturability in all manufacturing processes
- Material Standards: Converted parts follow different tolerance standards than machined components, with material type being the primary factor in achievable accuracy
- Design Optimization: Proper datum structure, realistic tolerance specifications, and clear drawing requirements can reduce manufacturing complexity while maintaining part performance
- Value Engineering: The most expensive tolerance is often the one that doesn't add functional value to your design
- Economic Reality: Tight tolerance manufacturing typically costs 2-24 times more than standard tolerances for machined parts, while converted parts may require 30% material overproduction
What Makes Tolerance Specification So Critical?
Tight tolerance refers to extremely precise dimensional requirements in manufacturing, but the definition varies significantly between machining and converting processes. The relationship between tolerance and manufacturing complexity isn't linear — it's exponential.
- For machined parts: Tight tolerance typically means ±0.05 mm (±0.002 inches) or smaller deviations from nominal dimensions. In precision machining applications, tight tolerance can extend to micron-level accuracy of ±0.025 mm (±0.001 inches) or even sub-micron levels for specialized components.
- For converted parts: Tight tolerance requirements depend heavily on material type and manufacturing process. Film materials might achieve ±0.25 mm (±0.010") under standard conditions, while foam materials typically require ±0.63 mm (±0.025") or looser tolerances due to material compression during cutting.
Precision feels like progress. When engineers specify tight tolerances, there's an inherent sense that tighter equals better — more professional, more precise, more reliable.
But here's the manufacturing reality: that 0.025 mm (0.001 inch) tolerance you just specified on a machined housing might have doubled your part cost and tripled your lead time. Similarly, specifying ±0.13 mm (±0.005") tolerance on a foam gasket when the material naturally achieves ±0.63 mm (±0.025") creates unnecessary material waste and production complexity.
Understanding this relationship across different manufacturing processes, and knowing when precision matters versus when it's engineering overkill, can transform your approach to design for manufacturability.
Read the full Design for Manufacturability guide.
When Precision Becomes Punishment
Tight tolerances don't just make parts more expensive. They fundamentally change how parts must be manufactured, inspected, and validated — regardless of whether you're machining metal components or converting rubber gaskets.
The Machined Parts Tolerance Challenge
Consider a seemingly simple machined housing with a 0.1 mm (0.004 inch) flatness requirement. Standard manufacturing processes can typically achieve this without significant difficulty.
But specify 0.025 mm (0.001 inch) flatness on that same surface, and suddenly you're entering precision manufacturing territory. The manufacturing process now requires temperature-controlled environments, thermal stabilization of machine tools, and specialized inspection routines.
Lead times extend as the machining process becomes iterative — cut, measure, adjust, repeat. Quality control transforms from standard inspection to comprehensive measurement protocols.
This exponential relationship affects every aspect of production:
- Setup Complexity: Fixture and tooling precision requirements increase dramatically
- Machine Requirements: Standard equipment may no longer be sufficient for required accuracy
- Environmental Controls: Temperature and vibration control become critical factors
- Inspection Protocols: Measurement uncertainty must be managed relative to tolerance bands
Even material handling requires additional care to prevent damage that could affect critical dimensions.
Read our Complete CNC Machining Guide.
The Converted Parts Reality
For converted parts like custom gaskets and seals, the tolerance challenge manifests differently but with equally significant cost implications. Converting processes cut sheet materials using waterjet, die cutting, or CNC knife systems, each with specific tolerance capabilities.
When engineers specify tolerances tighter than machine capabilities, manufacturers must produce additional parts to achieve statistical compliance. A waterjet system capable of ±0.13 mm (±0.005") tolerance struggles with ±0.10 mm (±0.004") specifications, requiring approximately 30% material overproduction to ensure adequate good parts for delivery.
Manufacturing costs increase exponentially with tighter tolerances. Moving from rough machining tolerances (0.76 mm/0.030 inches) to precision tolerances (0.025 mm/0.001 inch) increases costs by approximately 4x, while ultra-precision tolerances (0.0025 mm/0.0001 inch) can cost 24 times more than standard machining.
For converted parts, the cost relationship follows material type and process limitations rather than pure dimensional accuracy, but the exponential nature remains consistent.
Read our Custom Gasket Production Guide.
