Aerospace Parts Manufacturing: Precision Components for Critical Applications
June 30, 2025
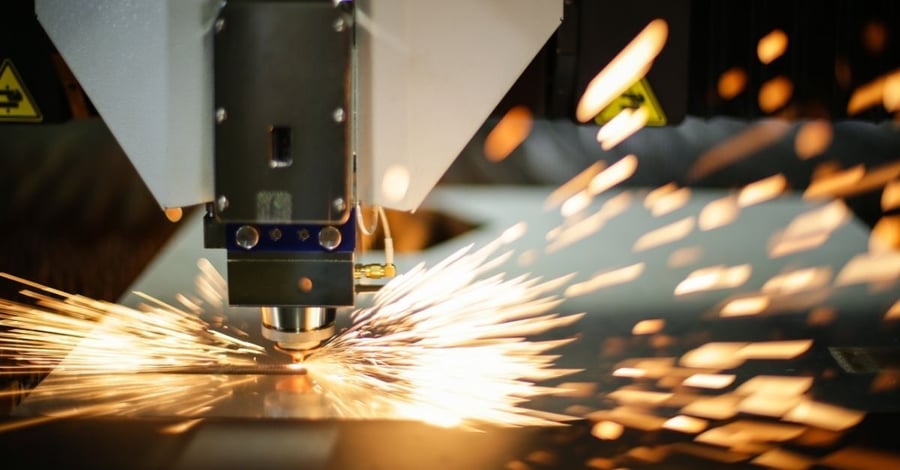
Manufactured with Speed and Precision
The manufacturing capabilities you need and the engineering support you want, all from a single partner.
Submit a DesignKey Points
- Precision and reliability requirements: Modern aerospace parts manufacturing demands unprecedented precision and reliability for components that protect lives and ensure mission success
- Quality certifications: Quality standards like AS9100 and NADCAP certifications establish the foundation for manufacturing critical flight systems
- Advanced materials expertise: Advanced materials including titanium alloys, carbon fiber composites, and specialized elastomers require sophisticated processing techniques and rigorous testing protocols
- Manufacturing tolerances: Aerospace manufacturing tolerances typically require extreme precision when compared to other industries
- Vertical integration advantages: Vertical integration capabilities allow manufacturers to control quality across multiple processes while reducing lead times for time-sensitive aerospace programs
- Strategic partnerships: Strategic supplier partnerships enable aerospace companies to accelerate development timelines while maintaining the exacting standards required for flight-critical applications
What is Aerospace Parts Manufacturing?
Aerospace parts manufacturing encompasses the design, production, and testing of precision components for aircraft, spacecraft, and defense systems. This specialized manufacturing sector serves both commercial aviation and military applications, producing everything from engine components and structural elements to electronic housings and sealing systems.
Aerospace parts manufacturing encompasses the design, production, and testing of precision components for aircraft, spacecraft, and defense systems where failure is not an option.
Aerospace parts manufacturing companies must meet stringent quality standards established by organizations like the International Aerospace Quality Group (IAQG) and comply with regulations from the Federal Aviation Administration (FAA) and Department of Defense (DoD).
The Stakes in Aerospace Parts Manufacturing
Aerospace components operate in environments where failure is not an option. A single defective part can compromise an entire mission, endanger lives, or result in catastrophic financial losses.
A single defective part can compromise an entire mission, endanger lives, or result in catastrophic financial losses.
The aerospace industry demands manufacturing precision measured in microns, materials that perform flawlessly across extreme temperature ranges, and quality systems that catch defects before they reach critical applications.
When a medical evacuation helicopter needs to reach a remote location, when a satellite must deploy communications equipment in orbit, or when a fighter aircraft requires reliable performance in combat, the components inside these systems must perform exactly as designed.
This level of reliability starts with manufacturing partners who understand the gravity of their role in the aerospace supply chain.
Understanding Aerospace Manufacturing Requirements
Material Specifications and Standards
Aerospace applications require materials that meet stringent performance criteria across multiple dimensions. Each material must demonstrate consistent properties under stress, temperature cycling, and long-term exposure to harsh environments.
