Table Of Contents
We carry an extensive line of Lord mounts, which are designed to manage the vibration, noise and shock that can cause mechanical systems to fail. The key to isolating vibration is to reduce its transmission to a component or supporting structure. In a nutshell, the rubber in a mount acts as a spring with its own natural frequency, and this frequency partly depends on the stiffness of the spring. But why is rubber such an ideal material in this type of situation?
-- Article Continues Below --
Helping you select the right vibration isolator
The answer to this question requires knowing some basic facts about both natural and synthetic rubbers. This includes defining what we commonly call rubber. Lord Corporation’s Design Monograph DM1101a (available upon request) states, it “is a synthetic or natural material whose long, coiled, high-molecular weight chains have been cross-bridged by certain chemical ingredients to form a network. It is characterized by the ability to accept and recover from extreme deformation of 200 percent or more. The term elastomer includes natural rubber and the many synthetic materials that possess rubber-like properties.” The diagram below shows the chemical structure of natural rubber, cis-polyisoprene. Natural rubber is composed of long chains consisting of at least 10,000 similar chemical units.
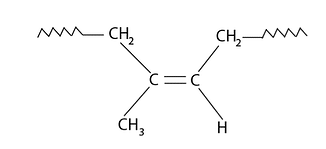
Image: Natural Rubber Chemical Structure
Charles Goodyear discovered in 1839 that when rubber is vulcanized with sulfur at 120-220°C, the rubber molecules join via sulfur atoms, as shown in the diagram below. This cross linking creates the molecular network that gives the rubber strength, elasticity and other important mechanical properties. There are various types of vulcanizates that vary according to the type of crosslinking that occurs. Vulcanizates with carbon-carbon crosslinks generally have higher temperature resistance, while vulcanizates with higher polysulphidic crosslinks are stronger.
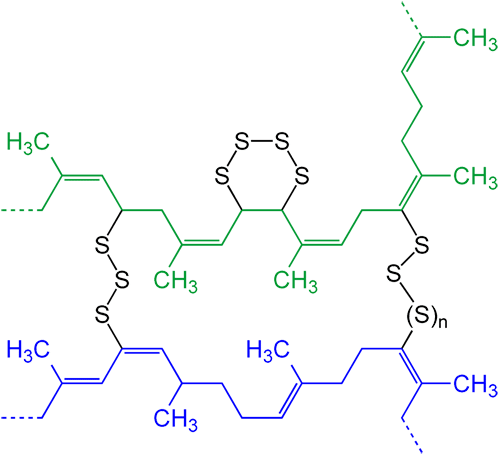
In addition, rubbers used for industrial and engineering applications generally are compounded with fillers that affect the properties of the vulcanizate. The fillers usually consist of carbon black, and the formulation used with greatly affect the properties of the rubber, such as tear and abrasion resistance, modulus, hysteresis and creep. Also, other chemicals may be added which protect the rubber from sunlight, ozone and oxygen.
The ability to formulate rubbers with specific properties makes it so versatile and useful in an almost limitless number of applications. Natural rubber in particular is especially valuable as a spring material because of its longevity, resilience, low cost, resistance to a wide range of temperatures, and ability to bond to metals. Natural rubber is used in many of our Lord Mounts because of these characteristics and its ability to reduce the transmission of both vibration and noise in harsh environments. For example, it can resist the the heat and chemicals encountered in vehicle engines, and its resistance to swelling when immersed in liquids means it can also successfully withstand underwater conditions for many years.
However, even rubbers with like properties may not perform the same in identical environments. As Lord states in its design literature, a 50 durometer natural rubber manufactured by one company will exhibit different characteristics than their own 50 durometer natural rubber compounded to perform correctly with their isolators. In fact, even standard mounts may not be suitable, and Lord compounds special elastomers with different spring rates and dimensions when custom-engineered solutions are necessary.
But when one thinks of a spring, an image of a coiled metal usually comes to mind. With steel springs, there is a linear relationship between the force and the deflection (think of the up and down motion of a mass suspended from a metal spring). However, rubber springs can be designed to provide different stiffness in non-linear directions. Shear forces such as friction occur when two opposite sides of the material experience forces in opposite directions, as shown in the diagram below. The shear modulus describes how a material responds to this type of stress, and is defined as the ratio of shear stress to shear strain expressed in gigapascals (GPa). To put this in perspective, a filled rubber at 2% strain may have a shear modulus of 0.0003 GPa versus 79.9 GPa for structural steel. What these numbers tell us is that rubber can be stretched much more than steel before it is permanently deformed.
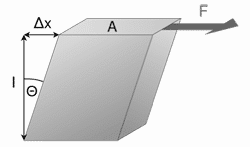
Image: Shear forces
Other important advantages of rubber over steel include its ease of handling and installation, energy storage capacity, and ability to convert some energy to heat when it is deflected. The latter characteristic is referred to as hysteresis, and it is the reason heat doesn’t build up in rubber to the extent it does in metals. Natural rubber without fillers exhibits very little hysteresis, and as a result it provides energy dissipation, or damping, in a system subjected to vibrational forces. The takeaway is that unlike steel, rubber has some inherent damping ability.
The discussion above should make it clear why rubber is so valuable in vibration isolation. However, it just provides some key points on a very complex subject. It’s important to keep in mind that picking the wrong mount can actually make vibration worse than if there were no mount at all. We recommend considering vibration control strategies early in the product design process and consulting with an engineering expert when selecting materials and mounts. We also recommend working with a top manufacturer like Lord Corporation, which has extensive facilities and engineering resources to perform product, material and prototype testing under real-world conditions.
We are a distributor of Lord Corporation standard vibration and noise control products for the entire Western U.S.A. Contact us today for expert advice on managing your vibration isolation challenges. Also, visit our website to see the large variety of Lord mounts we deliver to the marketplace.