Understanding Material-Specific Tolerance Standards
Unlike machined parts where tolerance capabilities depend primarily on machine precision and setup procedures, converted parts tolerance achievability depends heavily on material properties and cutting process selection. The Rubber Manufacturers Association (RMA) provides industry-standard tolerance guidelines that reflect real-world manufacturing capabilities.
These standards reflect material behavior during cutting processes. Foam materials compress during cutting, affecting final dimensions and requiring looser tolerances. Film materials maintain dimensional stability but present handling challenges that affect achievable accuracy.
Understanding these material-specific standards prevents engineers from applying machining tolerances to converted parts, where such specifications may be impossible to achieve cost-effectively.
RMA Standard Tolerance Guidelines
Material Classification | Under 25 mm (1.0") | 25-160 mm (1.0"-6.3") | Over 160 mm (6.3") |
---|---|---|---|
Film Materials (BL1) | ±0.25 mm (±0.010") | ±0.38 mm (±0.015") | Multiply by 0.004 |
Solid/Dense (BL2) | ±0.38 mm (±0.015") | ±0.63 mm (±0.025") | Multiply by 0.01 |
Sponge/Foam (BL3) | ±0.63 mm (±0.025") | ±0.81 mm (±0.032") | Multiply by 0.0063 |
Process-Specific Capabilities
Different converting processes offer varying tolerance capabilities based on cutting mechanism and material interaction:
Process | Typical Tolerance Range | Material Limitations | Setup Complexity |
---|---|---|---|
Die Cutting | ±0.13-0.51 mm (±0.005"-0.020") | Thickness dependent | Low for high volume |
Waterjet Cutting | ±0.08-0.13 mm (±0.003"-0.005") | Some thin films challenging | Moderate |
CNC Knife Cutting | ±0.13-0.38 mm (±0.005"-0.015") | Limited by blade geometry | High precision setups |
Understanding these capabilities during design prevents specification of unachievable tolerances that increase costs without functional benefit. Process selection often provides more cost-effective tolerance achievement than forcing inappropriate processes to meet unrealistic specifications.
The Tolerance Stack-Up Reality Across Manufacturing Processes
Most engineering problems that appear to require tight tolerances actually stem from poor tolerance allocation across the assembly, regardless of whether components are machined or converted. Smart datum structure and intelligent tolerance distribution can often achieve the same functional requirements with significantly looser individual part tolerances across both machined housings and converted gaskets.
Consider a telecommunications housing assembly that originally specified extremely tight positional tolerances for connector mounting holes on the machined housing while simultaneously requiring precise gasket compression dimensions that approached converting process limits. The original specification created a tolerance stack-up nightmare that made reliable manufacturing nearly impossible.
The solution involved relocating datum structures and understanding material behavior. This change allowed the same functional fit with tolerances that were significantly looser for both components, dramatically reducing manufacturing complexity while improving assembly reliability.
Effective Datum Structure Principles
Effective datum structure follows key principles that work across both machining and converting processes:
- Primary Datum Selection: Choose the most stable, easily manufactured surface that relates directly to part function
- Secondary Datum Optimization: Select features that constrain the part in the most manufacturing-friendly orientation
- Tertiary Datum Placement: Use features that minimize tolerance stack-up to critical dimensions
- Local Referencing: Position critical features relative to nearby datums rather than distant references
The goal is creating a measurement and manufacturing reference system that makes sense for both the part's function and its production process.
Material Compliance Benefits
Converted parts often provide compliance that compensates for manufacturing variation in mating components. A gasket designed with appropriate material selection can accommodate housing variations that would create assembly problems with rigid components.
This compliance relationship enables tolerance relaxation strategies that aren't available with machined-to-machined interfaces. Understanding material behavior and leveraging compliance reduces overall system tolerance requirements while maintaining assembly functionality.
Visit our full Design for Manufacturability resource center.
Understanding GD&T Impact Across Manufacturing Processes
Geometric Dimensioning and Tolerancing (GD&T) specifications directly dictate manufacturing and inspection complexity for both machined and converted parts, but the implications differ significantly between processes. Many engineers use default software settings or apply machining drawing conventions to converted parts without understanding the downstream implications.
Profile tolerances exemplify this challenge perfectly for both manufacturing processes. A profile callout requires inspection of the entire specified geometry, meaning every point along a complex curve must be measured and verified. Compare this to simple dimensional tolerances that require only key point measurements.