Aerospace materials must demonstrate consistent properties under stress, temperature cycling from -55°C to +260°C, and long-term exposure to harsh environments.
The materials commonly used in aerospace manufacturing include:
- Titanium alloys for high-strength, lightweight structural components
- Aluminum alloys for weight-critical applications with corrosion resistance
- Stainless steel for components requiring high temperature performance
- Carbon fiber composites for maximum strength-to-weight ratios
- Specialized elastomers for sealing applications in extreme environments
- Superalloys for turbine components and high-temperature applications
Quality Certifications and Compliance
AS9100 certification establishes the baseline quality management system for aerospace manufacturing. This standard builds upon ISO 9001 with additional requirements specific to aerospace applications, including risk management, configuration management, and product safety considerations.
AS9100 certification is the baseline quality management system for aerospace manufacturing, building upon ISO 9001 with aerospace-specific requirements for risk management and product safety.
Understanding the differences between these standards is crucial for aerospace suppliers. Our detailed comparison in Quality Certifications for Manufacturing: AS9100 vs. ISO 9001 explains how AS9100 builds upon ISO 9001 with aerospace-specific requirements.
Key aerospace quality standards include:
- AS9100 - Primary quality management system for aviation, space, and defense organizations
- NADCAP - National Aerospace and Defense Contractors Accreditation Program for special processes
- ITAR - International Traffic in Arms Regulations compliance for defense applications
- FAA regulations - Federal Aviation Administration requirements for commercial aviation
- MIL-SPEC - Military specifications for defense contractors
NADCAP (National Aerospace and Defense Contractors Accreditation Program) accreditation provides independent verification of special processes like heat treating, welding, and surface treatments. These processes directly impact component performance and require specialized equipment, trained personnel, and rigorous process controls.
ITAR (International Traffic in Arms Regulations) compliance becomes essential when manufacturing defense-related aerospace components. This certification ensures proper handling and protection of sensitive technical data while maintaining the security standards required for military applications. For military aerospace applications, understanding EMI in Military and Aerospace Electronics becomes critical for component design and manufacturing.
Critical Manufacturing Processes for Aerospace Components
Precision Machining Capabilities
CNC machining forms the backbone of aerospace parts manufacturing for complex geometries and tight tolerances. Modern aerospace components often require metal part tolerances within ±0.0005 inches while maintaining surface finishes that meet stringent specifications.
Multi-axis machining capabilities enable manufacturers to produce complex components in single setups, reducing part handling and improving geometric accuracy. This technology proves particularly valuable for turbine components, structural brackets, and complex housings that require multiple angled features.
Common aerospace machining processes include:
- 5-axis CNC machining for complex geometries and tight tolerances
- Precision turning for cylindrical components like shafts and fasteners
- High-speed machining for aluminum and composite materials
- Titanium machining requiring specialized tooling and techniques
The selection of cutting tools, workholding systems, and machining parameters requires extensive knowledge of aerospace materials and their machining characteristics. Titanium alloys, for example, require specific cutting speeds and tool geometries to prevent work hardening and achieve desired surface finishes.
Manufacturing engineers can benefit from understanding common challenges and solutions detailed in our guide Lessons Learned from Machining. Additionally, design engineers should consider 13 Design Features That Can Reduce Your Lead Times and Costs for Machined Parts to optimize components for efficient production.
Specialized Joining and Assembly Techniques
Aerospace components often require joining techniques that maintain structural integrity while meeting weight requirements. Friction stir welding provides high-strength joints in aluminum structures without the heat-affected zones associated with traditional welding processes.
Bonded assemblies using structural adhesives enable lightweight designs while distributing loads across larger areas. These joints require precise surface preparation, controlled application environments, and rigorous cure monitoring to ensure reliable performance. For critical applications requiring metal-to-elastomer bonds, understanding how rubber is bonded to metal becomes essential for reliable aerospace assemblies.
Form-in-place gasket dispensing creates custom sealing solutions for complex geometries while eliminating the assembly challenges associated with pre-formed gaskets. This technology proves particularly valuable for EMI shielding applications and environmental sealing requirements. Design engineers should consider 4 Keys to Successful Form-in-Place Gasket Design when incorporating FIP gaskets into aerospace assemblies.
Form-in-place gasket dispensing creates custom sealing solutions for complex geometries while eliminating assembly challenges and reducing manufacturing steps.
Surface Treatment and Finishing
Surface treatments enhance component performance by improving corrosion resistance, wear characteristics, and electromagnetic properties. Anodizing processes provide controlled oxide layers on aluminum components while maintaining dimensional accuracy.
Plating operations add protective or functional coatings to base materials. Nickel, chrome, and precious metal platings serve different purposes depending on application requirements, from corrosion protection to electrical conductivity enhancement.
Shot peening and similar surface enhancement processes improve fatigue life by introducing beneficial compressive stresses in component surfaces. These treatments prove particularly important for rotating components and structures subject to cyclic loading.
Advanced Materials in Aerospace Manufacturing
High-Performance Alloys and Composites
Modern aerospace applications push material performance beyond traditional limits. Inconel and Hastelloy superalloys maintain strength and corrosion resistance at temperatures exceeding 538°C (1000°F), making them essential for turbine applications and exhaust systems.
Carbon fiber reinforced polymers (CFRP) provide exceptional strength-to-weight ratios but require specialized manufacturing techniques. Autoclave curing, resin transfer molding, and vacuum infusion processes each offer advantages for different component geometries and production volumes.
Titanium alloys like Ti-6Al-4V combine excellent mechanical properties with biocompatibility, making them suitable for both aerospace structures and medical device components in dual-use applications.
Titanium in Aerospace Applications
Ti-6Al-4V is the most widely used titanium alloy in aerospace, representing over 70% of all titanium alloy production. This alloy provides:
- Density: 4420 kg/m³ (45% lighter than steel)
- Tensile strength: Up to 1000 MPa
- Operating temperature: Up to 204°C (400°F)
- Excellent corrosion resistance in aerospace environments
Ti-6Al-4V titanium alloy is 45% lighter than steel while providing tensile strength up to 1000 MPa and operating temperatures up to 204°C.
Applications of titanium alloys in aerospace include:
- Engine components (turbine blades, compressor discs)
- Structural elements (frames, fasteners, landing gear)
- Heat exchangers and exhaust systems
- Hydraulic system components
Specialized Elastomers and Sealing Materials
Aerospace sealing applications demand elastomers that maintain flexibility across temperature ranges from -54°C to +204°C (-65°F to +400°F) while resisting fuel, hydraulic fluids, and environmental contaminants.
Fluorosilicone elastomers provide fuel resistance superior to standard silicone while maintaining low-temperature flexibility. These materials prove essential for fuel system applications and engine compartment sealing.
Perfluoroelastomers offer chemical resistance to virtually all aerospace fluids but require specialized processing equipment and techniques. Their use in critical sealing applications justifies the additional complexity and cost.
Aerospace Elastomer Material Comparison:
Material Type | Temperature Range | Fuel Resistance | Chemical Compatibility | Typical Applications |
Nitrile (NBR) | -40°C to +121°C (-40°F to +250°F) | Excellent | Good | Hydraulic systems, fuel lines |
Fluorosilicone | -54°C to +204°C (-65°F to +400°F) | Excellent | Very Good | Engine seals, fuel systems |
Perfluoroelastomer | -26°C to +260°C (-15°F to +500°F) | Outstanding | Excellent | Critical sealing, chemical exposure |
EPDM | -54°C to +149°C (-65°F to +300°F) | Poor | Good | Weather sealing, non-fuel applications |
Testing and Validation Requirements
Material qualification requires extensive testing to verify performance under aerospace operating conditions. Tensile testing, compression set testing, and thermal cycling validate basic mechanical properties.
Environmental testing exposes materials to combined effects of temperature, pressure, fluid exposure, and mechanical stress. These tests often run for thousands of hours to simulate long-term service conditions.