For converted parts specifically, many engineers apply GD&T callouts designed for machined parts without understanding the manufacturing implications. Most converted parts serve as compliant sealing elements that conform to their installation environment.
GD&T Manufacturing Impact Comparison
Tolerance Type | Machined Parts Impact | Converted Parts Impact | Typical Applications |
---|---|---|---|
Linear Dimensions | Low inspection complexity | Standard measurement capability | Clearance holes, basic geometry |
Profile Tolerance | High programming complexity | Difficult for compliant materials | Complex sealing surfaces |
Position Tolerance | Moderate setup complexity | Limited applicability | Hole patterns vs. compression areas |
Concentricity | Specialized equipment required | Usually not applicable | Rotating assemblies |
Flatness | Surface finish control required | Material-dependent achievability | Sealing surfaces, datum references |
Perpendicularity | Fixturing and setup complexity | Assembly interfaces | Mounting surfaces |
The datum structure becomes even more critical when dealing with parts that interface across manufacturing processes. A feature tolerance that references a datum 300 mm (12 inches) away introduces potential error from thermal effects, machine deflection, and measurement uncertainty.
Thread Specifications Best Practices
Thread specifications present another common over-specification area that affects both processes:
- Functional Approach: Specify thread class and position requirements only
- Avoid Manufacturing Methods: Don't specify cut tap vs. roll tap unless functionally required
- Consider Engagement: Specify minimum engagement length rather than full thread depth
- Allow Process Optimization: Let manufacturers choose optimal drilling and tapping procedures
Default CAD software settings often specify cut tap drill sizes, but manufacturers frequently use roll taps for superior thread quality and tool life.
Visit our CNC Machining Resource Center.
Industry-Specific Tolerance Realities
Different industries have fundamentally different tolerance philosophies based on their operational requirements and risk profiles, but these philosophies must adapt to both machining and converting process realities. Understanding these industry-specific approaches helps engineers make appropriate tolerance decisions for their applications.
The cost of precision is often justified by the criticality of the application, but the approach differs between machined structural components and converted sealing elements.
Aerospace and Defense Manufacturing
Aerospace and defense applications often push tolerance limits due to weight constraints and performance requirements. Every gram matters when you're launching into space or designing flight-critical systems.
Machined aerospace components frequently require tight tolerances for weight optimization and interface precision. These projects typically involve extensive design reviews where mechanical teams evaluate whether proposed manufacturing tolerances affect weight calculations or performance parameters.
Converted gaskets and seals in aerospace applications often require environmental sealing performance rather than dimensional precision. The emphasis shifts toward consistent, reliable manufacturing processes and material performance rather than absolute dimensional precision.
Medical Device Manufacturing Tolerances
Medical device manufacturing operates under different constraints. Patient safety requirements drive quality standards, but functional tolerances are often more forgiving than aerospace applications.
Medical device machined components often require precise interface dimensions for reliable operation. The emphasis shifts toward consistent, reliable manufacturing processes rather than absolute precision.
Converted parts in medical applications typically focus on biocompatibility and sealing performance, where material selection proves more critical than dimensional precision.
Industry Tolerance Comparison
Industry | Machined Parts Tolerance | Converted Parts Focus | Primary Drivers | Cost Sensitivity |
---|---|---|---|---|
Aerospace | ±0.025-0.05 mm (±0.001-0.002 in) | Environmental sealing performance | Weight, performance, safety | Low |
Medical Devices | ±0.05-0.1 mm (±0.002-0.004 in) | Biocompatibility and reliability | Patient safety, regulatory compliance | Medium |
Telecommunications | ±0.1-0.2 mm (±0.004-0.008 in) | EMI shielding effectiveness | Assembly efficiency, signal integrity | High |
Consumer Electronics | ±0.2-0.5 mm (±0.008-0.020 in) | Cost optimization | Cost optimization, aesthetic fit | Very High |
The Economics of Over-Specification Across Processes
Manufacturing cost increases exponentially as tolerances tighten for both machined and converted parts, but the cost drivers differ between processes. Understanding these economics helps engineers make informed decisions about tolerance specification during the design phase.
Standard machining processes can typically achieve ±0.1 mm (±0.004 inch) tolerances efficiently. Tightening to ±0.025 mm (±0.001 inch) might require precision machining equipment, temperature control, and specialized inspection protocols.