Accelerated aging studies predict long-term material performance by exposing samples to elevated temperatures and stresses. Statistical analysis of test results provides confidence intervals for component life predictions.
Quality Control in Aerospace Manufacturing
Inspection and Measurement Technologies
Coordinate measuring machines (CMMs) provide dimensional verification for complex aerospace components. Modern CMMs achieve measurement uncertainties below 0.0001 inches while handling components weighing several hundred pounds.
Optical measurement systems enable non-contact inspection of delicate components and complex surfaces. These systems prove particularly valuable for thin-walled structures and components with intricate internal geometries.
X-ray and CT scanning technologies detect internal defects that escape visual inspection. These techniques identify porosity, inclusions, and structural discontinuities that could lead to premature failure.
Statistical Process Control
Control charts track key process parameters in real-time, enabling immediate response to process variations. Temperature profiles, pressure readings, and dimensional measurements receive continuous monitoring throughout manufacturing operations.
Capability studies (Cpk) quantify process performance relative to specification requirements. Aerospace applications typically require Cpk values exceeding 1.33 to demonstrate adequate process control.
Aerospace applications typically require Cpk values exceeding 1.33 to demonstrate adequate process control and statistical capability.
Design of experiments (DOE) methodologies optimize process parameters while minimizing the number of test runs required. These statistical techniques prove particularly valuable when developing processes for new materials or component geometries.
Traceability and Documentation Requirements
Complete traceability from raw materials through final inspection creates the documentation trail required for aerospace applications. Every component must include records linking it to specific material lots, process parameters, and inspection results.
Certificate of compliance documentation verifies that components meet all specified requirements. These certificates accompany components throughout their service life and support maintenance and overhaul operations.
Non-conformance reporting systems capture and analyze quality issues to prevent recurrence. Root cause analysis and corrective action processes ensure continuous improvement in manufacturing operations. Understanding how to Avoid Quality Control Issues with Component Manufacturers can help aerospace companies select reliable manufacturing partners and establish effective quality partnerships.
Aerospace Manufacturing Tolerances and Precision Requirements
Understanding Aerospace Tolerances
Aerospace manufacturing tolerances represent the acceptable variation limits in component dimensions and characteristics. These tolerances directly impact component performance, safety, and system reliability.
Typical aerospace tolerance requirements:
- Critical components: ±0.0005 inches (±0.0127 mm)
- Standard machined parts: ±0.001 to ±0.005 inches
- Surface finish: Ra 32 to Ra 125 microinches
- Geometric tolerances: Position within ±0.0002 inches
Factors Affecting Tolerance Achievement
Material properties significantly influence achievable tolerances. Titanium machining requires specialized techniques due to the material's work-hardening characteristics and heat sensitivity.
Machine tool capabilities determine the ultimate precision achievable. Modern aerospace manufacturing facilities utilize:
- High-precision CNC machining centers
- Multi-axis machines for complex geometries
- Advanced workholding systems
- Temperature-controlled environments
Process control measures ensure consistent results across production runs. This includes regular machine calibration, tooling management, and environmental monitoring.
EMI Shielding in Aerospace Applications
Electromagnetic interference (EMI) protection has become increasingly critical in modern aerospace systems as electronic components proliferate throughout aircraft and spacecraft. EMI shielding protects sensitive avionics, navigation systems, and communication equipment from electromagnetic interference that could compromise mission safety.
Aerospace EMI shielding requirements often exceed those of commercial applications due to the critical nature of flight systems. For engineers designing aerospace electronics, understanding What is EMI Shielding and Why is it Important for Your Design? provides essential foundation knowledge for effective shielding strategies.
Key considerations for aerospace EMI shielding include:
- Frequency ranges from DC to microwave frequencies
- Shielding effectiveness requirements often exceeding 80 dB
- Environmental durability across extreme temperature and vibration conditions
- Weight constraints demanding lightweight shielding solutions
Aerospace EMI shielding requires effectiveness exceeding 80 dB across frequency ranges from DC to microwave while maintaining environmental durability across extreme conditions."
Military aerospace applications face additional challenges with intentional jamming and electronic warfare considerations, detailed in our analysis of RF Absorbers for Military Applications.
For engineers incorporating EMI gaskets into aerospace designs, 3 Reasons to Use Nickel-Graphite Silicones for EMI Shielding Gaskets explains the advantages of nickel-graphite filled elastomers in aerospace environments.
Thermal Management in Aerospace Systems
Aerospace components operate in extreme thermal environments, from the sub-zero temperatures of high-altitude flight to the intense heat generated by high-performance electronics and propulsion systems. Thermal management becomes critical for maintaining component performance and preventing system failures.
Effective thermal interface materials enable heat dissipation from critical components while maintaining the reliability required for aerospace applications. For engineers designing thermal management systems, Thermal Management Solutions: 5 Keys to Thermal Dissipation Using Thermal Interface Material provides essential guidance for material selection and application techniques.
Aerospace thermal management challenges include:
- Wide temperature cycling from -55°C to +125°C or higher
- Vibration resistance maintaining thermal contact under dynamic conditions
- Weight optimization using lightweight materials with high thermal conductivity
- Long-term reliability over decades of service life
Engineers must often choose between thermal pads and form-in-place thermal materials. Our comparison guide What's My Solution: Thermal Pads or Thermal Form-In-Place? helps engineers select the optimal approach based on application requirements.
Vibration Isolation in Aerospace Applications
Aerospace systems experience significant vibration from engines, turbulence, and operational stresses. Vibration isolation protects sensitive components from damage while maintaining precise alignment of optical and navigational systems.
Rubber and elastomeric materials provide effective vibration isolation through their viscoelastic properties. Understanding Why Rubber is Used for Vibration and Shock Isolation helps engineers select appropriate materials and design effective isolation systems.
Critical factors for aerospace vibration isolation include:
- Frequency response across operational vibration spectra
- Temperature stability maintaining performance across flight envelopes
- Load capacity supporting component weights under acceleration
- Fatigue resistance for millions of vibration cycles
Supply Chain Considerations for Aerospace Manufacturing
Supplier Qualification and Assessment
Aerospace supply chains require suppliers with demonstrated capabilities in precision manufacturing and quality management. Initial supplier assessments evaluate technical capabilities, quality systems, and facility security measures.
On-site audits verify that suppliers maintain the processes and systems described in their quality manuals. These audits typically occur annually and include detailed review of process controls, measurement systems, and personnel training records.
Supplier performance monitoring tracks delivery performance, quality metrics, and responsiveness to engineering changes. This data supports supplier development activities and sourcing decisions for new programs.
Strategic Partnership Development
Long-term partnerships enable suppliers to invest in specialized equipment and capabilities that support specific aerospace programs. These relationships often span multiple years and include collaborative development activities.
Early supplier involvement in design processes leverages manufacturing expertise to optimize component designs for producibility. This collaboration reduces development costs and improves product quality.
Integrated supply chain management systems enable real-time visibility into production schedules, inventory levels, and quality metrics across multiple suppliers.
Risk Management and Contingency Planning
Supply chain risk assessment identifies potential disruptions from natural disasters, geopolitical events, and supplier financial instability. Multiple sourcing strategies and supplier diversification reduce exposure to single points of failure.
Inventory management balances carrying costs against the risk of production delays. Critical components may require strategic inventory positioning to support production schedules.
Supplier financial monitoring provides early warning of potential supplier difficulties. Credit assessments and financial statement analysis support proactive risk management.
Vertical Integration Benefits in Aerospace Manufacturing
Streamlined Production Workflows
Vertical integration eliminates transfer delays between multiple suppliers while maintaining quality control across all manufacturing processes. Components move directly from machining to surface treatment to assembly without intermediate shipping and receiving operations.
Process optimization across multiple manufacturing steps reduces overall cycle times and improves efficiency. Coordinated scheduling ensures that components arrive at each process step exactly when needed.