Process capability becomes a critical factor for both manufacturing approaches. A manufacturing process with natural variation of ±0.05 mm (±0.002 inch) can easily meet ±0.1 mm (±0.004 inch) tolerances but will struggle with ±0.025 mm (±0.001 inch) specifications without significant process control investments.
Hidden Costs of Tight Tolerance Manufacturing
The hidden costs extend beyond the obvious manufacturing time increases:
- Setup Complexity: Tighter tolerances require more precise fixturing and longer setup procedures
- Tool Requirements: Specialized cutting tools and inspection equipment may be necessary
- Quality Control: Inspection time increases dramatically as measurement uncertainty becomes significant relative to tolerance bands
- Yield Considerations: Tighter tolerances typically result in higher rejection rates, requiring overproduction to meet delivery quantities
- Environmental Factors: Temperature control and vibration isolation may be required
- Skilled Labor: Precision work often requires more experienced machinists and inspectors
Converted Parts Cost Impact
For converted parts, tolerance requirements that exceed process capabilities force material overproduction to achieve statistical compliance:
- Material Waste: When tolerances exceed machine capabilities, manufacturers must produce 20-30% additional parts to ensure adequate good parts for delivery
- Process Selection: Tighter tolerances may require more expensive cutting processes
- Quality Control: Complex geometric measurements take significantly longer than simple dimensional checks
- Setup Complexity: Achieving tight tolerances on converted parts often requires specialized fixturing and extended setup procedures
The most expensive tolerance is often the one that provides no functional benefit — whether applied to machined housings or converted gaskets.
Understanding the cost implications of manufacturing decisions is crucial for effective tolerance specification.
Smart Tolerance Allocation Strategies Across Manufacturing Processes
Effective tolerance allocation starts with understanding which dimensions actually matter for part function, recognizing that machined components and converted parts contribute differently to overall assembly performance. Not every dimension on a drawing requires the same level of control.
Critical dimensions that affect assembly fit, sealing performance, or safety functions deserve tight control. Non-critical dimensions for material removal, aesthetic features, or clearance areas can often accept much looser tolerances without functional impact.
The goal is creating a tolerance hierarchy that guides both design decisions and manufacturing resource allocation.
Tolerance Hierarchy Framework
Develop a tolerance hierarchy based on functional importance that considers both manufacturing processes:
- Critical Tolerances: Dimensions that directly affect part function, safety, or assembly — machined parts typically ±0.025-0.05 mm (±0.001-0.002 inch), converted parts follow material-specific standards with functional validation
- Important Tolerances: Dimensions that affect performance but have some functional margin — machined parts typically ±0.05-0.1 mm (±0.002-0.004 inch), converted parts use standard material tolerances with process optimization
- Standard Tolerances: Dimensions controlled by general drawing tolerances — machined parts typically ±0.1-0.2 mm (±0.004-0.008 inch), converted parts use RMA standard tolerances for material type
- Non-Critical Tolerances: Clearance and aesthetic features — both processes accept loosest practical tolerances
This hierarchy guides both design decisions and manufacturing resource allocation. Critical tolerances receive the most attention during manufacturing and inspection, while standard tolerances rely on normal process control.
Cross-Process Optimization Strategies
When assemblies include both machined and converted components, tolerance allocation should leverage the strengths of each process:
- Leverage Material Compliance: Converted parts can accommodate variation in mating machined components through material compression and flexibility
- Optimize Datum Structure: Reference critical dimensions to local features rather than creating tolerance chains across different manufacturing processes
- Consider Assembly Sequence: Parts installed first can be held to tighter tolerances, while final components can accommodate accumulated variation
- Material Selection Integration: Choose materials that provide appropriate compliance for the tolerance environment
Material Selection Impact on Tolerances
Material selection also influences tolerance achievability differently for machined and converted parts:
Temperature effects become significant for precision applications. A 300 mm (12 inch) aluminum part will expand approximately 0.07 mm (0.003 inch) for every 10°C (18°F) temperature change. Specifying tolerances tighter than expected thermal variation creates an impossible manufacturing situation.
Machined Parts Material Considerations
Material Type | Typical Achievable Tolerance | Manufacturing Considerations |
---|---|---|
Aluminum Alloys | ±0.025 mm (±0.001 in) | Excellent machinability, thermal stability |
Stainless Steel | ±0.05 mm (±0.002 in) | Work hardening, tool wear considerations |
Titanium Alloys | ±0.1 mm (±0.004 in) | Difficult machining, specialized tooling |
Engineering Plastics | ±0.1-0.2 mm (±0.004-0.008 in) | Thermal expansion, material variation |
Converted Parts Material Considerations
For converted parts, material properties directly determine achievable tolerances through cutting behavior and dimensional stability:
- Film Materials: Provide excellent dimensional stability but require careful handling to prevent damage during processing
- Dense Rubber Materials: Offer good tolerance capability and edge quality but may require specific cutting processes for optimal results
- Foam Materials: Present challenges with compression during cutting, affecting final dimensions and requiring looser tolerance specifications
- Specialty Materials: Some materials require temperature-controlled environments (frozen materials at -25°C/-13°F) or present unique handling challenges that affect tolerance achievability
Understanding material behavior enables appropriate tolerance specification that aligns with manufacturing realities rather than theoretical requirements.
Read our EMI Gasket Design Guide.
Drawing Communication Best Practices Across Processes
Clear communication between design and manufacturing teams prevents costly misunderstandings and revision cycles, with specific considerations for different manufacturing processes. The most common issues stem from ambiguous drawing requirements or conflicting information between CAD models and dimensional drawings.
Most companies establish precedence in their drawing standards, but individual drawings should confirm the hierarchy. Thread callouts frequently create confusion when engineers specify manufacturing methods rather than functional requirements.
Avoid specifying manufacturing methods unless truly required. Calling out specific tools, cutting speeds, or surface finish processes constrains manufacturing flexibility and often increases costs without functional benefit.
Process-Specific Drawing Requirements
Understanding the different requirements for each manufacturing process helps engineers create drawings that communicate design intent effectively:
- For Machined Parts: Specify datum structure, surface finish requirements, and geometric controls that align with machining capabilities
- For Converted Parts: Focus on overall dimensional requirements and material specifications rather than complex geometric controls that may not be achievable or necessary
- Cross-Process Assemblies: Clearly indicate which manufacturing process produces each component and ensure tolerance specifications align with process capabilities
Essential Drawing Clarity Requirements
Essential drawing clarity requirements that apply across all manufacturing processes include:
- Precedence Statement: Clearly indicate whether CAD model or drawing dimensions control
- General Tolerance Block: Specify standard tolerances for dimensions without specific callouts
- Material Specifications: Include grade, condition, and any special requirements
- Surface Finish Callouts: Specify functional requirements rather than arbitrary values
- Inspection Requirements: Indicate sampling plans and critical characteristics
Thread callouts frequently create confusion. Instead of specifying manufacturing methods like drill sizes, focus on functional requirements: thread class, position tolerance, and engagement length. This approach allows manufacturers to optimize their processes while meeting functional needs.
Surface Finish Considerations
Surface finish specifications deserve particular attention across both manufacturing processes. Very smooth finishes can actually hinder adhesion for Form-in-Place gasket applications, while overly rough finishes might affect sealing performance.
Understanding the functional requirements helps specify appropriate surface finish ranges rather than arbitrary values. This approach enables manufacturers to optimize their processes while meeting true functional needs.
Read our Complete Form-in-Place Gasket Guide.
When Precision Actually Matters Across Processes
Some applications genuinely require tight tolerances, and recognizing these situations is equally important for both machined and converted parts. The key is distinguishing between functional requirements and aesthetic preferences across all manufacturing processes.
Many tight tolerance specifications stem from a desire for "precise" drawings rather than actual functional needs. For converted parts specifically, engineers often apply machining-style tolerances without understanding that material compliance frequently accommodates dimensional variation that would be problematic in rigid assemblies.
Understanding when precision is truly necessary helps engineers make informed decisions about tolerance specification and associated costs.