Quality feedback loops between processes enable rapid response to issues and continuous improvement in manufacturing operations. Problems identified in downstream processes can immediately influence upstream process parameters.
Enhanced Quality Control
Single-source responsibility for component quality eliminates the finger-pointing that can occur with multiple suppliers. Quality issues receive immediate attention and resolution without complex supplier coordination.
Integrated quality systems provide complete visibility into component history from raw material receipt through final shipment. This transparency supports both current production and future problem resolution.
Cross-training between processes enables personnel to understand the impact of their work on downstream operations. This knowledge improves quality consciousness and process discipline.
Cost and Schedule Advantages
Elimination of supplier markups and transportation costs between processes reduces overall component costs. These savings can be significant for complex components requiring multiple manufacturing steps.
Coordinated scheduling across all processes minimizes work-in-process inventory and reduces manufacturing cycle times. Components spend less time waiting between operations and more time adding value.
Engineering change implementation becomes more efficient when all processes are under single management. Design modifications can be implemented across all operations simultaneously rather than coordinating changes with multiple suppliers.
Vertical integration eliminates supplier markups and transportation costs between processes while reducing manufacturing cycle times and enabling coordinated engineering change implementation.
Choosing Your Aerospace Manufacturing Partner
Technical Capabilities Assessment
Aerospace parts manufacturing companies must demonstrate capabilities across the full range of processes required for your components. Machine tool accuracy, measurement capabilities, and process controls should meet or exceed your technical requirements.
Key capabilities to evaluate:
- AS9100 certification and quality system maturity
- Multi-axis machining capabilities for complex geometries
- Material expertise in titanium, superalloys, and composites
- Measurement and inspection capabilities including CMM and optical systems
- Special processes like heat treating, plating, and NDT
Engineering support capabilities enable collaborative development and design optimization. Manufacturing partners with dedicated engineering resources can provide valuable input during design phases and ongoing production support.
Facility infrastructure including environmental controls, material handling systems, and security measures should align with aerospace industry standards and your specific program requirements.
Quality System Evaluation
AS9100 certification provides baseline assurance of quality system adequacy, but detailed assessment of actual implementation reveals the true effectiveness of quality processes.
Quality metrics including first-pass yield, on-time delivery, and customer quality ratings demonstrate actual performance rather than just system capability.
Continuous improvement initiatives show commitment to advancing quality and efficiency over time. Partners with active improvement programs provide better long-term value.
Strategic Alignment
Cultural fit between organizations facilitates effective collaboration and problem-solving. Partners who understand the critical nature of aerospace applications bring appropriate focus and urgency to manufacturing operations.
Investment in aerospace-specific capabilities demonstrates long-term commitment to the industry. Partners who continuously upgrade equipment and capabilities provide better support for evolving requirements.
Financial stability ensures continuity of supply throughout program lifecycles that may span decades. Strong financial partners can invest in capabilities and maintain operations through economic cycles.
Trends and Future of Aerospace Parts Manufacturing
Advanced Manufacturing Technologies
Additive manufacturing (3D printing) is transforming aerospace parts production by enabling complex geometries impossible with traditional machining. 3D-printed titanium parts can reduce aircraft weight by hundreds or thousands of pounds.
For engineers evaluating additive manufacturing versus traditional methods, understanding 3D Printing vs. Compression Molding: What's the Right Choice? helps determine the optimal approach for specific aerospace applications.
Industry 4.0 technologies including IoT sensors, machine learning, and predictive analytics are improving process control and quality assurance. These technologies enable real-time monitoring and adjustment of manufacturing parameters.
Digital twin technology allows virtual simulation and optimization of manufacturing processes before physical production begins. This reduces development time and improves first-time quality.
Sustainability and Environmental Considerations
Environmental regulations and customer demands are driving adoption of more sustainable manufacturing practices. This includes:
- Reduced energy consumption in manufacturing processes
- Recycling and reuse of aerospace materials
- Elimination of hazardous substances where possible
- Lifecycle assessment and environmental impact reduction
Market Growth and Opportunities
The global aerospace manufacturing market continues to grow driven by:
- Increasing commercial air travel demand
- Military modernization programs
- Space exploration and satellite deployment
- Urban air mobility and electric aircraft development
Aerospace parts manufacturing companies that invest in advanced capabilities and maintain rigorous quality standards are positioned to capitalize on these growth opportunities.
Prototyping Considerations for Aerospace Development
Rapid prototyping enables aerospace engineers to validate designs quickly while minimizing development costs and timelines. Prototype development for aerospace applications requires balancing speed with the precision and material properties needed for meaningful testing.
Different manufacturing methods offer varying advantages for aerospace prototyping. Understanding The Best Manufacturing Method To Prototype Custom Molded Rubber Parts helps engineers select appropriate techniques for elastomeric components in aerospace applications.
Key prototyping considerations for aerospace include:
- Material fidelity ensuring prototype materials match production specifications
- Geometric accuracy maintaining critical dimensions and tolerances
- Test validity confirming prototype performance predicts production behavior
- Iteration speed enabling rapid design modifications based on test results
For sealing applications, prototyping often involves evaluating die-cut versus molded gasket solutions.
Rapid prototyping for aerospace requires balancing speed with precision and material fidelity to ensure prototype performance predicts production behavior.
Frequently Asked Questions About Aerospace Parts Manufacturing
What are the most critical quality standards for aerospace manufacturing?
AS9100 is the primary quality management system standard for aerospace manufacturing, building upon ISO 9001 with aerospace-specific requirements. Additional critical standards include NADCAP for special processes and ITAR for defense applications.
What materials are most commonly used in aerospace components?
The most common materials include aluminum, titanium alloys (especially Ti-6Al-4V), aluminum alloys, stainless steel, superalloys like Inconel, and carbon fiber composites. Material selection depends on specific application requirements including weight, temperature, and environmental conditions.
How tight are typical aerospace manufacturing tolerances?
Critical aerospace components typically require tolerances within ±0.0005 inches (±0.0127 mm). Some applications may require even tighter tolerances, while others may accept ±0.001 to ±0.005 inches depending on the component's function and criticality.
What is the difference between commercial and military aerospace manufacturing?
Military aerospace manufacturing typically requires additional certifications like ITAR compliance, higher security standards, and adherence to MIL-SPEC requirements. Both require AS9100 certification, but military applications often have more stringent testing and documentation requirements.
How long does it take to qualify a new aerospace supplier?
Supplier qualification for aerospace applications typically takes 6-18 months depending on the complexity of parts and processes involved. This includes capability assessments, quality system audits, first article inspections, and process validations.
Accelerating Aerospace Innovation Through Manufacturing Excellence
The aerospace industry continues pushing boundaries in performance, efficiency, and capability. Aerospace parts manufacturing companies that combine technical excellence with strategic thinking enable their customers to achieve ambitious development goals.
Advanced manufacturing technologies, rigorous quality systems, and collaborative partnerships create the foundation for aerospace components that perform reliably in the most demanding applications. When lives depend on component performance and mission success requires absolute reliability, the choice of manufacturing partner becomes critical to program success.
The most successful aerospace programs combine innovative design with manufacturing excellence from partners who understand the stakes involved. These partnerships accelerate development timelines while maintaining the uncompromising quality standards that aerospace applications demand.
Bottom Line: Success in aerospace parts manufacturing requires a manufacturing partner who combines AS9100-certified quality systems, advanced technical capabilities, and deep understanding of aerospace requirements. The right partner accelerates development timelines while ensuring the precision and reliability that aerospace applications demand.
Ready to elevate your aerospace manufacturing capabilities? Modus Advanced combines AS9100 certification, ITAR compliance, and vertically integrated processes with a team where engineers make up more than 10% of our staff. Our Design for Excellence (DFx) process helps aerospace partners optimize component designs while accelerating development timelines. When your mission-critical applications demand manufacturing excellence, discover why industry leaders choose Modus Advanced as their obvious choice for precision aerospace components.