Critical Applications for Tight Machined Part Tolerances
Machined components often require precision for specific functional reasons:
- Rotating Assemblies: Demand careful tolerance control to prevent binding, excessive wear, or vibration issues — these applications often require both dimensional accuracy and geometric control like concentricity or perpendicularity
- Assembly Interfaces: Frequently drive tolerance requirements for connector housings that must maintain precise positioning to ensure reliable electrical connections
- Mounting Hole Patterns: Require positional accuracy to avoid assembly stress or connection issues
- Mating Surfaces: Need flatness and perpendicularity control for proper interface performance
Critical Applications for Tight Converted Part Tolerances
Converted parts rarely require tight tolerances for dimensional accuracy but may need precision for specific functional applications:
- Sealing Performance: Gasket compression requirements that demand specific thickness control for even compression across the entire sealing perimeter
- Assembly Interfaces: Parts that must align with tight-tolerance machined components where material compliance cannot accommodate dimensional variation
- Functional Clearances: Components where precise positioning is required and material compliance cannot accommodate dimensional variation
- Environmental Sealing: Applications requiring precise control to ensure gasket compression and performance
High-volume production sometimes justifies tight tolerances for assembly efficiency. Parts that must assemble automatically or with minimal adjustment benefit from precise dimensional control, even if slightly looser tolerances would function adequately.
Sealing Surface Requirements
Sealing surfaces often require precise control to ensure gasket compression and performance. A housing designed for environmental sealing might need flatness control to ensure even gasket compression across the entire sealing perimeter.
Understanding the relationship between surface finish, flatness, and sealing performance helps engineers specify appropriate requirements without over-constraining the manufacturing process.
Working with Manufacturing Partners Across Processes
Successful tolerance implementation requires collaboration between design and manufacturing teams from the earliest design phases, with expertise spanning both machining and converting processes. Manufacturing partners can provide valuable insight into process capabilities, cost implications, and alternative approaches to achieving functional requirements.
Early Design for Manufacturability (DfM) reviews help identify potential tolerance issues before tooling commitments or long-lead procurement activities. These discussions often reveal opportunities for tolerance relaxation without functional impact.
Manufacturing capability discussions should cover both standard and precision processes. Understanding what tolerances require special procedures helps designers make informed decisions about specification requirements.
Key Collaboration Areas
Effective collaboration between design and manufacturing teams focuses on several critical areas:
- Process Capability Discussions: Understanding what tolerances require special procedures across both machining and converting processes
- Material Behavior Education: Learning how different materials respond to cutting processes and how compliance affects assembly requirements
- Cost Impact Analysis: Evaluating the economic implications of tolerance decisions across different manufacturing processes
- Alternative Approaches: Exploring different design methods to achieve functional requirements through optimal process selection
- Quality System Alignment: Establishing appropriate inspection protocols that consider the different measurement challenges between machined and converted parts
Modus Advanced Engineering Partnership
At Modus Advanced, our engineering team — representing more than 10% of our staff — works directly with customers during the design phase to optimize tolerance specifications across both machining and converting processes. Our comprehensive manufacturing capabilities allow us to recommend the most efficient approach for each application.
Our AS9100 and ISO 9001 certifications ensure we maintain the quality systems necessary for precision work across all manufacturing processes. This combination of engineering expertise and quality systems enables us to provide realistic feedback about tolerance achievability and cost implications.
We believe that one day matters, and proper tolerance specification from the beginning prevents costly delays and redesigns that can extend project timelines by weeks or months.
Quality Control Integration Across Manufacturing Processes
Quality inspection requirements can dramatically affect production schedules and costs for both machined and converted parts, but the inspection challenges differ between processes. Understanding these differences helps engineers make informed decisions about inspection requirements during the design phase.
The difference between standard sampling inspection and 100% inspection can double manufacturing lead times. Different measurement techniques require varying amounts of time per part, which directly affects project timeline and costs.
Complex geometric measurements take significantly longer than simple dimensional checks, and these differences compound quickly across production quantities.
Inspection Complexity Differences
Understanding the measurement challenges for different manufacturing processes helps engineers specify appropriate inspection requirements:
- Machined Parts: Typically enable precise measurement with standard metrology equipment — geometric features maintain dimensional stability during inspection, and measurement uncertainty is well understood
- Converted Parts: Present unique inspection challenges due to material compliance — soft materials may deform under measurement pressure, while thin films require specialized handling to prevent damage during inspection
Best Fit vs. Exact Measurement
For converted parts specifically, "best fit" measurement techniques often provide adequate quality assurance while reducing inspection time and costs:
- Exact Measurement: Involves taking precise dimensional readings at specific points according to drawing specifications — provides definitive pass/fail results but requires more time and may reject parts that would function perfectly well in their intended application
- Best Fit Measurement: Uses mathematical algorithms to find the optimal geometric relationship between measured points and the intended design — evaluates how well the overall part geometry matches the design intent rather than checking specific points against tight tolerances
Best fit measurements work particularly well for compliant materials like gaskets and seals, where the part will conform to its installation environment during use. A gasket that shows minor geometric variations under best fit analysis may still provide excellent sealing performance once compressed into position.
Standard vs. 100% Inspection
Understanding inspection level options helps engineers make appropriate quality decisions:
- Standard AQL Sampling: Requires inspecting a statistical sample of parts based on lot size — provides adequate quality assurance for most applications while minimizing inspection time
- 100% Inspection: Requires measuring every single part produced — can extend lead times by days or weeks depending on part complexity and quantity
For most converted parts applications, standard sampling provides adequate quality assurance while avoiding the substantial time and cost increases associated with 100% inspection requirements.
Many customer quality manuals specify 100% inspection requirements by default. These requirements are often carried forward from previous projects without evaluating their necessity for specific applications.
Frequently Asked Questions About Tolerance Across Manufacturing Processes
How do converted part tolerances compare to machined part tolerances?
Converted parts typically require looser tolerances than machined parts due to material properties and cutting process limitations. Film materials might achieve ±0.25 mm (±0.010") accuracy, while foam materials typically require ±0.63 mm (±0.025") or looser tolerances. Machined parts can achieve ±0.025 mm (±0.001") precision under controlled conditions.
Can the same tolerance standards apply to both machined and converted parts?
No. Machined parts follow general machining tolerances, while converted parts must follow material-specific standards from the Rubber Manufacturers Association (RMA). Applying machining tolerances to converted parts often results in unrealistic specifications that increase costs without functional benefit.
When should I specify tight tolerances for converted parts?
Tight tolerances for converted parts should only be specified when genuinely required for function, such as specific gasket compression requirements or assembly interfaces with tight-tolerance machined components. Most converted parts perform their sealing function adequately with standard material tolerances.
How do I optimize tolerance allocation in assemblies with both machined and converted parts?
Leverage the strengths of each process. Use machined parts for precise positioning and interface requirements, while allowing converted parts to accommodate variation through material compliance. Reference critical dimensions to local features rather than creating tolerance chains across different manufacturing processes.
What industries require tight tolerance manufacturing?
Aerospace, medical devices, defense, and precision instrumentation industries commonly require tight tolerance manufacturing. These applications demand exceptional accuracy for safety, performance, and regulatory compliance. However, the specific tolerance requirements vary significantly between machined structural components and converted sealing elements.
How much more does tight tolerance manufacturing cost?
Tight tolerance machining can cost 2-24 times more than standard tolerances, depending on the precision required. Moving from ±0.13 mm (±0.005 inches) to ±0.025 mm (±0.001 inch) typically doubles costs, while ultra-precision tolerances of ±0.0025 mm (±0.0001 inch) can increase costs by 24x. For converted parts, exceeding process capabilities typically requires 20-30% material overproduction.
The Path Forward: Optimizing Tolerance Decisions
Smart tolerance specification requires balancing functional requirements with manufacturing realities across all manufacturing processes. The goal is achieving necessary performance with the most manufacturable design possible, whether that involves precision machining, converting operations, or both.
Start with functional analysis that considers both manufacturing processes. What does each dimension actually control? How does variation in that dimension affect part performance?
This analysis often reveals opportunities for tolerance relaxation without functional compromise. Consider the complete tolerance chain from raw material through final assembly, recognizing that machined and converted components contribute differently to overall system performance.
Sometimes tight individual part tolerances are necessary to compensate for accumulation across multiple assembly levels, while other applications can leverage material compliance to accommodate variation. Develop relationships with manufacturing partners who understand both machining and converting processes and can provide honest feedback about tolerance achievability and cost implications across different manufacturing methods.
Remember that the tightest tolerance isn't necessarily the best tolerance — whether applied to machined components or converted parts. The optimal specification achieves necessary function with maximum manufacturing efficiency, and that balance requires understanding both the design requirements and the manufacturing realities across all processes.
When lives depend on your innovation, partner with a manufacturer who understands what's at stake across all manufacturing processes. Contact Modus Advanced to discuss how our engineering expertise and comprehensive manufacturing capabilities can help optimize your tolerance specifications for both performance and cost-effectiveness.